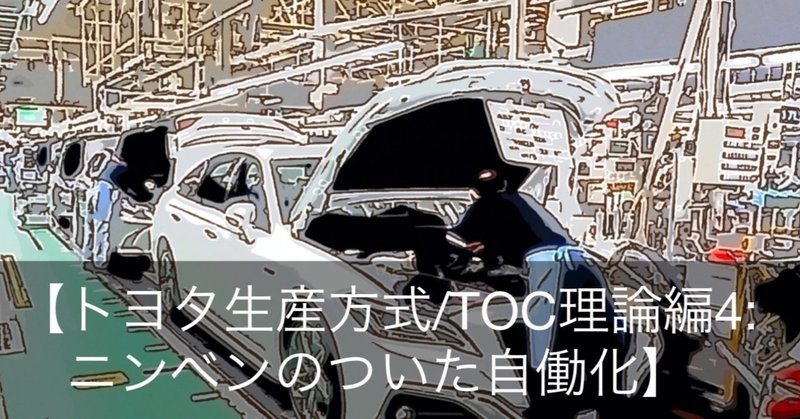
【トヨタ生産方式/TOC編4;ニンベンのついた自働化】
*前回までの投稿は上のマガジンに入れています。
大卒で大手素材メーカーの工場に配属された若手の紫耀(しょう)と同じ工場に転勤してきた別部署の中堅社員の管理者の健(タケル)との会話です。(もちろんフィクション?)
先輩に指導を受けながら、トヨタ生産方式について学び、自部署の課題を解決に挑戦するようです。前回の投稿ではジャストインタイムについて勉強し、今回はもう一方の柱、”ニンベンのついた自働化"について学ぶようです。
・・・・・・・・・
ニンベンのついた自働化
👱🏼;おはよう。
🧒;おはようございます。今日は自働化ですね。おさらいになりますが、トヨタ生産方式の基本は、徹底的なムダ排除による原価低減で、この基本思想を貫くトヨタ生産方式の2本柱がある。一つは前回学んだジャストインタイムで、必要なモノを、必要な時に、必要な分だけつくること、供給することですね。そして、もう1つは、自働化で、異常、問題があればその場で止まる、判ることですね。豊田佐吉さんが考えだし、それを体系化・実践化したんですよね。今日はその2本目の柱である、自働化について学んでいくんですよね。
👱🏼;すごいな。立て板に水のようだ。でも、わかってきたようだね。では、始めよう。
🧒;よろしくお願いします!
2つのジドウカ
👱🏼;早速だけどここで、「ジドウカ」って2つの感じがあるよね。“自動化”と“自働化”だ。違いが分かるかい?
🧒;ニンベンがついているものといないものなので、何か人がかかわることで違いがあるのでしょうか?
👱🏼:うーん。「自動化」は、人の作業を機械に置き換える事なんだ。ニンベンのついたほうの「自働化」は、人の働きを機械に置き換える事なんだ。
🧒;人の作業を機械に変える・・。人の動きを機械に変える・・。違いが、イマイチちょっとわからないです・・。
👱🏼;目的が異なるって言ったらいいかな。ニンベンの付いた自働化では、どんな人の働きを機械に置き換えるのか説明するとわかると思う。
目的は3つあるんだ。
・機械の異常を判断して、設備を止めること
・品質の異常を即座に見つけて、設備を止めること
・ライン・工程の異常を判断して、止めること
それに対して、ニンベンのつかないもの自動化は単純に人の作業が減る。楽になるということが目的になるんだ。
🧒;なるほど。機械に、判断するという機構が入っているということですね。
👱🏼;そうだ。異常が出たら止まる機構を機械が持つことで、作業者や、管理監督者の時間を、付加価値の高い、他の仕事へ振り向けることが出来るようになるでしょ。機械を止めること自体が目的でというわけではなくて、あくまで人に付加価値の高い仕事をさせ、原価低減に繋げることが狙いなんだ。
🧒;なるほど。あくまでも付加価値を上げて、原価低減に向かうということですね。違いはわかりました。
👱🏼:自働化において人の働きを機械に置き換えることにより、具体的には次の2つのアウトプットを狙っていくんだ。1つ目は、省人化。省人化においては、自働化により、人を機械の番人にしないことがポイントです。
🧒;機械の番人。。なんかわかります。あるあるですね。
👱🏼;そうだよね。そして、2つ目は、品質・設備・ラインのつくり込みだ。つくり込みにより、問題点を見える化し、自工程完結を進め、人材育成へ繋げていくことがポイントなんだ。この二つは重要だから少し追加で話そう。
🧒;重要そうです。そして、永遠のテーマな気が・・。
自動化による「省人化」
👱🏼;まず省人化から話していこう、ここでのキーワードは、先ほど話した、機械が異常で止まるかだ。機械が異常で止まらないと・・・作業者がその場に常にいないといけないよね。
🧒;はい。そりゃそうです。さっきの番人の話ですね。異常が止まらなければ、ひたすら不良を作ることになって、後で大変なことになります。
👱🏼:そう。ただの自動化の発想だと、人の手で行なっている作業を、自動で動く機械に置き換えるだけになって、「常時監視」が必要だ。これって人が減ってなくて結局原価低減にならなくて、「作業が楽になった」で終わるってしまうのよ。
🧒;なるほど。これは、ニンベンがないほうの自動化ですね。
👱🏼;くどくてごめんだけど。いくら機械を沢山導入したとしても、1人1台で監視をしなければいけないのであれば、結局省人化できず、原価低減に繋がらないんだ。目指すべきは、異常時に機械が自動的に停止する機構を組み込み、多台持ちが出来る、ニンベンの付いた自働化なんだ。
🧒;自働化によって、一人1台担当するのを1人で複数台持つように変えるということですね。ということは、多台持ちができると、作業が自働になるだけでなく、省人化ができるということになるんですね。
👱🏼;そう。異常時に、しっかりと停止してくれると、安心して1人で何台も面倒をみることができたり、他の付加価値の高い仕事を行なうことができるんだ。ちなみに省人化っていうのは、それは人員削減するということだけにはならない。現在よりも付加価値の高い仕事をさせるという意味を強く含んでいる。誤解しないでほしい。ここが管理者の腕と信念の見せ所。人が足りない部署や改善が進んでない部署は絶対にあるから、全体を見渡して最適化するんだ。それに少し時間軸を長く考えれば定年する人の補充分として人員を確保しておくこともできる。
🧒;だいぶ熱くなってますね・・。はい。わかりました。
自働化による「作りこみ」
👱🏼;では、次は「自働化によるつくり込み」について話そう。
ライン停止や設備トラブルは生産ロスの増加に繋がるよね。もし停止が発生した時には、「何で止まったんだ、何で止めたんだ、間に合わんぞ」、といって突っ込まれるよね。
🧒;はい。言われて、嫌になります。だから、「何かあっても機械は止まらないようにしておこう。」「止まってもすぐに起動させよう。」ってどうしてもなってしまいます。
👱🏼;でも、問題の真因が掴めないまま生産を続けるとさ、同じトラブルやロスが発生して、ムダが再発するよね。
🧒;はい。後工程に迷惑をかけることにもなります。最悪の場合、顧客に迷惑かけることになって会社の信用を失うこともあります・・。実際に・・。
👱🏼;だよね。でも、そうならないように、機械を止めることは非常に重要なんだ。しっかりと止めて、再発防止策を実行することで、下記のメリットがある。
・異常時の不良発生数が減少する。
・同じ問題が繰り返されなくなる。
・問題点が見える化され、埋没しない。
・自工程完結という考え方により、「品質は工程内でつくり込む」という意識が向上する。
・不良の再発防止策を考えることができ、その習慣により人材が成長する。
🧒;なるほどです。
👱🏼;特に自工程完結という考え方は、非常に重要なんだ。簡単に言ってしまうと自分の工程完璧に品質を作りこむってことなんだけど、これができると本当に後工程がスムーズになっていくんだ。異常を検知し、標準外の状態を知り、機械やラインが止まる、あるいは止める。そして、管理監督者が真因を見つけ、取り除き、それを標準に組み込むというサイクルを作ることを言うんだ。このサイクルが良い品質、良いライン、良い機械をつくるんだ。
🧒;なるほど。でも、実際に進めていくのは非常に難しそうですね。
👱🏼;そうなんだ。いきなりは無理だ。だから、まず小さいものでいいから今言ったサイクルを作るということに意識集中をするんだ。
🧒;まずサイクルを作る意識ですね。
👱🏼;トヨタ自動車のHPには複数の事例が乗っているよ。ちょっと古い感じがするけど・・。
///////////
無人運転ラインにおける機械による異常の検知(刃具折れ検知)
加工を行うごとに機械が自動で刃具を確認し、異常があったら停止する仕組み
機械加工(刃具折れ検知)
組立ラインでの異常の検知(ひもスイッチ)
人の作業が主体の工程では、異常が発生したら作業者がひもスイッチを引いて定位置でラインを止める
組立作業(ひもスイッチ)
部品選択における誤品取り出し防止(部品選択指示)
複数の種類の部品から1つを選択して組付ける工程に設置されるもので、正しい部品が指示されて、それが確かに手に取られたかどうかが確認できる機構を工夫したもの
部品選択指示
アンドン
「アンドン」は、ラインを効率的に管理するための道具で、関係者に作業や処置を促す情報を表示する。表示が機械異常の場合には担当者は異常処置を行い、職制は原因を調査し再発を防止する。
「アンドン」は、ラインを効率的に管理するための道具で、関係者に作業や処置を促す情報を表示する。表示が機械異常の場合には担当者は異常処置を行い、職制は原因を調査し再発を防止する。
アンドン(電光表示盤)の事例
//////////////
👱🏼;ここから見てわかるように、工夫を積み重ねているよね。いろんな試行錯誤があったはずだ。だから積み重ねるサイクルを作ることがやっぱり大事なんだ。
🧒;そうなんですね。
👱🏼;自働化はの説明はここまでだよ。
🧒;ありがとうございます!内容と何をしなければならないかはわかりました。
👱🏼;そうだね。まずは知ろう。そして実践の積み重ねなんだよ。どちらが先でもいいけど。さて、次回は、カンバンの使い方について説明するよ。カンバンはJITとニンベンのついた自働化を実現するにあたって非常に重要な役割をになっているんだ。大野耐一さんの著書にもページを割いて細かく説明しているんだ。
🧒;そうなのですね!よろしくお願いします。
・・・・・・・・・
今回は自働化について解説をしました。ポイントは”省人化”と”品質の作りこみ”ですね。一人1台ではなく、1人複数台をどう実現するか、また異常を見えるようにしたうえで品質の作りこみを自分の工程でどこまで行えるか。ここの部分をポイントに自分の工程を見てみると改善のヒントが多く隠れていると思います。次回は、日本柱を支えるためのかんばんの使い方について解説します。
次の記事は下記です。
なお、本投稿は大野耐一著「トヨタ生産方式」とカイゼンベースHPの内容に沿って、実体験からの解釈を入れながら対話型で解説をしています。
#製造
#現場
#理論と実践
#ものづくり
#トヨタ生産方式
#リーン生産方式
#改善
この記事が気に入ったらサポートをしてみませんか?