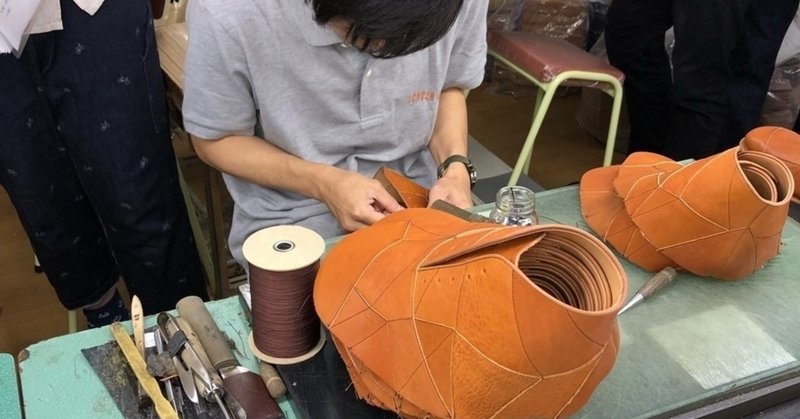
浅草で50年以上続く革靴作りの技術を目撃した話
ぼくたちが普段何気なく仕事中に履いている「革靴」。
紳士靴コーナーに行くとピカピカの靴がたくさんならんでいるのを目にします。
それらはいったいどこで、どのようにつくられているのか疑問に思ったことはないでしょうか?
今回は、150年以上続く革靴の生産地である浅草周辺のものづくりを発信するイベント団体、「浅草エーラウンド」さん主催の工場見学ツアーに参加しました。
今回は日本を代表する紳士靴ブランド「スコッチグレイン」の製造元である株式会社ヒロカワ製靴さんの見学。
この日も東京は35度以上の猛暑。
エアコンのきいた東武スカイツリーラインから、ツアーの集合場所である東向島駅におりたつとクラッとするくらいの熱気と日差し。
そんな中40名以上の見学者があつまって、東向島駅から徒歩で墨田区堤通一丁目にある工場へ。
10分ほど歩くと、ヒロカワ製靴さんの看板が。
まずはヒロカワ製靴の代表のお宅兼ショールームに集合。
そこから2組にわかれて工場を工程順に見学することに。
ぼくたちの班は株式会社ヒロカワ製靴の筆頭部長の酒井さんに先導され工場へ。
まずは靴作りに必要な主要パーツの説明から。
酒井さんから、靴の主要パーツである甲皮・本底・中底の素材の説明や、ヒロカワ製靴さんが採用する「グッドイヤーウェルト製法」にはかかせない「リブ」とよばれる縫いしろパーツの説明などがありました。
グッドイヤー・ウェルト製法とは、甲革や裏革などの部品を縫い合わせてできあがった「アッパー」と、底のパーツをジョイントする方法に最大の特徴があります。
またこの製法のその他の特徴として、中物をたっぷり入れられるので履き心地がいいこと、また修理がしやすいことなどがあげられます。
ちなみにリブとは、グッドイヤーウェルト製法の要である帯状の革「ウェルト」を縫い付けるための縫いしろになる部分だそうです。
下の写真のレールのような部分がそれ。
基本説明が終わると、いよいよ工場内へ。
まずは本底のパーツを裁断する工程から。
若手の職人さんが、CMC社というイタリアのタンナー(革をなめす事業者)から仕入れたぶあつい革をムダのないように金型をつかって抜いていきます。
靴のサイズによって微妙に革の厚みをかえることで、履き心地が最適になるよう考慮しているそうです。靴底ひとつとっても職人的な工夫が感じられます。
裁断したあとは、やすりがついた機械で革の厚みを調整しながら革表面に接着剤がつきやすいように荒らす作業。
職人技とはいえあらゆる工程が効率化され、たくさんのパーツを手早く仕上げられる工夫があらゆる所に見てとれます。
その横ではたくさんのヒール用のパーツに職人技で一気に接着剤を塗っていきます。みとれるくらいの速さ。
その次は中底のパーツに機械をつかってリブを縫いつける工程。ここでも若手職人が活躍しています。
次に工場を移動すると、いよいよ甲革を成型する工程へ。
まずは裁断した甲革のパーツに空気をとおすことで、革に穴があいていないかどうかを検査していきます。
甲革用の革は主に牛の背中のあたりを使うそうです。
このツヤが美しい革はフランスのタンナーのアノネイ社の革。
有名ブランドのエルメスにも採用されている質の高い革だとか。
ちなみに甲革の金型はこんな形。
ちょうどその横では、ヒロカワ製靴とデザイナーのコラボレーションにより生みだされた「スパイダー」という19のパーツを組み合わせてつくる靴の甲革を製作中でした。
靴業界の常識ではかんがえられない複雑な工程を経てパッチワークのような甲革のパーツがつくられるそうです。ミシンや手縫いの工程がうまく組み合わせることで美しいパーツが完成します。
さて次はいよいよメイン工場の地下へ。
ここにはヒロカワ製靴さんが持つたくさんのラインナップの木型がずらっとストックされていて壮観。
「木型」とはいえ素材に着色ができるバージンプラスチックを採用し、サイズ別に色分けをすることでサイズ判別の際の効率化をはかっているとか。
その後は上のフロアに移動し、いよいよ最後の工程。
これはイタリア製の機器で甲革と中底のパーツをつりこんで圧着する工程しているところ。
「つりこみ」と呼ばれる複雑な作業がイタリア製の最新機器により一瞬でおわってしまうのは圧巻です。
ちなみにその動画はこちら。
その後は甲革のあまっている部分をホチキス留めする工程。
ちなみにこれはそのホチキスの素材。巻きで大量に用意されています。
その後はグッドイヤーウェルト製法のかなめといえる工程。
「ウェルト」と呼ばれる細く裁断された帯状の革を、専用のミシンで甲革と中底にはったリブ、そしてウェルトを合わせてチェーンステッチしていきます。
ちなみにこちらは中底と本底の間に入る中物や心材(シャンク)といわれる素材。
靴の中物にはコルクを使うことが多いようですが、ヒロカワ製靴さんでは「EVA」という建築などに使われるクッション性の高い素材を採用しています。
コルクはつぶれたり腐ることがあるので、そういったことのない新しい素材をつかって耐久性を高めているそうです。
中物を入れた後は、こちらで本底のパーツとアッパーを圧着。
立体的に成型された靴底にあわせてローラーが複雑な動きをするようプログラムされています。
その動画はこちら。
さらにウェルトと本底を縫い合わせる「だし縫い」という工程が。ここでも専用のイタリア製グッドイヤーミシンが複数台稼働しています。このミシンが複数台ある工場は国内でもすくないとか。
その後は本底のサイドの余分な部分を機械で削る作業。このあたりは熟練職人の感覚による作業になります。
ちなみに削るのにはこんな特殊な歯がつかわれています。
削ったあとはコバをみがく作業。
こちらではヒールのパーツを貼っています。 これもガイドはなく職人の感覚が重要。
またこちらは最後の最後にサイズを型の色で確認し、靴底にサイズ刻印する段階。その後は型を抜き取ります。
この工程で木型の色分けをしていることがかなり効率化に役立っているのだとか。
最後は靴底を染めた後、バフで磨き上げます。
手作業の磨きにによりこんなに美しい靴底が。
もちろん甲革も丁寧に美しく磨きます。
最後はツヤを出す薬剤をふきかけることで、さらに高級感を出します。
最後に中敷きのパーツを入れ、検品、箱詰めをして全ての靴作りの工程が完了。
残念ながら最後の最後でiPhoneの充電が切れて、完成した美しい革靴の写真が撮れず....ホントに残念。
というわけで、本当に気の遠くなるような複雑な工程を経て、僕たちが履いている靴がつくられていることに感動の見学。
今回の見学では創業50年以上の歴史で培った技術と、ヒロカワ製靴さんに在籍している110人近くの職人の靴に対する思いがリアルに伝わってきました。
これを見る前と後では、革靴を買う時の見る目が確実に違うはず。
こんなすばらしい東東京のものづくりを発信する浅草エーラウンドさんと、暑い中土曜日に工場を公開してくださったヒロカワ製靴の皆さんに深く感謝しながら、この日は工場を後にしました。
ちなみに今回の見学の主催団体である浅草エーラウンドさんは、150年以上続く革靴の生産地浅草の意外な一面を楽しみながら知って欲しいという工房や地域のお店の想いから、定期的にこういった浅草を中心とした地域のものづくりを発信するイベントを開催しています。
興味が湧いた方はぜひこちらのサイトをチェックしてみてください。
・浅草エーラウンド オフィシャルサイト
ものをつくるひとを応援するために、いろいろな現場を取材しています。ここで得たサポートは、その取材活動に活用させていただくことにしています。