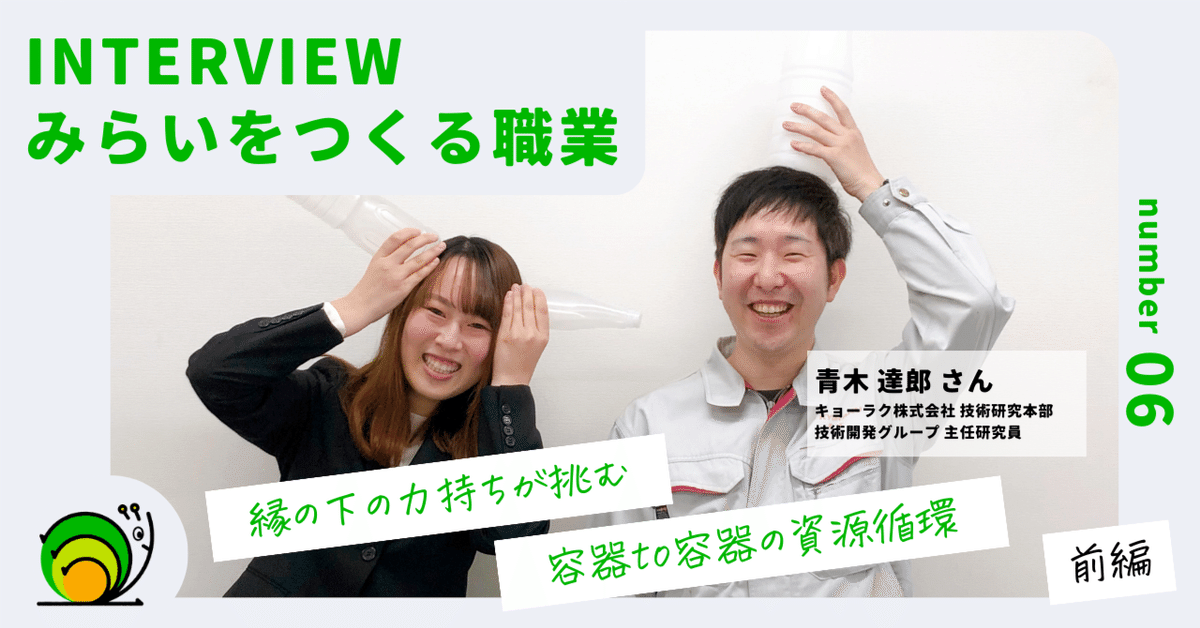
『カタツムリレポート#6 キョーラク株式会社』〈前編〉
こんにちは! 大学生カタツムリレポーターの片山知香(かたやまちか)です。今回はプラスチック製品の総合企業、キョーラク株式会社さんの大和研究所におうかがいしています。
インタビューにお答えいただくのは、大和研究所・技術研究本部主任研究員の青木達郎(あおきたつろう)さん。プラスチック容器の研究開発に取り組む青木さんに、未来につながる研究のワクワクについてお聞きしました。
「一人ひとりが循環者になる未来ってどんな未来だろう?」
カタツムリレポートは、よりよい未来をつくろうとする人達や研究者の方に、その研究や取り組みのワクワクをご紹介いただくインタビュー記事です。子どもたちが「みらいをつくる職業」をもっと身近に感じられるよう、参加企業や研究者の取り組みにググッとフォーカスしてお届けします。
ーーーーーーーーーー
このnoteは、JST「共創の場形成支援プログラム(COI-NEXT)」地域共創分野(慶應義塾大学×鎌倉市)リスペクトでつながる「共生アップサイクル社会」共創拠点の循環者学習分科会が運営しています。
話し手
キョーラク株式会社 技術研究本部 技術開発グループ 主任研究員 青木達郎 様
聴き手
株式会社高山商会 片山知香
(取材:荒井理美 / 撮影:蓮見洋平 / テキスト:原悠瑞)
キョーラク株式会社 大和研究所におじゃましました
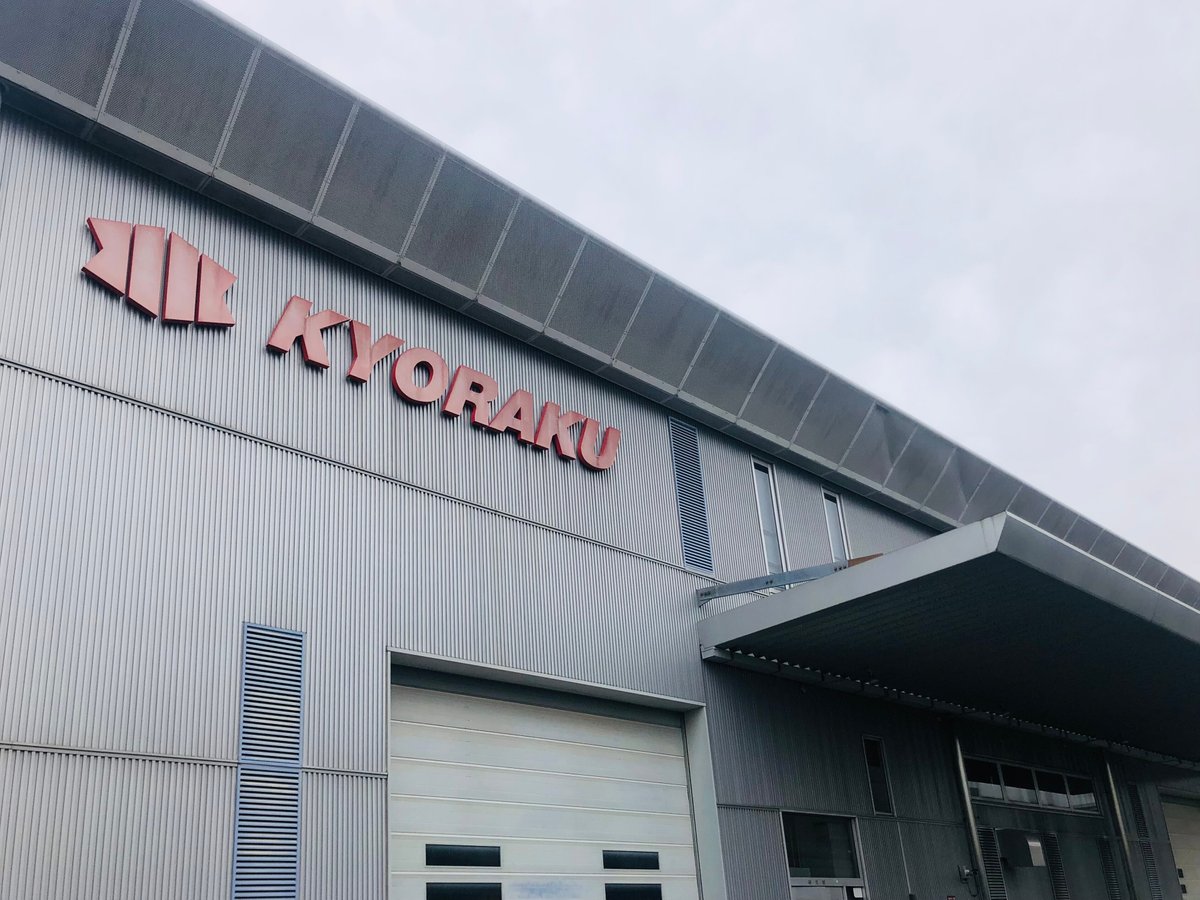
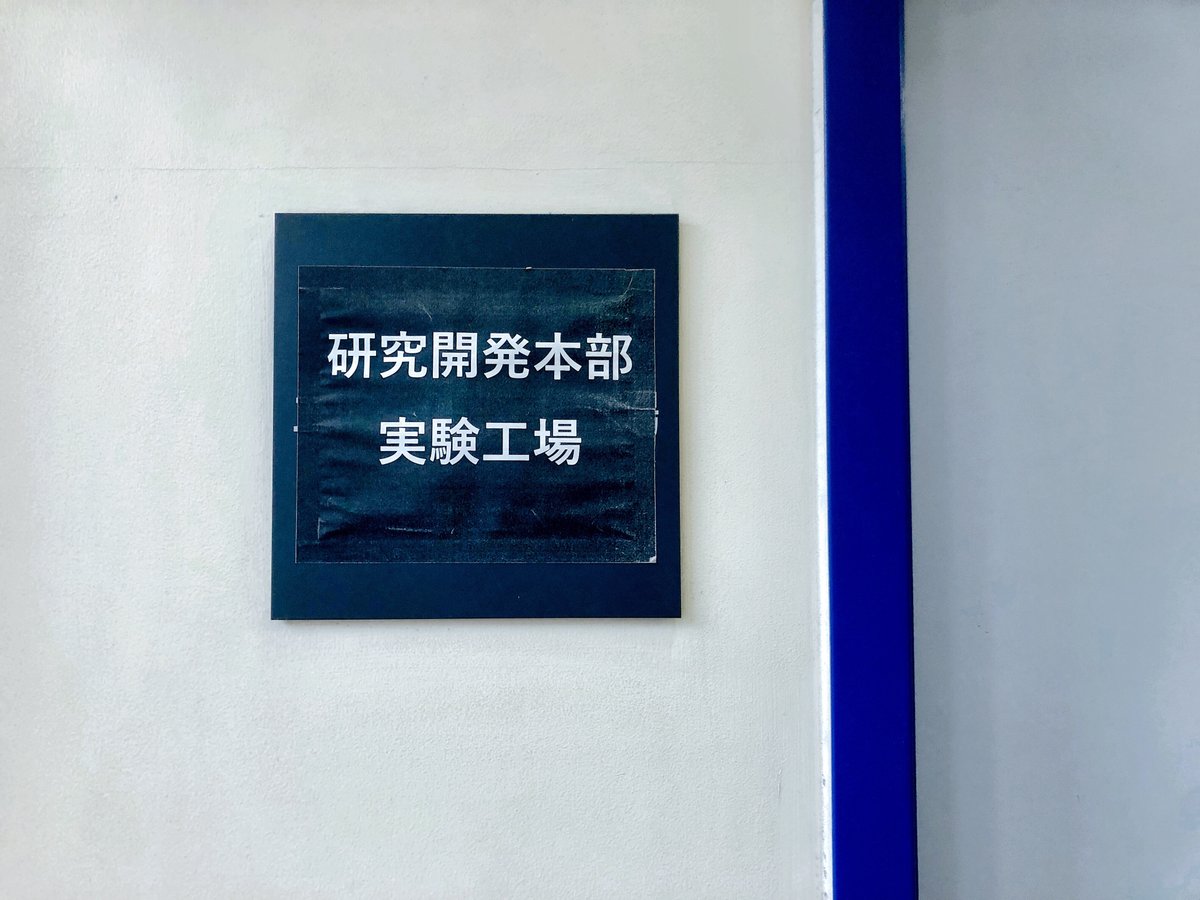
キョーラク大和研究所ってどんなところ?
片山 カタツムリレポーター飯島に代わって、今日は片山が取材させていただきます。よろしくお願いします!
はじめに、キョーラクさんの事業についてうかがわせてください。
青木さん キョーラク株式会社はプラスチック製品の製造販売を行っている会社です。創業は1917年京都で、もともとは不動産の開発会社だったのですが、戦後の1940年代からプラスチック業界に進出しました。
一番身近なところでいうと、マヨネーズ、ソース、油などを入れる食品容器の製造ですね。それから、化粧品や医療品の容器、空調ダクトのような自動車部品など、幅広い分野の製品を取り扱っています。
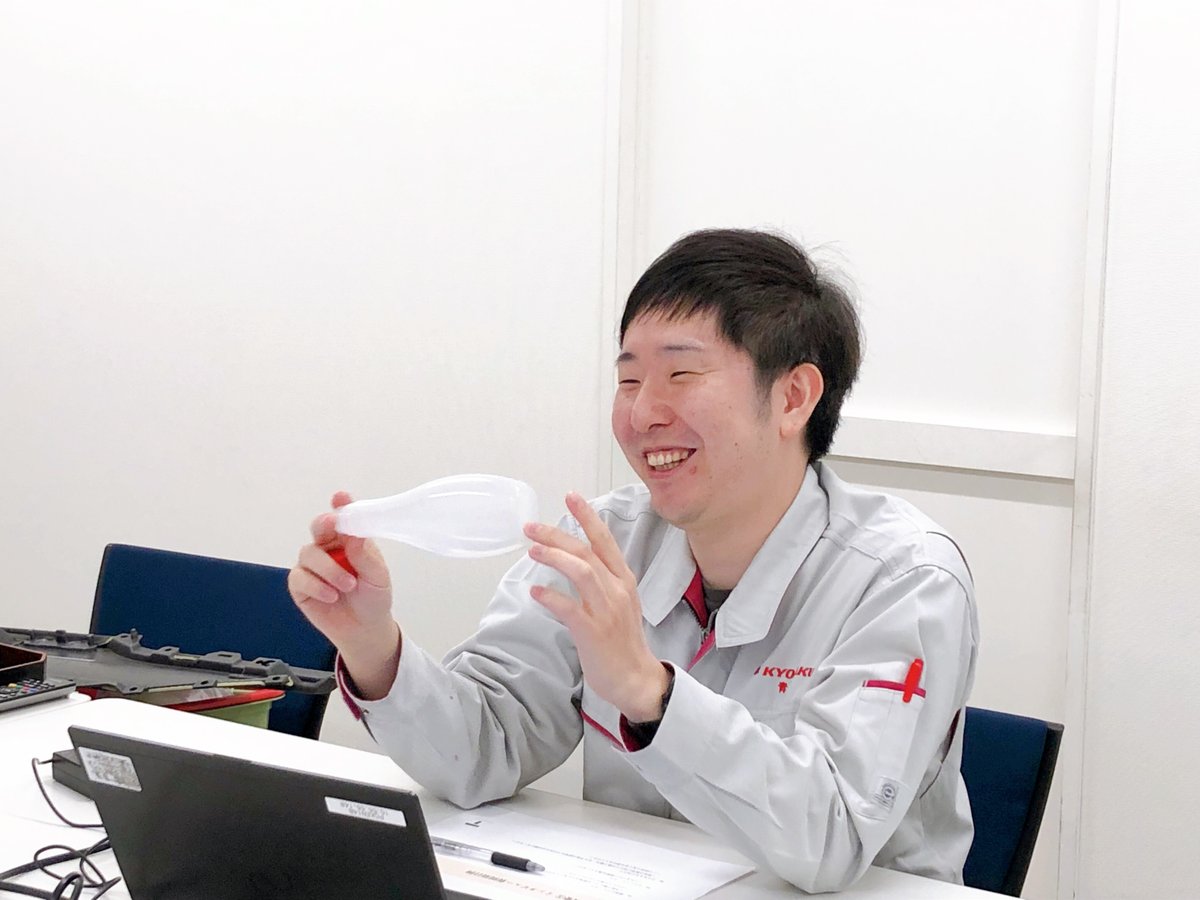
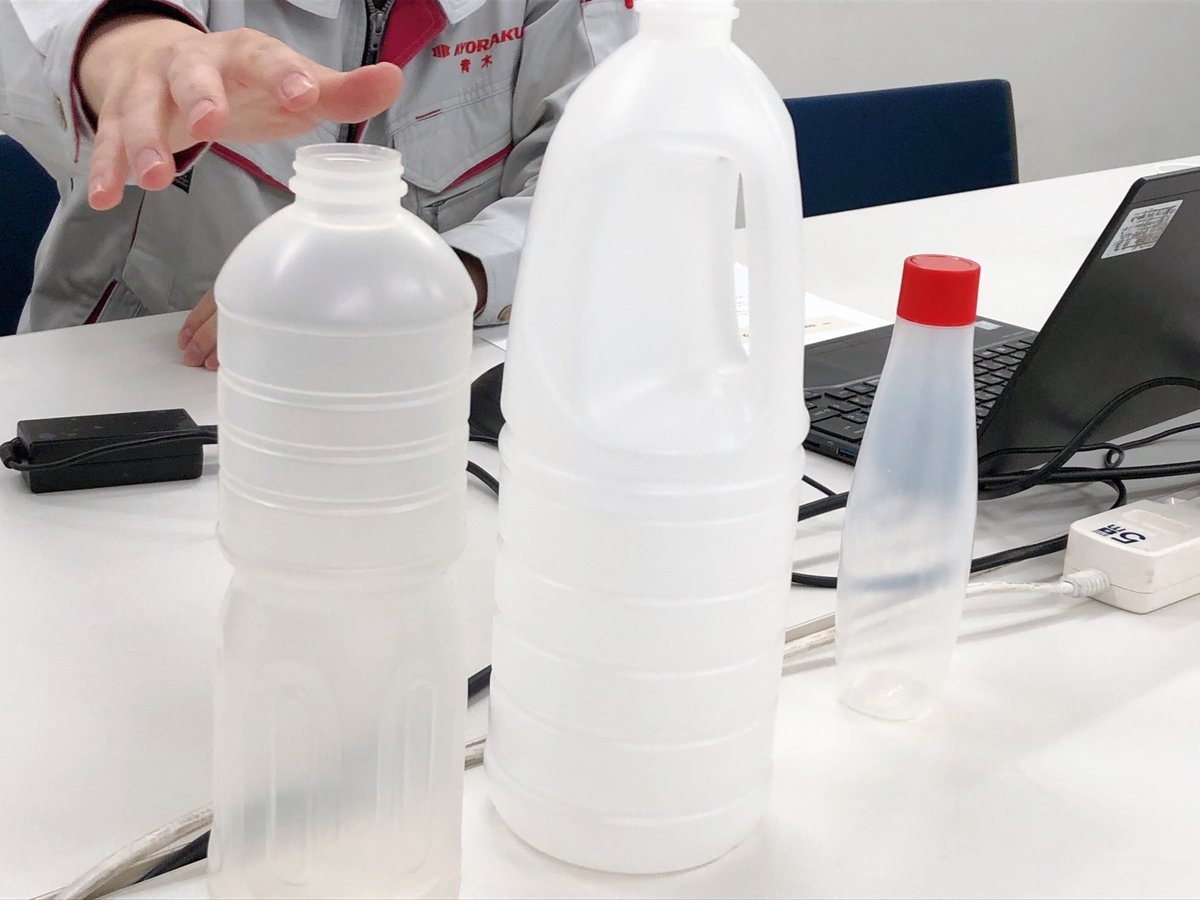
片山 今朝もマヨネーズを食べて、この容器使いました!
青木さん ありがとうございます(笑)大和研究所では、そういった容器類や自動車部品などの新製品・新技術開発に関する研究を行っています。近年は、お客様が要望する製品の製造にとどまらず、キョーラク発信の製品づくりに取り組んでいまして、潜在ニーズ調査から製品需要を検討して新製品を開発提案していくといった事業も進めています。
リサイクルに関する研究も、そういった社会ニーズへの取り組みのひとつです。資源循環はメーカーだけでは完結できない課題なので、リサイクラー(再資源化事業者)さんや自治体などとも協力して、大きな枠組みで取り組んでいく必要があると思い、COIプロジェクト発足時から参画させていただいています。
人にフォーカス!
大学での知識、経験が今のプラスチック研究に活きている
青木さん 私は大学時代に有機化学(炭素を中心とした有機化合物)を専攻して、機能性色素の合成について研究していました。機能性色素というのは着色以外の機能性を持つ色素のことで、プラスチックとはまったく違う分野の研究です。
そして、プラスチックの知識もなくキョーラクに入社しまして、食品容器の研究開発を担当しているのですが、材料、形状、設計、成形方法など、さまざまな検討要素が必要なのは共通するところなので、自分の得意を活かしながらなんとかやっています。
片山 大学で勉強したことが活かされているんですね。
青木さん 機能性色素とプラスチック、材料面では近しいものがありますし、研究や開発の仕方は同じなんです。試験計画を立てて実際に試験をして、その結果をレビューしてまた試験する。一連の流れは大学時代の研究の時から変わらないので、ものの考え方や経験が役立っていますね。
研究にフォーカス!
製品や内容物に合わせてプラスチック原料を使い分ける
片山 青木さんが取り組んでいる研究はどんなことですか?
青木さん 私は主に食品容器について研究しています。食品容器の役割として、中身の品質を守る、押し出しやすく使いやすい、落としても割れない、輸送中に破損しない、といったいろいろな性能が求められます。品質や性能を保つために、材料面や形状面、肉厚のような成形面などをそれぞれに工夫して、より良い容器をつくることがメインテーマです。
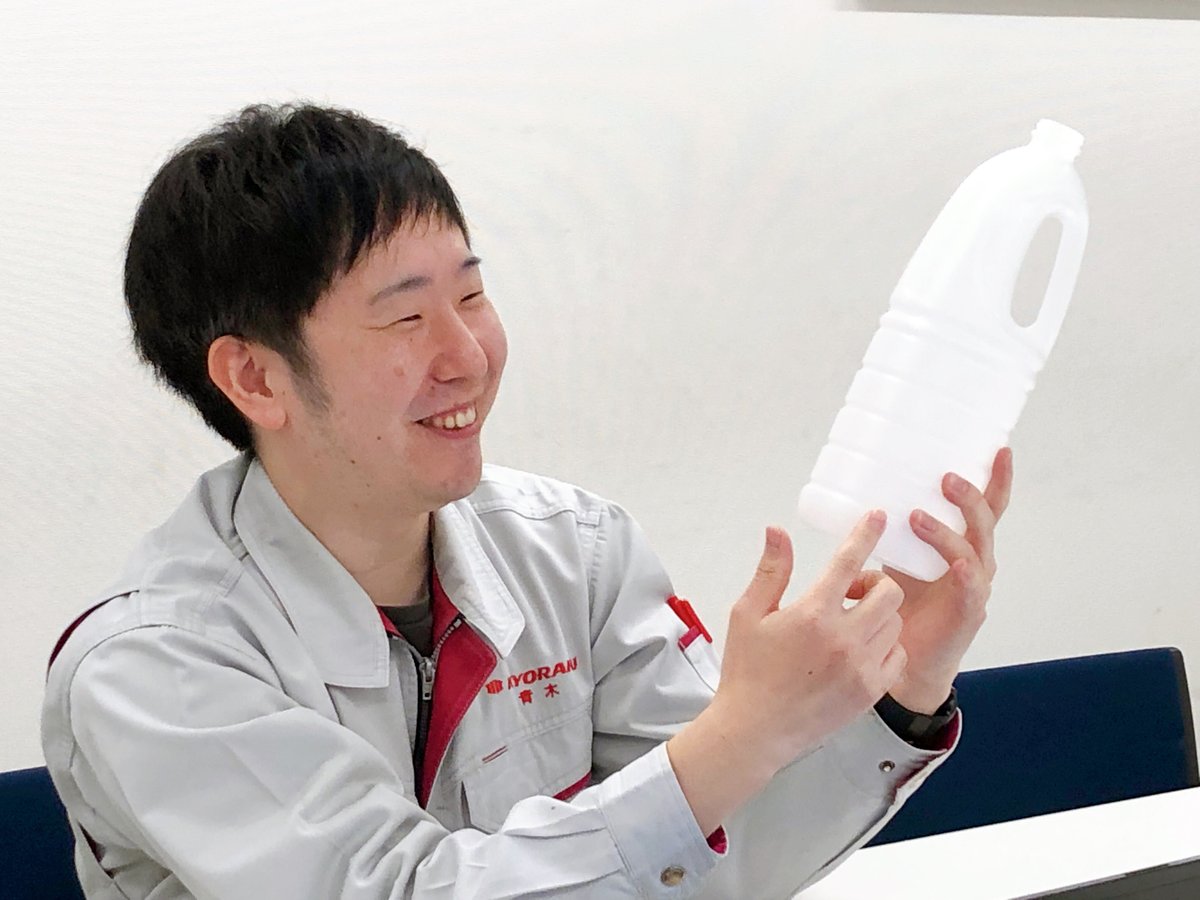
片山 材料面というと、製品をつくるための原料を選ぶところからですか?
青木さん そうです。プラスチック素材の種類は大きく分けるとPP、ローデン、ハイデンの3種類で、製品や内容物に合わせてそれらを使い分けます。
プラスチック素材の種類
① PP(Polypropylene):ポリプロピレン
② LDPE(Low Density Polyethylene):低密度ポリエチレン
③ HDPE(High Density Polyethylene):高密度ポリエチレン
青木さん それぞれの材料の特徴ですが、まず、LDPEの特徴は柔らかさです。柔らかさしなやかさが中身の絞り出しやすさにつながるので、マヨネーズやケチャップのような粘度(ねんど)の高い調味料を入れる容器に使います。
HDPEの特徴は不透明であることと強度の高さ。業務用の大きな容器などはそれ自体が重いし、落とした時の衝撃も強くなるので、破損しやすい材料では作れません。ですので、業務用の容器などはHDPEを使うことが多いです。
そして、PPの特徴は、耐熱性が高い、ある程度の強度がある、HDPEと違って透明性があること。ソースや焼肉のタレの容器などにPPが使われています。
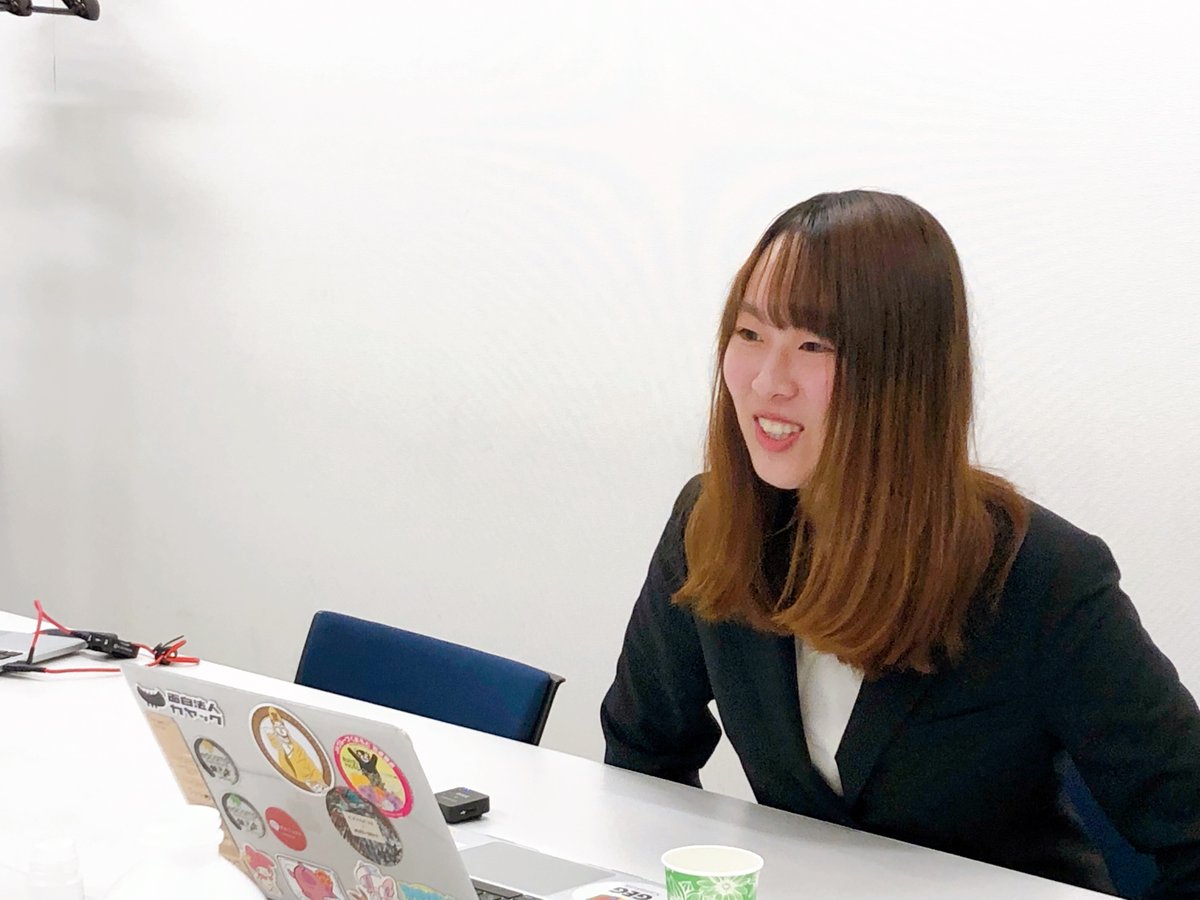
片山 なるほど!マヨネーズは中の色が見えた方が美味しそうだから、柔らかくて透明なLDPEが使われているんですね。
容器のプラスチックの厚みは部分的に変えられるのですか?
青木さん はい、変えられます。例えば食品容器はブロー成形という加工技術を使って成形するのですが、キャップをはめる口部はある程度の厚みを持たせる、押す部分は押し出しやすさを考えて薄くするなど、部分ごとに肉厚を調整します。
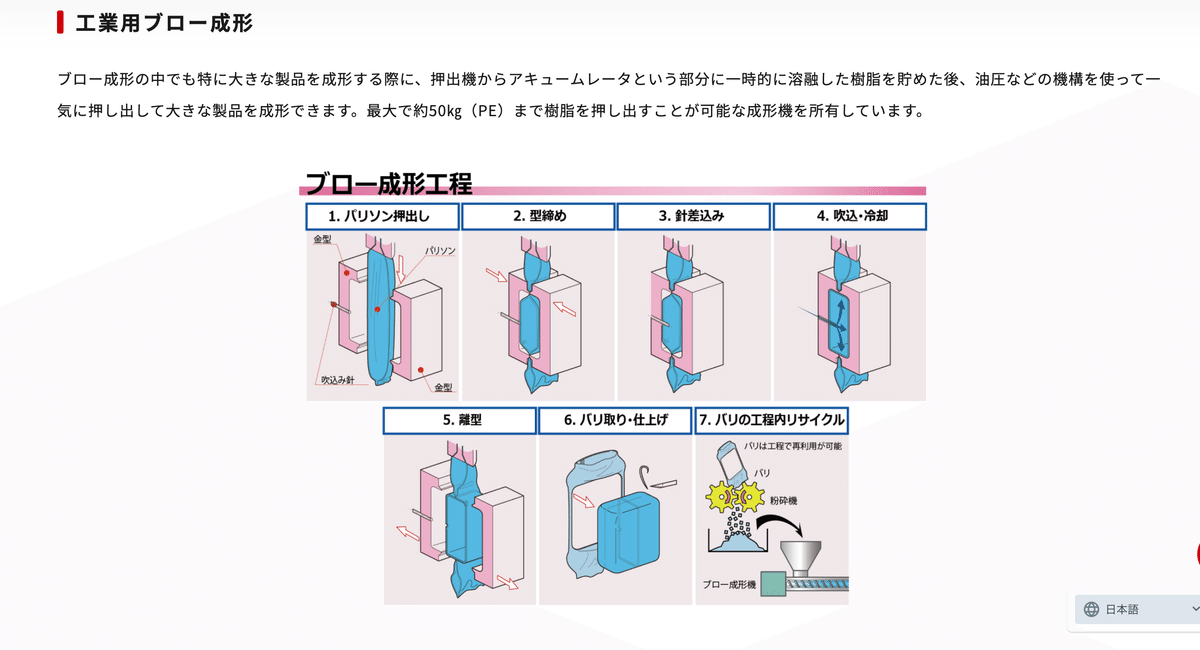
青木さん お客様のご要望を叶える製品を製造するために、キョーラクではブロー成形以外にもいろいろな成形の技術を持っています。私もこういった容器を何気なく使っていたんですけど、考えに考え抜かれた設計や製造方法になっているんだなと、入社してはじめて知りました。
片山 研究開発した食品容器が店頭に並ぶまでに、どのくらいの期間がかかるのですか?
青木さん 新しい技術を活用したものになると、2~3年はかかりますね。
片山 2~3年、そんなに!
青木さん 量産にあたっては、試作機でうまくできても量産機で不良品がたくさん出てはいけないので、安定した品質で生産できる体制や、効率のいい製造工程なども必要になります。そもそもプラスチックは長いひも状の高分子が集まってできていて、その高分子材料自体に特性やばらつきがあり、その上で成形のばらつきも出てくるので、扱いがなかなか難しい素材です。不良品が数%でも出たらよくないので、そこをできるだけ抑えて、いかに安定して生産できるようにするかにも苦心しています。
後編に続く
この記事が気に入ったらサポートをしてみませんか?