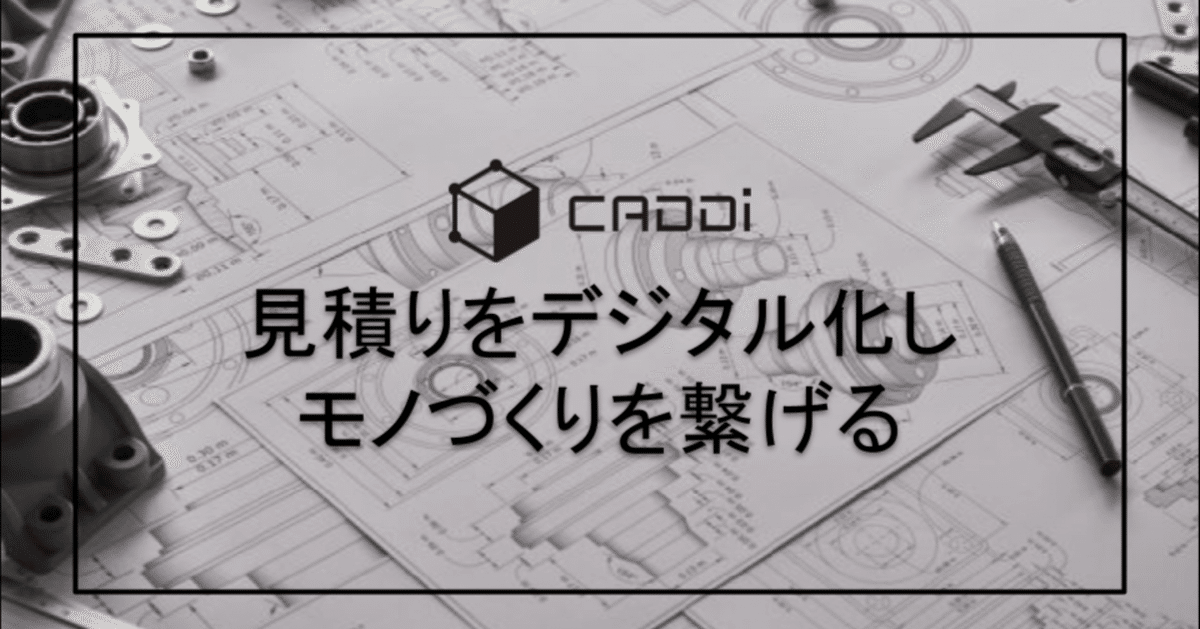
見積りをデジタル化し、モノづくりを繋げる/キャディ創業5周年に寄せて
こんにちは。創立5周年記念noteの5日目を担当します、キャディ株式会社の笹口です。
2019年6月に入社し、プロダクトマネジメント、オペレーションマネジメント、事業企画などの役割を通じて、主に見積りや原価計算、発注先パートナーの選定といった領域の仕組み化を進めてきました。
現在はコストアルゴリズムグループの責任者として、原価計算の仕組みに関わる事業・テクノロジー両面のマネージャーを務めています。
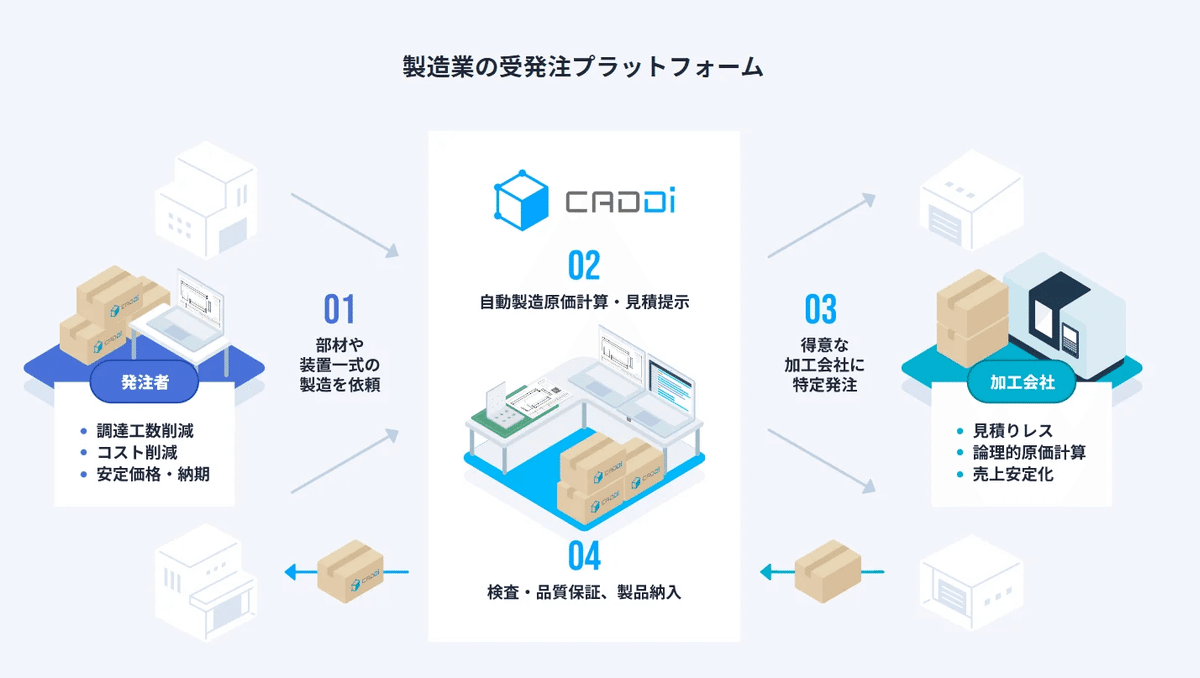
このnoteでは、キャディ創業5周年という一つの区切りに合わせて、これまでの見積り・原価計算の歩みに触れながら、その先に目指しているビジョンについてお話できればと思います。
このnoteで言いたいことをさっくり読みたい方向けに三行でまとめると…
・製造業において、見積りは重要かつ大変。キャディは原価計算システムを用いた見積りのデジタル化に創業以来挑戦してきた
・地道なシステム構築を通じ、見積りの省力化と見積りに伴って生じるデータのアセット化を実現。機械学習モデルの開発といった更なる付加価値の創出に繋がりつつある
・今後は、生産工程改善との連動や、原価計算に限らない用途へのデータ活用を進め、将来的には製造業における”標準プロトコル”の実現に繋げていきたい
1) 見積りは難しい
まずはじめに、見積りというものの難しさについて触れます。
キャディにおける見積りは、世間のいわゆる見積りと同じ機能を有しています。お客様から頂いたご依頼に対して、いくらで対応できるかを試算し、結果を見積書という形で回答します。
見積りとは、金額や量、期間などを前もって概算することを指します。
かかる金額や期間が明確なもの(例:電車での移動、ECでの商品の購入など)であれば、さほど難しいことはありません。
しかし、それらが一つでも失われた途端に、見積りは大変難しい作業へと変貌します。身近な例として「引越し」を挙げます。
引越しは業者や繁閑、物量などによって価格が大きく変動します。利用者はなるべく安く収めたいですし、業者はなるべく適正な価格で受注したいと考えます。
そのために行われるのが相見積や訪問見積です。相見積を取ることで、利用者は複数業者の価格を知ることができ、その範囲内で最も条件がいいものを選ぶことができます。また業者はというと、訪問見積によって現物を確認しながら所要時間や必要なトラックの台数を試算することができるため、きちんと利益の出る価格を見積ることができます。
これらは一見とても良さそうなのですが、代わりにいくつかの問題を生じます。
これらの行為自体にコストがかかるが、結果的に良い条件に出会える、受注できるとは限らない
行う人のスキルや経験値によって結果がぶれる
製造業の受発注においても、実は全く同様の課題が存在しています。
提供されるスペックや価格、納期が明記されているカタログ品も存在しますが、キャディが取り組む多品種少量生産は毎回新たに製品が設計され、価格や納期については設計指示情報が記載されたCADデータや図面を介して都度見積りを取ることが通例です。ここでもやはり相見積が行われます。
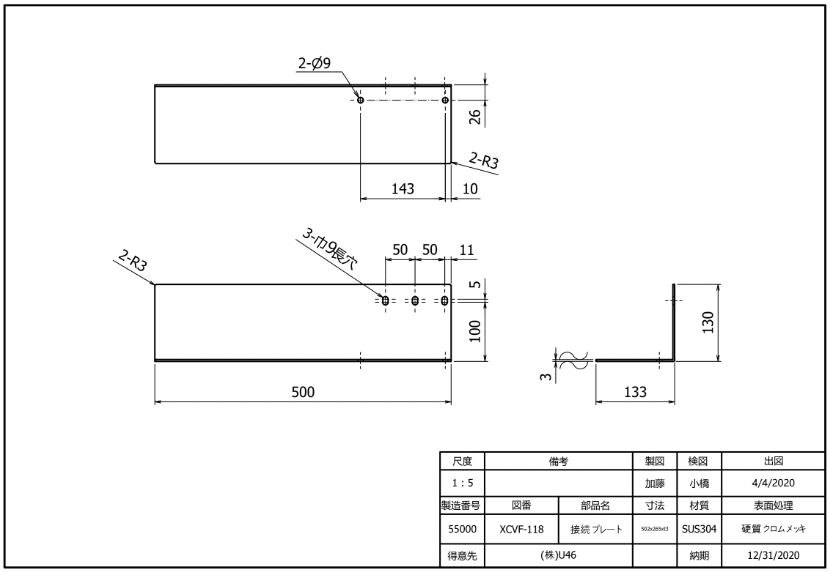
見積りを取る側の加工会社にとって、これは非常に難しい作業です。事前にサンプルを製作するケースもありますが、多くの場合は設計指示情報からどのように製作するか、それにどの程度の時間がかかるか、歩留まりはどの程度かを長年の経験から予測し、価格を概算しなければいけません。
そのリスクの高さから社長や営業責任者などが見積ることも多く、単にコストが高いだけでなく、経営層や管理職が本来他の業務に当てたい時間も見積りに当てざるを得ないという問題も発生しています。
見積りは受注に向けた最初の工程であり、見積りを通過した案件の合計値が売上の最大値となるため、ここにボトルネックを生じさせないことが経営上重要なのです。
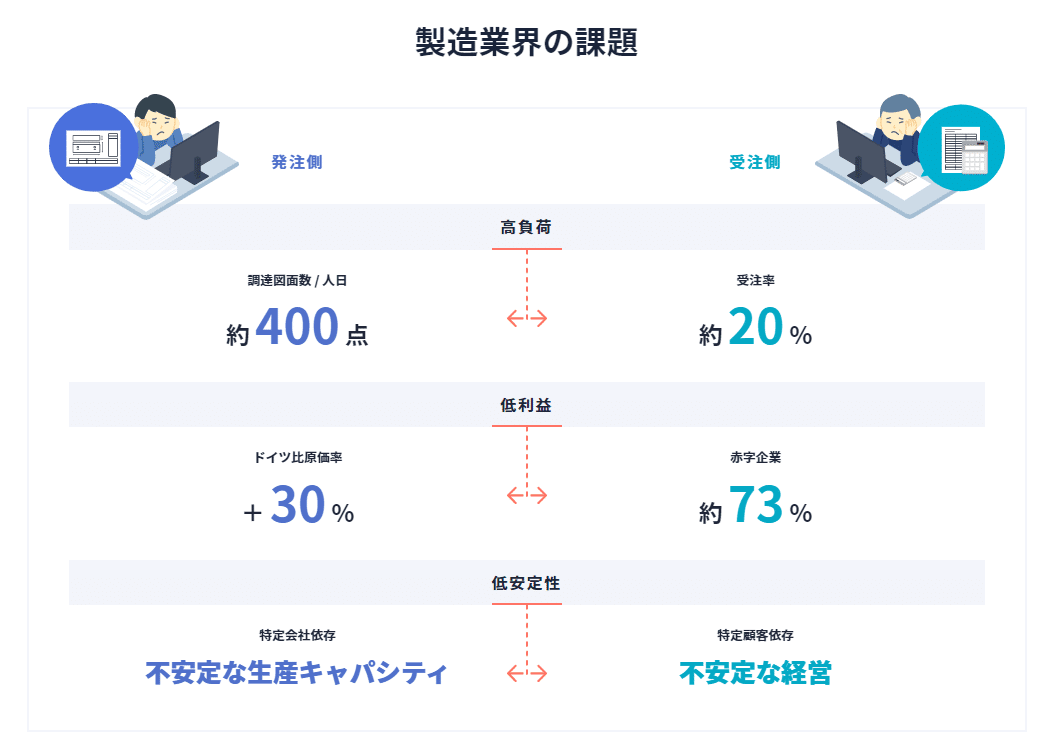
言い換えるならば見積りとは、本来はやってみないとわからないという不確実性を前もって可能な限り下げることで、受注機会の最大化と経営リスクの最小化を両立させる行為であり、売上と利益の創出に直接的な影響を与えるとても重要な作業です。
キャディでは、創業当時からこういった見積りの課題を解消することに取り組んできました。すなわち、見積りにおける属人性の排除と、精度向上及び均質化の実現です。そのために我々はコストモデルと呼ぶ関数の集合体を構築し、創業以来改善を続けてきました。
2) 見積りのデジタル化
キャディは、自社開発の原価計算システムによって、見積りのデジタル化に取り組んできました。
2-1. コストモデルによる原価計算
原価計算をシステムで行う、という発想は決してユニークなものではありません。大手メーカーをはじめ、多くの企業が独自の原価計算システムを構築していますし、またそういったシステムを販売しているベンダーも数多く存在します。これは見積りにかかるコストや属人性の課題が普遍的かつ大きいことの証左ともいえます。
キャディでは、前述のコストモデルをQuipuという原価計算プロダクト上で操作することで、原価計算のシステム化を行っています。CADや図面に基づいたINPUTデータを用い、自動的に原価計算を行う仕組みです。
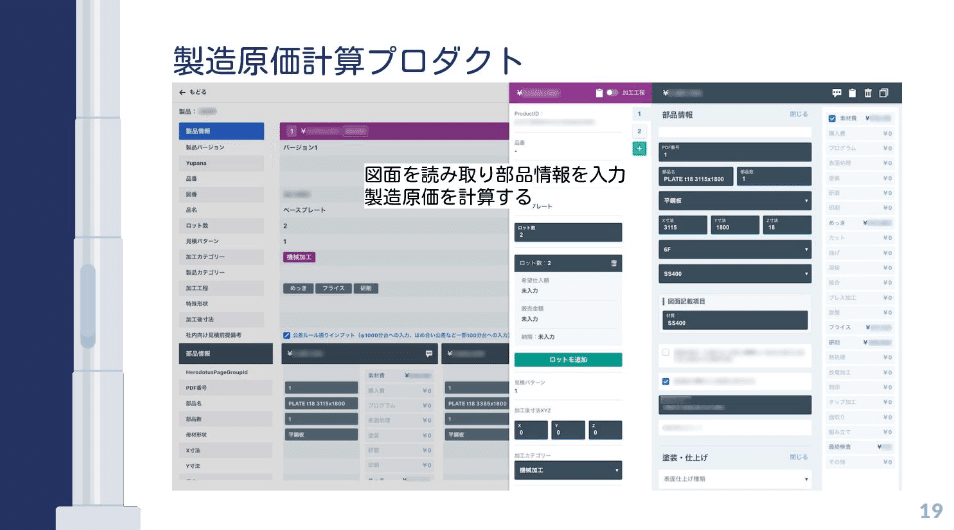
原価計算のシステム化で望まれるメリットは、属人性の解消と見積りの省力化です。従来見積担当者が行っていた判断をプログラム化して他社員でも扱えるようにすることで見積担当者を増やし、各処理の自動化によって省力化を叶えることが期待できます。
一方のデメリットとしては、システム構築及び運用にかかるコストがあげられます。日本ではオンプレミスで独自システムを構築する企業が多く、構築にはざっくり500~1000万円程度はかかります。
加えて、システムの中長期的な保守運用が必要になりますが、保守案件に追加費用がかかるケースが多く、ここを含めて完全に機能させられている事例は決して多くありません。システムは構築したが使い物にならなかった、システムを扱うこと自体が職人芸化している、といった事例は少なからず耳にします。
しかしながら、私はむしろこの保守運用にこそ、原価計算システム化の要点があると考えています。
材料費が上がった、人件費が上がった、新しい機械を導入して加工速度が向上したなど、正確な原価計算を行うための前提となる情報は日々変わっていきます。これが属人的な見積りであれば担当者が頭に入れさえすればよかったのですが、原価計算システム化のメリットを享受するには、システムを改修する必要があります。システム改修が追い付かなければ正しい値を得られなくなり、いずれ元の属人的な見積りに回帰してしまいます。
つまり原価計算システムは、変わり続けることを前提としたシステムであるべきなのです。言い換えると、原価計算システムには高い可用性が求められます。パッケージ製品ではここが叶いづらく、スクラッチで内製したとしても持続的な運用体制の構築や属人化などの組織課題と向き合い続ける必要があります。
原価計算はキャディのMANUFACTURING事業におけるコアな機能として位置付けられ、経営に非常に近いところでコストモデルの改善を続けてきました。継続的な投資と地道なシステム改善により、毎年x倍で急速に成長する事業にあって、見積りをボトルネックにすることなくここまでこれたと自負しています。
2-2. データのアセット化という価値
原価計算システムの構築にあたって、見積りの省力化と並んで重視してきたのがデータのアセット化でした。ここでいうとデータとは、原価計算のINPUTとなるCADや図面データとそこから読み取った形状情報、原価計算結果の出力データなどを指します。
データのアセット化については、先日公開された代表の加藤のnoteに詳細に触れられておりますので、是非ご参照ください。
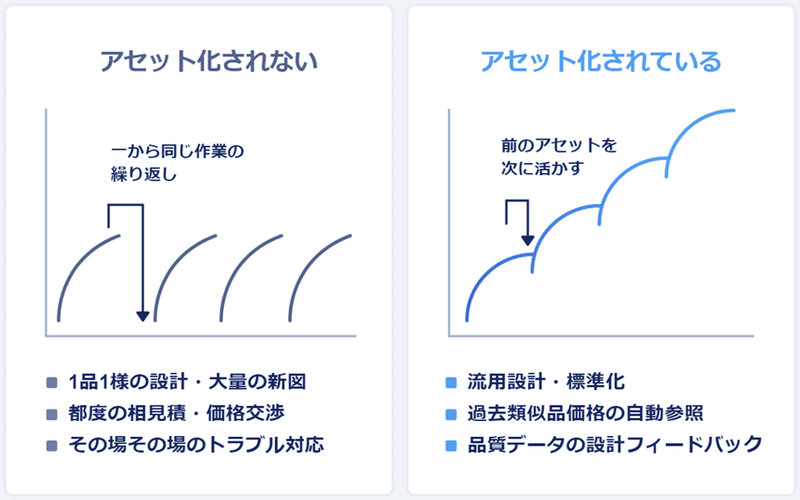
キャディのコストモデルは、主に製品の形状情報からその実現に必要な加工工程を推定し、工程ごとに原価を算出します。そのため、上述したようなデータを蓄積することが可能です。
しかしながら、私が入社した2019年当時はこれらを構造化されたデータとして蓄積できておらず、日々貴重な資産が失われている感覚を持っていました。そこで、原価計算システムの構築に合わせてIA(情報設計)を行い、INPUT/OUTPUTデータが構造的に蓄積され、活用できる環境を整備しました。
特にアセットとしてすぐに効果を発揮したのが、図面データと紐づけて蓄積した製品の形状情報でした。
図面は画像データとして保存するため、システム的に処理する難易度がどうしても高くなります。一方、それを所定のデータフォーマットに変換し、データベース上で機械的に扱いやすい形で保持できる形状情報と合わせることで、例えば最適な発注先の選定であったり、機械学習モデルの構築であったりと、様々な用途に活用することができました。発注実績データやNG情報など、他のデータと紐づけて分析することもでき、オペレーションの効率化にも寄与しています。
見積りのデジタル化とは、原価計算/見積りをシステムで行うことによる属人性の排除と効率化。そしてそれに付随するデータのアセット化による更なる付加価値の創出を実現することです。それにより、見積りの制約を受けずに成長した事業がより多くのデータを生み出し、そのデータから創出された付加価値がさらに事業成長を加速させるという正のスパイラルを生み出すことができるのです。
3) コストモデルがモノづくりを繋げる
見積りのデジタル化によって事業成長に寄与してきたコストモデルですが、既に次の進化を見据えた取り組みを始めています。それは、より有機的にモノづくりをデータとモデルで繋げる取り組みです。
3-1. CFSとしてのコストモデル
CFSとは、CADDi Factory Systemの略で、一言でいうと「サプライパートナーの QCD-FIT するキャパシティを創り出す仕組み」です。
多品種少量~中量産の製造コストにおいて固定費も変動費も下がりづらいジレンマを、あらゆる工場においてスケーラブル(再現可能・低属人性)に解消し、製造機能にイノベーションを起こすためにキャディが投資しているのが、”CADDi Factory System(通称CFS)”です。
具体的に CFS が持つ特徴は大きく2つあります。
・多品種少量であっても製造コスト・生産キャパシティ・品質のレベルを大きく上げることができるパッケージである
・そのパッケージは一定の強みの源泉(=ポテンシャル)を保持している会社であれば、誰でも簡単に利用でき、スケーラブルである
CFSについてはこちらのnoteに詳細がありますので、是非ご覧ください。
河野のnoteにも書かれているように、キャディはある時から「QCD-FIT するキャパシティ(いわゆる青い鳥)を見つけてくるのではなく、取引のあるサプライパートナー・今後取引させていただくサプライパートナーと一緒に成長していこう、という大きな戦略転換」を行いました。
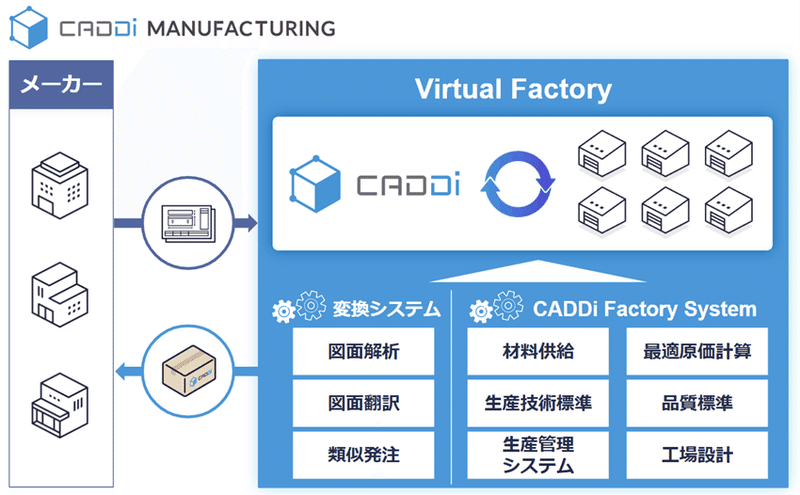
これに対してコストモデルは、世界トップレベルの生産工程を自動的に再現できるコスト計算アルゴリズムの実現という点で連携を図っています。
基本的に、コストモデルの改善は様々なフィードバックをトリガーとして行われますが、ここにCFSによる生産改善結果という力強いフィードバックが加わることになります。
コストモデルによる自動的な工程再現機能によって、現場での生産改善と見積業務とが連動し、より競争力のある原価の算出を可能にしているのです。
3-2. 標準プロトコルへの進化
CFSとの連携に加えて、今のコストモデルが見据えるもう1つの未来が「標準プロトコルへの進化」です。
全世界が共通のプロトコルに従って通信を行えることで爆発的に発展したインターネットと比較すると、製造業が個々に構成するネットワークは、過去からの慣習に基づいた独自のプロトコルを有している傾向があります。また、デファクトスタンダードと呼べる規格やシステムがないことによる規格の乱立、共通フォーマットの不在という問題も根深く、デジタル化の恩恵を受けづらい要因となっています。
製造業の各産業やクラスタをまたいで通用する標準プロトコルの構築は製造業の更なる発展に欠かせないものであり、その実現はキャディが目指す大きなゴールの1つです。
私は、コストモデルの進化こそが、この標準プロトコルの実現に向かう道程であると確信しています。そのためには、達成しなければならない大きなマイルストーンが2つあります。
原価計算用フォーマットから、Machine Readableな共通データフォーマットへの進化すること
キャディが力をつけ、そのフォーマットがキャディ社外でも活用される状態を作り出すこと(デファクトになること)
2点目の実現に向けては、ただただキャディの事業成長の実現に向けて邁進するのみですが、1点目の実現は戦略的に為す必要があります。既に一部原価計算以外の用途でもコストモデルのデータは活用されていますが、この用途を広げ、例えば製造や品質管理などへも共通で活用することができるデータフォーマットを再設計していくことが必要です。
その一環として、弊社の寺田が構想しているMO CADというコンセプトがあります。下記のブログにて詳述していますので、是非ご覧ください。
この標準プロトコルの実現に向けては、コストモデルの進化が必要不可欠なのです。我々が日々向き合うモデル改善こそが、コストモデルの進化の種であり、製造業における標準プロトコル実現に向けた大事な一歩であると考えています。
4) ビジネスとテクノロジーの合わせ技が求められる面白さ
そんなコストモデルの進化を担うコストアルゴリズムグループですが、新しい仲間を積極的に募集しています。
コストモデルアナリストの特徴は、ビジネス・分析・プログラミングの3つの要素を求められる点にあります。
パートナー経営層との交渉におけるビジネスディベロップメントスキル、モデル構築のために取得したデータの分析、Pythonを用いたコストモデルの実装などがそれにあたります。
当然ながら、全てを1人で行う必要はありません(できる人もいますが)。
Bizdev、分析、Pythonのうち得意な領域を活かして活躍しながら、各々が伸ばしたい領域でも経験が積めるよう配慮しています。海外のパートナーが増えている傾向を受け、海外出張の機会に恵まれている点も特徴です。
また、コストアルゴリズムグループにはTECH本部所属のエンジニアが複数名兼務で所属しており、ビジネスとTECHが同じ目的を共有しながら協働していける環境を構築しています。
こうした環境に加えて、何よりもまずは製造業を大きく前進させうるコストモデルの取り組みとその意義に共感頂ける方に是非JOIN頂きたいと考えています。少しでもご興味あれば、是非気軽にカジュアル面談にお申込みください。
最後に
「言うは易しで、確かにできたらすごいけど、さすがにこれは無理だろう」
これは、最初にキャディの事業内容を知ったときの私の感想です。笑
そんな考えを抱きながらも好奇心を止められず、面接に応募し、「もしかしたらできるかもしれない」と考えが変わり、それでも悩みに悩んで入社を決めてから、3年半が経とうとしています。
この間、いくつか役割を変えながら、ずっと見積り/原価計算の進化に携わってきました。改めて、一筋縄ではいかない取り組みだと感じます。
キャディに来てからも、何度も「もう無理じゃないか」と思ったことがありました。しかし振り返ると、確実に前に進んでいますし、頼もしい仲間も増えました。
自分たちが手掛けている取り組みが、もしかしたら明日の製造業をもっとよくできるかもしれないというわくわくも、擦り減る気配を見せません。
しかしそれでも、まだまだたくさんの仲間と時間が必要な取り組みです。
「大変そうだなぁ、でも面白そうだなぁ」と感じて頂ける方がもしいらっしゃいましたら、是非一緒にお仕事してみませんか?
ということで、最後までお読み頂き、ありがとうございました。是非Twitterのフォローもよろしくお願いします。
この記事が気に入ったらサポートをしてみませんか?