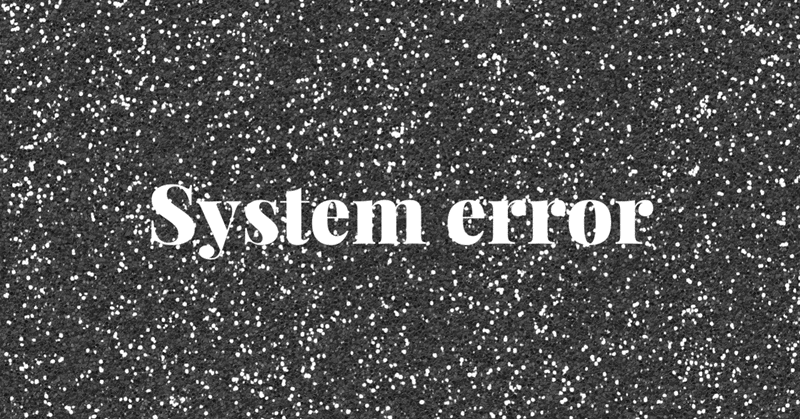
【経費大幅削減メソッド】消耗品費の高止まりはシステムエラー
こんにちは。
森永の牛乳プリンが大好きな『Factory Labo』です。
今回は製造業以外の業種の方にも深く関係のある、経費についての話をしようと思います。
製造業の消耗品費(主に消耗工具)についての話になりますが、皆様それぞれの業種の経費、もしくは家で使う日用品にかかるお金に置き換えて読んでいただければ製造業以外の方にも役に立つ内容になっています。
▼誤った認識
製造業で働く中間管理職の方や現場作業者の方、上司から
「先月の消耗品費(消耗工具費)かかり過ぎているぞ。」
なんて言われたことはないですか?
もしくは経営者さん、管理職さん言ったことないですか?
これは数字を眺めた気づきを声高らかに発しただけであり、この発言には全く改善効果はありません。
これを言われた現場の人間がとる行動は、大概が買い控えだからです。
消耗品というのは文字通り消耗する訳ですから、この対応は問題の先送りであり一切改善されることはありませんよね。
つまり一定サイクルでこの流れを繰り返すだけなので、全くの無意味なのです。
そもそも消耗品費というものは必要経費なのです。
つまり消耗品費がかかり過ぎてしまう原因が、経費に対する意識等といった人間の行動に起因するものだという考え方がそもそも間違いなのです。
▼システムエラーと捉える
では消耗品費の高止まりの原因は何かというと、ずばり「システムエラー」です。
重要なところなので2回言います。
人間の行動が原因はなく「システムエラー」です。
これは多くのケースに当てはまることなのですが、問題に対する対策を人間の行動に求めても大概が失敗します。
ダイエットのために明日から食事制限をする、と同じくらい大概失敗します。
安全衛生のリスクアセスメントという言葉をご存知でしょうか?
リスクアセスメント(英: Risk assessment)とは、リスク特定、リスク分析、リスク評価を網羅するプロセス全体を指す。 引用 Wikipedia
わかりやすい言葉に置き換えると、危なそうな場所や作業を洗い出し、
それぞれどんな怪我が起こりうるか、起こりうる可能性はどの程度あるかを総合的に判断し、危険度ランク4段階に評価づけをする作業です。
通常リスクアセスメント後、危険度の高い作業にリスク低減処置を行います。
そしてこの時取るべき対策には優先順位が存在します。
①危険な作業の廃止、変更(危険そのものの排除)
②工学的対策(安全装置など機械を使った対策)
③管理的対策(マニュアルの整備、立ち入り禁止処置)
④個人用保護具の着用(安全眼鏡をしましょうね!など)
可能なら①の対策、無理なら②、それも無理なら③、どれも無理な場合やらないよりはいいというレベルで④があります。
一番優先度の低い対策が人間の行動による対策です。
想像してみてください。
安全眼鏡をしましょうと言っても必ずしない人がいますよね。
安全衛生の観点でも、人間の行動改善を対策とする事は下策とされ、期待値や確実性は薄いと考えられているのです。
少し話が逸れてしまいましたが、要は経費管理に関しても人間の意識や行動を改善する事は対策として下策であり、そこを原因と考えるのは間違いなのです。
では何が原因と捉えるべきか。
また、どんな対策を取るべきか。
答えはシステムエラーと捉え循環型の仕組みを構築するべきなのです。
実際何をどうすれば良いのかわからない方も大勢いらしゃると思いますので、私が過去に取り組んだ具体的な対策を詳しく解説、紹介します。
経営者の方や管理職の方、ぜひ取り入れてみてください。
ちなみにこの対策は仕組みですので、一度導入してしまえば人員の異動があってメンバーがかわろうとも変わらず効果を発揮し続けてくれます。
▼3つの大きな効果
今回お話しする具体的な対策には、3つ大きな効果があります。
これは仮説や見込みではなく、私が実際に実施した結果得られた効果の紹介です。
まず一つ目ですが、『消耗品の在庫を定量管理出来る事』です。
必要な時に物がなかった、なぜかこれだけ異常にたくさん在庫がある、といったことがなくなります。
つまり機会損失や納期遅れのリスク低減にもなりますね。
次に、本来の目的である『消耗品費を安定的かつ継続的に最小限に抑えられる事』です。
この「安定的かつ継続的」という部分がポイントです。
多角的にアプローチすることでこれを実現します。
最後に三つ目が、『安定的に最小限に抑えた消耗品費を継続的に更に削減していける事』です。
改善効果の高い品目が判別でき、毎月この改善効果の高い品目に対して対策をとることをルール化する事でこれが実現します。
「購入単価を50%削減した!」といっても内容が「月に1回しか買わない100円のものを50円で買えるようになった」では意味がありませんよね。
効果金額の大きい品目をしっかりと選定出来ることが重要です。
▼3つの事を実施する
ではいよいよその具体的な方法を、順番に説明します。
これから説明する3つのことを必ず順番通りに取り組んでください。
〜その1〜消耗品置き場を集約する
まず初めに、消耗工具置き場をチームや部署につき1カ所に集約してください。
「動線が伸びる!」、「このドリルはここの機械でしか使わないからここに置きたい」などと言った意見が必ず出てくると思いますが1カ所に集約です。
「毎日30分作業時間が伸びてしまう」といったレベルで作業効率が落ちない限り例外は作らないで下さい。
1つ例外があると2つ目、3つ目の例外が高確率で発生し、例外が増える事でシステムが破綻するからです。
作業性を十分に考慮した場所に工具棚を設置した後は、全ての引き出しにテプラなどでラベリングをします。
基本的には工具毎に引き出しを割り当ててください。
ちなみにここで加工用途や工具の種類などによって色分けすると、より見つけやすくなり作業性は少し向上します。
例えば炭素鋼用の工具は白のテプラ、ステンレス用の工具は青のテプラといった感じですね。
またこのタイミングで、用途が似たような工具でそれぞれを在庫しておく必要性の低いものはどれか1つに選抜してください。
ここで選抜されなかった方は今後発注しないだけで、処分せず優先的に使い切りましょう。
さらに、この1カ所に集約している作業の際、必ず不動在庫となっている工具が出てきます。
それらには引き出しは割り当てず、思い切って処分してください。
もし高額で処分したくない場合や、今後使用する可能性が多少ある場合はそれらを1つのケースにまとめて保管しておきましょう。
繰り返しになりますが、工具棚の引き出しに定位置がある工具、保留工具保管ケースに入れる工具、このどちらにも該当しない例外は作らないでください。
重要ポイント
・例外は極力作らない。
・消耗工具在庫を集約することで在庫品目数(種類)を最小限にする。
・ジャンル分け、ラベリング+色分け→引き出しを開けずに何がどこにあるかひと目で分かるようにする。
〜その2〜かんばん管理システム
有名なトヨタ自動車の「かんばん方式」の応用で、工具を定量管理するための仕組みになります。
まず〜その1〜で集約した工具全てに「かんばん」を作成します。
1、大きさは名刺より小さい程度のサイズ。
2、メーカー名を記載。
3、工具の品名を記載。必ず特定の品目を指す詳細な品名を記載してください。
4、1回の発注でいくつ発注するかを記載。
5、残りいくつになったら発注するかを記載。
6、購入先(発注先)を記載。(私は●シールで識別する方法を採用しています)
7、ラミネートする。
この「かんばん」は先ほどの工具棚の引き出しに、工具と一緒に入れておくものになります。
ちなみに実際に私が作成し運用しているものがこちらになります。
汚くてすみません。
初めは文字も印刷していましたが、変更がある度にかんばんを作り直すのが手間がかかっていました。
そこで文字を印刷しないかんばんを作成し、上記2〜5の項目をテプラで貼り付ける方法に切り替えました。
こちらは変更頻度に応じてそれぞれに合った方法を選んでください。
また、6の購入先は丸いシールを使って識別しています。
これにより購入先変更の対応がシールを貼り替えるだけで済みます。
別途シールと購入先を紐付ける一覧が必要にはなりますが、、、
次に発注指示を出す際にこのかんばんを入れる入れ物を用意します。
ちなみに私は引き出しを用意し、購入先毎に割り当てました。
先ほどの発注先識別の丸いシールを同じように引き出しにも貼り、同じシールの引き出しにかんばんを入れるというシンプルルールです。
ちなみにこの時、必ず「発注依頼」と「注文中」の2つを設けてください。
これをすることで注文状況が追えるようになります。
運用時のかんばんの動きが下図のようになります。
重要ポイント
・全ての消耗工具分作成する。
・誰が見てもわかるように詳細に記載する。
・追加や作り直しの際の手間を最小限にする(テプラの活用)
〜その3〜購入品管理
みなさんの会社には必ず購入品費を管理する仕組みがあると思います。
その仕組みで以下の点を確認してみてください。
1、個別に最終購入日が検索出来るか。
2、個別に最終購入時の単価、購入先が検索出来るか。
3、個別に今までの総購入数が検索出来るか。
4、1〜3が多い順に並び替えが出来るか。
この4つが出来ると、現場の人間は最大効果が得られる活動を常に取ることが出来ます。
もしあなたの会社のシステムが上記項目が出来ない場合、システムの改良を検討してみることを強くお勧めします。
多少の費用がかかったとしても、消耗品費の削減で必ず減価償却出来ます。
なぜこの4項目が出来るということが重要かというと、
1の項目では回転(循環)のいい工具と悪い工具が分かります。
最後に購入したのが何年も前の工具を商社と価格交渉し単価を下げても購入頻度が低ければ経費削減効果は期待出来ませんよね。
ちなみに購入回数だけでは、以前は頻繁に購入していたが最近は購入しなくなった工具が判別出来ません。
つまり改善効果の高い品目の判別に効果があり、3の項目と合わさることでより精度の高い判別が可能になります。
2の項目では今まで購入していた物を別な商社から購入する際、明確に比較が出来ます。
いつでも相見積もりが出来るということです。
初めのみ相見積もりをしてその後は他の商社の見積もりはとったことがない、といったことありませんか?
あらためて相見積もりをすると購入単価が下がるケースは非常に多いです。
3の項目では購入頻度の高い工具がまずはわかります。
そこに単価をかけることで消耗品費の中で高いウエイトを占めるものを洗い出すことが出来ます。
さらに4の項目でランキング形式にしてしまいます。
つまり、工具の再選定や相見積もりで単価を下げることで、効果金額が大きい順に並び替えることが出来るということです。
「毎月この上位の中から1つに絞り改善を行う」などのルールを作ってしまえば継続的に消耗品費を削減出来るでしょう。
*ちなみに安価に購入品管理システムを提供出来ないか、開発検討中です。
重要ポイント(確認項目のコピペです)
1、個別に最終購入日が検索出来るか。
2、個別に最終購入時の単価、購入先が検索出来るか。
3、個別に今までの総購入数が検索出来るか。
4、1〜3が多い順に並び替えが出来るか。
▼システムの一人歩きが理想
元々このやり方は私が消耗工具の管理発注を担当していた頃に、
1、余剰在庫を持たないように管理する。
2、欠品がないように管理する。
3、消耗品費を最小限に抑える。
これらに費やす時間的コストに嫌気をさしたことが、考案したきっかけです。
ですので基本的に上記3つに費やす時間を徹底的に減らすことを前提に考えました。
結論としてこれらの作業に一切時間をさく必要がなくなりました。
時間的コスト0の達成です。
さらに3にいたっては最小限に抑えるだけでなく、継続して削減し続ける効果が得られています。
システムとして仕組みを構築することで、担当者をそもそも専任しなくとも最大限の効果が得られるのです。
具体的には
〜その1〜の項目で置き場を1カ所にしたことで種類が厳選され、在庫点数が削減されます。
〜その2〜のかんばんに発注時の残数が記載されているので、使用者がそのタイミングで発注依頼箱へかんばんを移動させます。
これにより欠品、余剰在庫がなくなり1、2の管理が不要になります。
また、私の場合発注依頼箱を商社毎に用意していたので、その箱を商社に来社時毎回確認してもらいます。
かんばんが入っていれば発注依頼として認識してもらい、商社の方に発注依頼済みのかんばんを注文中の箱に移してもらいます。
当然こちらも商社毎に用意します。
これにより発注作業すらなくなりました。
〜その3〜で分析が明確になっているので、現場作業者の毎月の改善活動の1つに「効果金額の高い工具を1つ単価の見直しや、再選定の実施」を盛り込みました。
結果継続した消耗品費削減の活動が実現します。
▼3つの最小限
最後に私が実際に数年間この仕組みを運用してきて、明確に成果の出た内容をお伝えします。
まず、在庫工具点数とそれぞれの在庫量の定量管理により
在庫数量が最小限になります。
次に消耗工具の在庫管理に費やす
時間的コストが最小限になります。
3つ目が、経営者や管理職の方には特に魅力的な響きの
経費が最小限になります。
実際私がこの仕組みを取り入れて以降、工具が欠品してしまうことや在庫量が多くなり過ぎてしまったことは1度もありません。
また、売り上げ金額に対する消耗品費の割合も2〜3%程度に抑えられています。
もちろんこれは在庫管理や単価の管理だけではなく、加工条件の最適化や工具寿命管理のしっかりとした体制があって初めて実現している数字ではあります。
ですがこの仕組みも大きく寄与していることは間違いないでしょう。
▼明日からすぐ始めよう
あとは行動あるのみです。
まずは消耗品の置き場所を少しずつ集約することから始めてみましょう。
今回私の職業柄、そして「Factory Labo」という都合上製造業(機械加工業)でお話しさせていただきましたが家庭の節約にも応用の出来る内容です。
缶詰やボックスティッシュ、乾麺の備蓄などに置き換えて考えてみてください。
実際我が家では備品置き場を集約し、テプラでラベリングし、定数管理をしています。
管理と言うと堅苦しく聞こえるかもしれませんが、もちろんかんばんなどは使っていません。
常に一定数置いておくように決め、買い物に行く前に確認し、スマホのメモアプリを使って必要数のみ購入してきます。
ただ家庭ではセール品や特価品を見つけてしまうと、ついまとめ買いしてしまうんですよね、、、
家計の管理の方が難しいです。
最後まで読んでいただきありがとうございました。
これからも製造業を応援する記事を書いていきますので、応援宜しくお願いします。
記事を読んでいただきありがとうございます。いただいたサポートは「Factory Labo」の活動費に充てさせていただきますので、活動に賛同していただけましたら応援よろしくお願いします。