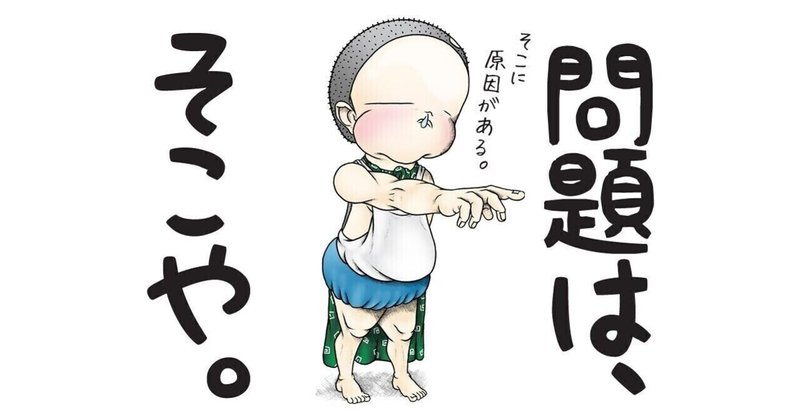
【1分で分かる工程改善】老舗カッパ業者でみたトヨタ生産方式のエッセンス
こんばんは。
今回は、トヨタ生産方式のエッセンスが詰まった動画の紹介していきたいと思います。
この動画では、主に生産数量の最大化を目的としていますが、最適化する場合も同様のことが転用できますので是非参考にしてください。
1.設備中心のボトルネック基準にした前後工程の最大化
この改善で実施している最初の活動は裁断工程の生産量の最大化です。
具体的には、機械の構造上、製造時間を短縮できない裁断機をボトルネックに設定し、前工程の材料の裁断工程を低コストで生産量を上げ、裁断機を止めない様にしています。
この手法をとることで、ネック工程の最大生産量まで全工程の生産量を引き上げることができます。
1.基準作りと標準化
この動画のすべての改善紹介でトヨタの社員が共通して言っていることは、「基準作り」と「標準化」です。
基準作りを行うことで、材料は毎回同じ動きをします。それにより、工程での材料の位置が決定することで、工程の品質ばらつき(位置ズレやサイズ)が小さくなります。
工程の品質ばらつきが小さくなることで、後工程のばらつきも小さくなり、最終的には製品の歩留まりが増えて生産量が上がります。
標準化は、物を置く場所や作業者の動きにルールを設定し一定にすることです。
標準化を行うことで、作業者は毎回同じ動きをすることになり、作業時間のばらつきが小さくなります。
加えて、動作をルール化することで作業者の習熟度も向上し、回を追うごとに作業者の作業速度が向上し、同じ時間で生産できる製品の量が増えます。
2.問題の顕在化
徹底して基準作りと標準化で、安定したモノづくりのベースを作った後に、問題の顕在化を行います。
この動画では生産管理板を用いた予実管理とズレの要因の徹底調査・解消にあると紹介されています。
予定数量とのズレが発生している場合は、標準や基準とはずれた動きができない不具合が発生していることになります。
このズレの要因を5ゲン主義で徹底的に究明・解消することで、対処方法を探すことが最も重要なことであるといえます。
生産管理板は下記サイトに実物があります。
3.ボトルネック基準にした前後工程の最大化
問題の顕在化を実施した後に、行うことはボトルネック工程の前後工程の生産量の最大化です。
具体的には、機械の構造上、製造時間を短縮できない裁断機をボトルネックに設定し、前工程の材料の裁断工程を低コストで生産量を上げ、裁断機を止めない様にしています。
この手法をとることで、ネック工程の最大生産量まで全工程の生産量を引き上げることができます。
4.実作業を自ら行い無駄はすぐに排除する
この動画に出演した指導者の言葉で最も印象に残ったことは、「作業を自ら行ってムダ、ムラ、ムリを見つけた」、「できる改善はすぐに安価に行った」という言葉です。
改善技術者が自ら、作業を行うメリットは下記にあります。
①普段の作業者が当たり前に思っている負荷を発見できる
②作業者の負荷を共有することで改善提案に説得力を持たせられる
また、改善を迅速かつ安価に行うことで、作業者の負荷を小さくする努力を見せることで作業者の信頼を勝ち得ることができます。
この動画では、100円ショップやアマゾンで購入した部品を大量に流用することで部品調達コストと入手リードタイムを最小化していました。
5.まとめ
この動画ではトヨタ生産方式のエッセンスである下記項目を実例を交えて学ぶことができます。
①基準作りと標準化
②問題の顕在化
③ボトルネック基準にした前後工程の最大化
④実作業を自ら行い無駄はすぐに排除する
皆様も、ぜひ動画を見て実例を見ていただけますと嬉しいです。
コストカット手法や工程構築に関するマガジンも発行しているので、興味のある方はぜひ読んでいただけると嬉しいです。
最後までご覧いただきありがとうございました。
この記事が気に入ったらサポートをしてみませんか?