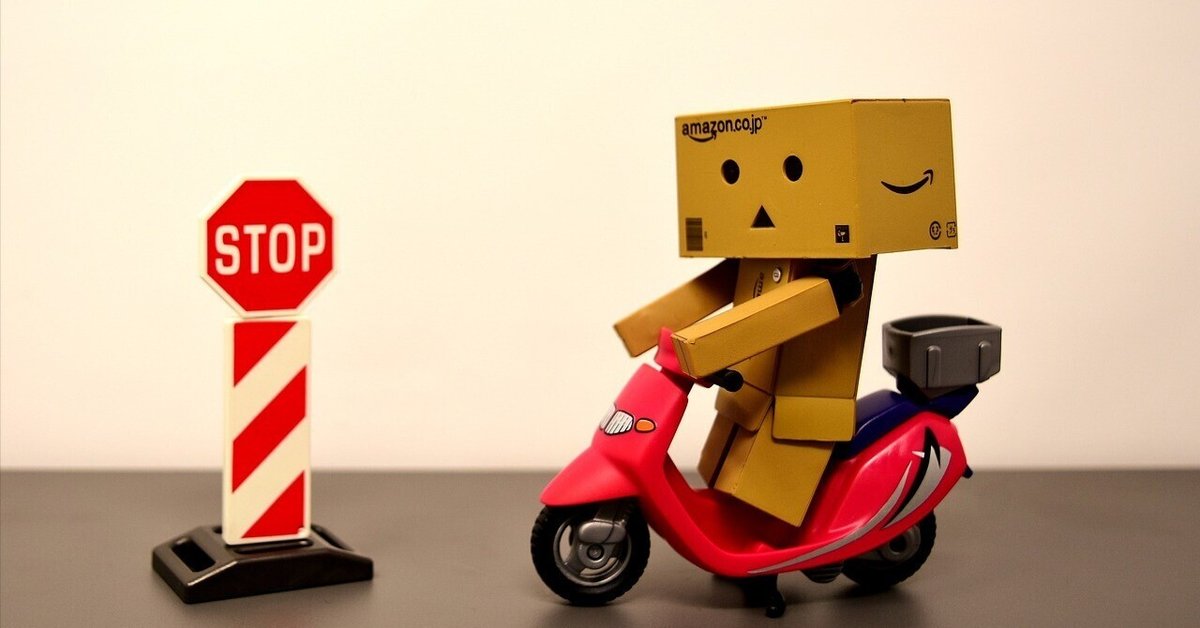
工場メンテナンスはなぜ行き届かないのか 「6つの罠」
工場の運営はメンテナンスの可否で8割方が決まると思います。しかし、色々な工場を見ていると、工場メンテナンスが上手く出来ていない現場がとても多くあります。
メンテはとても重要なことで、工場の成績の成否が決まる。なのにちゃんとできない。なぜこのようなことが続くのでしょうか。私の経験上は、6つの根本原因があって、それを取り除くことによって組織は良い工場になっていきます。その6つを重要なものから順番に説明したいと思います。
1)課題に優先順位付けが無い
「優先順位づけ」とは、とにもかくにもコスト比較のことです。
設備故障は生産停止ロスですから、全てを損失金額に換算することが出来ます。その金額の高い現象から先に取り組む。とても簡単なことを言っているようですが、これがちゃんと出来ている工場組織は非常に少ないです。
「優先順位をつける」とは、「重要なものに絞って下位のものは放っておく」という言い方が出来ます。その概念を下の図に示します。この棒グラフで、一つ一つの棒は故障の種類、横軸は停止時間を示しています。
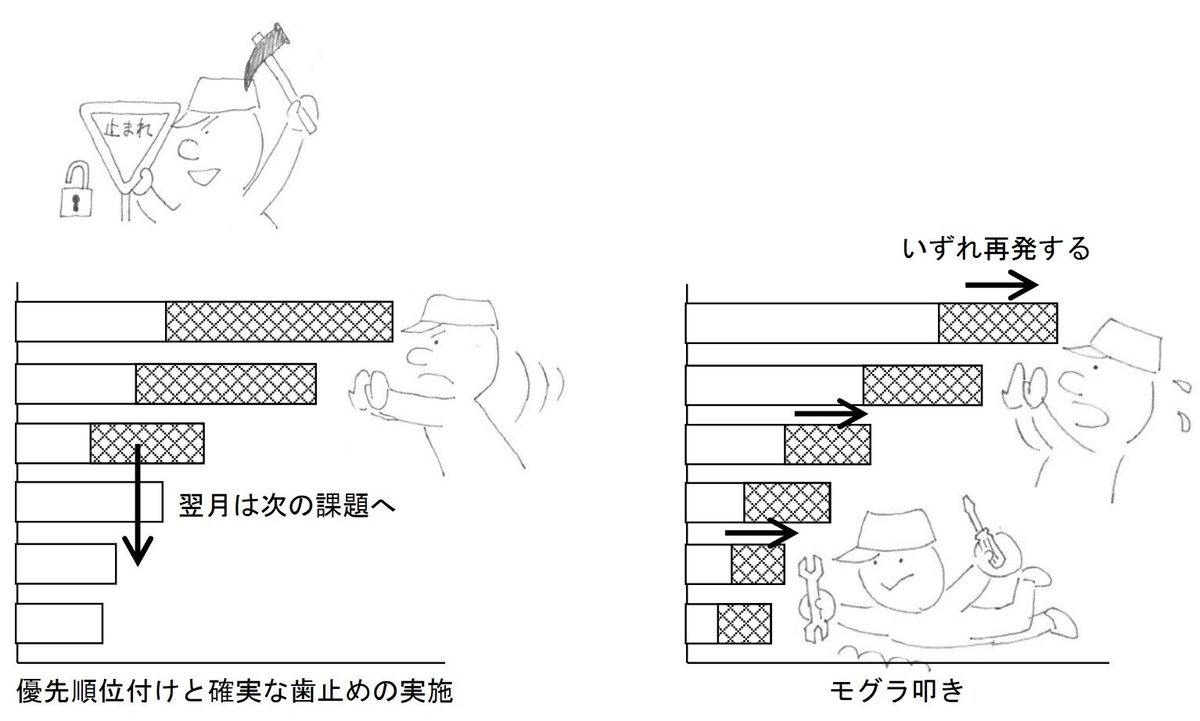
左が理想の形、右側が良く見られる残念な形です。
このグラフで網掛けの部分は、解決・対策に投入したマンパワーの量です。
左側では上位3つの故障に集中し、じっくりと時間を掛けて再発防止策まで取り組みます。
右側ではどの故障も中途半端にしか対応していないので、全ての故障がいずれ再発します。すると、この故障件数はずっと続くことになります。
「メンテが忙しく故障対応しているが故障件数は一向に減らない」という時は、このようなことが起こっています。
2)生産現場とメンテの関係が悪い
生産現場とメンテは、放っておくと必ず仲が悪くなります。これはもう、生まれ持った習性と言っても過言ではありません。人類の、と言っても大げさではないでしょう。私が世界各地の工場を飛び回る経験の中で、日本でも、アジアでも、ヨーロッパ大陸でも、アメリカ大陸でも、アフリカ大陸でもこのことを目撃しました。
生産現場は生産の成績が悪いことを「設備のメンテ状態が悪いからだ」と不平を言います。メンテは「生産現場が正しい扱い方をしないからだ」と言います。実際は両方の要素のミックスであり、どちらと断定できる性質のものではありません。
放っておくと仲が悪くなるこの2つの組織をつなぎ、協業させるのはその1個上の階層のリーダー、多くの場合は工場長の腕の見せ所です。
メンテスタッフは職人集団ですが、生産現場からの「おかげで助かった、有難い」という感謝を最大のモチベーションにするものです。生産現場からの感謝・信頼の感情とメンテの動機をうまくつなぎ合わせるチーム組織運営が必要です。
3)メンテスタッフの将来キャリアが見えない
チーム組織運営の視点が欠けている工場でメンテスタッフは「故障に対応する余計な労務費用」のように認識をされており、出来れば掛けたくない費用として、将来性のある人財としては捉えられていません。
このような組織では「分からずやの頑固職人」のようなベテランが幅を利かせたり、それによって若手がすぐに離職したりします。
メンテ経験者は生産現場にローテーションすることで、内部顧客視点を得て将来の業務に活かすことが出来ます。またそういう広い視野を得た人材は工場の幹部として育っていき、またその姿を見た若手にも、頑張れば自分にもそのような道が拓けるのだ、という夢を与えます。
4)メンテスタッフとキャリアエンジニアスタッフの協業が無い
製造業の会社の中では大学の工学部を卒業したエリートエンジニアスタッフが技術部門に所属し、またメンテスタッフは叩き上げで現場に所属し、この2つの人財層の間に距離があるケースが見られます。
1)で述べたような課題の分析と優先順位づけはエンジニアスタッフが得意とするところですし、叩き上げのメンテスタッフは優先順位が定まったところで具体的解決策を進めるのが得意です。それぞれの得手/不得手があるのでそれを組み合わせて協業させることで良い結果を出すことが出来ます。
5)メンテチームの自己解決力が育っていない
これは3)に触れた「分からずやの頑固職人」のようなベテランが幅を利かせる組織や、工場幹部がメンテチームに対して「クレーマー」のようなスタンスで接する組織によく見られます。
古株の頑固職人がいつも自分のやり方を振り回して若手の自由な発想を否定するので、チームは思考停止に陥って指示待ち状態になっています。
あるいは工場幹部が故障が起きたら怒る、というスタンスだけで接してくるので、言い訳ばかりを考えて自発的な工夫をしない組織が出来上がります。
6)保全リソースが足りない
「リソース」とはマンパワーとお金のことです。これが絶対的に足りないのであれば、どれだけチーム力で克服しようとしても限界があります。このことは経営者が考えるべき部分です。
これら6つ挙げたことが、「メンテナンスが上手くいかない根本原因」です。
上役で現場にやってきてこんなことを言う人がいます。
「メンテナンスが出来ていない。もっとメンテナンスの重要性を一人一人がちゃんと認識し、5Sなどの基本動作を徹底して、故障を一つずつ取り除いていかないとダメだ。」
私は「これは参りました、頑張ります ヒー」とか適当なことを言って受け流します。そんなことは根本原因でも何でもありません。野球で言えば、
「勝つことが出来ていない。もっとチームの結束力と勝ちに行く意識を一人一人がちゃんと認識し、守備攻撃の基本動作を徹底して、1点ずつ点数を取っていかないとダメだ。」
と言っているようなものです。参考になる情報が何一つ含まれていません。
根本原因とは、現在の課題があるエコシステムを変化させるために修正を掛けなければならないポイントのことです。メンテが上手くいかない工場ではこの文章に上げた6つのうちどれかが機能不全に陥っているはずです。
この記事が気に入ったらサポートをしてみませんか?