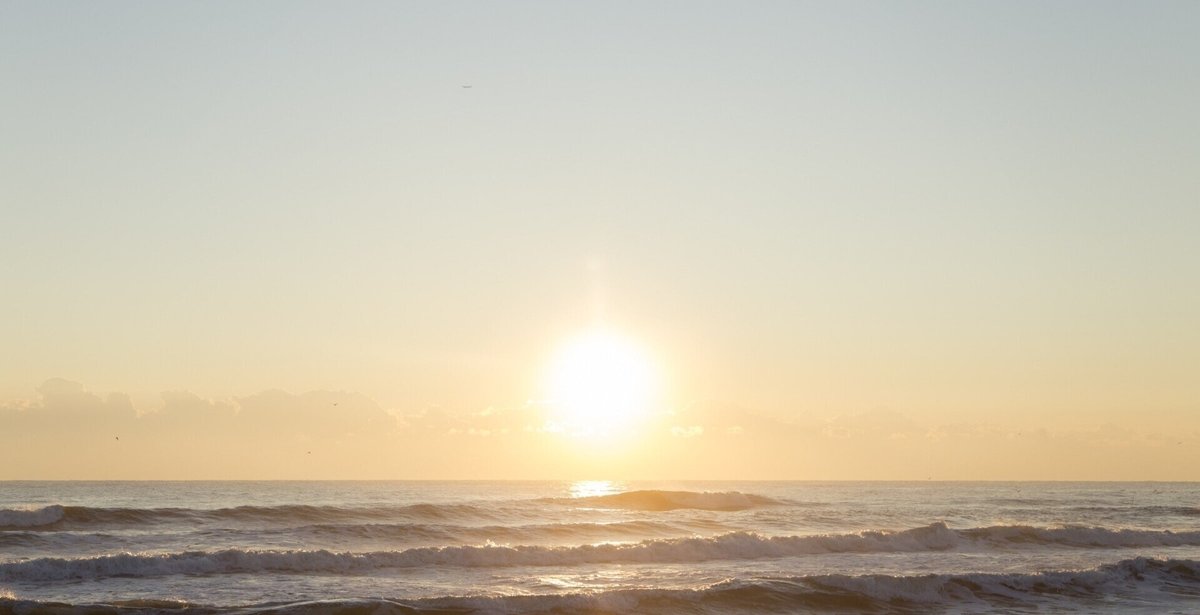
値上げ、値上げで不安です。
皆さん、こんにちは!
パッケージ製造を佐賀で営む石:::.川大二朗です!
今週も日曜日がやってきました。
1,111日に向かって、チームでコツコツと!
本日も元気よくブログを繋いでいきたいと思います。
よろしくお願いします。
昨日のブログは、黒田..拓也.さんの
『非常識が常識へ』という内容で、
家具業界の価格高騰のお話を交え、
家具の買い時を記載いただいています!
本文にも触れられておりますが、
これは家具業界に限ったことでなく、
パッケージ業界でも今春から今夏にかけて
大幅な資材の値上りが叫ばれています。
全般的に物価を上げざるを
負えない状況になってくるかもしれませんし、
下請けメーカーは、よりダイレクトに
お客さまに販売し、
粗利を確保しながら安く提供できる方法を
考えていかなければならなくなってきます。
または、いかにお客様に価値を
共感していただけるか、付加価値の高いサービスを
提供する方に舵を取るべきでしょうか?
社内の方をみると、給与水準のUPは、
当然のように、対応できるように経営をしていかなければなりません。
ものづくりメーカーも、
大幅に変化が求められる状況に
本格的に突入してきた感じが非常にしてきますね。
とはいえ、長期・中期・短期と先を考えながら、
長期的な部分は、なかなか時間はかかりますので、
割り切った上で焦らず、
一歩一歩着実に前に進んでいくしかありません。
短期的な部分では、
資材の値上りにどう対応していくか。
ということが必要になってきそうです。
資材が上がったので、全てお客様に被ってください!
とはいかないもので、
社内での努力がもちろんに必要になります。
改善に繋げるための数値化が重要
社内での企業努力は、
仕入れ面であったり、
多々対策はあると思いますが、
製造の観点から記載させていただきます。
製造業では、いかに安定して生産活動が出来るか、
が重要な要素の一つだと思っています。
1日100個が生産の上限だとしたときに、
今日は、残業して120個、翌日は40個の生産だった。
なんていうよりは、
今日が80個で、翌日も80個の生産の方が、
同じ160個だとしても、良い分けです。
80個を基準値にしていると、
3か月後には85個を平均値にするためには、
どうすれば良いのか??
もしくは、
倍の160個を基準値にするためには、
どうすれば良いのか?
と作業内容の改善がやりやすくなります。
恐らく、
なぜ40個の生産しか上がらなかったのか?と
質問を振ったとしたら、
返ってくる返答は、
前日に120個も作ったので前準備が出来ていませんでした。
という昨日は頑張りました!みたいな内容が返ってくることでしょう。
現場は、一時的な120個は、
そもそもキャパオーバーなので、
やり遂げるためにガムシャラになるかと思います。
そうすると、上述のように、
どうすればもっと!という思考をする余力がなくなると思います。
翌日は、40個と数的に少ないので、
そもそも改善を、と考えません。
だからこそ、考えるために、
安定した数値基準を整えることが重要だ、と思っています。
また、実体験としては、
なぜ40個??という話をし続けると、
結論、現場からキレられます。
それは、120個というキャパオーバーを
必死に対応してくれた感情があるからです。
120個と40個が発生する仕組みなのに、
40個に焦点を当て続けると
120個の努力を見られていないと感じますよね。
これは、確かにキレます。
ですので、淡々と生産できる現場づくり、
は業績的にも現場的にも、
ゆとりを持ちやすくなるために、
重要なことだと思います。
■最初に取り組んだこと
まだまだ、会社も小さく、
未熟で駆け出しですので、
参考になるか分かりませんが、
今までの中で、大事だと思ったことをシェアさせていただきます。
①自社の現状の生産能力を知る
②他社から学ぶ
③注文状況を調整する(短納期を恒常化しすぎない)
①自社の生産能力を知る
自社がどれくらい作れるか、をデータ化(見える化)しないと始まりません。
どういう作業があるのか?その作業はどういった時間がかかっているのか?
当社では、7年ほど5S活動を実施いてきましたので、その取り組みの中で、タクトタイムを出しながら作業内容の精査を行っています。
まだまだ、出来ていないところも、多いですが少しずつ進めています。
②他社から学ぶ
同業他社の会社さんに連絡をさせていただき、
現場見学をさせていただきました。
これは、一番重要かと思います。
自社の当たり前に対する違和感は、
何かと比較して、でないと分かりません。
同業さん以外でも製造の現場を
見学させていただくことで、
自社が勝っているもの、足りていないことや、
改善ができそうなヒントを沢山、
見つけることができます。
基準値についても、当社の数値は、
当たり前なのか、ということも
再度見直しができます。
お願いすることは、無料ですので
相談してみましょう。
僕の場合は、皆さん新参者として、
可愛がってくださる
優しい同業者さんばかりでした。
③注文状況を調整する(※当社は受注生産です)
家業に戻ったばかりの頃は、
手書きや、FAXの紙で注文を管理していました。
そうすると、今の注文状況を常に電卓で計算しなくてはいけないので、非常に非効率でした。
正確に把握できておらず、納期が偏ってしまったりすることで、
120個から40個の生産みたいな非効率な状況が、実際に多発していました。
データで管理することにより、お客さまとの納期調整もその場で返答でき、現場にも突発的な負担を避けやすくなりました。
--------------------------
上記は、帰ってきて
初めの頃に取り組んで経験した一部になります。
無暗に、営業で案件をガムシャラに取ってくると、現場から喜ばれません。
120個から40個みたいな、
ことを恒常化していると、
現場の残業代も嵩みますし、現場は負担がかかり、
頑張ってます!感が増える一方で、利益は上がりにくくなります。
結局、社員さんに対して還元できない。。という負のサイクル。
上記の改善だけでも、年間の生産数量は、
多少予測してコントロール出来るように
なりますし、資材の値上げに対して、
どこまで生産数をアップしなければならないか、
予定が組み立てられます。
これから、値上げは、度々発生してくる可能性はあります。
ですので、資材値上げしたから、
当社も同じく値上げ!と対処していけると思えません。
出来ることから、努力をしていきましょう!
(もちろん、適正な値上げは大事です。)
正直、コロナ返済もありますし、
経済状況も不安定で、資材も値上り、
となると不安で不安で仕方ないです。
ただ、不安は、先が分からないから起こることです。
不安を解消するためには、
先の計画を見える化するしかありません。
資材費の値上げは、非常に頭が痛い部分に
なりますが、自社と向き合い、
お客様と向き合いながら、
乗り越えていきたいと思います。
今年は、製造の仕組みづくりを改革をしていく年にしますので、
また、実体験(学び)を共有させていただければと思います。
今週もありがとうございました!
来週は、いつも心温まるブログをアップしてくれる、堀たつさんです。
楽しみにしています~!