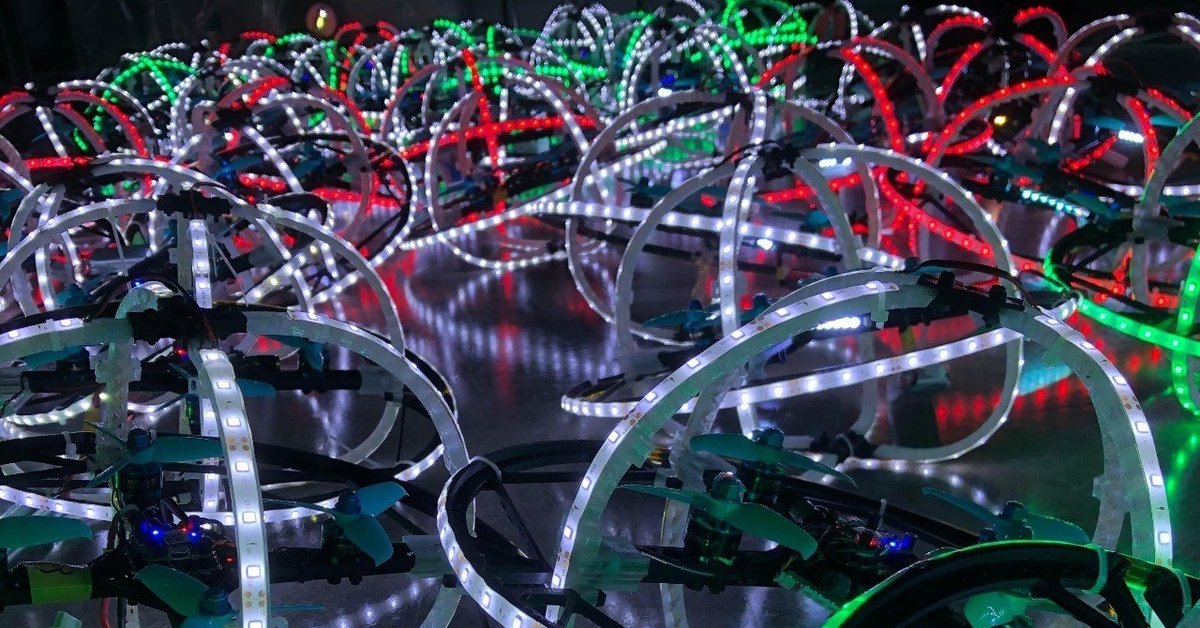
200機のドローンを3Dプリンターで作ってわかったこと-vol.1- 3Dプリンターを使う理由と利点
こんにちは。
フリーランス設計者の浅井です。
設計者の視点から新しい設計方法・生産環境構築ということを常々チャレンジしています。
さてひょんなことから、有名ゲーム「モンスターストライク」を運営するX-FLAGの一年に一度の祭典「X-FLAG PARK」での新規アトラクションで使用するプロダクトの開発生産を担当させていただくことになり、試作機能検証さらにはそのまま本番生産し納品するという案件を通じて得た開発・生産ノウハウを備忘の意味も込めこれから3Dプリンティングを利用される方や検討されている方のお役に立てればと思い、こちらで公開していければと思います。
※一個一個がかなり細かく出来るのですが、ちょっと書ききれないのでご興味ある方は直接ご連絡いただければと思います。
もしくは、リクエストいただければ執筆させていただきます。
ちなみにそのモンストのアトラクションはこちら https://event-info.xflag.com/park/2019/event-specials/drone/
企画の趣旨としては、ドローンシューティングというドローンを動く的としてプレイヤーがそれを狙い撃つという前代未聞のアトラクションでした。
※段落ごとにvolを分けて掲載致します。
vol1:3Dプリンターを使う理由と利点
vol2:3Dプリント生産を前提にした設計のキモ
vol3:3Dプリント生産ノウハウ
vol4、実際に3Dプリントで生産しての所感と可能性
3Dプリンターを使う理由とメリット・デメリット
【3Dプリンターを使用する理由】
そもそも3Dプリンターの利用は当初それこそ試作品を作る目的にて使用していましたが、アトラクションの仕様は常にブラッシュアップがなされ、その仕様は日毎にアップデートされ都度都度最適化された形状の検討を行い、テストをするという形で進行して行きました。
結果として、そういった柔軟な試作や生産をするということは既存の生産技術では対応することができないため、3Dプリンターを使用して試作品をそのまま本機として生産を実行することとなりました。
【3Dプリンターを生産で使用するメリット・デメリット】
ここでは3Dプリンターを生産で使うという事のメリット・デメリットを整理しておきます。
比較対象は主に既存の射出成形などのある程度の数を量産することを前提とした生産方法と比較します。
またデメリットについても記述いたしますが、それを補うための考え方も併せて記述させていただきます。
メリット
1:試作品がそのデータのまま本生産品になる
2:超柔軟に仕様変更が生産が開始していても可能
3:機械導入の初期コストが低い
4:インフィル形状など、既存の技術では難しい形状も可能
5:低資本での試作・生産が可能
デメリット
1:大型造形での大量生産は時間的に不利
2:造形失敗による時間的損失が大きい
3:樹脂が完全溶融されていないので、強度的に不利
4:製造コストは個数が増えるに従い増大する。
5:精度や見栄えは圧倒的に不利
【メリット】
1:試作品がそのデータのまま本生産品になる。
このメリットは非常にイメージがつきやすいのではないでしょうか?
金型化をさせる必要がないため、始めから3Dプリントでの生産を前提にしている事のメリットであると言えます。
生産方法が試作品を生産する方法と変わると、当然試作と生産する品物にはいくつか設計変更をする部分が出てきます。
例えば金型を使用して生産をする場合には、抜き勾配やアンダーカットの配慮といったように3DCAD上でのシミュレーションと配慮するポイントが変わってきます。これはプレス品でもなんでもそうですが、既存の生産システムに組込むための通過儀礼として必ず存在します。
つまり今まで、機能検証として形を作ってきた試作品を生産品にするためにまた設計をしなければならないということになります。
この手間はかなり大きな時間的な負荷を強いられることになり、どんどん開発期間を逼迫させることになります。
また生産をするための検証も別途必要となるため、検証についても機能と生産それぞれ検証することとなります。
しかしながら、試作品も本生産品も同一の機材をしようすることができるため、この検証を同時に行うことができ非常に効率的に開発を進めることができる大きなメリットと言えます。
2:超柔軟に仕様変更が生産が開始していても可能
「生産は始まったら引き返す事のできない一本道」
こういったことが通常の生産現場においては通説かと思いますが、その実情をひっくり返すようなメリットが3Dプリンターを使用しての生産をすることによって生まれます。
3Dプリンターの大きな特徴として、従来の旋盤やフライス盤などを用いた除去造形ではなく、一層一層積み重ねていく積層造形でありデータさえ存在していれば出力することができるということです。
つまり、型やワーク(あらかじめ切り出しておいた材料)等は必要ではないということになります。
上記準備物が必要でないとういうことは、現場での突発的に発生したニーズに対しても初動時間が圧倒的に短くなるため極めて短期間での対応についての可能性が大きく上昇します。
実際に案件を通じての当時このようなエピソードがありました。
アトラクション開始まであと2週間というところで形状は固まり納期までの時間も無いため生産を黙々と行い1/5の数量の生産が終わったタイミングで、現場から、ゲーム性を考慮しもう少し形状を変えてみたいという連絡が来ました。
通常であれば、生産が始まっており機能としても問題ないためこのようなオーダーは取り下げられるかもしくはトラブルに発展することが往々にしてあるかと思いますが、こちらは上記したメリットを生かし、データを要望の通り修正し、その場で了承を取り付け次の生産ロットから新たな形状でのパーツを生産し納品することができました。
つまり、どれだけ生産が進んでいようと形状の変更は可能となるということになります。
ただし一点オーダー側が気を付けなくてはならないのが、個数を準備する必要がある場合には、当然仕様変更する分生産数が当初の計画より落ち込むため予め見込んでのオーダーをすることが必要になります。
3:機械導入の初期コストが低い
一般的な加工機や生産機器は、非常に高価で基本的には融資や助成金などの補助資金がなければ調達をすることは難しく、なおかつ資金をペイするための仕事量も非常に多くなりがちです。
また、接地面積もバカにはなりませんので、維持費の面においても時間をかけてリサーチをしなければなりません。
一方、3Dプリンターであれば、amazonからですら購入が可能であり、金額帯も安いもので20,000円程度から購入することが可能です。
金額の安い高いは、ほぼ10万円オーダーまでは性能によるものの差がありますが、それより高くなってくると品質保証についての付加価値で金額が上がってくる傾向があります。
主に10万以上の機械は産業機として大企業や研究期間向けに販売がされていて個人ユースでは正直入手は困難であると言えますが、値段相応の品質は担保されます。
ただ、安いから悪いということも決してなく、必要なスペックを下調べしておき機材を選択し数を揃えることで、非常に安価に生産体制を確立することができます。
また購入した機材をアップグレードすることもできますので、場合によってはthingiveusなどでデータを引っ張りアップグレードすることも可能です。
今回使用した3DプリンターはANYCUBIC社のCHIRONという機材でした。
生産ユースでの主なスペック判断基準は以下のような部分になるかと思います。
【FDM型3Dプリンターのスペック】
・造形範囲
→ベッドサイズが400mm×400mm程度あればデスクトップ型では大型になります。
・対応可能材料の種類
PETGまで対応できると幅広く対応できるかともいます。ヒートエンド300℃・ヒートベッド100℃まで昇温程度がベンチマークになるかと思います。
・フィラメント切れ検出機能
→フィラメントセンサーが付いているかですが、フィラメント切れは意外と頻発する造形トラブルですのでこれを未然に防ぐフェイルセーフ機能としてあると安心です。
・オートレベリング機能
→ヘッドとベッドの平行が出ていないために、造形不良となるケースは多くありますので、レベル調整は最も重要な設定値と言っても過言ではありません。
しかしながら、おおよそのFDMの場合ベッド側での調整を採用しているケースが多く見受けられその制御は4点のネジで調整することとなります。
この調整にはかなりの熟練が必要になるのですが、オートレベリング機能はその熟練度をグッと下げてくれる機能です。
(とは言え、最終的な微調整は必要になります。)
本体を完成させた後、スムーズな出力をするためにこちらの機能は付いていて損はないかと思います。
・ベットの性能
→印刷中のワーク剥がれ造形不良を発生させるトラブルを定着不良という風に呼びますが、このトラブルも3Dプリンターとは切っても切り離せないトラブルの一つです。
純正のプラットフォームが付いている、もしくは後からプラットフォームをつけられる拡張性があるかを確認しておくとトラブル低減につながります。プラットフォームは付けておいて損はないかと思います。
4:インフィル形状など、既存の技術では難しい形状も可能
既存の生産技術を使用する場合、形状に制限が発生する場合があります。
最も難しい形状と言えば、外壁が完全密閉、内面が中実(中が詰まっていない)などの形状になる場合は生産は不可となります。
また、画像のような肉抜き形状などの場合においても型が高額になるもしくは形状の変更をやむなしとされます。
既存生産技術では実現が難しいような形状を達成する必要がある場合に関しても3Dプリンターは造形再現性を持って生産をすることが可能です。
5:低資本での試作・生産が可能
今までのハードウェア開発にはある程度の元手が必要となり、ソフトウェア開発のようにパソコン一つで始められるということはありませんでした。
結果として、事前に自己資産を貯めるもしくは、融資を受けて資金を確保する必要がありました。
しかしながら、3Dプリンターをそのまま生産に流用する場合には、生産機器および加工機を同時に入手することにつながりますので、生産に関する資産的ハードルはグッと下がり、チャレンジをすることができます。
ただし、後述するデメリットの生産数がある一定のしきい値を超えることでコストの逆転現象が発生するので、その部分には注意が必要となります。
【デメリット】
1:大型造形での大量生産は時間的に不利
既存の生産ラインに比べ、一万個オーダーでの生産は正直向いてはいません。それどころか、後述しますがコストの面でも大きく不利になります。
この理由はシンプルで、造形にかかる時間が既存の生産技術に対して非常に時間のかかるものであることに起因します。
一つのパーツを作るのに、金型であればものの数分でできるものが、平気で1時間などかかる場合があります。
しかしながら、3Dプリンターの強みはトライ成形が本番成形になりうるというポイントですので、金型本体製造時間内にテスト・量産が完結する場合には、3Dプリンターを用いることのメリットが発生します。
2:造形失敗による時間的損失が大きい
こちらも上記と同じく、造形時間に大きく関係することなのですが、3Dプリンターでは一度の失敗が命取りとなることがあります。
例えば、24時間で出力が完了するものが、残り2時間というところで何かしらのトラブルが発生した場合、当然その造形は失敗となり造形に費やした22時間と電気代、材料を損失することとなります。
こういったトラブルを未然に防ぐ手立てとして、そういった長時間での造形を断行せず、パーツを分ける・ノズル径を大きくする/積層ピッチを大きくするなどして造形時間を短縮する。などの工夫が必要になります。
当然造形時間が短くなれば、発生するトラブルの際のダメージが少なくなりリカバリーが効くようになります。
また、人手がかかりますがベッド上に大量に並べるのではなく一つ一つ生産するという方法も対処法のひとつとしてあります。
とにかく肝は、いかに短く強度を出して機能するものを作るか?ということが設計上の一つのキモとして必要になります。
このキモについてはまた別のvolにて公開いたします。
3:樹脂が完全溶融されていないので、強度的に不利
FDM(熱溶解積層方式)とは、一筆書きのように溶解した樹脂の線を少しずつ積み上げることにより造形物を作っていく方式です。
積み上げることで造形していくため、ピッチ(積み上げていく距離)間において完全溶解しないため、強度的に強い方向と弱い方向ができてしまいます。
他の樹脂成形方法は、完全に溶解させて造形をしますので、強度的に強弱方向は発生しないことになります。
つまり3Dプリントに関しては使用用途に合わせて造形方向も事前に設計段階から検討をしておく必要があります。
4:製造コストは個数が増えるに従い増大する。
おおよその所感ですが、だいたい本生産金型を一面(一パーツ)作るのに100万円からのコストが発生します。
その後、型を使って生産をするので、その際の成形コストも発生します。
おおよそ150万円程度からのコスト感ですが、ペイする方法としては、当然それ以上の付加価値をつけて大量に売りさばくことで金型代はペイすることになります。
しかしながらロット数が10~100などの超少量の場合はこの生産方法は難しいと言えます。
(アルミ型やコア組み換え式の方法などは存在するので、場合によってはこちらを検討するのも一つです。)
あくまで3Dプリンターが対応可能数は多くて100前後というのが今後一般的な数量になってくるかと思います。
それ以上の場合は、アルミ型などを検討するなどが良いかと思います。
上記のメリット・デメリットを理解した上で、3Dプリントで生産をするということのメリットが優っている場合、生産方法として合致していると言えますので、3Dプリントを使用する必然性が出てきますので、ぜひ検討してみるといいかと思います。
5:精度や見栄えは圧倒的に不利
やはり精度や最終的なアウトプット品の見栄えなどは、出力したそのままであれば、正直にいうと比較にならないくらい悪くなってしまいます。
当然これは出力してそのまま使用するということを前提での条件となってしまいますが、ここに関しては否めない結果であることは明記しておかなければなりません。
確かに昨今プリンターの性能向上に伴い、出力品の精度や見た目という部分はかなり向上してきていますが、あくまで一品ものという中での話で、生産にその精度や見た目を維持できるか?という問いに対しては正直厳しいということが正直な感想であります。
つまり、精度や見た目を維持する場合において、生産数の増加はそれらのパラメーターと連動して納期を大きく伸ばすといった方向性へと転じます。
一つの考え方として、そこまで見た目や精度を気にしないということに腹をくくれば、実は上記においてはそこまで生産上脅威にはならずむしろ特性として認めておくことが重要であると思います。
またもう一つの考え方として、それらの部品それぞれに対して精工さを求めず、その製品自体の肝となる部分においてのみコストを掛けることによって最適化を図ることができると考えられますので、プロジェクトの進行具合や何を大事にしたいかを製品設計のタイミングでチームとしてしっかりと認識して進むことが非常に重要であると言えます。
vol2へ続きます。