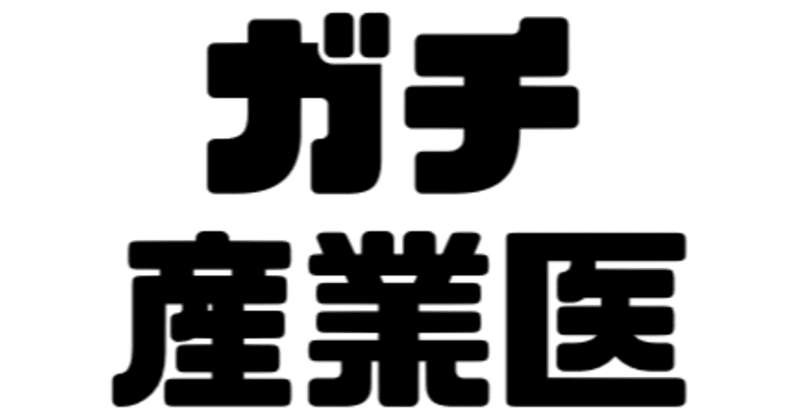
48.リスクアセスメントの落とし穴
はじめに・法的背景
我が国では、労働災害は昔よりも減ってきているとは言え、今なお重篤な労働災害が起き続け、その減少は鈍化しています。これは、設備等の大型化、高エネルギー化、工程等の多様化・複雑化、混在作業が広がっていること、未熟練労働者に対する安全衛生教育が不十分となっていること、事業者の安全衛生への意識が不十分であることなどから事業場における安全衛生管理が低調となっていることが要因として指摘されています。また、生産工程の多様化・複雑化が進展するとともに、新たな機械設備・化学物質が導入されていること等により、労働災害の原因が多様化し、その把握が困難になってきていることも要因としてあげられます。2011年には、印刷会社において未規制物質による胆管がんの発生もあり、労働安全衛生関係法令に規定される最低基準としての危害防止基準を遵守するだけでなく、さらに事業者による自主的な安全衛生管理が求められています。(参照:「リスクアセスメントの目的と意義」)
平成 18 年の労働安全衛生法等の改正により、リスクアセスメントに係る様々な事項が規定されました。
(1)リスクアセスメントの実施が努力義務化
(2)安全・衛生委員会の付議事項に追加
(3)総括安全衛生管理者、安全管理者、衛生管理者の業務に追加
(4)安全管理者、職長教育の教育内容に追加
(5)機械等の設置に伴う計画届の免除要件として明記
法的には労働安全衛生法28条と、労働安全衛生規則第24条に規定され、その内容は指針に細かく示されています。
(事業者の行うべき調査等)
第二十八条の二 事業者は、厚生労働省令で定めるところにより、建設物、設備、原材料、ガス、蒸気、粉じん等による、又は作業行動その他業務に起因する危険性又は有害性等(第五十七条第一項の政令で定める物及び第五十七条の二第一項に規定する通知対象物による危険性又は有害性等を除く。)を調査し、その結果に基づいて、この法律又はこれに基づく命令の規定による措置を講ずるほか、労働者の危険又は健康障害を防止するため必要な措置を講ずるように努めなければならない。ただし、当該調査のうち、化学物質、化学物質を含有する製剤その他の物で労働者の危険又は健康障害を生ずるおそれのあるものに係るもの以外のものについては、製造業その他厚生労働省令で定める業種に属する事業者に限る。
2 厚生労働大臣は、前条第一項及び第三項に定めるもののほか、前項の措置に関して、その適切かつ有効な実施を図るため「必要な指針」を公表するものとする。
上記の「必要な指針」が「危険性又は有害性等の調査等に関する指針」です(下はリーフレット)。
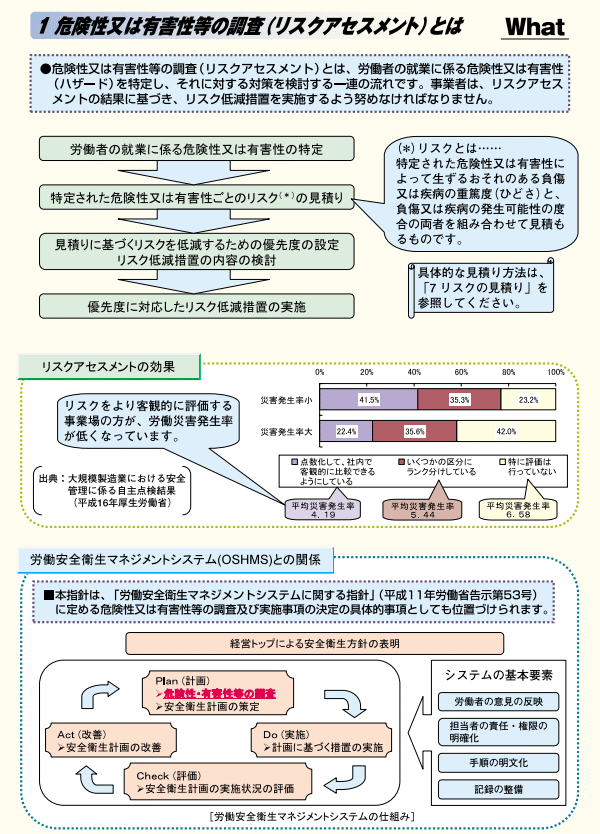
「平成30年の労働安全衛生調査(厚生労働省)」では化学物質を取り扱う際のリスクアセスメントの実施状況は以下のように示されており、リスクアセスメントの実施状況は低調のようです。
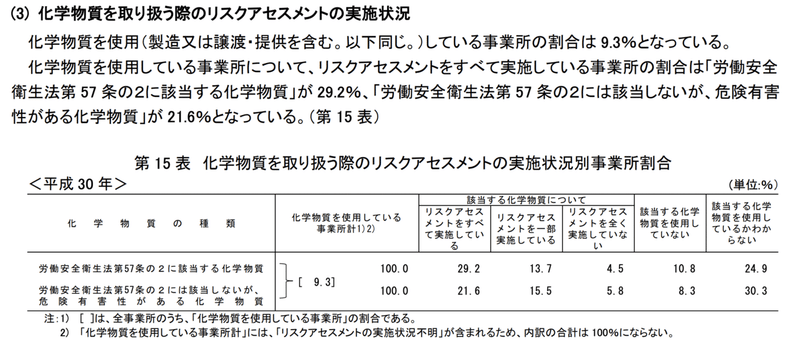
このような背景から多くの産業保健職がリスクアセスメントに関与しているのではないかと思われます。そこでこの記事では、リスクアセスメントや、リスクマネジメント、リスクの取り扱い方について落とし穴として説明していきます。
リスクゼロの落とし穴
働く以上は何らかの安全衛生(健康)上のリスクが発生します。だからこそ安全衛生活動を行うのですが、実際にはそれぞれの目指すべき安全やリスクの定義が異なっていることが往々にしてあります。国際的には安全はISO/IEC GUIDE 51:2014で「許容できないリスクがないこと」“freedom from risk which is not tolerable”と定義されています。そして、リスクには許容可能なリスクと、許容可能ではないリスクに分けられます。安全衛生活動において、リスク許容可能なレベルにまでリスクレベルを低減することが求められます。許容できないリスクがない安全な職場とすることで、安全に働くことができます。しかし、ここでリスクゼロを目指すこと(全てのリスクに対策をすること・「リスクを許容する」という選択をしないこと)は、結果的には過剰/過少な対策につながったり、労災隠しや、優先順位を間違えたり、それがひいては防ぐべき事故が防げないといった事態につながってしまいます。リスクといっても、許容できるリスクと、許容できないリスクがあるということにご注意ください。(参照:「労災ゼロの落とし穴」)
参考になりますのでこちらもどうぞ
岸本充生, 平井祐介 ISO/IECガイド51における「安全」の定義の変更を巡って 日本リスク研究学会誌 2015, 24(4): 239–242 (2015)
許容できないリスクの落とし穴
そもそも「許容できないリスク」”not tolerable risk”とはいったいなんでしょうか?ISO/IEC GUIDE 51:2014では、この“tolerable risk”は下記の要素から決まるとされています。
―社会の現在の価値観
―絶対安全という理想と達成可能なものの間の最適なバランスの探求
―目的への適合性や費用対効果といった要素すなわち,安全を定義しようとすると,客観的・科学的に一意に定められるものではなく,社会的合意に基づく約束事にならざるをえないこと
労働安全衛生マネジメントシステムでは、「ALARP: as low as reasonably practicable」という概念があります。

(資料2より)
許容レベルは、ほとんどすべての労働者に対して健康障害が生じないレベルと定義され、化学物質の場合には「ばく露限界値(TLV: Threshold Limit Values)」が設定されています。しかし、この設定は”ほとんどすべての労働者”が悪影響がみられないレベルであり、”すべての労働者”ではないことに注意が必要であり、リスクは必ず残ります。労働者によっては感受性が高い(例:皮膚感作性物質に対してアレルギー症状があるなど)、脆弱性がある(例:腰痛を発症しやすい、夜勤で不眠が出やすいなど)という労働者側の要因もあります。化学物質や騒音などにおいては個人ばく露レベルや作業環境濃度の許容レベルを「数値」として線引きしてはいますし、リスクアセスメントは手法としてツールを使うことで数値化して許容できるか許容できないかを決めることになります(例:リスクアセスメント等実施支援ツール)。しかし、それはあくまで便宜上の線引きであり、クリアカットに線引きできないことの方が圧倒的に多く、許容できるか/許容できないかの線引きは非常に難しいものです。企業においては、最終的に事業者が許容できるか/許容できないかを決め、リスク低減の優先順位や程度を決めて、リスクマネジメントを行うということになるでしょう。その過程で、許容するかしないかは当事者である労働者(+そのほかのステークホルダー)ともコミュニケーションが必要になるでしょう。当然、専門家の関与が必要になるケースも出てきます。しかし、すべてリスクを満遍なく低減することは難しく、どのリスクを許容するかしないかを決めることがリスクマネジメント上はとても重要になります。企業で行われるリスクアセスメントを含むリスクマネジメントでは、このリスクへの考え方の理解が不十分なことが多いですので、産業医としても十分に理解した上で関与していく必要があります。
参考:作業環境許容濃度(ACGIH)、
補足:有害物質管理の基本戦略
Step 1 健康障害リスクを許容レベル以下にする
Step 2 例外的な健康状態の労働者に対して、適正配置で対応する
Step 3 労働者の職務適性を向上させるための健康増進の取組を実施する
Step4 Step 1/2でカバーできなかった健康障害を発見する
後追い型のリスクアセスメントの落とし穴
リスクアセスメントは、労働災害防止のための予防的手段(先取り型)であり、従来までの自社で発生した(他社で発生した)労働災害から学び、労働災害発生後に行う事後対策(後追い型)とは異なる取組みです。つまり、本来は労働災害が起きた後に行うものではありません。しかし、実際には労働災害が起きてから事象のリスクアセスメントを行っていることがあります。リスクアセスメントの方法としては本来のやり方ではありません。また、労働災害が発生した場合に、事前にリスクアセスメントが実施されていなければ、企業としてのリスクアセスメントのやり方自体を見直す必要がありますし、リスクアセスメントを実施していたのであれば、その事象が事前に許容できるリスクレベルと判断されていたのか、許容できないリスクと判断されていたのかが重要です。前者であれば対策は不要ということになりますし、後者であれば許容できないリスクを対策(リスク低減)せずに放置していたということになります。
一般的には法令は後追い型になり、事故や健康障害が起きてから規制するという順序になります。法令順守をしていても、健康障害は防ぎきれません。まだ記憶に新しい胆管がんや膀胱がん発生の労災のように、法令では規制できない未知の化学物質も多く存在します。新しい働き方で新しい健康障害も発生することもあるでしょう(例:VR・ARを使った業務や、宇宙での業務など?)。だからこそ、リスクアセスメントを行い、自主的に先取り型で事故や健康障害を予防することが大切になります。
ヒヤリハットの落とし穴
ヒヤリハットとリスクアセスメントを混同している場合が多くあります。しかし、ヒヤリハットについてもリスクアセスメントを実施していたか、実施していなかったが重要です。ヒヤリハットした事象について、リスクアセスメントが実施されており、そのアセスメント結果が許容できるとされていれば、その事象が起きることも許容されると判断した、ということになります。その場合には、その事象を起こさないように安全行動を心がけることが必要でしょう。一方で、アセスメント結果が許容できないとされていた場合には、その事象は起こしてはならないことになります。直ちに対策を行うとともに、なぜそのリスクが対策されずに放置されていたのかを検討する必要があります。また、ヒヤリハットした事象についてリスクアセスメントが実施されていなければ、それはリスクアセスメントそのもののエラーです。リスクアセスメント手法を見直しましょう。
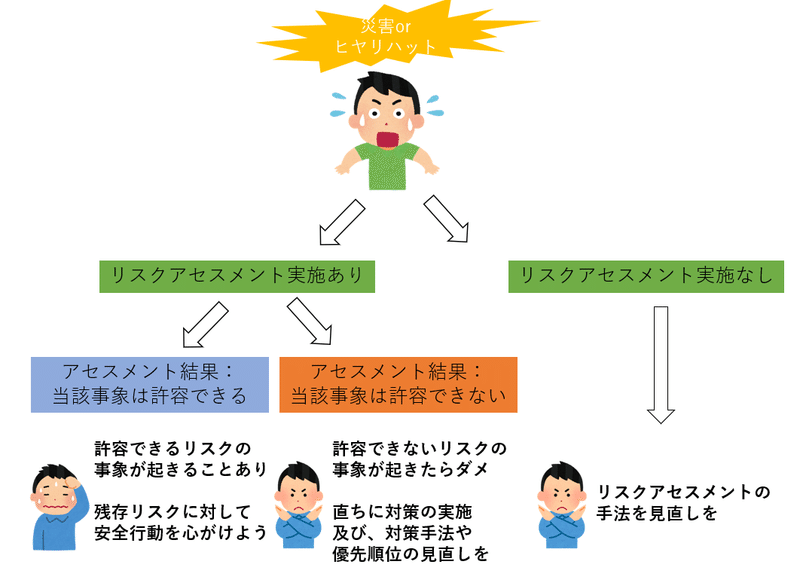
KYTの落とし穴
「KYT」とは、危険予知訓練の頭文字をとったもので、作業や職場にひそむ危険性や有害性等の危険要因を発見し解決する能力を高める手法です。このKYTもリスクアセスメントと非常に混同しやすいものです。KYTは基本的には許容できないリスクが存在しない現場(許容できるリスク(残存リスク)は存在する現場)で実施されるものです。許容できるレベルのリスクのハザードは職場に残存していますので、そのハザードに対して各個人や職場レベルで気をつける・不安全行動をしないように、注意を促すためにKYTを行うというものです。あくまで訓練(トレーニング)であり、リスクの評価やリスク低減対策ではない点に注意してください。許容できないリスクが職場にあれば、安全とは言えませんので、本来は作業を行うべきではありません(そのリスクを許容したと捉えれば安全と言えるかもしれませんが)。そして、許容できないリスクは、各個人の裁量ではなく、事業者の責務としてリスクマネジメントするということにも注意が必要です。
車を運転する場合には、事故を起こすリスク(起こされるリスク)はゼロになりません。運転している方は、その選択をした時点で、事故のリスクは望まずとも許容しているということになります。最悪の自体死亡事故になるとしても、そのリスクを理解し許容した上で運転しているのです。その上で、事故のリスクを少しでも下げるために、道路に数多く残存するリスク(許容したリスク)に対して、ヒヤリハットしたら改めて気をつけることや、危険予知することで安全運転を心がけるということになります。
リスクマネジメントの落とし穴
リスクマネジメントは以下のような要素で構成されています。
A.リスクアセスメント
リスク特定
リスクの分析
リスク評価(対策の要否と優先順位の決定)
B.リスク対応
リスク回避
リスク最適化(リスクの低減)
リスクの移転
リスクの保有
C.リスク受容
D.リスクコミュニケーション
あくまでリスクアセスメントとは、最初の段階に過ぎないことに注意が必要です。アセスメントしたリスクにどう対応したか、どのリスクを受容するのか、どうリスクコミュニケーションしたのか、ということはリスクアセスメントと同じように重要です。この一連の流れが実施されていることを産業医としてサポートしていくことが求められます。
おまけ
カナダ心臓血管学会(Canadian Cardiovascular Society)が1992年に初めて発表した「Risk of Harm Formula」は、突然の心臓イベントに見舞われたドライバーのリスクを定量化することを目的として作成されました。これは突然運転不能になる持病を持った方が職業運転していいかどうかを評価するためのもので、次の式で「社会的に許容されるRH」を0.00005以下と設定し、それ以下であれば運転が許可されるということになります。
RH= TD x V x SCI x Ac
RH : Risk of Harm, TD : the proportion of Time of Driving(年間運転時間), V : the type of Vehicle(車両のタイプ), SCI : risk of sudden incapacitation(突然運転不能になる年間確率), Ac : the probability of injury or accident after SCI(突然運転不能により受傷または事故を起こす確率:0.02で固定)
健康事象は常に不確実なもので、誰しもが運転不能になるリスクを持っています。その中で、どこかで線引きをしなければ働くこと(運転すること)はできなくなってしまいます。社会はどこかで線引きをしてリスクを許容していく必要があると言えます。また、事故が起きてしまった際の補償は別の問題としてあります。運転する際の事故のリスクは絶対にゼロになりません。ゼロにならないリスクはなんらかの形で必ず許容しなければなりません。
・Interactive Risk of Harm Calculator(RHの計算サイト)
・心臓植込み型デバイス植込み・失神およびてんかん患者の自動車運転
参考資料
https://www.hse.gov.uk/foi/internalops/hid_circs/permissioning/spc_perm_37/index.htm
2. 【ISO45001】6.1.2.2 労働安全衛生リスク及び労働安全衛生マネジメントシステムに対するその他のリスクの評価(2) (J-VAC)
この記事が気に入ったらサポートをしてみませんか?