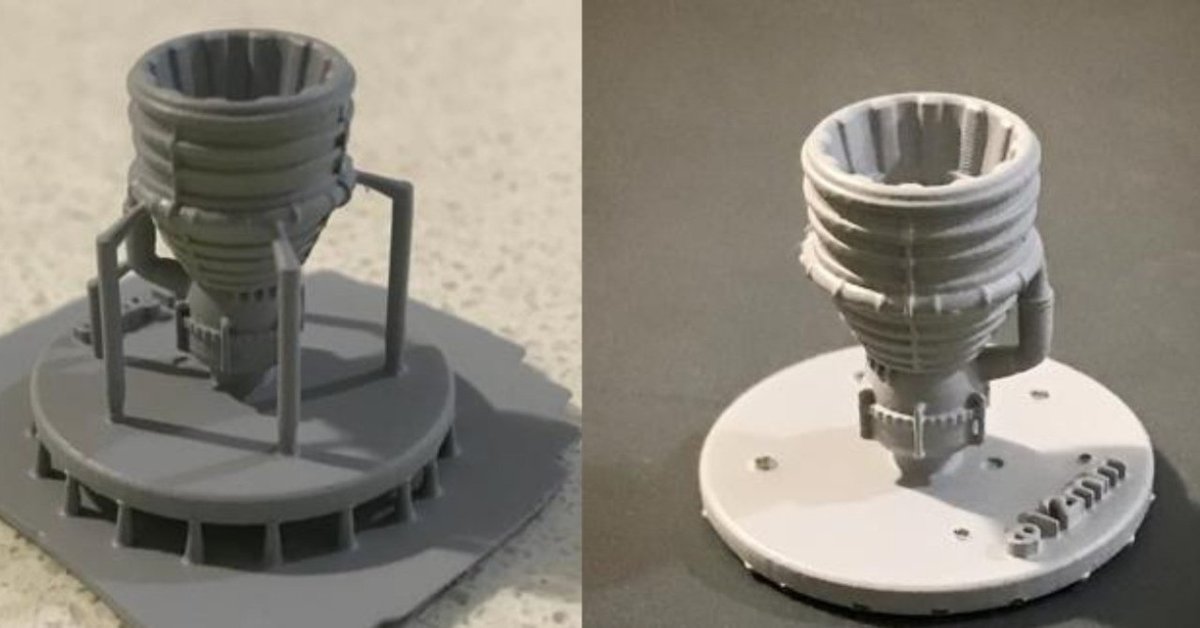
3Dプリンターでプラモを作る編[②サポート材の設置の工夫]
今回の記事では、サポート材設置に関する内容です。
下記の記事の続編となりますので、まだ読んでいない方は、先ず下記のリンクから記事を読んでみてください。
本題です
出力したモデルの出来具合はサポート材に影響する場合が多々あります。そのため、パーツに応じて常にサポート材設置の工夫が要求されます。今回は、私が実施しているサポート材設置時の注意点や工夫点の一部を紹介していきます。
1. サポート材設置面は、板厚を最低1mm以上にする
結論から言うと、サポート材の設置面の板厚が薄いと、サポート材の除去時に割れてしまうためです。もちろん、サポート材の太さを変更してあげれば、極力出力品への負荷を軽減することができますが、限度があります。どうしても割れてしまう場合は、本体の板厚を増やしてあげるほうがいいでしょう。
どうしても1mm以下がいい場合は、1mm以上で出力し、仕上げの研磨で板厚を薄くしています。
2. 広がり防止のための内部サポート材を付けるべし
出力品の材質や厚さにもよりますが、1次硬化時、もしくは2次硬化時に下図のように広がってしまう(変形)パーツがあります。多くの場合は樹脂を使っているため、このような変形は避けられません。
板厚を厚くすればいいのですが、板厚が限定されている場合はどうすれば、この変形の影響を軽減できるのか?
私が実践しているのは下図のように内部にサポート材を設置しています。このサポート材はモデリング時にマニュアルで設置する必要があります。広がりや変形を防止したい方向に対し内部サポート材を設置してあげます。
こうすることで、硬化時の変形を極力抑えることができます。2次硬化が完了した段階で内部のサポート材を外します。(ポイントとして、通常のサポート材を外した後に、内部サポート材を外しましょう)
3. 分割面を貼り合わせてサポート材跡を消すべし
サポート材を設置する上で一番厄介なのが、サポート材の除去跡のせいでパーツの仕上がりが下がることです。また、表面処理をしたせいで、ディテールが消えてしまうことがあります。ただの表面処理ならまだディテール部の深さや厚さを増やしてあげればよいのですが、サポート材跡の表面処理は結構磨く必要がでてきます。
例えば、下図のようなピンもしくは円筒形のパーツを使って説明します。
このパーツを出力するために下図の箇所にサポート材を設置すると、その面にある、面取りや突出部のディテールが、表面処理時に消えてしまうもしくは歪んでしまいます。
ピンにしろ円筒形のバーツにしても、性質上隠すことができない箇所が多いため、プラモデルとしては大きな問題となります。そのため、私は下図のように2つのパーツに分割して、それを最終的に接着剤等で接合するとういう方法を使っています。
こうすることで、外側のディテール部を傷つけることなく仕上げることができます。(簡単な全体の表面処理は実施します)
今回の記事ではここまでにします。機会があれば、また実際に使っているテクニックを紹介していきます。
4. サポート材の除去を効率的に行うために
サポート材への対策は3Dプリンターを使う上で最大の課題となってきます。サポート材除去を効率的に行うためには、不要なサポート材を付けないようにすることです。何度か実績を積み重ねることでこれらのスキルは上達すると思います。
又、近年ではサポート材の除去に特化したツールが販売されています。そちらを使ってみるのも手かもしれません。
5.さいごに
今回はサポート材に関するテクニックや、仕上げのクオリティを上げる方法を紹介しました。何かご質問等ございましたら、コメント欄にご記入ください。
最後まで読んでいただきありがとうございました。
これからも何か役立つ情報を発信していきますので、フォローやいいねをよろしくお願いいたします。
又、ツイッターでは最新のモデリングの進捗をUPしていますので、よかったフォローをよろしくお願いいたします。
この記事が気に入ったらサポートをしてみませんか?