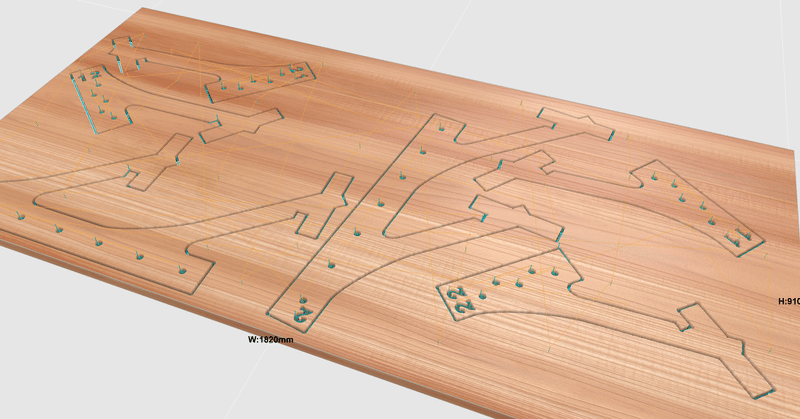
【EMARF】地獄組取り付けプロジェクト -設計編-
こんにちは、ND3MのAZUです。
今回は、地獄組プロジェクトの設計編ということで、EMARFを使いどのようなデザインをしてきたか、というところを紹介したいと思います。
プロジェクトの概要については、こちらをご覧ください。
なぜ今回EMARFが適しているか
具体的な設計に入る前に、今回EMARFを使用して感じた利点をまとめてみます。
・複雑な形状の加工ができる
・オンラインで設計から発注までが完結する
・費用が明確である
・慣れ親しんだ木材である
・施工を簡単にする工夫ができる
・とにかくわかりやすい
・複雑な形状の加工ができる
今回は、取り付ける対象(地獄組)がすでにありますが、天井に取り付けるために作られたものではありません。そのため、地獄組と天井との間で、うまく合わない部分を今回作成する部材で吸収する必要があります。
そのため、うまく合うように目視でモデリングした結果、寸法はキリのいい数字とはならず、自分で加工しようとするとかなりの労力です。しかし、EMARFならデータをそのまま加工できるため、複雑な加工へのハードルを一気に低くしてくれます。
複雑な形状でなくても、寸法を気にせずフリーハンドで作画した後、EMARFプラグインで加工可能な形状に変換できる(角のフィレットなど)ため、とても簡単に自分のつくりたい形をつくることができます。
・オンラインで設計から発注までが完結する
今のコロナ禍で、オンラインでプロジェクトを進めなければならなかったということもあり、プロジェクトを進める上で無くてはならなかった要素です。
しかし、今回のような場合以外でも大きなメリットがあると思います。EMARFという一つのサービスに設計の支援から配送までが組み込まれているため、手順もスムーズで、明確です。加工品が手元に届くまでに経由するサービスがEMARFのみなので、打ち合わせなどのやりとりで生じる設計者の負担も軽くなります。
また、オンラインで完結するということは、地方や都心関係なくサービスを利用できるということでもあります。これまで加工場所や環境の問題で諦めていたものも、気軽に実現できるようになるのではないでしょうか。
・費用が明確である
自分で加工する時でも加工を依頼するときでも、最終的にかかる費用がどれくらいなのかということが分かっていることはプロジェクトを進める上で大きな安心材料になります。EMARFでは、データをアップロードすると費用の概算が表示され、材質や厚さを変えながら何度も試すことができます。形状を変更した際にも都度確認できるため、安心して作業を進めることができました。
・慣れ親しんだ木材である
木は生まれたときから身近にある素材です。いくらオンラインで完結するといっても、やはり具体的なイメージが湧いたほうが設計はしやすいと感じます。慣れ親しんだ素材でなので、施工と完成のイメージがしやすく、設計をスムーズに進めることに繋がりました。
また、自分で加工することも簡単にできます。EMARFで届いた部材を削ったり、切ったり、塗装したり、と、自分の思い描く形に向けて様々な加工ができ、自由度をさらに高めてくれます。
・施工を簡単にする工夫ができる
こちらは適用できる範囲が限られていまいそうですが、今回の場合施工のガイドとなるような下穴を開けたり、どの部材かすぐに判別できるよう部材の番号を掘っておいたり、というような工夫をしました。もともと後で加工を追加する予定でも、その助けとなる工夫をすることで、面倒なことは機械に任せ、人の手で行う作業を楽にしていくことができました。
・とにかくわかりやすい
と、ここまでいろいろ書いてはきましたが、全てに共通していることは、わかりやすいということです。
これまで書いてきたように、わかりやすくて明確なサービスであるだけでなく、チュートリアルが動画やドキュメントで用意されており、それでも困ったときには気軽に問い合わせることができます。また、無料で初心者向け説明会や相談会もあり、とりあえず使ってみよう、という気にさせてくれます。
それでは、実際にEMARFでどのようなデザインをしていったのか、紹介していきます。
配置の調整
まずは、地獄組が鑑賞しないように位置を調整します。
Graashopperで組んだだけの状態だと、画像のように地獄組とブレースや照明がぶつかっている部分が多数あります。
こちらをひとつひとつ修正していきます。今回の場合取り付ける垂木と地獄組だけでなく、ブレースと照明天井にあり、その間を縫っていくように配置するためかなり細かい調整が必要でした。
これらの調整は、画面上で確認するだけでなく、VRやARを活用しながら、慎重にチェックしていきました。
取り付け部材のデザイン
地獄組が配置できたところで、いよいよデザインをしていきます。
板を切り出すという加工の制約のため、垂木の側面でビス止めをして固定することにしました。地獄組本体には極力加工をせず、簡単に固定できる方法ということで、フックのように引っ掛けた後、ずれないように釘で固定する方法を考えました。
EMARFには、ほぞやあられ組など、接合部を簡単に制作できる機能もあるのですが、今回はシンプルに1枚の板のみとします。理由としては、既存部材に適合させなければいけないため現場でズレを修正する可能性が高く、できるだけ簡単に修正ができる単純な形状・固定方法にしたい、ということが挙げられます。
初期のデザイン案です。地獄組と一体となるようなデザインを考えました。
しかし、これだと枝の付け根の部分が心もとないということと、もう少しEMARFの自由な加工らしさが欲しく、案をブラッシュアップしていきました。
ブラッシュアップし、試作品の発注時の形状がこちらです。地獄組の枝の感じを取り入れながら、付け根の部分は曲線で構成しています。
配置時にも干渉のチェックを行いましたが、取り付け部材をデザインしていると、それも干渉の原因となり再び修正をしました。また、設置時には干渉していなくても、施工の際にぶつかってしまい取り付けができないということが分かった部分もあり、部材の長さや位置を微調整していきました。
施工時の干渉については、Fologramという、Rhinocerosのデータをスマホやタブレットにリンクさせ、ARで動かすことのできるツールを使用し、実際に様々な角度から地獄組を設置するシミュレーションを行い確認していきました。(こちらについても後日紹介します。)
施工にむけた工夫
先程メリットのところで述べましたが、施工を楽にするために、モデルデータにいくつかの工夫をしました。
・ビス留め位置の彫り込み
今回は垂木に対してビスを打ち込んで固定します。今回の場合、そこまでビスの位置に神経質になる必要はないのですが、目印があれば施工時に悩まずに済みます。エンドミルの直径が1/4インチなので、それよりも少し大きめで5mmだけ穴を彫りました。今回は初めての発注ということもあり、加工した断面の様子もみたかったので、多めに穴を開けています。
・部材のラベリング
机などわかりやすい場合はいいですが、今回のような、それぞれ似ているけれどすべて寸法が違い、それが大量にあるという場合、どれがどこの部材かを簡単に見分けることができると作業が大幅に楽になります。そのため、今回は部材に番号を指定し、それを彫り込むことで対応しました。完成時に番号が表に出てくるような場合は難しいかもしれませんが、今回は目立たない場所があるためそこに印字しています。
追記
部材のラベリングについてですが、最新版のRhinocerosプラグインに機能が追加されています。
emLabelコマンドで、指定した順番にラベリングをすることができ、EMARFに送信する際にラベルを指定すれば、自動で番号を彫り込んでくれます。
ラベル位置も調整できるので、今回のように手動で文字を入れる必要はなく、簡単にラベリングが可能になります。
以上追記でした。
以上のような工夫をしつつ、モデルを作成しました。
今回はテストということで、同じ部分の部材ですが、2本分つなげたもの(施工は楽だが板の歩留まりが悪い)と1本ずつバラバラにしたもの(施工は手間だが歩留まりはよい)を用意し、実際に施工してみて検討することにしました。
EMARFでの作業・発注
データが完成したら、いよいよEMARFを使用します。
チュートリアルもありますが、こちらでも簡単に紹介します。
様々なコマンドが用意されていますが、今回は部材同士の接合部もないので、とても単純です。
EMARFコマンドを適用するだけ。
ひとつひとつコマンドを順番に適用させていってもよいのですが、EMARFコマンドはそれらを一度に処理してくれます。
溝加工、穴加工(線や点にそってエンドミルの直径で溝や穴を開けます)の有無を指定し、
エンドミルの直径に合わせたフィレットも形状を指定するだけで適用されます。
そのままEMARFに送信ボタンを押せば…
EMARFがブラウザで立ち上がり、素材を選択ののち、加工データが生成され、費用の概算も表示されます。
生成したデータは、保存しておくことができます。
加工依頼を選択し、フォームを入力すれば完了です。
しばらくして、EMARFの担当者様からメールが届き、そちらで最終確認をして、正式発注となります。
到着〜取り付け
発注後ワクワクしながら待つこと数日、このようなかたちで送られてきました。
#EMARF から部材が届きました!
— ND3M (@nagoya_d3m) July 28, 2020
さっそく、やすりがけをしながら調整しています。 #ND3M pic.twitter.com/7hhSKxWSqF
開けてみるとこんなかんじです。
今回指定したのは、24mmのヒノキ合板。
バリも削られ、きれいな状態で届きました。ビス穴やラベリングのところはかなりささくれていた部分があったので、発送前にきれいにしてくれたのだと思います。(念の為、手袋着用推奨です。)
試しに地獄組をはめてみます。今回は試作ということで、地獄組が嵌る部分のクリアランスを1mmと、かなりきつめに設計しました。もちろんスムーズに嵌まらないので、やすりで削り、次回以降にむけてのクリアランスを探っていきました。今回は最終的に釘で固定するので、ピッタリ嵌るよりも、スムーズに設置できることを優先します
地獄組取り付けプロジェクト、とりあえず1組目、取付完了!
— AZU (@azusa353) July 28, 2020
今回出てきた問題点を元にモデルをブラッシュアップして、残り18本も取り付けていきます!
かなりかっこいいのでは。#EMARF #ND3M pic.twitter.com/FHsRsYz8uV
本来ならここでARを用いた施工も試してみたかったのですが、準備が間に合わず断念。人の手で計測し、位置決めを行いました。
ブレース・照明とのクリアランスはかなりギリギリで設計しましたが、モデルデータ通り、無事干渉なく設置することができました。今回のような複雑で大きさもバラバラのものを、一つ一つ手でつくるとなると時間もかかり精度も保証できないため、EMARFの利点が最大限に発揮された場面なのではないかと思います。
実際に施工してみてのフィードバック
実際に取り付けてみると、いくら事前に検証しても、やはり印象が違います。
・塗装をして、垂木か地獄組に色を合わせたい
・下に飛び出た部分の長さと太さを調整して、地獄組と印象をあわせたい
・斜めに取り付くのでクリアランスをかなり大きめに確保したい
・歩留まりを優先して、分割したモデルのほうを採用したい
これらの観点からブラッシュアップをして、残りの18本も、9月までの完成を目指して取り組んでいきます。
今回はここまで。
今後もTwitterやnoteで、EMARF学生アンバサダーとして取り組んでいることを発信していくので、よろしくお願いします!
それでは!
文責;AZU
この記事が気に入ったらサポートをしてみませんか?