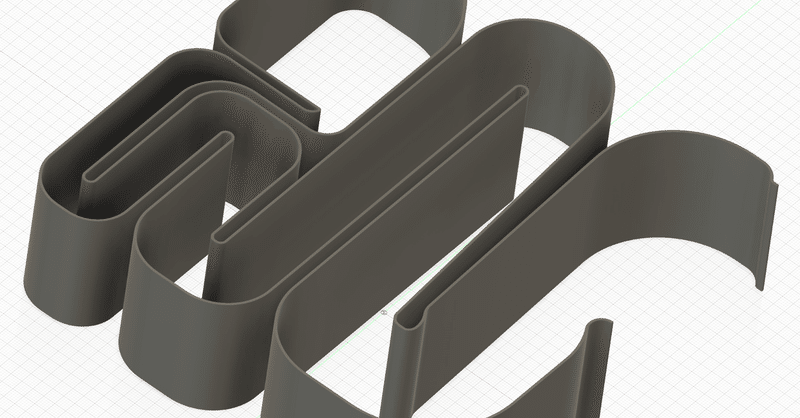
3Dプリンターでスピーカー(エンクロージャー)を作る
最近、3Dプリンターでスピーカー(エンクロージャー)をつくる人をチラホラ見かけるようになった
3Dプリンターでスピーカー(エンクロージャー)を作るにあたっての、メリット・デメリットを考えてみよう
メリット
形状が自由自在
3D CADで設計して出力するので、木でできた四角い箱ではなく丸みを帯びたものや複雑な内部構造を持ったものなど、通常の木工でできる範囲を大きくハズレたものができる
https://blog-imgs-113.fc2.com/m/o/n/monokeros1100/blog_import_5c85fa9aa9591.jpeg
>こんなの作ってみたいですよね!
木工技術など必要ない
木で作るとなるとそれなりの設備や技術が必要となる。
3Dプリンターで作れば最終仕上がりまで、そのような設備や技術は不要(もちろん3Dプリンターありきの話ですが)
デメリット
所詮、プラスチックなので高品位な音は期待できない
スピーカーエンクロージャー材質の条件としては、内部損失を持った材料ということとなる。これは材質自体が振動してしまうのを防ぐという意味
これがプラスチックだと、内部の反射や振動などを抑えられす思ったような音質が得られないことがある。
制作時間
20cm角クラスでも全部を3Dプリンターで作ろうとすると、だいたい1日以上かかる。木工であれば慣れた人なら数時間でできる
プリンターの性能やノズルの大きさによってもずいぶん時間は変わってくるが、時間がかかればかかるほど出力失敗のリスクも上がってくる
ーーーーーーーーーーーーーーーーーーーーーーーーーーーー
というような感じである
そこで3Dプリンターを使ってスピーカー(エンクロージャー)を作る場合どのようにすればデメリットの無いようにできるのか考察していく
自作スピーカーの中で最も人気のある形状はバックロードホーン(以下 BH)だと思います。比較的小さなユニットでも、迫力のある低音再生ができるので、日本の住宅事情とも相まって緒戦する人が多いと思います。
BHは板材を切り出したキットも多く販売されており、初心者でも手軽に挑戦できる環境となっている
しかしながら、BHは内部が迷路のように複雑に音道が作られており、これを木材で実現しようとすると必ず直線的なカクカクとなってしまう。
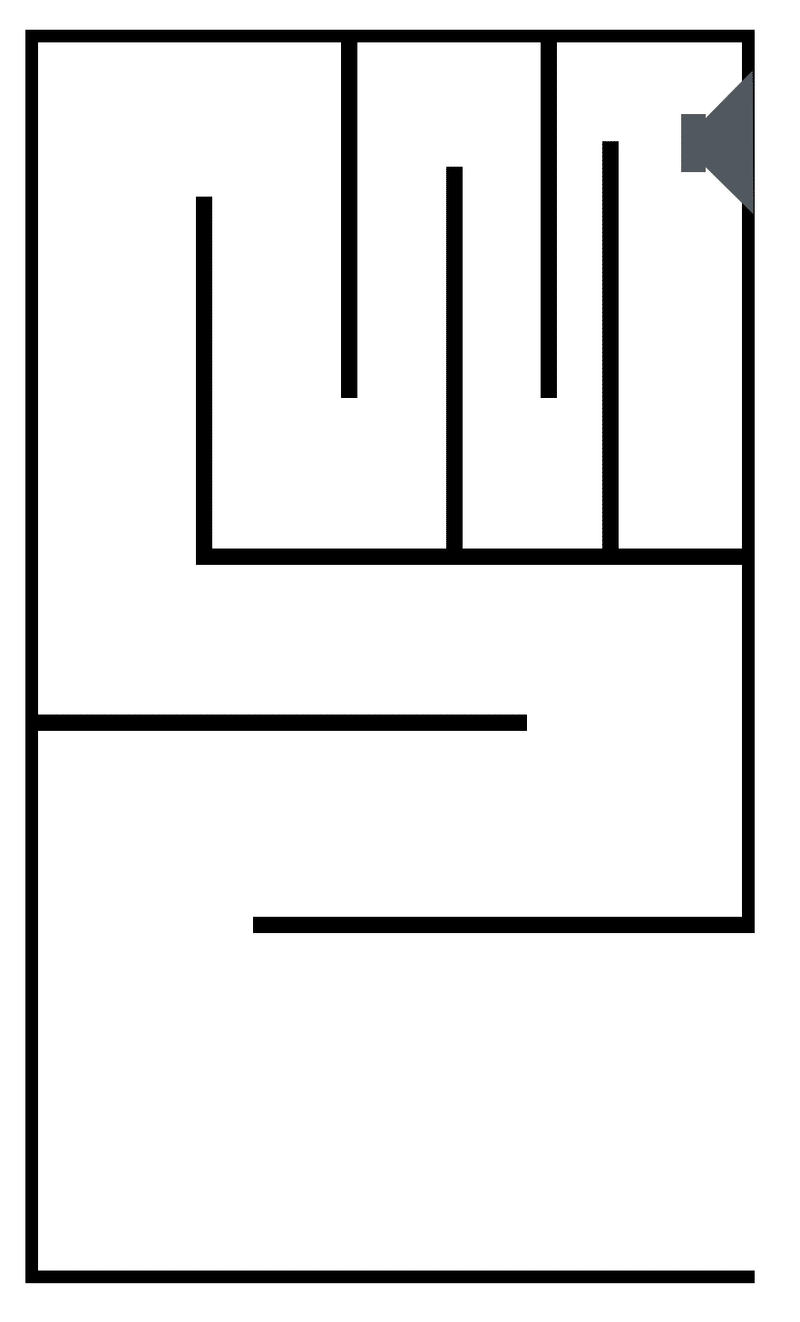
3DプリンターでBHを作りたいと思う人は、このカクカクではなく滑らかな音道を実現したいと思って挑戦する人が多いのではないか?
BHの概念は下の図のようなもので
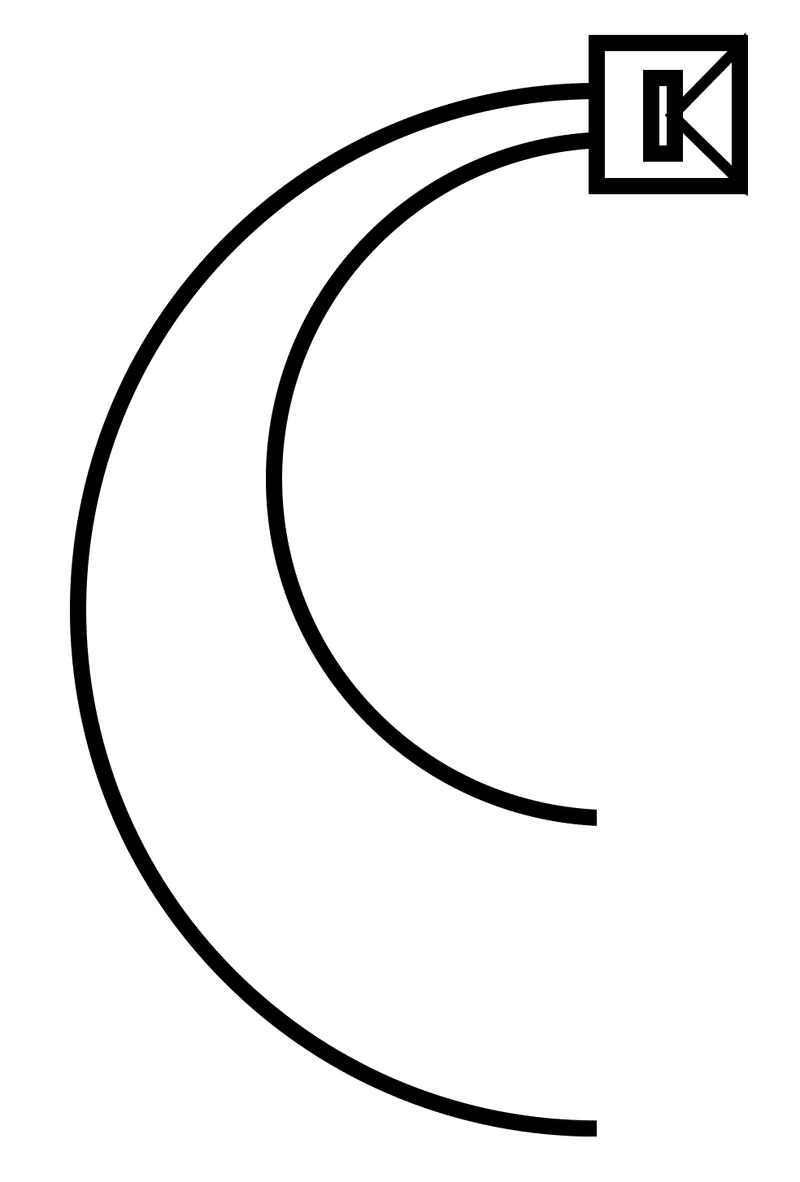
スピーカーのユニットはもちろん前側に音が出るのだが、それと同時に後ろ側にも音が出る。しかし、前に出る音と後ろに出る音は位相が全く逆なのでそのままでは低音が全く出ない。そのため普通のスピーカーはユニットを箱の中に入れて、後ろ側の音の逆位相の音が干渉しないようにしている。
それに対してBHは後ろ側から出る音を最大限増幅させて低音再生に利用するというものである。そのためBHは通常の密閉型やバスレフ型に比べ、同じユニットを使っているにも関わらず数デシベル能率が高い。(聴き比べると驚くくらいに音量が違う)
そしてこの概念を箱にすると、箱の中でクネクネ・カクカクした音道を持つエンクロージャーとなる
さて、このカクカクな音道よりも丸みを持ったカーブにするほうが音質的にも優れていると言われているので3Dプリンターで作る意味合いが出てくる
実際に3DCADで設計したBHがこれ
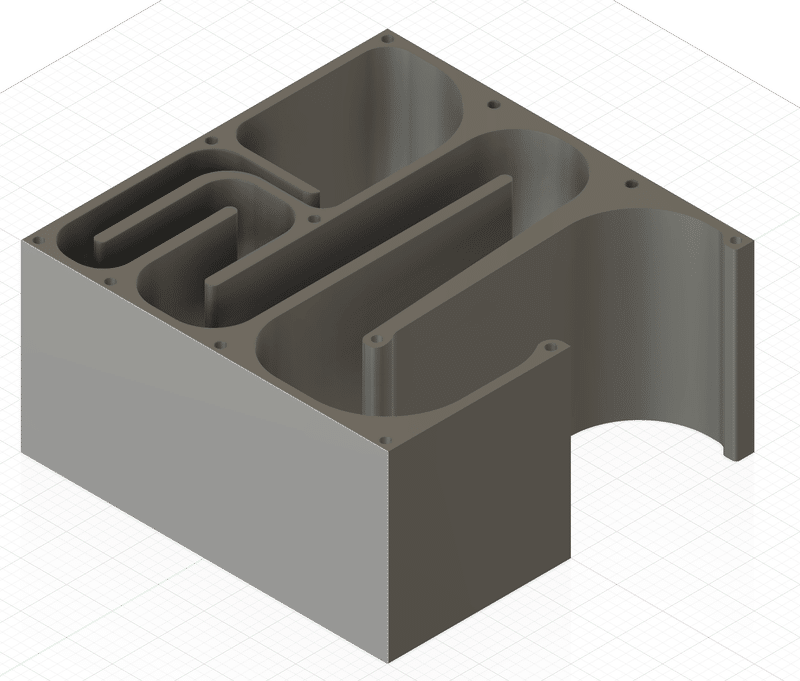
板材で作ったBHに比べると角が無く、いい音がしそう(あくまでも個人的な希望w)である現在の木材加工機器を使えばこのような形を木材で作ることは不可能ではないが、個人レベルでは無理さて、ここでこのような自由な設計ができるということはご理解いただいたと思うが、ここで冒頭のデメリット>所詮プラスチックなのでいい音が望めない・・・ということこれの解決策として、この3DCADデータから平面図を出して、板材からこの形を作る・・・つまり5mmとか10mmの板材であればレーザーカッターであっという間で切り出すことができる。厚みが10センチなら、10mmの板を10枚切り抜いて重ねれば上の図のようなエンクロージャーが出来上がる
3Dデータといえども、見てもわかるように垂直方向は全くの同じ形なので何枚か重ねれば、自由な設計のものを木材として作り出すことができる
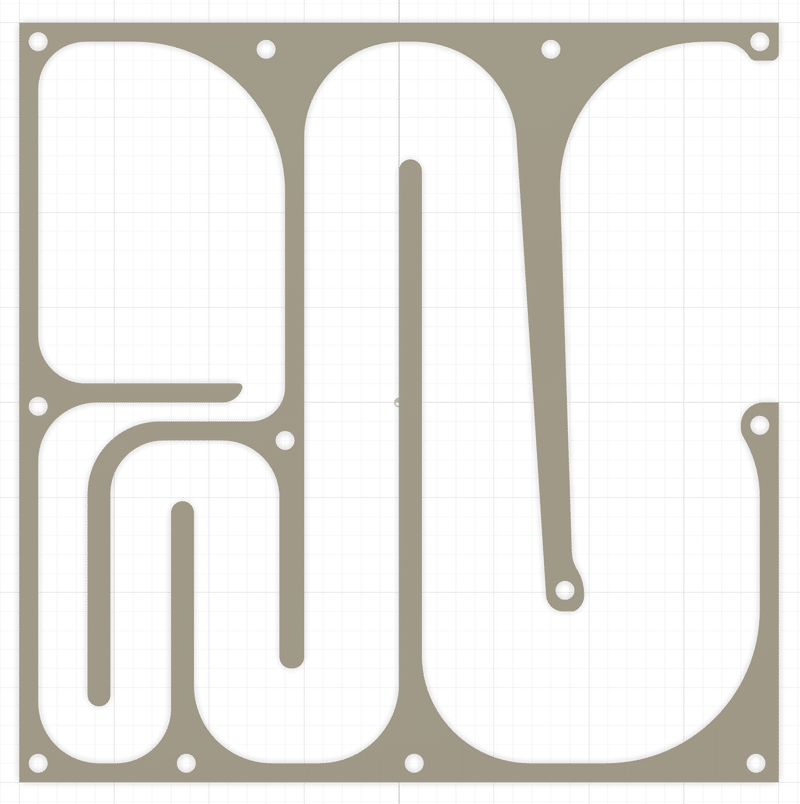
この3Dデータは側板を省略しているので、最終的には両側に板材を付けると出来上がりとなる。
もう一つの手として、木質フィラメントを使うということ
3Dプリンターはいろいろなフィラメント(積層する材料)を使うことができる。一般的に使われるのはPLAやABSというプラスチックが圧倒的に多いが他にもTPUと呼ばれる柔らかい材料やPETボトルの材料のPET等がある
ちょっと特殊ではあるが、木質フィラメントというものもある。これは木を粉末状にしたものをPLAなどに混ぜたもので、仕上がりはMDFと同じような(もっと密度が低いのでLDFクラス?)風合いとなり、内部損失もそれなりにあるので、音質的にも期待ができる。
先程の3DCADで作ったモデルを木質フィラメントで出力すればMDFで作ったものと遜色ないレベルでの期待はできるが、問題はその出力時間。
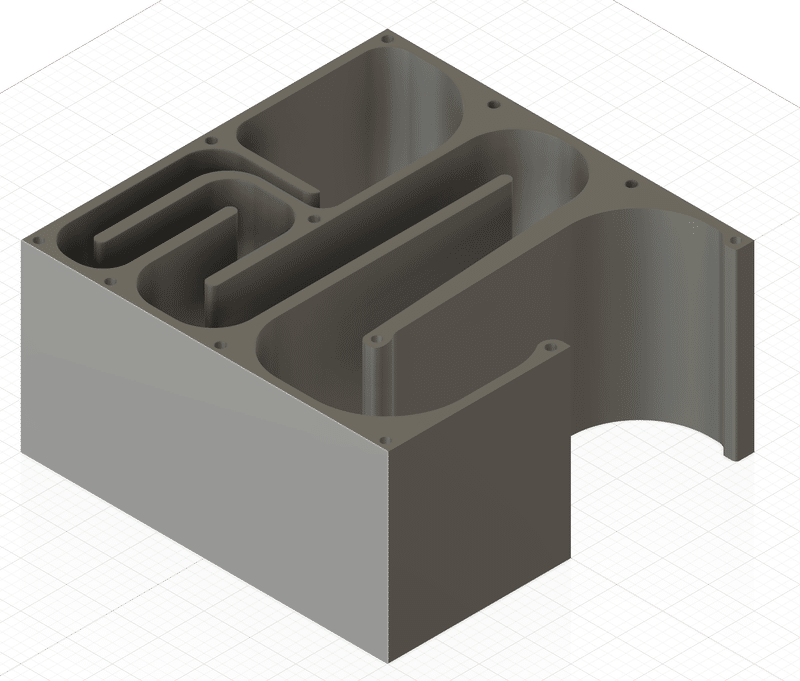
時間短縮のために側板はあえて作っていない、側板は普通の板でも買ってきてつければいい。側板のように100%の面積を何層にもわたって出力するのが一番時間がかかる。インフルの密度を落として時間短縮する手もあるが、側板は強度を保ちたいし、重量も持たせたいのでここはMDFなどの板を付けたほうがいい選択となるだろう
3Dプリントされたものと板材の接合であるが、そのために要所に穴を開けてある
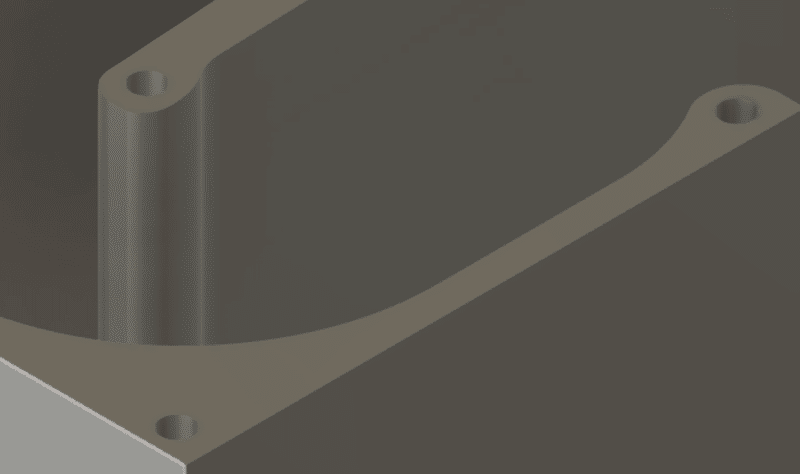
この穴に鬼目ナットを埋め込む。フィラメントは熱で柔かくなるので、鬼目ナットを加熱してウニウニっとねじ込む。加熱しないでねじ込むと確実に割れるので加熱は必須です
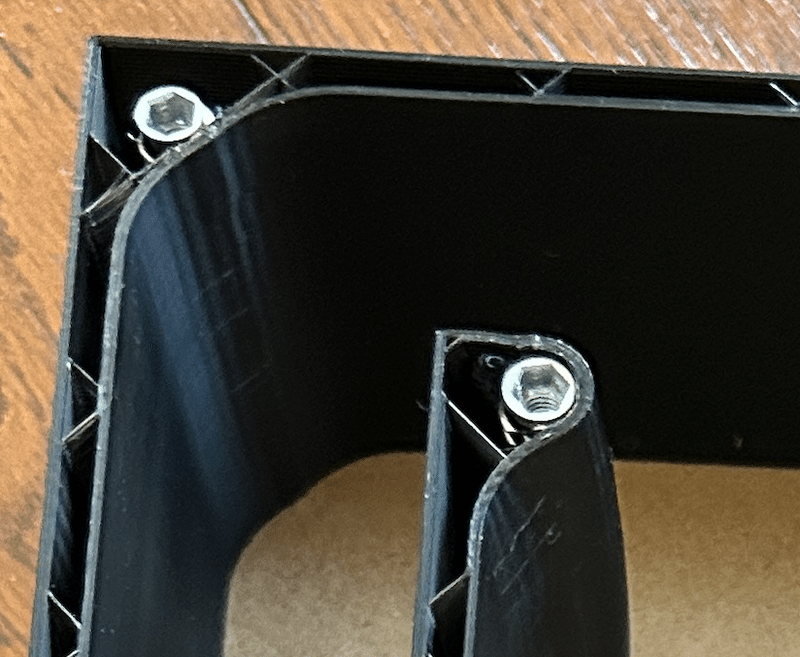
鬼目ナットを埋め込みボルト締めできるようにしておけば、ちょっとした調整も難なくできるようになる
ということで、側板を板材を使うことで比較的短時間で出力が可能となる
でも、もっと短時間で出力したいという人は、3Dプリンターで出力する部分を極限まで削ることで時間短縮はできるので、音道部分のみを出力することもできると思います
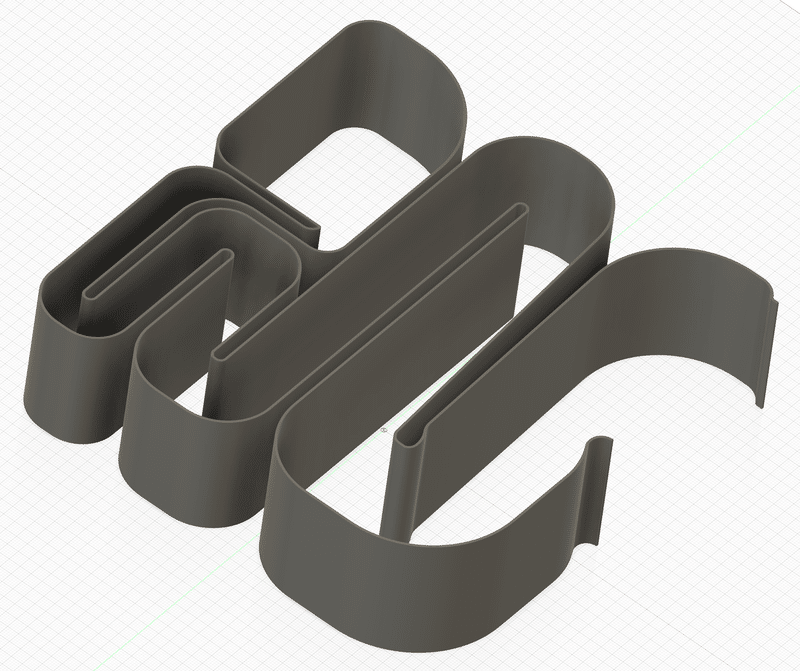
このような音道部分のみを出力し、側板で挟んで要所はコーキングなどで固定するという方法も取れると思います
まとめ
3Dプリンターを使ってエンクロージャーを作る場合
できるだけ時間をかけないようにするため、側板は木板を使い時間を節約する
もっと時間をかけないようにするため、音道部分だけを3Dプリンターで出力し、側板で挟み込む。強度が必要な部分には対策を行う
音質を上げるために木質フィラメントを使う
PLAなどのフィラメントを使う場合は、音道に沿ってフェルトなどを貼る
鬼目ナットを埋め込むなどして、あとからも調整できるような作りにする
3DCAD設計だが、3Dプリンターを使わずに、板材をレーザーカッターで切り出し、積層して作る
3Dプリンターの最大のネックは、その出力時間ですね
20cmクラスなら一晩かかる・・・
対策としてはノズルの径を大きくするというのがあります
通常のFDMプリンターのノズルは0.4mmですが、0.8mmや1.0mmにするとはやはりその分速く出力できるようになります
その時気になるのが、積層痕ですが、例えば0.4mmノズルで0.3mm積層とすると、ちょっと気になる感じですが。1.0ノズルで0.6mm積層だと、なんだかテクスチャーの模様のように見えてかえっておしゃれっぽく見えることもありますw
単純に計算すればWHDで8倍ということ無いなりますが、実際はそんなに早くするとフィラメントが追いつかないので、2−3倍といったところでしょうか?
このコラムが皆さんのDIYのご参考になるようでしたら幸いです^^
この記事が気に入ったらサポートをしてみませんか?