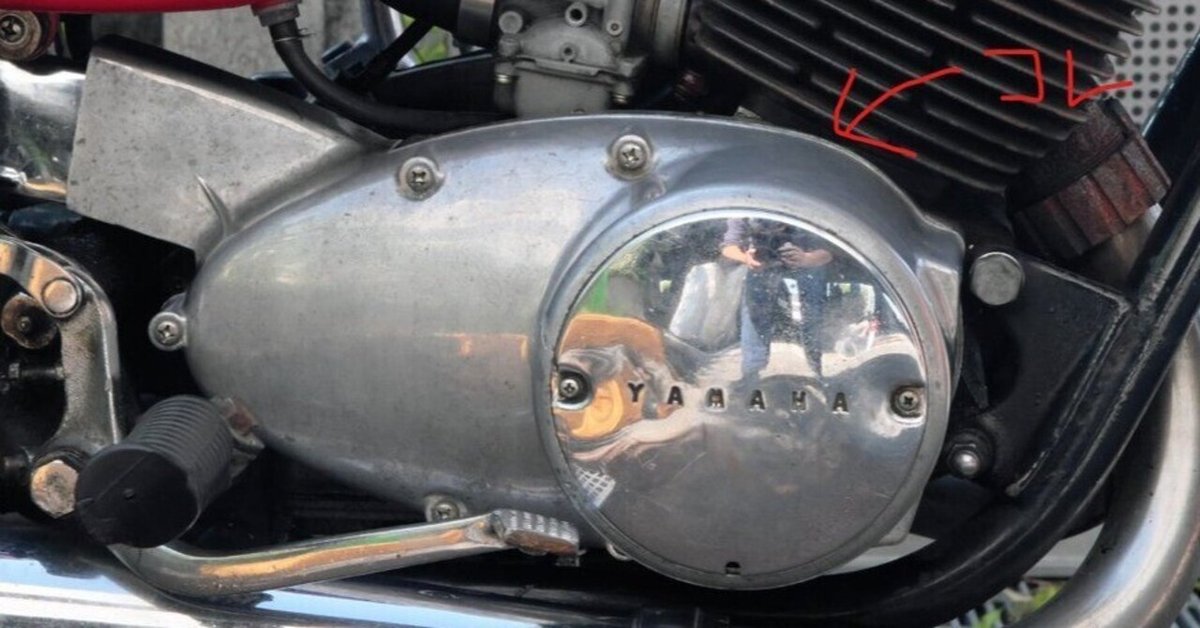
3Dプリンタでバイクの絶版部品を複製した話
業務用3Dプリンタを手軽に使えるサービスがある。
https://note.com/hexcapbolt/n/na22ea93a3329
個人向け3Dスキャナもかなり性能がよくなってきた。
https://note.com/hexcapbolt/n/n21e938e36380
つまり「高度なリバースエンジニアリングもDIYでやれるレベルに降りてきたのでは?」と思ったのでやってみた話です。
何をつくるか
ヤマハ YDS3/YM1用のクランクケースカバーを作る。
部品の外寸は約300 × 150 × 200 mm程度で、肉厚2mm程度のアルミ鋳造品だ。エンジン側面に装着されている発電機・点火機構を保護している部品。
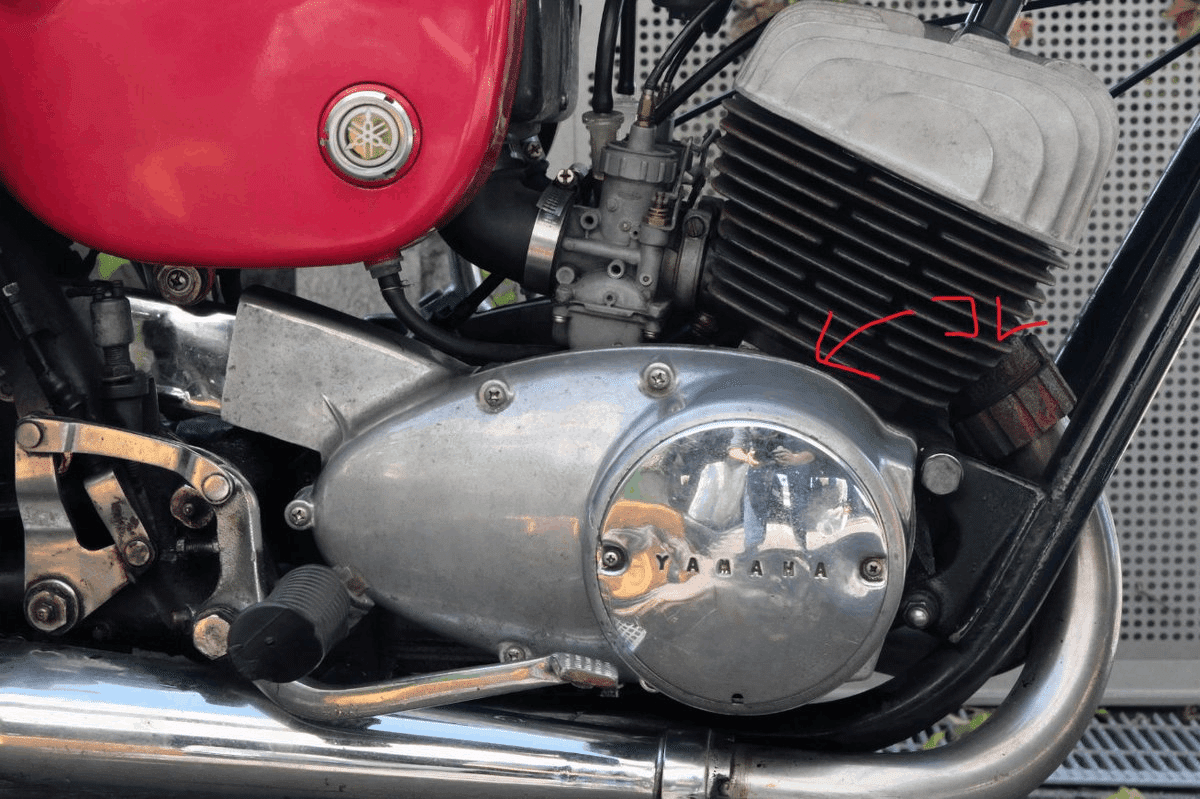
なぜこの部品か?というとこれら4つの理由によるところが大きい。
気密・水密・油密が必要ないこと(平面度が要らない)
強度・剛性が必要とされないこと(機能部品ではない)
適度な大きさであること(小さいと映えない)
最悪の場合、壊れても自走不能にならないこと
3Dスキャン・採寸・モデリング
2DCADや部品現物から3Dモデルを起こす業務の経験から、リバースエンジニアリングにおいてストレスなポイントはこの3つだと思う。
イチからモデルを起こすので工数が大きい
作ってみるまでモデルが正しいか答え合わせができない
測定が難しい箇所がある
3Dスキャンは2、3を解決してくれる。
特にモデリング中に3Dスキャンデータを参照しながら作業できることは非常に良い体験をもたらしてくれる。しかも抜き勾配や奥まった位置の角Rなど測りづらいところも良く撮れている。これはとても効率的で革命的に良い開発体験だった。ちなみにモデリングはFusion360のソリッドモデリングで行っている。形状が単純なのでサーフェスモデリングまではいらなかった。
昭和40年当時、大昔のダイカスト部品の抜き勾配なんて測るのも面倒な部位も、スキャンデータとの照らし合わせで視覚的に合わせ込んでいける。本当に3Dスキャンデータがあると楽。 pic.twitter.com/A9k48Gyf3e
— capbolt (@hex_cap) May 25, 2022
3Dスキャンの様子はこんな感じ。Revopoint POP2というスキャナを使った。
昨日3Dスキャンした部品は、まず点群データが得られ、それを自動でノイズ除去したうえメッシュ化ができるけれども、限界があるので手動で点群データのゴミ取りをします・・・ pic.twitter.com/81Q52f0eyX
— capbolt (@hex_cap) May 21, 2022
3Dスキャンの要点に関してはこの記事に少しだけ書いた。
https://note.com/hexcapbolt/n/n1df1838d6eda
モデルがある程度完成したところで、寸法確認のために家庭用3DPで出力して仮組みをした。
起こした3Dモデルを3DPで出力して、仮フィッティングをしました。モデルのねじ穴位置がずれていないことを確認できました。 pic.twitter.com/qwuwQZVxyO
— capbolt (@hex_cap) July 2, 2022
製造
モデリングが完成すれば、あとは製作するだけだ。
「個人」で可能な範囲だとこれくらいの選択肢がある。リストの上のほうがコスト安、というつもりで並べた。DIY鋳造はよく知らんが。
樹脂3Dプリント
CNC削り出し
金属3Dプリント
DIY鋳造
今回は一番コスト安な「樹脂3Dプリント」を選んだ。
さて、どの樹脂を選ぶか、という話があるが、クルマ・バイクに使うなら、特にエンジン部品として使うならナイロン樹脂(PA、ポリアミド)が第一候補になる。なぜならHPのMJFが多面的に見てとても強いから。
価格が安い、納期が早い、精度が良い、表面性状も比較的良い
物理特性の異方性が少ない
造形制約が少ない(SLSなので)
耐薬品性が良く、ガソリン・クーラント・オイルに耐える
トヨタ・ニッサンの補給部品として採用実績がある
というわけで外注プリントで作った。当時は2万円弱だったが、最近は3DP業界も値上げが続いているのでもうちょっと高くなるだろう。
https://note.com/hexcapbolt/n/na22ea93a3329
オリジナル部品と複製、瓜二つでイー感じです。装着確認はまた明日。 pic.twitter.com/TtULkDuRRR
— capbolt (@hex_cap) September 30, 2022
装着・運転
ヤスリがけするとか修正することもなくポン付けできた。3Dスキャンを使った精度が良いモデリングと、MJFの高精度な造形の合わせ技によるものだと思う。装着したまま約200km走ったが特に問題なかった。部品の破損はもとよりネジのゆるみ等もなかった。
←複製品(ナイロン樹脂)
— capbolt (@hex_cap) October 1, 2022
純正部品(アルミ)→ pic.twitter.com/bbN5vaOSH2
まとめ
約300x150x200mmのバイク部品を複製した。
個人向け3Dスキャナーを活用してモデリングした。
業務用3DPで造形して約2万円で製造した。
実車に装着して特に問題なかった。
個人でも精度の高いリバースエンジニアリングができる時代になった。
DIYで廃盤部品を3Dスキャンしてデータ化し、3Dプリンタで出力することで古いバイクのクランクケースカバーを複製できました。 pic.twitter.com/dWE9jufUjh
— capbolt (@hex_cap) October 8, 2022
おまけ
透明部品 ブレーキランプを作った話
StratasysのJ750 (DMM.makeでいうマルチマテリアル)を使うと透明部品も作れる。バイクに装着して以来、丸3年間は使えている。
試作テールランプ届きましたわ。 pic.twitter.com/gjHttnC0NN
— capbolt (@hex_cap) July 11, 2020
発色いーかんじじゃない?ゴミはいりまくったから今から塗装剥ぐけど。 pic.twitter.com/xFQti8Nq3l
— capbolt (@hex_cap) July 12, 2020
ウィンカーをゼロから作った話
純正ウィンカーがヤフオクで1個1万円、車両1台分4個4万円で取引されているのにキレて作った。これも丸2年は問題なく使えている。缶スプレー塗装はちょっと禿げたが。
バイク用ウィンカーをフルスクラッチしました。既製品はネジと電球、ソケットだけです。 pic.twitter.com/zIk4yfrXDk
— capbolt (@hex_cap) May 5, 2022
この記事が気に入ったらサポートをしてみませんか?