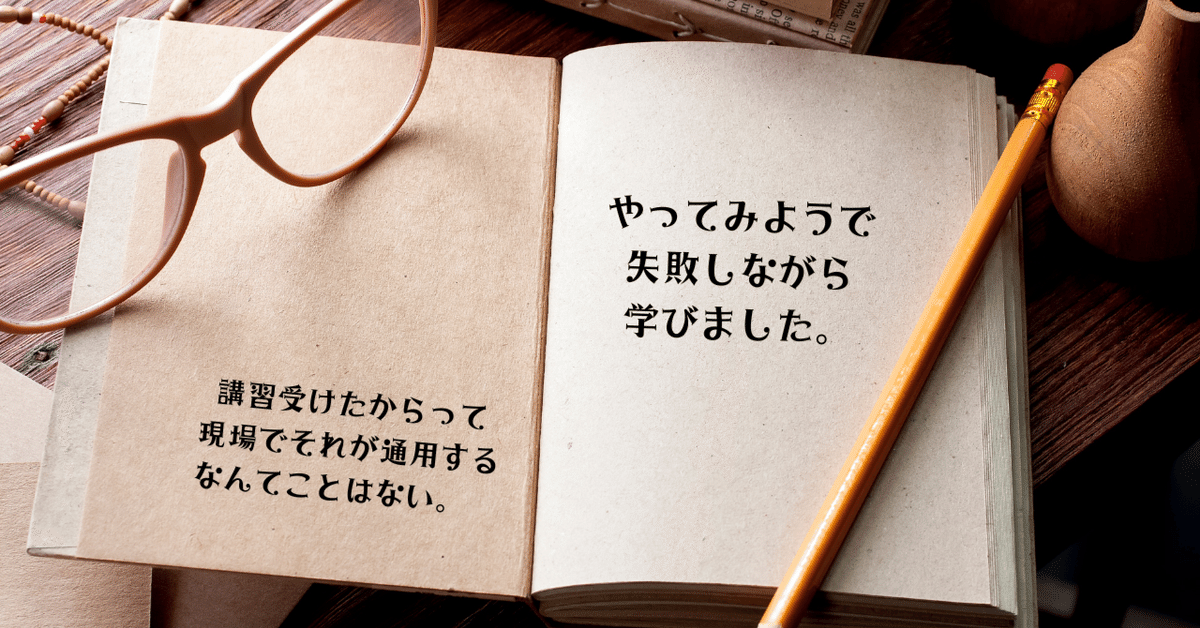
やってみよう!で失敗しながら学びました。
現場の社員さんが退職されることをきっかけにCAM、マシニング・ワイヤーを教えてもらい現場に入ることになりました。
当時はスマホなんてなかったのでこの写真しか残ってないですね💦
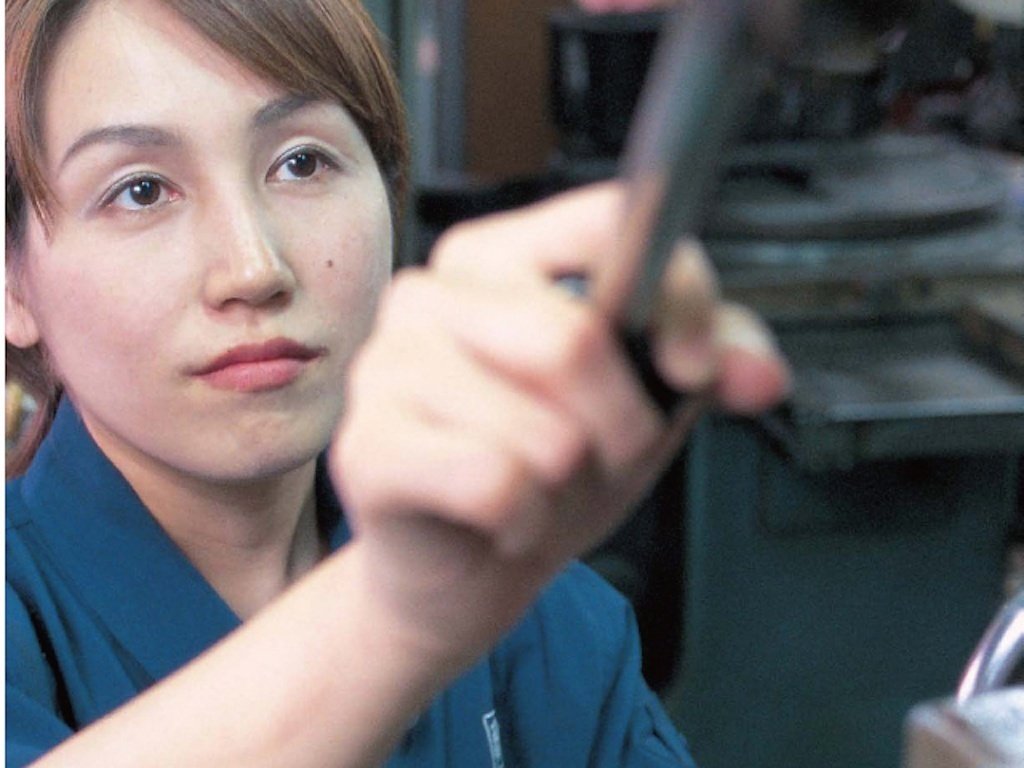
機械加工を始める
プログラムに関しては前職の経験もあってか抵抗はなく、むしろ簡単に感じました。Gコードと言われる工作機械のコードを覚えて。プログラムを作って機械を動かしていきます。
その当時、現場で機械が空いてることが多かったので在庫している材料持ってきては何かしら加工して練習していました。
加工するモノを考える力はなかったので穴開けるとか四角く削るとかそんなことばっかりでしたが練習するにはそのくらいからでよかったのかもと思います。
その後、3次元のCAD/CAMの講習に行かせてもらうことになり、TOOLS(現CAM-TOOL)とCADCEUSを勉強して使い始めました。
当時は小規模のプレス金型メーカーが3次元CAD/CAMを導入していることは珍しかったようです。確かにそうでした。3次元形状の加工が必要となる仕事はあまりなかったように記憶しています。
私の父(当時社長)は先見の目があって、これは絶対強みにになる!と考えて早々に3D CAD/CAMを導入していました。2001年の頃です。
仕事しててたまたま見つけた見積書の金額を見て目が飛び出そうになりました。「中古の家買えるやん!」ってくらいの金額だったので。
しかし、その当時、現場で使いこなしている人がいなかったことと、まだそれを使う仕事がなかったのです。後から振り返ると父の目が先の未来を見ていたんです。
動き出したら3D加工の仕事がきた!
私はその状況を受けて勝手に使命感を感じ、「これで仕事できるようにならないと!」と思って1週間の講習を受けて動き出しました。
しかし、仕事がなければ動かせない。。。でも勉強しておかないと。
そう思って毎日現場で練習していました。
そうこうしていたら、お客様からのご縁で愛知の金型メーカーさんと繋がり、「3D持ってるんか?そしたらこの仕事できるか?」と仕事の依頼を受けることになりました。
講習受けたからってできるわけではない。
しかし、講習で勉強しただけで加工できるなんて甘い話はなく、仕事を受けるも加工工程を組むにも知識がなく、何回失敗するねん!ってくらい失敗してトライしてました。何回も泣きそうになりながら。
切削工具もいくつ壊したか・・・今思えばそれを黙って見守り、チャレンジさせてくれていた父はすごい人だと尊敬するばかりです。
ある時、これは自分だけでは無理!って思ってCADメーカーさんにヘルプを頼みました。そうして加工品が出来上がり、なんとか納品することができました。
3Dの加工は加工プロセスを組み立てないとできないのに、そんな知識がない中でこれか?それともこれ?みたいな感覚でチャレンジしていたのでそりゃ時間がかかりました。
そんな中で学んだこともたくさんあり、加工できるものの幅が広がっていきます。
失敗して学びました。
そして加工はできる!と思って加工ばかり仕事を受注するようになり、機械加工のお仕事をたくさんさせて頂きました。CAD/CAMとマシンがあれば部品加工できる!そう思って材質も分野も関係なく加工仕事をしていました。
順風満帆にことが進んで・・・・いくわけもなくある時、不良を出してしまいます。
機械加工したことないステンレス切削部品を受けていつも通り加工したのですが歪みが出て20個NGに。
職人さんに修正してもらいなんとか乗り切りましたが今思えば機械は使えても材料のことを理解していなかったんですね。
素材が熱変形するなど力学や化学のことを全く理解してなくて、機械が動けばなんでもできる!と思っていたんです。
機械はプログラムを作れば動かせるし、条件を合わせれば加工ができます。
でも、素材のことを知らないと正しく使えない。
その時に学びました。
何でもかんでもデジタルで便利なものを使ったらものができる、モノづくりはそんな簡単なことではありませんでした。
「機械はあくまで道具なので使い手次第でいいものも悪いものもできる。」
私の場合、汎用機を使って加工したことがなかったので材料の性質や特性など基礎知識がないままで加工をしていたんですね。
今思えば恐ろしい・・・でもできてしまうのがNCなんですね。
そんな経験を積みながら、プレス金型製作に携わっていきました。
つづく・・・・・
この記事が気に入ったらサポートをしてみませんか?