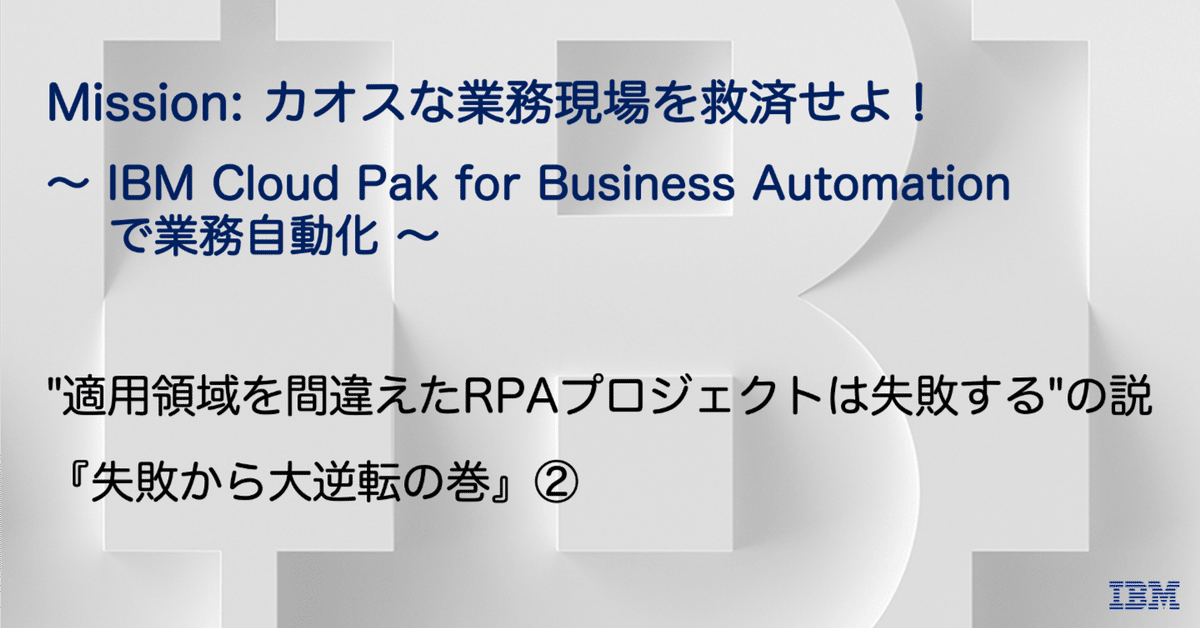
Mission: カオスな業務現場を救済せよ! 〜 IBM Cloud Pak for Business Automation で業務自動化 〜 "適用領域を間違えたRPAプロジェクトは失敗する"の説: 『失敗から大逆転の巻』②
前回(第一回目:https://note.com/jl25377/n/n1d900fc15ae2?magazine_key=m527981263098)は、なぜ業務現場がカオス化してしまうのか、その要因を抽象化した例で考えてみました。
RPAは、コピー&ペーストや入力作業といった手作業を自動化し、業務の効率化を促進します。しかし、適用領域を間違えてしまうと、思ったほどの効果がでない可能性があります。今回は、一つの失敗例をもとにそうなってしまった原因と、失敗からのリカバリー方法、更に改革を加速したお話をしたいと思います。
ある製造業のお客様において、半導体のパッケージ組み立てプロセスの後半処理として、マスター登録やMES/品目製造管理情報の更新など、煩雑な処理が課題となっていました。今後の多品種対応や増産対応のためには、これらの煩雑な処理を効率化し、生産性の向上や人員再配置を早期に実現することが喫緊の課題でした。
そこでRPAに注目し、煩雑で時間がかかっているところに適用するプロジェクトを実施されました。ところが、かなりの投資とワークロードをかけてプロジェクトを推進するも、なかなか思ったほどの効果が出ない。なぜだ?何が悪いんだ??RPAはこんなものなのか???・・・ という事で、我々にサポート依頼をいただきました。
我々はまず、現在の状況(As-Is)の分析を行いました。もともと、RPA適用のためお客様自身で分析を行われており、どの工程にどれくらい時間がかかっているかを可視化されていました。その結果が以下のグラフになります。
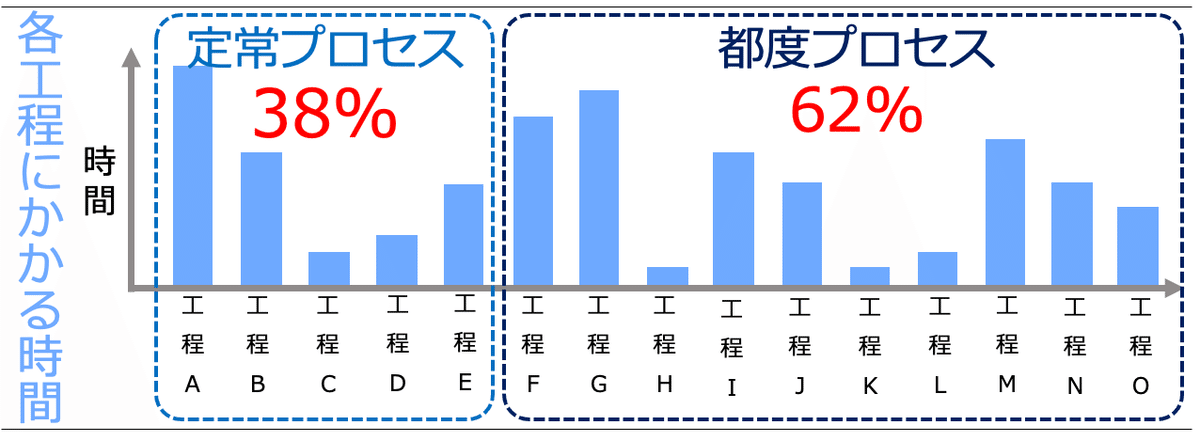
作業は大きく2種類のタイプに分類され、一つは毎回必ず実施する”定常プロセス”、もう一つは状況に合わせて必要な時だけ実施する”都度プロセス”、になります。業務現場では、やったりやらなかったりする”都度プロセス”の方が手間がかかり煩雑だ、という声が圧倒的に多く、実際の処理時間も、”定常プロセス”にかけている時間は全体の38%、”都度プロセス”には62%、という結果となっていました。そこで迷いなく”都度プロセス”にRPAを適用されたのですが、現場の感覚を重視したこの選択に大きな落とし穴が潜んでいたのです。
我々は、プロセス・モデリング・ツールを使って、更に深くAs-Isを掘り下げてみました。お客様自身の分析は、工程レベルでしたが、我々は更に各工程内の手作業レベルまでブレークダウンし、各作業の正味作業時間を炙り出しました。その結果が以下のグラフになります。
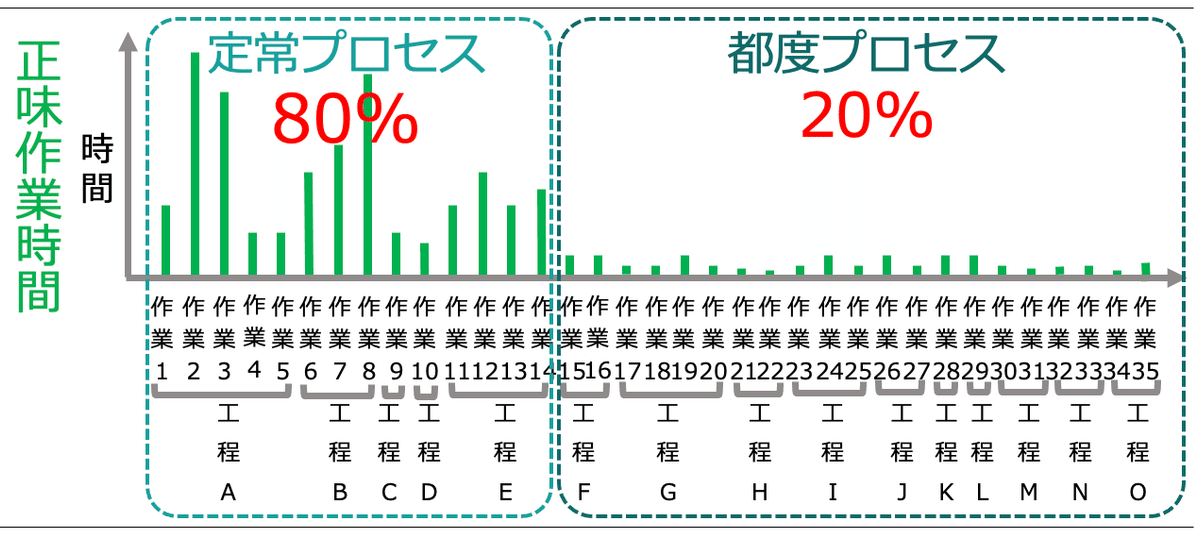
なんと、工程にかかる時間の割合は低かった”定常プロセス”に80%の手作業が集中しています。圧倒的に煩雑で時間がかかっている”都度プロセス”ではなく、毎回必ず実施する”定常プロセス”の方に手作業が偏っている、という事実が見えてきました。RPAは手作業を自動化し効率化するテクノロジーなので、適用により効果が見込めるのは”都度プロセス”ではなく”定常プロセス”の方だという事がわかります。どこで手作業がかかっているのか、ということを見誤ってしまったため、適用したものの思ったほどの効果がでないという落とし穴にはまり、残念な結果につながっていました。
そこで、”定常プロセス”にRPAを適用する方針に切り替え、手作業の自動化を進めることにしました。その結果、作業の省力化が実現でき、見違えるような効果を出すことができたのです。
これで、当初の目論見であったRPAによる手作業の効率化は大成功!めでたし、めでたし、一件落着!
んっ?ちょっと待て。確かに部分的には効率化できましたが、そもそも圧倒的に煩雑で時間がかかっているのは”都度プロセス”じゃなかったか??そこを改善しないと、本質である全体的な生産性向上にはならないのでは???・・・ 確かに、これでは大逆転とは言えません。
”都度プロセス”は、なぜ各工程で時間がかかっているのでしょうか?その原因を探るために、更に深く業務現場のヒアリングを進めました。
現場の声からは、他の部門や工程からのインプットを待っていたり、不備に伴う手戻りが発生したり、人が物事を考えることが多いため、結果的に時間がかかってしまい煩雑に感じる原因になっていることがわかってきました。これらはRPAで解決できる問題ではありません。
そこで、Business Process Management (BPM)を適用し、業務の見直しを行う事でできるだけ待ち時間や無駄を削減し、工程内/工程間の効率化をはかりました。BPMは、As-Isの業務プロセスの問題点(ボトルネック、待ち時間、手戻りによる無駄、など)を分析し、あるべき姿(To-Be)を描いて実装することでそれらの問題点を解決することができます。その結果として、エンド・ツー・エンドでの効率化を図ることができ、全体で50%以上の生産性の向上を実現できました。まさに、RPAプロジェクトを立て直しリカバリーで同点に追いつくだけでなく、期待以上の効果をあげて『失敗からの大逆転』につなげることができたのです。
大逆転のポイント
現場の感覚だけでなく、使いやすいプロセス・モデリング・ツールによる客観的な分析で、RPAの適用領域を間違いなく見定めることが重要
手作業だけの部分的な効率化だけでなく、BPMを組み合わせて待ち時間や無駄を削減することで、業務全体の生産性向上を実現
この事例には、まだまだ効率化を促進するポイントが残っています。それは、人が物事を考えている時間です。
次回(第三回目)、この未踏のエリアにメスを入れ、さらに業務自動化を推進し改革を実現するダメ押し策と、トータルで実現するプラットフォームをご紹介したいと思います。
Stay Tuned !
第一回目:https://note.com/jl25377/n/n1d900fc15ae2?magazine_key=m527981263098
この記事が気に入ったらサポートをしてみませんか?