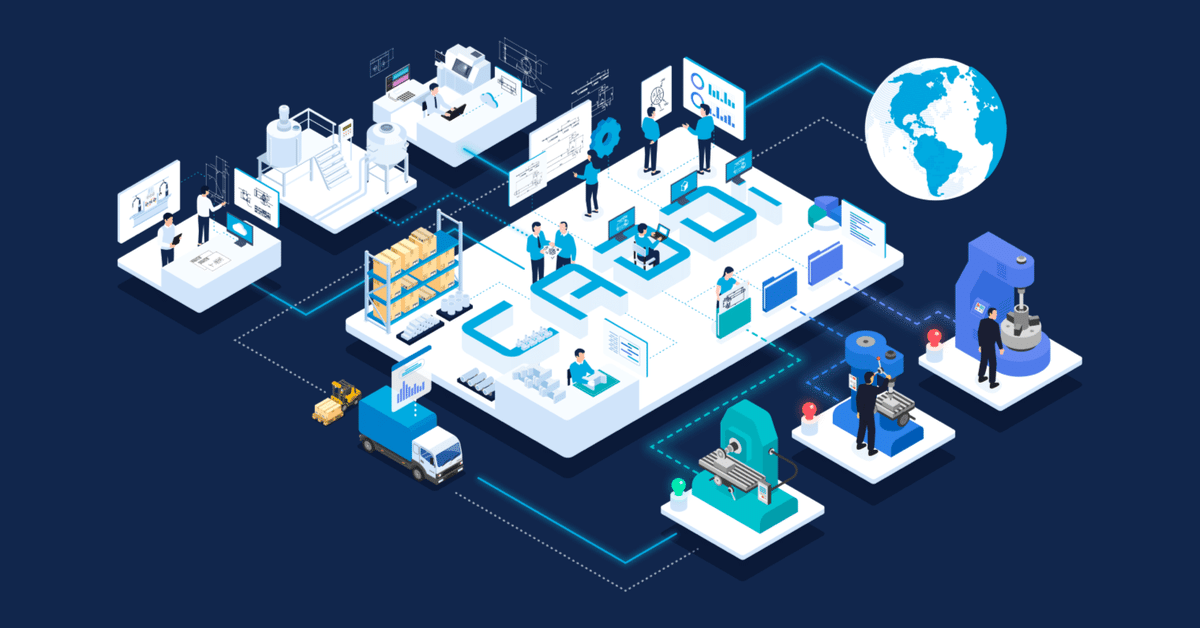
サプライチェーンに始まる、グローバル製造業の再進化。/キャディ創業5年記
明治維新からちょうど150年の2017年11月9日にCTOの小橋と2人で始めたキャディは、今日でちょうど丸5年になりました。キャディの5周年と、日本近代化の155周年を区切りとし、思考を少し整理してみようと思い立ちました。
ちなみに、長いですw(1万文字くらい)
モノづくり産業のポテンシャル解放とは
キャディが掲げるミッションは「モノづくり産業のポテンシャルを解放する」です。
モノづくり産業に従事する1人ひとり、1社1社が、自らの持つ付加価値に特化し、それを強めていく構造を作ることで、本来持つポテンシャルを解き放ち産業全体の価値を上げていくことを意味しています。すなわちこれは、少し雑に言い換えれば、1人あたりの付加価値=1人あたりGDPを上げていく取り組み、というわけです。
そんなマクロなことどうでもいいよ、と思われるかもしれませんが、結局生産性そのものが製造業従事者の賃金にほぼイコールでつながり、業界の人材獲得につながります。またそれにより、新たなイノベーションにつながります。逆に言えば、賃金レベルの比較優位性を持つことで、他の業界に人手を奪われることを防ぐことができる。だからこそ、個社にとっても、人類にとっても重要なのです。
少し長くなりますが、前提としての課題から説明します。
5年間で見えてきた、製造業における2つの課題
日本の製造業における1人あたりGDPの推移を見ていくと、悲しきかな、この25年間ほぼ横ばいで推移していることに気づきます。要は、1人ひとりが生み出す付加価値が上がっていないということです。でも、各企業を見ていくと当然努力を積み重ねています。それでも、産業全体の生産性は上がっていないわけです。
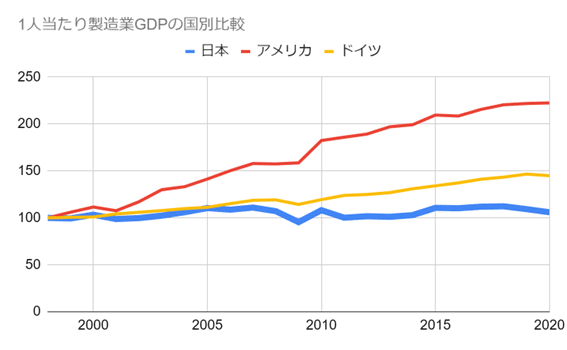
ここまでは、よくある話です。日本は製造業以外に関しても、そもそも1人あたりGDPはほとんど成長していませんから、まあそんなもんだろうと。ただ、面白いことに、1人あたりGDPがしっかりと上がっているように見えるアメリカとドイツについても、実は経済全体と比較すると製造業の伸びはとても劣っていることがわかります。
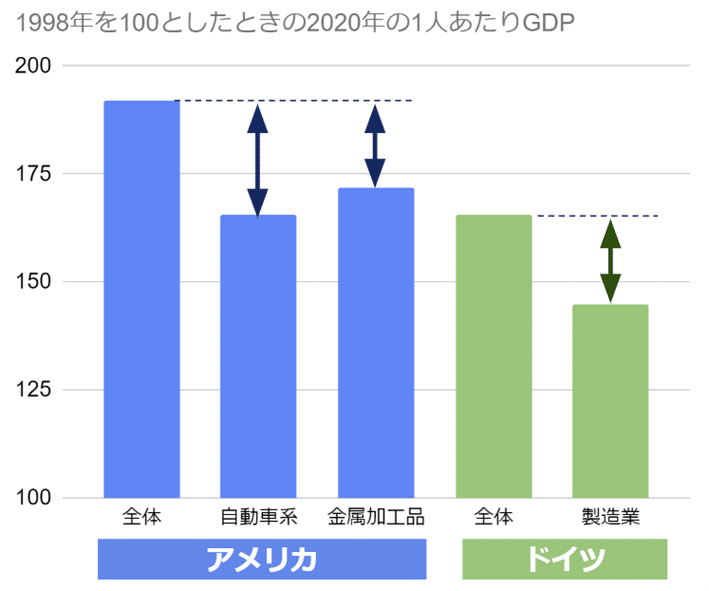
上述したように、製造業における1人あたりGDPが上がりづらい現実は、他の業界に人材を奪われていくことを意味するわけですから深刻です。実は、このグラフの前の25年間で、日本の製造業は実に4倍以上の成長をしています。では、なぜ製造業においてこの25年間、生産性の伸びが低いのでしょうか。
そもそも、製造業においては、「モノを売るデマンド(需要)側」と「モノを供給するサプライ(供給)側」の2つの側面があります。その中で製造業の特徴は、サプライ側(モノを設計し、作り、供給する)に圧倒的に大きなコスト・時間がかかっており、また価値の根源も多くがサプライ側に宿っていることです。
それを考えると、人々のライフスタイルを一変するようなレベルの製品イノベーションの欠如、というものを除けば、サプライチェーンにおけるイノベーションの欠如が、生産性が上がらない要因として極めて大きいわけです。そしてそれは、後ほど詳述しますが、下記の2つに大きく分けられると思っています。
1: 製造イノベーションの欠如
2: サプライチェーンデータアセットの欠如
なお、サプライチェーンを「物流」などと理解されている方もいると思うので定義をしておきます。
サプライチェーンは「製品の原材料・部品の調達から販売に至るまでの一連の流れ」であり、モノを作り供給するまでに必要な機能の総体であり流れであると思ってみていただければと思います。厳密には「設計」の機能は「エンジニアリングチェーン」とも呼ばれますが、モノを作るための重要機能ということでここでは設計機能もサプライチェーンに含めてお話させてもらいます。
1: 製造イノベーションの欠如
話を戻して、まずは1: 製造イノベーションの欠如について。
サプライチェーン全体を眺めていくと、実は物流要素よりも製造業においては圧倒的に「製造」機能が最も重要であることに気づきます。なぜなら調達コスト(=サプライヤの製造コスト)も含めた、自社+他社の製造にかかっているコストが、製造業における売上の実に80%程度を占めているからです。
そのうえで、時価総額100兆円規模のTeslaや、50兆円規模のTSMCという世界を代表する製造業イノベーターを見ていくと、明確な共通点があります。
Teslaは、イーロン・マスクが何度も”the factory is the product(自分たちのプロダクトは工場そのものだ)”と言っているように、彼らは車の会社ではなく車の作り方にイノベーションを起こすことで生産コストを下げ、スケーラビリティを上げて大きくなっている会社です。
また、TSMCは「ファウンドリー(半導体製造特化企業)」という製造機能だけを水平分業化して切り出し、今や世界の半導体製造の60%を担っている「メガファクトリー」であり、彼らしか再現できない生産性で、どこよりも微細な半導体製造を行うことができます。
どちらも、製造そのものをコア価値とし、そこに資源を集約化している会社なわけです。
一方で、製造産業全体に目を向けると、製造やそれを含むサプライチェーンにおけるイノベーションは製品におけるイノベーションに対してほとんど語られることはありません。また、1910年代に作られたフォード生産方式、1960~70年代に作られたトヨタ生産方式という製造方法・製造管理方法のイノベーションから50年、いまだTeslaやTSMCの起こす「個社内に閉じたクローズドなイノベーション」を除いて、生産性とQCDを急激に上げるイノベーションは起こっていないように思えます。
そこが、製造産業全体の1人当たりGDPが向上しないことの大きな要因の1つだと思うわけです。
特に、フォード生産方式もトヨタ生産方式も、TeslaもTSMCも、大量生産のコストを下げ、品質を上げるイノベーションです。一方で、今世の中が個別ニーズに対応する多品種少量生産化していく中、多品種少量・中量産規模の製造イノベーションは全くと言っていいほど起きていないわけです。
それはなぜかを紐解いていくと、多品種少量においてはその性質上、同じものを大量に作りません。規模の経済が効きづらいが故に、集約するメリットが出づらい。結果として生産の主体はほとんど全て中小企業であり、モノの受発注関係が極めて分散化された少量の1対1取引の集合体となってしまいます。それらの1体1の取引がクローズドかつ暗黙知に則って行われ、クローズドかつ個別的に磨き込み・改善が行われているわけです。しかしながらこれは、産業全体を進化させるようなものではありませんでした。
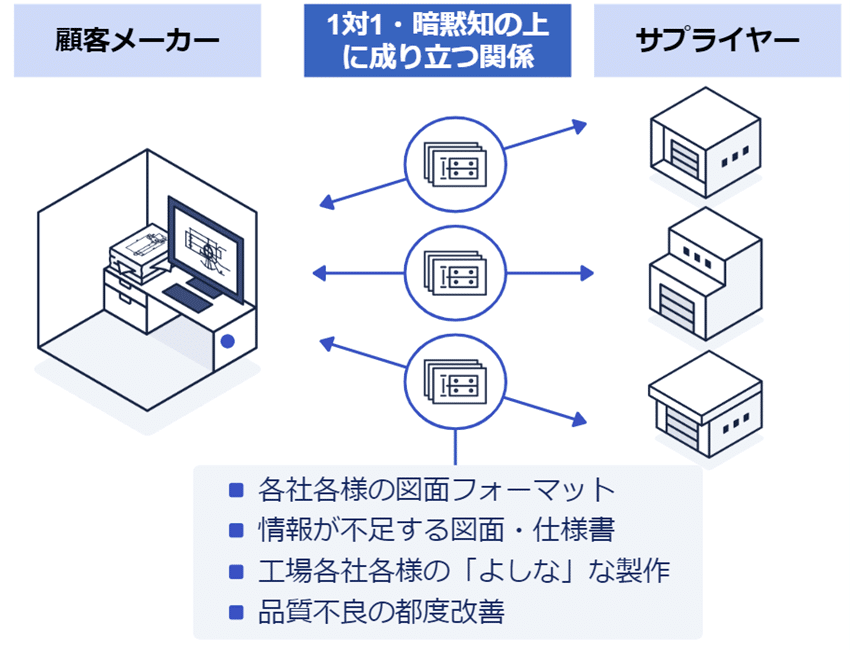
2: サプライチェーンデータアセットの欠如
これはサプライチェーンに限らずですが、何かの生産性を継続的に高めていくには、「アセットを使った複利での積み上げ」が極めて重要です。
例として、よくある複利の話をします。
毎日の1%の積み上げが1年後に37倍を作る、というやつです。今日100しかできないことも、毎日1%ずつ生産性を上げていくと、1年後には毎日3700できるようになります。
・・・というのは本当でしょうか?
溶接工の例で考えてみましょう。今日1日100個溶接部品を作っています。それが、1年後には1日かつ同じ時間内で、3700個作れるようになれ、というわけですから、これはベテラン溶接工も驚きのパフォーマンスです。
そんなことは普通に考えるとただの「コツコツ努力」では不可能なことにすぐに気づくわけです。この「1%複利理論」は、複利をうまく説明しているようで、あまりできていないような気がしてきます。
但し、これを唯一と言えるかはわかりませんが、可能にする方法があります。それは、「昨日やったことを今日、半年前にやったことを今月、なるべくやらなくて良くすること」です。
今日100個作っている人が、1年後には3700個は普通に考えると難しいですが、仮に昨日まで作っていた量の9割はほぼノーコストでできる、と仮定するならば、100個の生産量を1年後に400個程度にすればいいという計算になります(≒3700個×10%+37個)。もしも、98%をアセット化できてノーコストでできるのであれば、1年後も110個だけ作っていればよい計算になるわけです(≒3700個×2%+37個)。
これは当然非常に極端なシミュレーションですが、生産性を上げるということのミソは、以前やったことをやらないで済むようにする、または以前のやり方より賢いやり方を見出していくことであるわけです。また、多品種少量においては新たな部品であっても適用できなくてはならないため、そのアセットには汎用性が求められます。
逆に、昨日までやっていたことを、自分が同じように繰り返している限りにおいては、複利的な成長はなかなか期待できないわけです。
前置きが長くなりましたが、製造業のサプライチェーンにおいては、毎日100個作り続けること(厳密には半年後には120個作れるようになっているが、また部品が変わると100個に戻ること)が起こり続けているのではないかと思います。
多品種少量業界においては特にこれが散見されます。
装置を受注するたびに、ほとんどゼロから設計を行う(または新図比率が極めて高い)。その新たな図面をもとに購買先に毎回相見積もりを行う。生産に入ると、毎案件同じような生産調整が行われる。品質のすり合わせを部門間で毎回行う。昨年と同じものをずっと作り続けることが少ない多品種少量業界であれば、こういったことは日常茶飯事です。
複利を生み出す源泉は、「明日の自分を楽にする」ためのアセットを作ることです。つまり、1人当たりの生産性を上げようと思ったら、アセットを作らなければならないわけです。
なお、サプライチェーンアセットに関しては、装置があるじゃないか!という人もいるかもしれません。しかし、特に多品種少量業界において装置による生産性の改善は実は限定的です。手作業も多く残っており、また装置を操作するための固定費(段取り替え、プログラミングなど)が大きく、さらには装置の設定の仕方等を個別部品に最適化しなければ時間は改善されません。必ずしも装置が改良されていくからといって、全体の生産性が劇的に上がるわけではないのです。
私は最も重要なサプライチェーンアセットは「データアセット」だと考えています。具体的には後述しますが、これは上述した「部品にあった装置の設定の仕方のノウハウ」などを含む広い意味でのデータをもとに、同じ思考・同じ作業をしなくていいようにしていくためのアセットです。
なお、サプライチェーンのデータアセットに関しては、大量生産においても同じことが多くの部分において言えます(例えば、似たような設計を隣の部署で大量にしている、5年前にベテランが買ったものを若手がゼロから相見積している、など)。
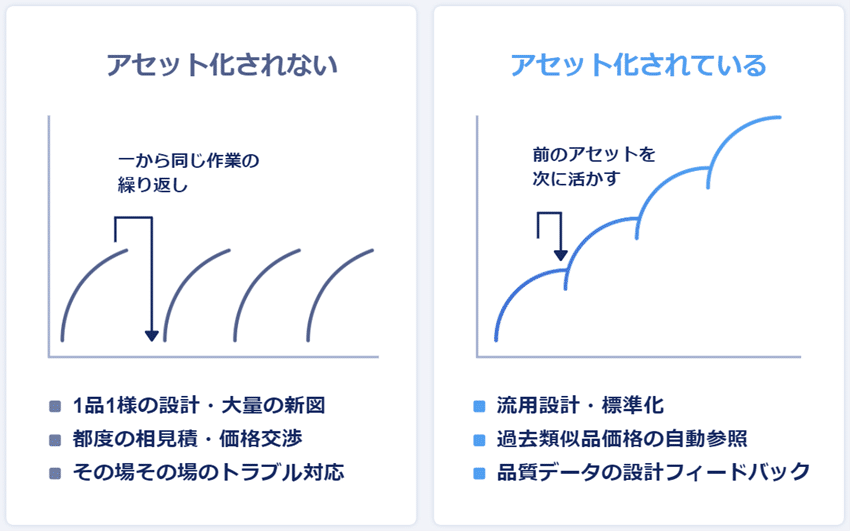
CADDi MANUFACTURINGという、製造機能のイノベーション
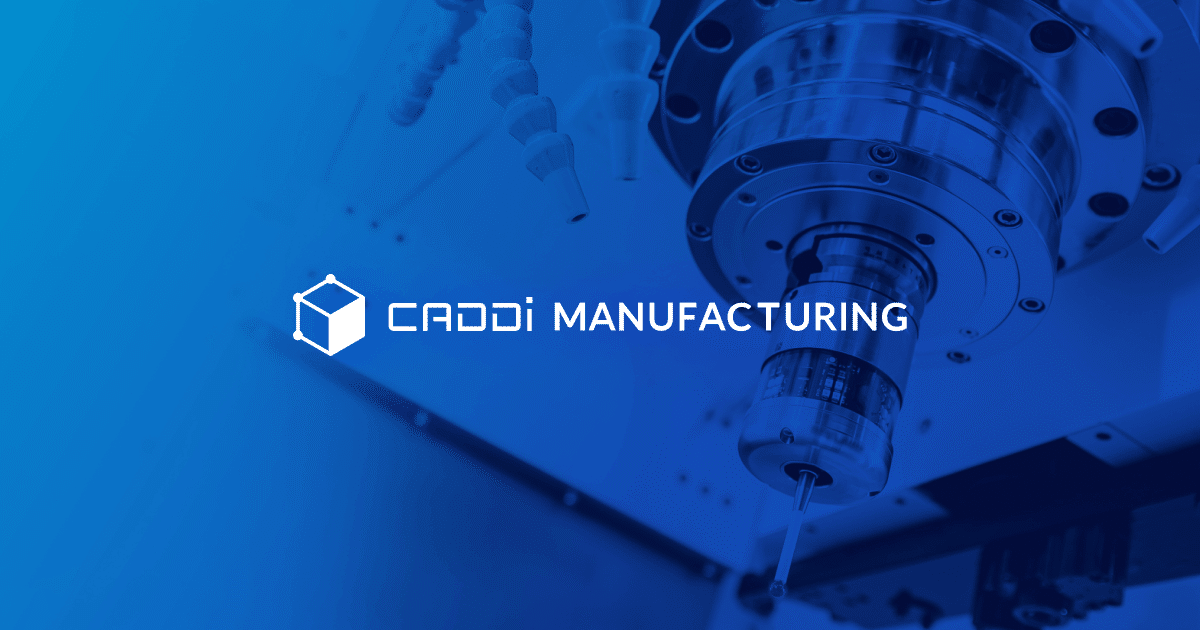
CADDi MANUFACTURINGは、少し前までは「受発注プラットフォーム」と呼んでいましたが、今は「調達・製造のワンストップパートナー」と呼んでいます。それは、サプライチェーンにイノベーションを自ら起こし、サプライチェーン全体をまるっと任せられるパートナーという存在になる、という宣言です。
また「CADDi MANUFACTURING」とあえて”MANUFACTURING”=「製造」を強調しているのは、上述したように製造業におけるサプライチェーンの価値のほとんどが製造機能に宿るからであり、そこを中心に、特に多品種少量~中量産の業界においてイノベーションを起こそうとしているからです。
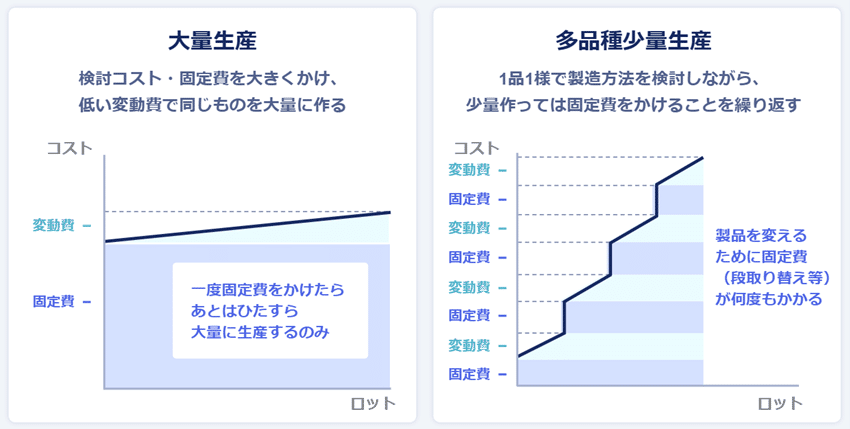
この図は、製造業における製造コストを表しています。製造コストは大きく、固定費的要素(1個作っても2個作っても変わらないコスト)と、変動費的要素(個数に応じて純増するコスト)に分かれます。
当然、大量生産はその名の通り1種類の部品を大量に作るわけですから、1個あたりにかける変動費を少なくするために、固定費的要素に集中的に投資します(例えば生産技術・工法の選定や製造装置そのものなど)。だからこそ、TeslaやTSMCは製造機械や工法の研究にコストを兆円単位で大量に投下し、生産性を上げて1個あたりの変動費を低くするわけです。
一方で、多品種少量・中量産においては、作る数が少ないため、固定費が薄められず、固定費の割合が大きくなります。そうなると固定費をあまりかけたくないため、製造方法は改善されず、結果的に変動費も大きくなってしまいます。
多品種少量~中量産の製造コストにおいて固定費も変動費も下がりづらいジレンマを、あらゆる工場においてスケーラブル(再現可能・低属人性)に解消し、製造機能にイノベーションを起こすためにキャディが投資しているのが、”CADDi Factory System(通称CFS)”です。
具体的にCFSが持つ特徴は大きく2つあります。
・多品種少量であっても製造コスト・生産キャパシティ・品質のレベルを大きく上げることができるパッケージである
・そのパッケージは一定の強みの源泉(=ポテンシャル)を保持している会社であれば、誰でも簡単に利用でき、スケーラブルである
パッケージの中身はキャディのコア価値となるため詳細には書けませんが、項目としては例えば下記のようなものがあります。
‐ 世界トップレベルの生産性を汎用化した製造方法標準(生産技術)
‐ 世界トップレベルの生産工程を自動的に再現できるコスト計算アルゴリズム
‐ 工場設立・拡張におけるヒトモノカネの支援やレイアウトを含めた支援標準
‐ 材料をキャディで集約購買して提供する材料供給標準
‐ 製造時点でのデータの受け取りを最適化する新たなCADシステム
‐ 類似製品の集約・最適分配機能
また、「なんでわざわざ自社で検査をするの?」とよく聞かれますが、不良を流出させないこと以上に、CFSにおいて重要となる、最適検査方法の標準化、品質基準を標準化、検査不要箇所の自動特定などによって生産性を著しく上げ、品質を構造的に向上させることが最大の目的なわけです。
これらはいずれも、固定費と変動費を同時に著しく下げるものとなります。これらを行うことで、キャディのパートナー工場は、1品1様なものであっても汎用的に扱うことができるため、大量生産のような効率性に近づけることができます。また、製造そのものという工場にしか持ちえない付加価値に徹底的に集中でき、それによってまた新たな工法やスタンダード・パッケージが生まれる、というサイクルを繰り返すことが可能になります。
そして、パッケージとして標準化されているため、新興国の工場であっても、すぐに適用が可能です(工場が既に持っている「一定のポテンシャル」の見極めが肝となりますが、そこもキャディのコアなので割愛)。
このようにキャディは、あえて製造業が製造業たる所以でもあり、最重要工程である製造・品質管理にディープに入り込み、製造業の根底課題を解決しにいっています。だからこそのCADDi “MANUFACTURING”であり、サプライチェーンの根幹である製造に根差したイノベーションをパートナー工場とともに作り上げ、新たなパートナー工場に急速にインストールし、スケールしていっているのです。
CFSと発注者を繋ぐ変換システムとプロトコル
実はCFSだけではサプライチェーンにおける生産性の課題を完全には解決できません。製造側を汎用化しても、発注者からの情報がバラバラでは、生産性の向上に限界があるからです。すなわち、CFSのインターフェースと発注時のバラついた情報を繋げるようにデータ変換する機能が極めて重要なのです。
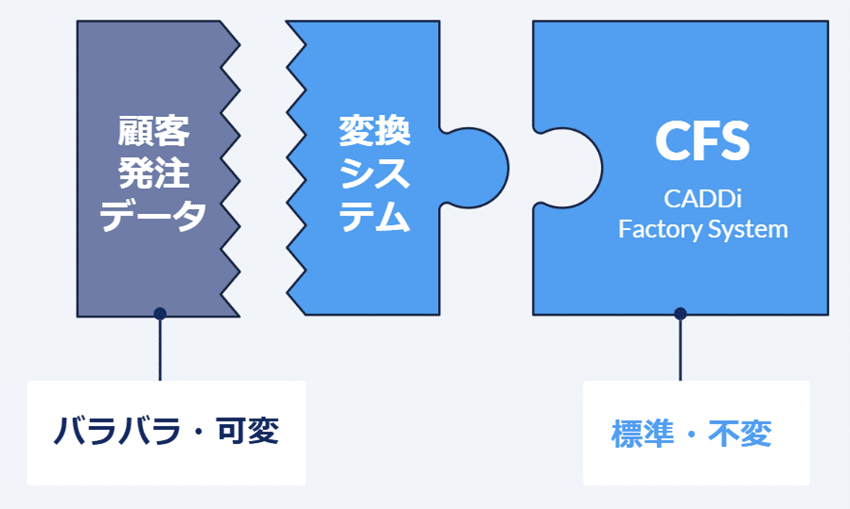
現状、図面フォーマット、設計や仕様の書き方、品質基準、調達の仕方といった様々な顧客からのインプット情報に極めて大きなばらつきがあります。故に、CFSのインターフェースにあった情報に変換することが必要になります。
この変換を行わなければ、製造コストは高止まりしたままになります。また、製造にうまく接続されなければ、品質管理のコスト等、取引コストも高いままになってしまうわけです。
例えば、図面の自動翻訳システムがあります。これは図面に書かれている情報や書かれていないけれど必要な情報を、スタンダードな書き方に自動変換・自動追記してくれるキャディ独自で特許取得済のシステムです。
また、変換作業のために必要な顧客とのコミュニケーションについて、最初は一定程度マニュアル作業が残っても構わないと割り切って行っています。顧客コミュニケーションを含めた変換作業を続けることでデータを蓄積し、将来的な自動化に繋がっていくからです。
だからこそ、サプライチェーン全体でのマニュアル作業を含めたデータ取得・作成・管理を行うための地道なプロダクトに5年間大きな投資をしてきました。今ようやく、諸々のオペレーションの自動化に本格着手できているのも、こうした地道な取り組みの成果だと思います。
また、翻訳・変換作業のデータの積み上げによって、将来的には汎用的なプロトコルを作っていって、そこに合わせてもらうことでの非連続的な生産性向上にもチャレンジしていきます。
私は前職でIndustry4.0に関する取り組みの調査・顧客適用という役割を持っていましたが、個人的にはこれは政府主導のトップダウンでの取り組みだとうまくいかないという結論に達しました。それは、共通プロトコルを作るためには各社での膨大な取り組みが必要になるのに対して、その過程で個社に対してメリットがないからです。だからこそ、我々キャディは、プロトコルを作る過程でも個社に対してもメリットがある状態を作りながら、将来的に業界全体最適かつ個社最適になるようなプロトコルを生み出していくことを目指しており、今はそのための壮大な投資フェーズとも言えるわけです。
これらのCFSと発注情報の変換システムを進化させ続けていることにより、この5年間で、産業機械業界におけるトップメーカー20社のうちの70%の企業様から、QCDのメリットを感じていただけるようになりました。ただちょっとした部品を買ってもらうサービス、ではなく、「調達・生産機能のワンストップパートナー」として、いくつかのトップメーカーにおいては、発注量としてもキャディがトップになっているほどサプライチェーンの中核として機能し始めています。
また、CFSの適用によってベトナム・タイといった海外工場でも世界トップレベルのQCDの実現と急速な工場拡大を実現できてきています。結果として、現在は日本最大はもちろん、アジア最大規模の加工工場に匹敵する生産量を誇る「Virtual Factory(仮想工場)」となりました。
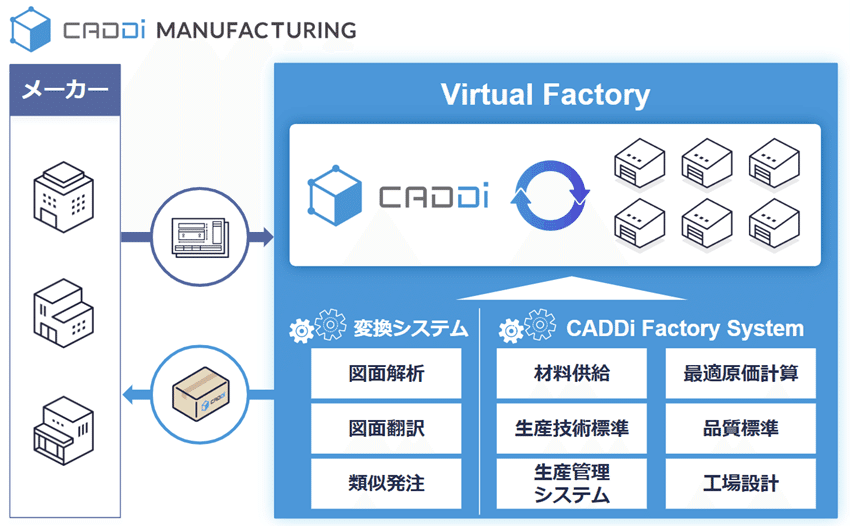
なお、CADDi MANUFACTURINGは自社で製造を行うメーカー、でもなく、マッチングを行うマッチングプラットフォーム、でもありません。あくまで「Virtual Factory(仮想工場)」なわけですが、その理由は以下の通りです。
1-1: マッチングは、暗黙知やトラブル対応コストの極めて重い特注品の世界において、取引コストの大部分を低減しないため手間がかかるうえ、品質に弱い
1-2: マッチングは、分散化された中小企業各社が持つ強みをそのまま活かすのであって、強みを創出・強化・標準化しないため、価格に弱い
2-1: メーカーは、特注品という無限通りのカテゴリ・工法組み合わせが必要な領域において、製品カテゴリの拡大に強い制限がかかる
2-2: メーカーは、製造行為そのものに資源の大半を集中させなければならないが、製造イノベーションおいてはノウハウ部分=CFSに資源を集中させたい
3: マッチング・メーカーのいずれも業界における設計から調達までのトータルプロセスそのものを変革しない
故に我々はVirtual Factoryであり、それによってモノの作り方、および供給のあり方そのものが変革されると確信しています。
CADDi DRAWERという、サプライチェーン全体をアセット化するイノベーション
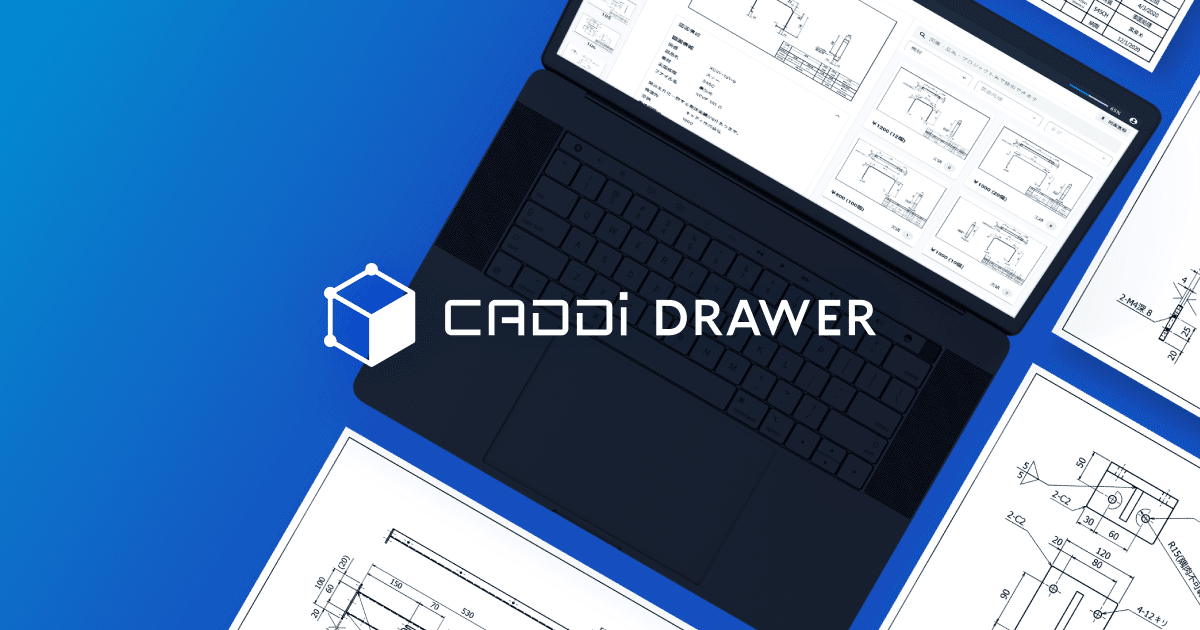
CADDi DRAWERは、去年からクローズドで提供を始め、今年6月に提供を開始した、サプライチェーンにおけるデータをアセット化するプロダクトで、まずは図面データのアセット化を可能にしています。ソフトウェアをクラウドで、サブスクリプションで提供している、いわゆる”SaaS”です。
”DRAWER"とは、図面(”DRAWING”)を引き出す(”DRAW”)ことで、貯めるだけではなくより賢く再利用する・積み上げていくということを意味しています。
我々のアンケートでも、製造業における60%以上の人が、図面が最重要データであると回答しています。だからこそ、どの会社も何らかの方法でこの図面データを保管しています。一方で、データを保管してはいるものの、バインダーに入れた紙が百万枚単位で倉庫に保管されていたり、ローカルフォルダで管理されていたり、また高度な検索ができなかったりと、引き出すのに最適な状態とは程遠く保管されています。保管していても、賢く使われなければ結果的にアセットではなく、作られては消耗される「消耗品」的なものとなってしまいます。
また、図面は単体で機能することはまれで、様々なデータと繋がることで価値を発揮します。その代表例が発注情報です。特に調達部門においては、2次元図面をもとに相見積先を決め、相見積をして価格を回収し、比較し、交渉するプロセスを経ます。その中で、図面と価格を行き来することが当然多くあります。但し、現状では図面データと価格のデータは別々のデータベースで管理されており、繋がっていることは極めて稀です。そういった、データ管理の一元化自体も、将来アセットとして様々な形で利用することを考えると大きな課題です。
CADDi DRAWERは、サプライチェーン全体に眠るデータをいかにアセットにし、引き出せる状態にすることで「昨日やったことを今日やらなくてよくするか」「昨日やったことより今日賢くできるか」「昨日やったことを新人メンバーでもできるようにするか」に解を提供する、サプライチェーンデータアセット化のイノベーションです。
より具体的には
5年前に隣の部署で書かれた図面を即座に探し出すことができ、新図を描かなくてよくなる
3年目に買った類似品が即座にサジェストされることで、発注価格のブレを抑えることができる
ベテランの自分の調達先選定力を、新人社員でも再現することができる
といったことをシステムの力で実現できます。
結果として、リリース後の短期間に、兆円単位の業界トップメーカーに次々と導入されています。
なお、広大なサプライチェーンデータの中で、図面データからスタートしているのは、サプライチェーンのほとんどの課題の起点が図面だからです。ただ、それはただの始まりにすぎません。
近い将来、生産工程のデータ、部品の品質のデータ、販売後のメンテナンスデータ、などサプライチェーン全体に渡るデータを統合し、それを簡単に見つけ再利用するだけではなく、そこから高度な解析技術によって、下記のようなことを可能にしていきます。
過去の類似品における品質不良と発注価格のデータから、調達時に自動的に発注先と発注価格がサジェストされる
顧客導入後の故障データから、設計変更がサジェストされる
こうしたサプライチェーンの各機能をまたいだ改善が、データに基づいて当たり前になされるようになるわけです。
さらに将来的には、上流からプロトコルを作っていくことも目指しています。自動的に設計にフィードバックがかかる仕組みが作れれば、その先にはより設計の仕方を標準化していくための図面フォーマットやCADといったものから手がけることで、設計時のバラツキ・エラーを防ぐことができるようになり、抜本から1人当たりの生産性アップができるようになるわけです。
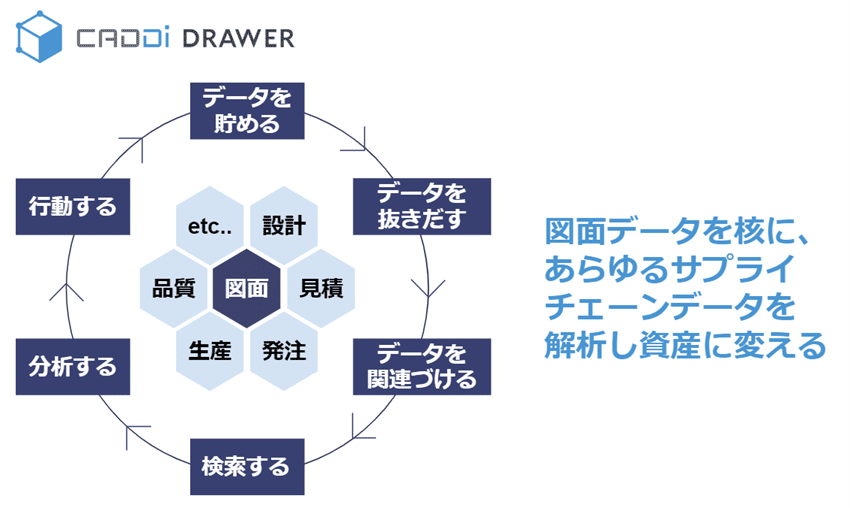
CADDi MANUFACTURINGとCADDi DRAWERの2本柱を保持する意味
これらの2事業は、製造業における1人当たり生産性を改革するだけでなく、具体的には書きませんが、実は非常に大きなシナジーがあります。
大きな観点でいえば、製造を中心とする下流からプロトコルを作っていくCADDi MANUFACTURINGと、設計・調達という上流からプロトコルを作っていくCADDi DRAWERの2つによって、製造業サプライチェーン全体を上流と下流から挟み込んで全体最適になるプロトコルを作りにいっているということもできます。
その意味で、キャディは、”SaaS-Enabled Virtual Factory”であり、”Virtual Factory-Enabled SaaS”と言えます。相互にenable(支援・補完・イネーブル)し合うわけです。サプライチェーンにおける製造のあり方・モノの供給のあり方を変え、またデータをアセット化していくことが、この2つが相互に影響し合って初めて提供できるのです。
おわりに
これまで5年間、顧客・パートナーに対する本質的な価値基盤を作り、世界トップクラスのQCDを実現するため、製造を中心とするサプライチェーンにとても地道に泥臭く向き合ってきました。
「個に迫る」という標語のもと、顧客・パートナーに多数の人間が常駐し、まずはとにかく顧客とパートナー工場のペイン・プロセスに顧客・パートナー以上に向き合い、肌身を持って知る。生産技術・品質管理など「製造」という製造業のコア領域を双方以上に知り、自らが改善活動を主導し、パートナーの製造コストを30〜50%の低減という抜本的製造改革ができるようにしていく。調達・取引のプロセス・ペインを双方以上に知り、またそれをなるべく多くキャディで吸収し、汎用化して丁寧にシステムに落とし込んでいく。
そんなことにじっくりと向き合うことで、ようやく世界トップのQCDの厳しさを持つ日本の大規模産業機械メーカーの多くに対して、サプライヤー内トップレベルで価値が出せるようになり、取引規模もアジア最大規模の工場と並ぶにいたりました。
これは繰り返しですがファンシーな要素はほとんどなく、ポールグレアムもびっくりの「スケールしないことをする」だったのではと思うほど、想像される以上に地道な作業です。その意味で、この5年間はスケールするためのコア価値を徹底的にフォーカスしながら見つけ、基盤を整備することに100%投資をしてきたと言ってよいでしょう。
徹底的にフォーカスするということは、組織にとってはとても苦しいことです。それはあたかも、世界最大産業である製造業というとてつもなく巨大な壁を目の前に、たった1つの小さな穴をひたすらに掘り続けてきた感覚です。数字は伸びていても、本当にこれでいいのだろうか?これで世界を変えるスケールができるのだろうか?と不安になります。それでも、その先の世界を信じて課題に真正面からぶつかってきました。そして、ようやく小さな穴が壁を貫通し、その先の世界の光をわずかに感じられた、そんなタイミングが今です。そしてこの穴を一気に拡大するための装置を設置する大きな土台が、並行して整備してきたシステム・仕組みの基盤だったのだと思っています。
6年目からは、その小さな穴を一気に広げ、本当の意味でグローバルに「スケール」をしていく5年間になります。
個社ごとのバラツキ・ニーズを汎用化し、CFSと簡単に接続できるようなシステムを、幅広い業界に対して構築していく。AIを含めた最先端テクノロジーを用いて変換システムを含めたオペレーションを自動化していく。あらゆる加工分野に対してCFSを構築し、パートナー工場自体をCFSによってスケールさせていく。グローバルに需要・供給を広げ、世界中の顧客・パートナーとともに製造イノベーションを起こしていく。
また、サプライチェーンにおけるデータの蓄積・活用のあり方を変えていく。よりインテリジェントな解析を可能にすることで、製造業全体のQCDのレベルを上げていく。ノンコアな相見積や図面・価格情報検索の時間を削減し、製造業従事者が真に付加価値を磨ける環境を作っていく。それによって製造業の暗黙知ベースのカルチャーをデータドリブンに変えていく。
キャディは、「VISION 2030」として、CADDi MANUFACTURINGのモノの流通規模を1兆円に、CADDi DRAWERのソフトウェア販売規模を1,000億円にする、それによってサプライチェーンのあり方を変えていく、という目標をグローバルで掲げています。
しかしながら、これですら小さな目標に見えるほど、製造産業の変革においてもたらしうるインパクトの全体像は壮大です。産業革命以降の200年間で、人類の生活を急激に進化させてきた人類にとっての根幹産業なわけですから、当然のことです。
「モノづくり産業のポテンシャル解放」がなされた世界を想像すると、とてもワクワクします。
6年目からもまた、キャディを宜しくお願い致します。
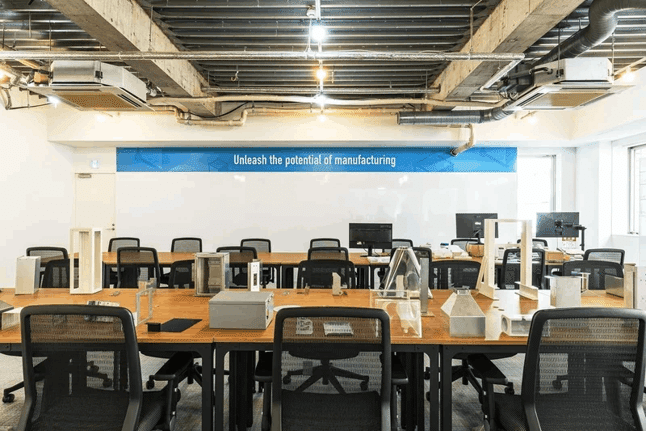
――
最後になりますが、この壮大な取り組みを行うにあたって課題がてんこ盛りで、それぞれをリードしてもらう仲間が必要です。恐縮ですが、最後に採用の宣伝をさせてください。
1:CADDi MANUFACTURING
‐CFSを進化させる生産技術人材・コストアナリスト
‐CFSをパートナー工場に導入していく工場立ち上げ人材
‐CFSインターフェースの変換機能を進化させ、運用を担うプロジェクトマネジメント
2:CADDi DRAWER
‐サプライチェーンデータのアセット化を実現するエンジニア
‐アセットの利用を支援するカスタマーサクセス
3:MANUFACTURING / DRAWERをグローバルに広める人材
‐アメリカ、タイ、ベトナムにおける顧客・SPへのアライアンスセールス
‐マーケティング・PR
4:グローバル組織を作るコーポレート人材
‐グローバルでの採用・育成・組織活性化をリードするHR
‐グローバルでの事業成長の基盤となる経営管理・経営戦略
すべての募集職種一覧
迷った人は一番上の「オープンポジション」がおすすめです!
https://herp.careers/v1/caddi
■会社概要Q&A
■募集ポジション
JP-BIZ:https://herp.careers/v1/caddi
GLOBAL:https://caddi.freshteam.com/jobs
TECH:https://recruit.caddi.tech/