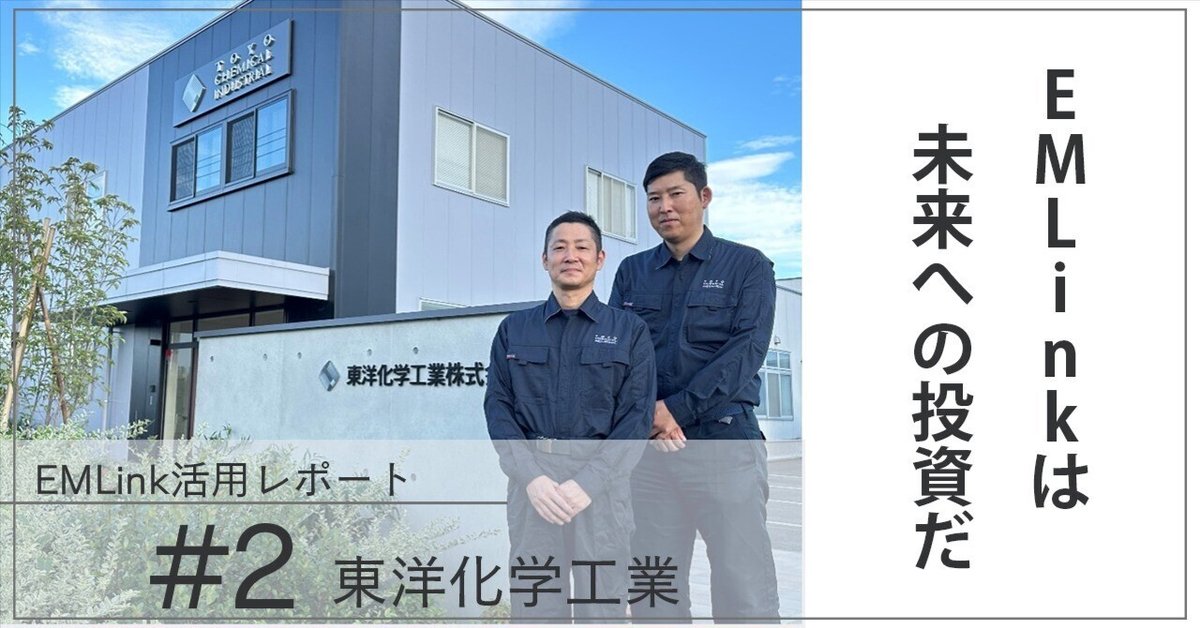
【EMLink活用レポート#2】EMLinkは未来への投資。成長企業がEMLinkと取り組む保全改革とは
企業の成長に伴い工場が拡大し、機械化されていく工場も多いだろう。しかし工場の拡大や機械化により、それまでに生じていなかった不都合が発生してしまうケースも少なくない。小さな工場であれば紙やExcelによるアナログな管理体制でもうまく回せていたものが、規模の拡大や機械化によって追いつかなくなってくるからだ。
今回ご紹介する東洋化学工業株式会社も、工場の拡大と機械化によってアナログな管理体制による課題が浮き彫りになったプラントの1つだ。東洋化学工業ではEMLinkを保全活動の中心に据え、管理体制の改革を進めている。そんな東洋化学工業の三浦氏と長沼氏に、EMLink導入に至った経緯と導入後の取り組みについて話を聞いた。
運命的なタイミングで届いた1通のメール。無料トライアルを経てEMLink導入
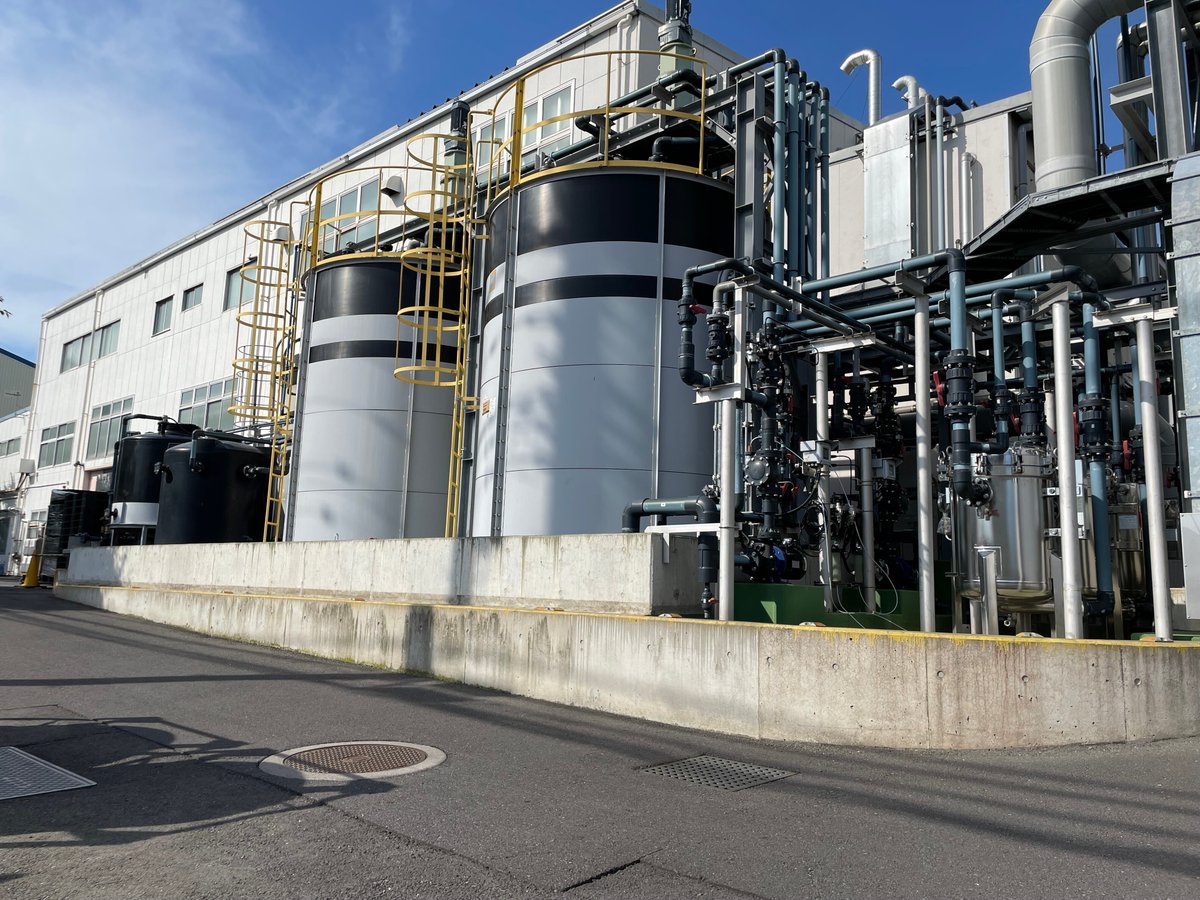
東洋化学工業は大正15年に創立された歴史ある企業だ。主力商品は銀やパラジウムの貴金属化成品で、本社がある東京と神奈川に構える計3箇所の工場が稼働している。
しかし工場のプラント化に伴い電子制御システムを導入した結果、それまでのExcelを使用した設備管理に限界を感じたのだという。「機器ごとにExcelで設備台帳を付けていたのですが、その管理方法では振り返りが弱く、故障時期が予測できないため急な対処に追われることが多くなっていたのです。東洋化学工業では機器が壊れたら修理や交換が必要になるため、急な故障が発生すると生産活動が止まってしまいます」(三浦氏)
そんな不都合に対し設備管理の見直しを考えていたときに出会ったのが、EMLinkだったという。
「プラントができて数年経ったあたりから様々な面で課題が浮き彫りになり、“今の設備管理方法から変えなければいけない”と話していました。そのときにちょうど届いたのがEMLinkを紹介するメールでした。さっそく説明を受け、無料トライアルからはじめてみたところ、“これはいいものだ”と実感し、導入に至りました」(三浦氏)
一元管理だから手間がない。データ入力の効率化で記録漏れを防ぐ
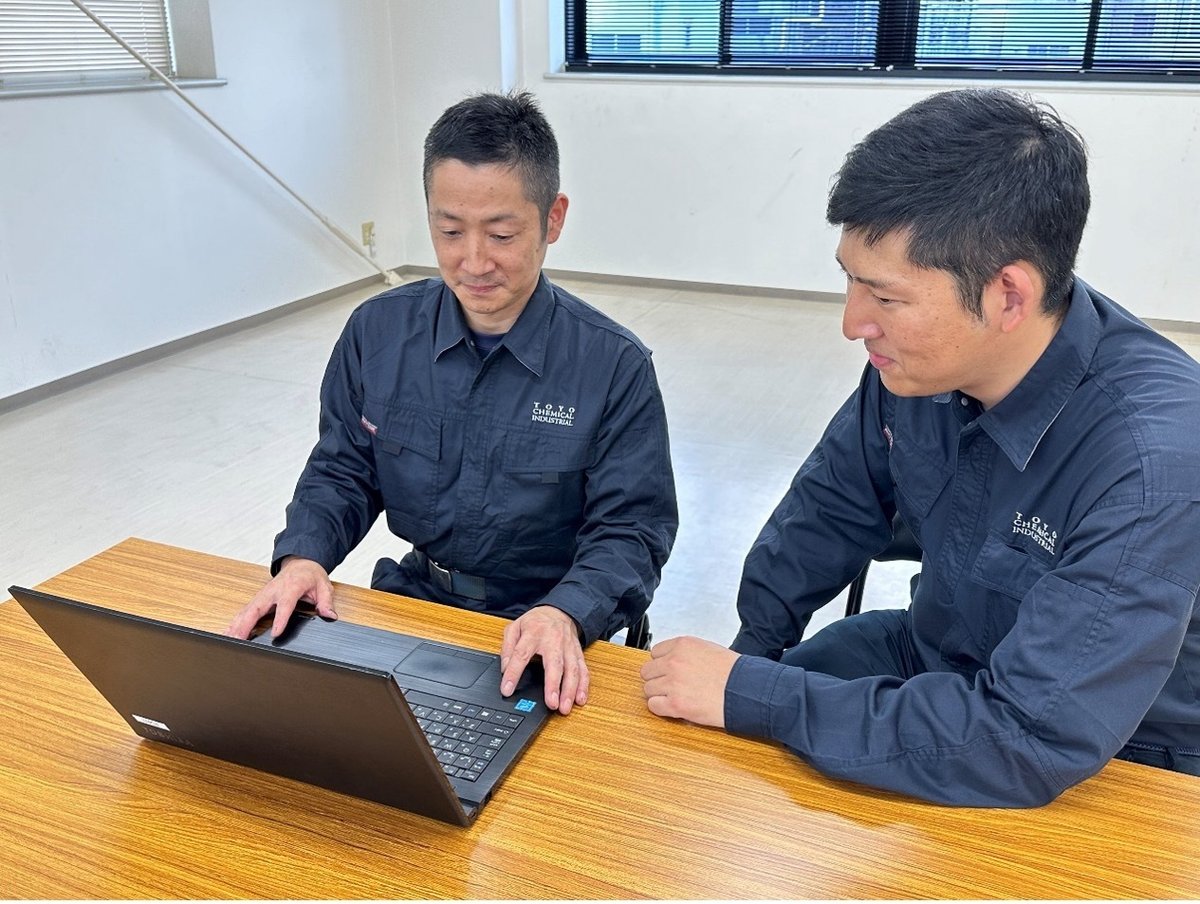
プラント化に伴い設備管理の面で様々な課題に直面したという東洋化学工業。そんな課題の解決に向けて導入したEMLinkの効果の中で、特に期待しているのが設備交換時期の予測だと三浦氏は語る。
「製造業である弊社にとって、設備が事業の要です。従来は設備が壊れてから更新していましたが、急な故障で生産を止めてしまわないよう事前に更新したいと考えていました。今後はデータの蓄積によって設備の寿命が把握できるので、設備を前もって更新しておくことが可能になり、急な故障に慌てることもありません」
設備管理の見直しに関しては、特にプラント化に伴い導入した電子制御システムの影響が大きいという。電子制御システムを導入している工程では装置が故障した際に手動での生産に切り替えることが難しく、大きな手間を要したり生産が止まってしまったりしていたのだ。そうした事態を防ぐため、以前の東洋化学工業では設備ごとにExcelで設備台帳を作成して管理していたのだが、その管理方法では限界があったと三浦氏は語る。
「定期的にExcelの設備台帳を見直していたのですが、修理・交換など細かなデータが揃わない部分が出てきていました。設備ごとに台帳を作っていたため、記録を付け忘れてしまう箇所が出てきてしまったからです。EMLinkにしてからはすべてのデータをEMLinkに入れることが出来るのでデータの収集が楽になり、記録漏れを防げるようになりました」(三浦氏)
「設備台帳だけでなく保全の履歴や今後の予定、日常点検の記録など、今までは異なる台帳に記録をしなければならず、二度手間三度手間になっていると感じていました。今はどんなデータもEMLinkに入れているのでそうした手間もなくなり、効率化されたと感じています」(長沼氏)
EMLinkを保全活動の中心に据え、あらゆるデータを記録していると語る両氏。実際EMLinkにより作業が効率化しているのを感じているようだ。また、東洋化学工業では保全だけでなく、そこにかかるコストも全てEMLinkに登録する構想を持っている。「例えばポンプが壊れた場合、その修理や交換にいくらかかっていたかを調べるだけでも、以前の管理方法ではすぐに情報を引き出せませんでした。EMLinkに記録してあればすぐに情報を引き出せるので、予算管理の面でもメリットを感じています」と長沼氏が語るように、修理交換費などの予算データも一元管理できるようになったことで、予算管理の面でも効果を期待しているという。
”今”ではなく“未来”のための投資。EMLinkと共に描く未来図
EMLink導入により様々な効果が見え始めた東洋化学工業。しかし東洋化学工業がEMLinkを導入した狙いは、直近の改善ではなくこれから先の未来にあるという。
「我々がEMLinkを導入したのは、“今”ではなく“未来”のためです。まだデータを蓄積している段階なので、実際にそうした効果が得られるのは1年後2年後にあると思っています。そのために今、工場全体でEMLinkへの記録をルーティンにしていくよう皆が意識しているところです。今後導入する設備はすべてEMLinkと連携させていく予定ですし、今は伊勢原工場でしか導入していませんが、システムに慣れ次第他の工場にも採用していきたいと考えています」(三浦氏)。
未来を見据え、EMLinkのルーティン化に取り組んでいるという東洋化学工業。EMLinkの使用感についても尋ねてみた。
「新しいシステムなので最初はやはり手間取りましたが、今は随分慣れましたね。デジタル機器に強い社員を中心に、徐々に社内に浸透しています。操作に困って“そろそろ相談したいな”と思っている頃にいつもEMLさんがフォローの連絡をくれるので、相談もスムーズにできています。こちらから連絡するのは遠慮してしまうので、定期的に連絡をいただけるのはありがたいですね。こんなにお世話していただけるとは思っていませんでしたから、非常に助かっています」(三浦氏)
成長を続ける東洋化学工業にとって、EMLinkは未来図を描くための欠かせないパートナーになっているようだ。
プラント・工場の課題解決ならEMLinkにおまかせ
設備の急な故障や発注漏れなど、予期せぬトラブルに見舞われることも多いプラント・工場運営。EMLinkはそんな予期せぬトラブルを予防し、迅速に対応するために開発された設備管理システム(アセットマネジメントシステム)です。プラント・工場運営に関する多種多様なデータを蓄積・一元管理してリンクさせることでトラブルを未然に防ぎ、業務を効率化。「紙やExcelによる煩雑な管理から脱却したい」「社員同士の情報共有を簡易化したい」「無駄な業務やコストを削減したい」など、プラント・工場が抱える様々な課題を解決に導きます。
プラント・工場を知り尽くした元プラントエンジニアが手掛けるEMLinkなら、現場ごとに異なる課題に寄り添い、その現場に最適な管理システムをご提案します。安心の無料トライアルも可能。まずはお気軽に資料ダウンロードフォームよりお問い合わせください。