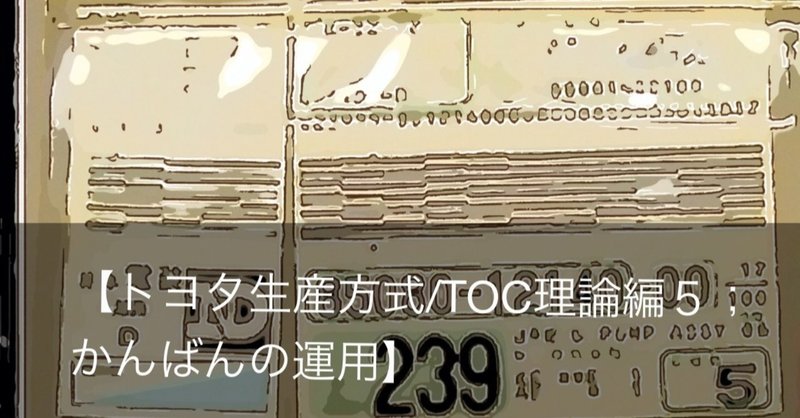
【トヨタ生産方式/TOC編5;かんばんの運用】
*前回までの投稿は上のマガジンに入れています。
大卒で大手素材メーカーの工場に配属された若手の紫耀(しょう)と同じ工場に転勤してきた別部署の中堅社員の管理者の健(タケル)との会話です。(もちろんフィクション?)
先輩に指導を受けながら、トヨタ生産方式について学び、自部署の課題を解決に挑戦するようです。前回の投稿までで、ジャストインタイムとニンベンのついた自働化について学び、今回はそれを支えるカンバンの運用に進むようです。
・・・・・・・・・
カンバンとは、かんばんの運用
👱🏼;おはよう!
🧒;おはようございます。今日は、マガジンの3本目(JIT)と4本目(自働化)を支えるツールかんばんの学習ですね。
👱🏼;その通りだ。じゃあ始めていこう。かんばんとは、製造や運搬に必要な情報が記載された、1枚の紙切れのことだ。君のいう通り、トヨタ生産方式の2本柱であるジャストインタイムとニンベンの付いた自働化を成立させるためのツールの1つだよ。簡単におさらいすると、ジャストインタイムは、「必要なモノを 必要な時に 必要な分だけ」、ニンベンの付いた自働化は、「異常や問題があればその場で止まる、判る」だったね。この2つの柱をカイゼンする過程で、徹底的なムダ排除による原価低減を実現すること、これがトヨタ生産方式の目的だ。
🧒;はい。二本柱を支えるってカンバン。それが紙切れ一つって、すごいですね。
👱🏼;必要な情報が入っていれば、シンプルが一番だ。まずは、かんばんの生い立ちについて説明しよう。かんばんが始まったのは、今から60年以上前の昭和28年頃と言われていて、当時は、自動車工場でも在庫は至る所に山積み状態だったみたい。例えば、鋳造工程から機械加工工程への粗材や、エンジン組付工程から車両組立工程へのエンジンの完成品などです。何万パーツとある自動車工場で在庫が山積みって、現場の混乱が容易に想像できるね。そんな状態に、大野耐一氏が在庫の運搬に関して2つの指示を出したのです。
1つ目は、あらゆる在庫は、後工程が取りに行くまでは運ばないこと。
2つ目は、在庫にはそれが何なのか明示すること。
これが後工程引取りの誕生になるんだ。
🧒;おー、大野耐一さん。すごいですね。というか、先日から興味がわいてきて、ネットで調べたら発明協会のページで写真が出てきました。めっちゃ強面ですよ。こんな人にしごかれたら・・。
👱🏼;相当厳しかったみたいよ。ここでは記載しないけど、大野耐一の「鬼十訓」とかあるみたい。でもそのくらい、自分にも他人にも厳しい人だったからこそ、トヨタ生産方式が出来たんだと思うよ。情にも厚かったといわれている。さて、そのままかんばんの役割について進めていこう。かんばんには、大きく分けて3つの役割があるんだ。
1つ目は、運搬や生産の指示としての役割
2つ目は、目で見る管理としての役割
3つ目は、カイゼンの道具としての役割
それぞれ解説していくよ。
🧒;なるほどです。お願いします。
👱🏼;まず、運搬や生産の指示としてのかんばんだ。かんばんには引取りや運搬指示に関することが記載されており、運搬、つまり次の工程に送るための必要情報がそこに入っているんだ。
🧒;ということは、これが、後工程引き取りタイミングであったり、量をコントロールすることができるのですね。
👱🏼;その通りだ。それと、生産指示情報も記載されているため、前工程はかんばんが外れた分だけ造ればよいため、生産管理が非常に楽になるんだ。とはいえ、かんばんだけで動く工場ってなかなか作れなくて、生産計画とカンバンを併用している現場はあると思うよ。この辺は実践の時、肝になってくるから、よく覚えておいて。
次に、目で見る管理としてのかんばんだ。かんばんが無い時は造らない・運ばないので、造りすぎや運び過ぎを防ぐことが可能になるんだ。また、必ず現物にかんばんが付いていることで、誰が見てもそのモノが何か一目で分かり、現物票としての役割も果たすよ。
🧒;カンバンで生産状況を管理するのですね。
👱🏼;そうそう。次は、カイゼンの道具としてのかんばんだ。かんばんは必要な数のみが記載されており、かんばんに記載されている以外の余分な在庫は運んではいけないんだ。
これによって、不良品が度々混ざっていると、前工程はしょっちゅう不足分を補充しに行かなければいけないよね。つまり、不良品を出した工程が「痛さ」を感じる仕組みにより、後工程に不良を出さないということが推進される。これは自働化の時に話した、自工程完結の考え方につながってくるよ。在庫管理や問題を顕在化するためにも、当然かんばんは役割を発揮する。かんばんの枚数を減らしていくことで、問題が顕在化され、異常が少ない高レベルなライン実現が可能になっていくんだ。
🧒;まさに改善ツールになるのですね。異常の見える化ツールといったらいいですかね。
👱🏼;その通りだ。役割、使い方が簡単に表になっているものがあったから、記載しておくよ。
🧒;ありがとうございます。
かんばんの基本ルールと前提条件
👱🏼;では次はかんばんのルールについて説明しよう。とはいえ、自分の現場で合わせて使えばいいんだど、ベーシックな使い方ということで考えてもらえばいいよ。
🧒;わかりました。
かんばんの主な3つのルール
👱🏼;基本となるかんばんの主な3つのルールを説明するね。1つ目は、「使い始めにかんばんを外し、速やかにポストへ入れる」ことだ。後工程がかんばんを外し忘れ、ポストに入っていないと、前工程は後工程でまだその部品が使われていない、つまり減っていないと考え、次回その分を生産しなくなってしまう。そして欠品やラインストップに繋がってしまうよね。要するに情報の流れが途絶えてしまう。外し忘れが発生しないように、教育がしっかりと出来ていることが重要となるんだ。
🧒;習慣づけですね。
👱🏼;うん。2つ目は、「小刻みに回収する」ことだ。大きなロットで運搬することは、在庫過剰やリードタイムの悪化の原因なるのは分かっていると思う。工程の流れ化のところでやったね。可能な限り小刻みに回収し、在庫低減やリードタイム短縮に繋げることが重要だ。当然ながら、かんばんがポストに溜まる状態は厳禁だ。大ロットになっている証拠だからね。
🧒;なるほど、これまでの知識がだんだんつながってきます。
👱🏼;そう。常につながりで考えていくこと、それを自分で文字や図で起こしていくことで頭の中の体系化につながっていくよ。さて、3つ目は、「等ピッチで回収する」だ。回収ピッチが大きくばらつくと前工程は生産数量のばらつきが増えて、生産量が多くなってしまったら欠品のリスクが高くなり、それを回避しようと余計な在庫を持つことに繋がってしまうんだ。
後工程は、生産の先食いや大きな遅れの後の急激な追い込みは避けなければいけないんだ。
🧒;平準化が重要ということでしょうか?
かんばんの前提条件は、後工程が平準化されていること
👱🏼;その通りだ。かんばんの前提条件は、後工程が平準化されていることなんだ。平準化はJITのところで勉強したね。事前の生産見込みを確認し、それに対応する変動の大きさを客先(工程間)できめておく、つまり生産数量の幅を可能な限り安定化させるという考え方だ。この平準化は、ジャストインタイム生産が成立するための前提条件として非常に重要なんだ。
🧒;いまならすごくわかます。JITや自働化いっても万能ではなく、お客や前工程が無茶苦茶な生産計画を強いれば、どんなに一つの製造工程がしっかりしても全体が成り立たないですね。
👱🏼;そう。そうなんだよ。だから意識改革が必要だし、全員の考えが揃っていかないとなかなか実現は難しい。
🧒;なるほど。知れば知るほど、やりがいありますね。
カンバンの種類
👱🏼;いいね。さて次にカンバンの種類について解説するよ。
🧒;はい。これまでが流れで具体的にどうしていくかということですね。
👱🏼;かんばんは、基本は2種類あるんだ。1つ目は、引取りかんばんだ。これは運搬用のかんばんだ。引取りかんばんには、“工程間引取りかんばん”と“外注部品納入かんばん”があるんだ。当然、自分の会社で製造して次の工程に送る部品に関しては“工程間引き取りカンバン”で、そうではなく、他社から部品を納入して直接、次の工程に入れるものには“外周部品納入カンバン”を使うんだ。それぞれのカンバンでわけるんだ。自社ですべて完結している現場は、外注納入カンバンは不要だね。全部のカンバンの例は出しきれないけど、引き取りカンバンのイメージをがコンサルソーシングさんのHPにあったから記載しておくよ。
🧒;なるほど。
👱🏼;2つ目は、仕掛けかんばんだ。まさに仕掛ける(準備するかんばんだ)さっきは、引き取りカンバンは工程間で使用していたけど、仕掛けかんばんは工程内で使用するものだ。仕掛けかんばんには、“工程内かんばん”と“信号かんばん”がある。“工程内かんばん”は工程に引き取られた量を引き取られた順序で後補充生産するために使うかんばん、つまり工程内で必要数量を伝達するカンバンだ。“信号かんばん”はロット単位の情報を伝えるかんばんで、ロット生産工程の仕掛けに用い、一定量になった段階でかんばんが外れロット生産指示となり、在庫が無くなるタイミングと生産が完了するリードタイムを見比べながら仕掛けを行うんだ。つまり、ロットの大きさを決めるカンバンなんだ。
🧒;工程間で運搬するもの、運搬してから工程内で効率よく動かすものの2種類ということですね。
👱🏼;その通り、基本は2種類なんだ。それとその他にも、いくつかかんばんの種類が存在するよ。“プールかんばん”もその1つだ。後工程のバラツキにより、自工程の作業が振られてしまい、ロスが大きくなり過ぎる場合に使用するんだ。つまりバラツキ吸収のために、通常とは別に追加するかんばんなんだ。発行する際には、後工程へのカイゼン要求と共に、いつまで使用するかを明確にする必要がある。それと、”非常かんばん”というものもあるんだ。設備に安定可動する実力が無いことで、後工程が欠品になる場合、特別に追加するバックアップ在庫用のかんばんだ。非常かんばんの場合は、上位職の承認許可や、日時、どの製品に使用したかを記録する必要があります。これらのかんばんはあくまで期間限定の臨時で使うかんばんなんだ。
🧒;なるほど。基本以外のかんばんを使う必要があるとなると、どこかに異常やアンバランスが存在しているってことになるのですね。これすら、異常の見える化になっているんですね・・。
引取りかんばんと仕掛けかんばんの運用方法
👱🏼:そうなんだ。最後にかんばんの基本である、引取りかんばんと仕掛けかんばんの運用方法について、自動車の組立ラインを例に説明するよ。
① 後工程の運搬者は、必要な数の引取りかんばんと空のパレット台車に乗せて、前工程の部品置き場にいく。その時、後工程の生産のためはずされた引取りかんばんが、事前に定められた一定の枚数だけ“引取りかんばんポスト”にたまっている。あるいは、30分ごとなど時刻を決めて定期的に引き取りに行く。
② 後工程の運搬人がストアAで部品を引き取ると,パレット内の部品に付けられている生産指示かんばんを取りはずす。そしてこの生産指示かんばん「かんばん受取りポスト」に入れる。空のパレットを前工程が指定し場所においておく。(次の器になる。)
③さらに 運搬人は、自分が取りはずした生産指示かんばん1枚につき、引取りかんばん1枚をかわりに付けておく。これが、部品と共に後工程に行く。
④ 後工程で作業が始まると、引取りかんばんは、また、引取りかんばんポストに入れられて①に戻る。
🧒:なるほど。引き取りカンバンと仕掛けカンバンのイメージができました。
👱🏼:最初に行ったけど、実際の運用時には複数の工程であったり、製造リードタイムの違いなど、色々な制約があり、状況や現場によって適応の仕方は違うんだ。てか、全てきちんとできたらトヨタだよ。(笑)そんな工場めったにないからね。ゴールイメージをまず明確にして自分たちでできる部分からステップを作っていくことが重要だ。
🧒;なるほど、そして最初のゴールイメージが達成出来たらもう一度勉強して次のゴールを考える。そこからまたカイゼンを回していく格好ということですね。
👱🏼:その通りだ、これも地道でしょう。結局時間の積み重ねが大事ということがわかってきたかな?これでトヨタ生産方式の大まかな考え方については終了だ。次回は、トヨタ生産方式の最後に7つのムダについてに解説するよ。要するにこれまで説明してきた内容はこの7つのムダをカイゼンするためなんだ。JITと自働化でどんなムダが省けるか認識していこう。トヨタ生産方式は、ものづくりすべてを語っているから、、まだまだ、学ぶことあるんだけどきりがないから、次回でトヨタ生産方式の解説はいったん終了だ。
🧒;ですね。ここまででもだいぶボリュームがありました!よろしくお願いします。
・・・・・・
今回は、カンバンについて解説しました。長々と書いてしまいましたが、トヨタ生産方式での運用方法はまず頭に入れておくのがよいと思います。そして、自分の工程でどこまで対応させるべきか検討し、難し考えすぎず、まず、“仕掛品自体の情報・状態の見える化”を実施することをお勧めします。そこからその情報をどう伝達させるかに発展させていけばオリジナルのカンバンの運用が見えてくると思います。
さて、次はトヨタ生産方式の最後に7つのムダについて解説します。これまでの解説が何のムダにつながっているか考えながら読んでいただければと思います。どうぞよろしくお願いいたします。
本投稿は大野耐一著「トヨタ生産方式」とカイゼンベースさんのHP、コンサルソーシングさんのHPで解説されている内容に沿って、実体験からの解釈を入れながら解説をしています。
次の記事は下記です。
#製造
#現場
#理論と実践
#ものづくり
#トヨタ生産方式
#リーン生産方式
#改善
#かんばん
この記事が気に入ったらサポートをしてみませんか?