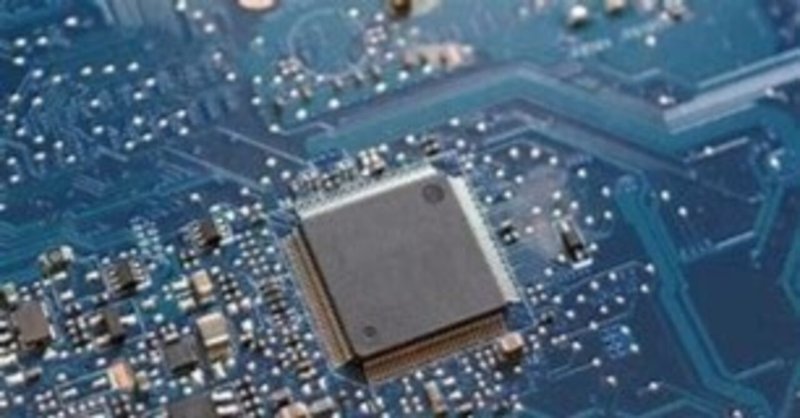
半導体製造の工程について語る
半導体とはいまは誰でも耳にするものであろう。「導体」とは電気を通すものであり、逆に当たるものが「絶縁体」である。つまり半導体とは、「電気を通しやすかったり通さなかったりするもの」ということが元々の名前の由来である。
そんな半導体は生活に欠かせない物となっている。スマホや車、パソコン、冷蔵庫など挙げればきりがないほどに様々な場所で使われている。
半導体市場は2030年には2倍に拡大し、100兆円産業になるといわれており、水の市場規模を超える予想が立っている。
今後、株式市場も半導体を中心として動いていくことが予想される。
そんな中で半導体がどのようにしてできるのか、またその各工程のトップ企業はどこなのかを探っていく。
大まかな流れとしては
フォトマスク製造:半導体を作るための原板の作成
シリコンウェーハの製造:半導体の基となる材料の生成
前工程:半導体の基本となる工程
後工程:商品として出荷するための仕上げの段階
に分かれている。
マスク製造工程
回路・パターン設計
半導体チップにどのような回路を配置するのかを設計し、半導体の用途に合わせて回路を設計する工程。
シミュレーションを何度も繰り返すことで、半導体のチップの上に効果的なパターンを生成できる。
代表的な企業
NVIDIA、ARM
フォトマスク生成
上記で生成した回路のパターンを透明なガラス版に書いて作成する。
今後このフォトマスクをシリコンウェーハ上に転写して作る。半導体を製造するための原板にあたるのがフォトマスク。
代表的な企業
・HOYA
・大日本印刷
・凸版印刷
シリコンウェハの製造
シリコンインゴットの切断
まず、シリコンインゴットと呼ばれる、シリコンの塊を薄くスライスし、シリコンウェーハを製造する
代表的な企業
信越化学工業、SUMCO
シリコンウェーハの研磨
細かく切ったシリコンウェハの側面、裏表面を研磨し鏡のようにする。
これによってウェーハ上の微粒子や凹凸を排除する。
前工程
シリコンウェーハ表面の酸化
シリコンウェーハ上に絶縁層の膜を作るための工程である。高温の酸素によってウェーハーを酸化させることで、酸化シリコンの膜を作る。
この酸化シリコンの膜は、「トランジスタ」と呼ばれる電流を増幅させたり、スイッチのオンとオフを切り替えるような特性を持つ電子部品の構成要素になる。
シリコンウェーハ表面の薄膜形成
シリコンウェーハの表面に様々な材料の薄膜をつける工程。
酸化膜の上にアルミニウムやガスなどの薄膜を生成する。薄膜をつけることと、不要な部分を除去することを繰り返すことで、複数の層が作られる。
フォトレジストの塗布
フォトレジストと呼ばれる感光材をウェーハ表面に均一に塗る。
今後、原板を半導体上に転写するために感光材を塗ることで、回路パターンをウェーハ上に焼き付けることができるようになる。
ウェーハを回転させながら塗ることで均一にフォトレジストを塗っていく。
代表的な企業
東京エレクトロン:レジストを塗布する機会でシェア9割ほどを持つ
東京エレクトロンについて語る|ソクラテス@個別株情報発信 (note.com)
フォトマスクのパターン転写(露光・現像)
シリコンウェーハ上に、フォトマスクの回路を転写する工程。ウェーハ表面にフォトマスクと縮小レンズを通して光を照射して回路のパターンを焼き付ける。フォトレジストに露光された部分は、現像液で溶かしてパターンが転写された部分を残す。
感光した場所が除去されるポジ式と、観光しなかった場所が除去されるネガ式がある。
代表的な企業
ASML:シェアは9割ほどで独走状態
エッチング
フォトレジストの露光によって形成されたパターンに沿って、作成した酸化膜と薄膜を削り取る。
フォトレジストに覆われている部分は残る。
代表的な企業
・東京エレクトロン
・ラムリサーチ
2社がトップを取り合うような関係性
レジスト剥離・洗浄
残っているフォトレジストを剥離させて、薄膜を露出させます。
その後、ウェーハ上に残っている不純物を焼く液に浸して取り除く。
代表的な企業
・SCREEN、東京エレクトロン
イオンの注入
シリコンウェーハに電気的な特性を持たせるためにドーパントと言われる不純物イオンを注入し熱処理によって活性化させる。
このイオンを注入することで半導体に電気を通せるようになる。
代表的な企業
アプライドマテリアルズ:ほぼ独占的なシェアを持っている
シリコンウェーハの研磨
シリコンウェーハの表面は、研磨し凹凸がなくなるように平坦化する。
このようにして表面をきれいにした後に、再度今までの前工程を行い、層を重ねていく。
この表面化の精度は甲子園球場の中に花粉が一つ落ちていてはいけないレベルの精度で研磨される。
電極の形成
チップの内部とチップの外部を電気で繋ぐために電極配線用の金属をウェーハに埋め込む。
電極を絶縁膜上に引き上げるため、酸化膜にコンタクトホールと呼ばれる穴をあけて内部と外部を接続する通り道を作成する。
ウェーハ検査
ウェーハ上にある数百個のチップすべてを検査する工程である。チップの傷や汚れ、サイズ、電気的な異常などをプローブと呼ばれる針を接触させて検査をする。
代表的な企業
KLA
後工程
シリコンウェーハのダイシング
シリコンウェーハをダイヤモンドブレードで切断をする工程。シリコンウェーハをチップに分離して製品として使える良質なチップを分けて切り出す。
代表的な企業
・ディスコ
・東京精密
ワイヤーボンディング
チップとリードフレームという金属製の枠を約25μm(1μmが1mmの1/1000000)の金線でつなぐ作業。
これによりちっぷんとの配線が可能になる。
チップのモールディング
チップを傷や衝撃、ホコリなどから守るために樹脂やセラミックで包み込む作業。
最終検査
半導体をリードフレームから切断・分離して、半導体製品として成型する作業。
製品の初期不良を減らすため、異常がないか何重もの試験を行い、不良品を取り除く。
以上が半導体製造の全工程になる。
正直気が遠くなるような工程数だが、精密な製品ゆえに多くの工程や検査が必要になる。
半導体の工程についてまとめました。引き続きわかりやすいような記事を上げていきますのでフォローお願いします。
また一気に投資の知識を得られるメンバーシップも公開しています!
初月無料公開しているので参加お願いします🙏
この記事が気に入ったらサポートをしてみませんか?