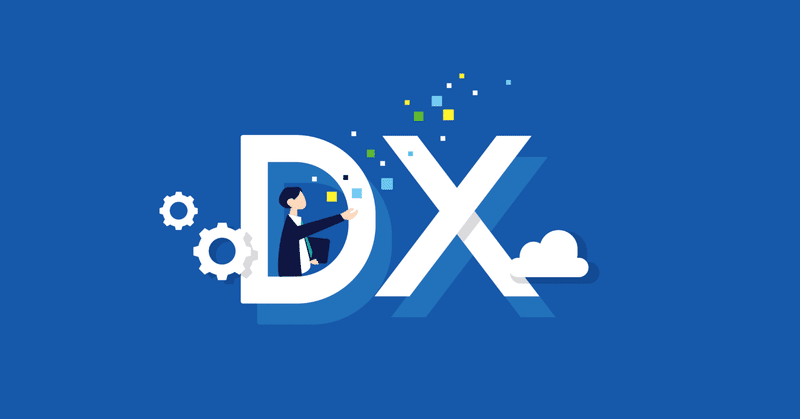
製造業のDX化
製造業のDX化に関する記事がありました。
図面が3Dデータ化されていないというおはなしですね。
日本でDX化が進まない理由は・・・いくつもあります。
あまりにもありすぎて全てを網羅することは難しいと思います。
なお、記事の中ではメーカーと外注先での3Dデータのやり取りだけを扱っていました。
※)データのやり取りそのものは30年ぐらい前からありました。
他方、記事では踏み込んでいないのですが、欧州のDX化は様々な企業が情報共有をしあうインダストリー4.0ですから、記事中で論じているのは一段低いものになりますね。
まあ、それぐらい日本の製造業はデジタル化が遅れているともいえるのですが・・・
ちなみに、インダストリー4.0の記事もご紹介しておきます。
DX化が進まない理由として、色々な意見があると思います。
それこそ異論百出するぐらいに・・・
ただ、最深部に眠る闇の部分に触れた記事は少ないです。
その闇の部分にフォーカスせずに論じたところで、海面上に出ている氷山の形だけを論じているので、すぐに暗礁に乗り上げてしまうでしょう。
下請けのジョブショップなどがこうした投資をしてこなかったことも、デジタルへ完全移行できない理由の1つになっています。
冒頭の記事の内容が浅いなあ・・・と思ったのは、上記の引用文だけで終わっているからです。
企業努力の範囲で先行投資をする。
これは経営者であれば普通のお話です。
にもかかわらず、業界全体で周回遅れとなっている。
ここに着目すべき何か? があるとして深堀しておかないといけないのですが・・・
さて、業界に身を置く経営者としては、これはもう自明のお話なんです。
それは何かと言いますと・・・
日本製造業界には工数「情報」に関するハードルがあります。
どういうものか? と言いますと、日本には、商慣習として工数x単価で値段を決めるいうものがあります。
工数は時間チャージという表現が行なわれる場合もあります・
この計算方法の大本を辿れば、元々は建設業界のもので、人工計算と呼ばれています。
製造業も昔は人海戦術が主流でしたから建設業と同じ概念で見積をしていたのです。
ですが、コンピュータ制御の工作機械が導入され始めると、無人化へ向けジワジワとシフトチェンジが起きてきました。
その結果、人工計算では現状にそぐわないことが多くなってきたんですね。
だから、工数(時間チャージ)が人工に置き換わっていったのです。
一方、QC活動やカイゼン活動が普及したことで、生産効率(工数)もめざましく効率化されていったのです。
その結果、工数をいかに削減するか?
という方向で、各社しのぎを削り合っていくようになったのです。
人工の場合は人手が主体であるため時代が変わったとしても平均的日本人が一日にこなせる肉体労働の量には大差が出てきません。
※)もちろん重機やロボットの導入で効率化の進んでいる分野も存在します。
が、製造業の場合、わずか50年余りの間に建設業の比ではない程の工数短縮現象が生じているのです。
そのため製造業では企業間で工数に大きな差が生じてしまっているのです。
製造業界は、この熾烈な工数削減競争を経て価格戦争を生き抜いてきたわけです。
まさしくカイゼン、カイゼン、カイゼンです。
その一方で問題となったのが工数を削減したという情報が顧客に漏れたら、即座に工数を削減した分だけの値下げを要請して来るようになったのです。
カイゼンしました。(下請け)
じゃあ、値下げしなさい。(発注元)
の繰り返しになったのです。
冒頭記事の引用である
下請けのジョブショップなどがこうした投資をしてこなかったことも、デジタルへ完全移行できない理由の1つになっています。
は、正しくは、投資をしなかったのではなく、投資が出来なかった、というのが正解です。
改善したら、その分の利益を削られ投資原資を奪われること
デジタル化で工数改善したと思われれば、より強力な値下げ圧力が加わること
これが、日本製造業界でDX化が進まない根源部分の理由です。
これが作り話などではなく、常態化しているといえる根拠として、
中小企業庁や公正取引委員会が警告を発している文言を挙げておきます。
現場の生産性改善など、コスト削減に向けた発注者による協力がないにもかかわらず、 受注者の努力によるコスト削減効果を一方的に取引対価へ反映させていませんか。
こんな文言がわざわざ記載されるぐらい
製造業界でカイゼン努力が搾取されるのは ”ありふれたお話” なのです。
ですから、インダストリー4.0は日本では受け入れられません。
設備投資資金もさることながら、利益が奪われるという恐怖心、この心理的ハードルの方が「べらぼう」に大きいのです。
そう考えると、むしろ人工で計算している建築業界の方がDX化が進みやすいといえるでしょう。
人間一人が出来る作業量平均は何年たったとしても、そう大きな差は生じないからです。
さて、根源部分のお話をしたあとで、もう一つの根源的な問題についても触れておきます。
今なお二次元図面が過半を占めている理由について現場サイドから説明しておきます。
それは、
日本の設計者は、ものづくりの要である公差設計を理解できていないから
です。
以下、日刊工業新聞の16年間の調査記事ですが・・・
https://pubdata.nikkan.co.jp/uploads/book/pdf_file57c912d044c42.pdf
実に、80%もの設計者が公差を企図していないという状態です。
つまり、立派そうに見える3Dデータも80%は公差設計されていないということです。
公差設計が行なわれていないと何が問題になるのか?
単純に喩えるならば・・・
頭の中で、立体駐車場を思い浮かべてください。
車高制限で1.8m以内でないと駐車設備内に入らないというのが仕様として明らかにされているとします。
普通の人は、車高が1.8m以内の自動車を購入します。
一方、何も考えていない人は、欲望のおもむくままハイエースを購入したりします。
ハイエースの車高は2m級ですから、当然、立体駐車場に入りません。
その結果、路駐せざるを得なくなります。
あるいは、全長制限を無視して道路にはみ出している車とかもそうですよね。
製造設計でも、これと同じことが起きます。
公差が設定されていない場合、各下請け企業からは、図示寸法に対し、プラスマイナスの普通許容差(JISにある公差指定がない場合の基準値)を用いて納品してきます。
で・・・
マイナス公差に仕上がっている穴にプラス公差で仕上がっているピンを挿入しようとして・・・
入らない! 不良品だ! 今すぐ修正しろ!
と怒鳴りつける事例が多くなるのです。
3Dデータだけでやり取りを済ませている場合に多い、製造業アルアル なんですよね・・・
そういった事態を解消すべく間を取り持ってくれているのが、
バラシ図面屋(二次元化部隊)さんたちです。
組立図から各部品をバラシて機械加工部品図を作成する図面屋さんのことです。
3Dデータの二次元化や、3Dデータではあるけれども公差を加味した3Dデータに置き換える業務も、彼らがこなしています。
このバラシ図面屋さんたちは、概ね中間業者や下請けに在籍している人達です。
無駄といえば無駄なのですが、3Dデータだけでものづくりを完遂させるには、設計者の技量が必要になるのです。
私も過去何度もバラシ図面屋として業務をこなしてきておりますが・・・
一級建築士の資格を取っていても公差一つ理解していない人は大勢いました。
例えば、4メートル級の梁と柱を組み合わせる際、部材の反りやネジレを考慮して丸穴から長穴へ書き換え、ワッシャの外径を大きめのものに変更する旨の設計変更承認書を提出したことがあります。
設計者の承認なく勝手に図面を書き換えるわけにはいきませんからね。
そうしたら、えらい剣幕で叱り飛ばされました。
で、設計変更が出来なくなり、そのまま部品を調達、現場で施工を開始すると・・・
組み立てられへんがな!
と、施工会社から大クレームが発生。
一級建築士は私のせいにして逃げを打ち泣く泣く修正加工を施したことがあります。
※)幸いにして事情を組んでくれた施工会社さんが順延の費用負担は求めないという配慮をしてくれましたので・・・
このように、日本では組立や工法といったことまで把握した上で設計をしている人は非常に少ないのです。
3DCADが扱えるようになれば設計者になれた気でいる人が、かなり多いです。
ですから、強度計算もしたことがない人が意外に多いです。
過去の事例から、そのままコピペしてきて使用している。
そんな感じですね。
日本の産業界のためにも、現場を知っている設計者によるノウハウ伝承が行なわれるべきかと思いますが・・・難しいでしょう。
公的機関でも、ものづくり設計講座を開講したりしていますが、彼らは机上の理論しかお話できません。
私の場合も、サラリーマン時代は設計から入り、現場はよく分からないままでした。
その後、親元に戻り現場で指揮を執っていくにあたり、実際に工作機械を動かし、加工ノウハウを習得していくことになりました。
ですから、今では加工を熟知した設計が可能になっていますし、多くの図面で荒が見えるようにもなりました。
教えても良いのですが、無名の町工場のオッサンに講義を依頼する方は少ないですね。w
まあ、私がくたばれば、私が得た知見は露と消えるだけでしょう。
実際問題として、私の知見が消滅した程度ではどうということはないのですが・・・
いずれにせよ、
公差設計が出来ない(設計者が未熟すぎる)
加工工程を理解できていない(設計者が未熟すぎる)
工数共有に関する心理的ハードル(発注側の問題)
工数削減利益吸い上げによる設備投資余力消滅(発注側の問題)
違うアプリだとデータのやり取りで問題が生じやすい(ソフトの課題)
というのは、日本のものづくりを危機的状態に追いやる原因となる事だけは間違いありません。
もちろん、DX化を押し進め効率改善を図る企業は、たくさん存在します。
ですが、インダストリー4.0のように別の企業の工場内情報にまでアクセスできるようなことが出来るようになるには・・・
国や民族が、お互いの歴史認識の差からいがみ合うことが永続しそうなのと同じぐらいのレベルで容易ではない、と考えた方が良いです。
でも、冒頭の記事にあったような3Dデータのやり取りレベルまでは十分に実現可能だと思います。
その場合、バラシ図面屋による公差付与が行なわれずに済むように設計者教育が進んでいなければなりませんが・・・
しがないオッサンにサポートが頂けるとは、思ってはおりませんが、万が一、サポートして頂くようなことがあれば、研究用書籍の購入費に充当させて頂きます。