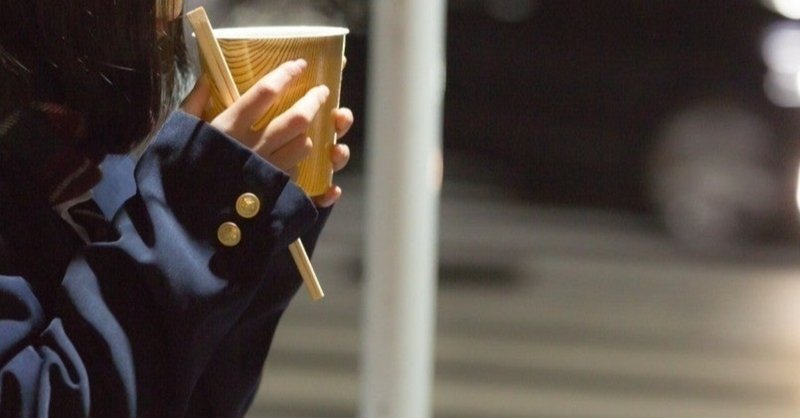
WMSを導入した時の話
配車係のたろーです。
今の会社ではないのですが、前にいた会社でアナログで管理していた倉庫にWMSを導入したことがあったんですよ。WMSとは、Warehouse Management Systemの略で、いわゆる倉庫管理システムのことです。
倉庫管理をアナログでやっていた会社からすると、システム化をするってのは会社的にも一大事で、てんやわんやだった記憶があります。ロケーションって何それ?棚番ってどうやってつけるの?みたいな。
ということで、どんな感じだったか記憶を辿ってみたいと思います。
ちなみに、私がいまから書く話は体験談であり、効率的なシステム導入の話ではない事を先に記しておきます。ていうか、システム自体はシステム会社の人が入れてくれましたが、どんなふうに導入するのか?どんな運用方法がいいのか?というのは全く無く(おそらく会社がケチってパッケージのみ購入したと思われる)、全て手探りで導入したからであります。
導入1ヶ月前
システムを導入するにあたって在庫管理は必須です。倉庫の集約もついでにやったこともあり、各拠点から在庫を移動し全棚を行いました。
この全棚が厄介で、その当時の倉庫の在庫は帳簿上あるんだけど、実際は在庫がないというのが山ほどあったんですよね。ピッキング中に在庫がないと帳簿から在庫を消すんですが、大量にありすぎて一気に処理出来ないような状況です(損失になるからね)。で、倉庫責任者はこれをずっと放置というか、隠していたわけですが、この拠点集約の全棚にて全てが明るみになってしまったわけで…。
このせいで多少の処分があったものの、とりあえず先に倉庫集約・システム導入を成功させなければならなかったので大きい問題にはならず、命拾いした人も多数いたのでした(笑)
輸入物の商品はトラップ案件
全棚をやると同時に、商品管理をするためのJANコードと会社用の商品コードを紐つける作業を一緒にやってたんですよね。
ここでも問題が色々勃発しました。
まず、うちの会社は既存商品とリニューアル商品を同一コードで管理していたのですが、リニューアル商品ってバーコードが変わるってるんですよ。当時導入したWMSは1商品につき、1バーコード(JANコード)という設定になっていたので、こうなるとバーコードで在庫管理が出来ないんですよね。
また、輸入商品も多数扱ってたのですが、こちらも代理店が違う同一商品でバーコードが違うというのがありました。特に輸入商品はコロコロと代理店が変わっていたため、一つの商品コードで4つも5つも出てきちゃうんですよ。おそらく、輸入した時にバーコードを張り替えていたのかな?よくわかりませんが、上から貼られているのが多数ありました。
そんなわけで全棚は取ったものの、在庫が合ってるのか合ってないのか、どれが同じなのか同じじゃないのか、棚をとる人間も普段倉庫をやってない営業とかを動員してやったもんだからカオスな状況になったのは言うまでもない…。帳簿上の在庫と実棚があってるかどうかわからないまま、システム導入に向かうのでした…。
棚割りは非常に大事
WMSを導入している倉庫ならわかると思いますが、在庫というのはロケーションと呼ばれる住所に必ず紐づいております。このロケーションがしっかりと設定されてないと、日付逆転で出荷してしまったり、あるべき在庫がない、という状況になるわけですね。
もちろん、そういうことは事前に説明はされてたんですけど、出荷頻度というのをきちんと考えてロケーション管理しないと大変だということに、その時は誰も気付いてなかったんですよね(システム屋さんは気付いてたと思うんですが、何せ金払ってないからね…)。
よく触る大ロット品というのは、出荷バースの近くに配置し、あまり出ない小ロット品は遠くの方に配置。小口商品はリフトを使わない二階に置いて、みたいな簡単なことが分かってなかった我々は、普段通りの要領で在庫を格納していたわけで。
しかもです、よく考えないでロケ割りしてるもんだから、ロケの逆転なんかも起きたりしてですね(これやると、ピック中にバックしないといけないので非常に効率が悪い)。
ほんと、なぜケチって導入を全てシステム会社に面倒見させなかったのか?気が知れないですよ。そんな簡単なもんじゃないでしょうに、システム導入ってさ。
ハンディターミナルが使えない問題
私がいた問屋は100年企業というかなりの老舗で従業員も高齢な人が多かったんですよね。当時はまだスマホも一般的じゃ無くて、好きな人は触り始めてるけどおじさん連中はみんなガラケー。簡単な操作しか出来ませんって感じでした。
そんな人たちなもんで、ピッキングが全部ハンディになった時にかなりブーイングが巻き起こりました。しかし、システムが入ってしまった以上、使わざるを得ません。
今まではピッキングリストを見ながら、積みつけしやすい、取りやすい順番でピッキングをしていたおじさんたちですから、いちいち積みつけしづらいピッキングの指示にイライラが募りましてですね。
これは後でピッキングする作戦を敢行するようになっちゃったんです…。
この後に取りやすいやつが出るはずだから、とりあえず取ったことにしてピッキングリストを進めよう、これは取る予定だから紙に書いておいて後で取りに戻ろう、みたいな。
もはやロケの意味をなさないピッキング状況で、戻ってくるはずのないピッカーがバックで戻ってきたり、引当されてない商品をピックしてしまったり、ピック漏れが多数発生したりとてんやわんやな状況に。
最初の導入だからゴタつくのは仕方ありませんが、やっぱり導入前に教育しないといけないよね、というのはここで学んだのでした。しかし、あれは本当にカオスだったな…。
棚卸しが出来ない問題
冒頭の方でも書いたんですけど、バーコードが一意じゃなかったんですよ、うちの倉庫は。そうなるとどうなるかというと、在庫をバーコードで取ることができないということなんですよね。
バーコードで在庫があってるかどうかわかるってのは本当に重要です。ピッとやってその在庫が本物かどうかわかるっていうのは、正確さが断然違いますからね。しかし、それが出来ない。誤出荷してるのかどうかすら把握出来ない。
特に輸入物は海外表記なので、品名で合ってるかどうか確認するのが非常に難しいです。バーコードが通れば合ってるって確信は持てますが、通らないけど合ってる可能性もあるという、これまたカオスな状況でありまして。
導入当初も在庫あってるかわからない状況でしたから、これはもう永遠に在庫が合わないなってことになりました。えぇ、会社もサジ投げました。
システム導入後は、アイテムがちゃんとロケに入るようになったので迷子になることはほぼ無くなりましたが、それでも以前の在庫が合わないままなので大量の過小過剰が存在する倉庫として今でも運用しているようです(それでも多少合ってきたと元同僚と飲むと教えてくれますw)
WMSの導入はプロに任せよう
私は昔SEをやっていたのでシステム導入って綿密に計画してやるもんだよ、と思ってましたが、当時はただの倉庫作業員でしたので何も言えることはなく、ただただこの混乱に巻き込まれるだけでした。
この後、別の倉庫でシステム導入に初期から携わることになるんですが、その時は気を付けるところを当時のセンター長にがっつりレクチャーしたので、大きな混乱は起きませんでした。やっぱり事前準備は大事よね。
ただ、結局のところバーコードが一意じゃない問題はずっと続いていたので、誤出荷や棚卸しが合わない問題は解決しなかったんですけどね。今はどうなってるんだろう?
WMSの導入は是非ともお金がかかっても全部プロに委託することをオススメしますよ。
お金が貯まったら飲みに誘います。