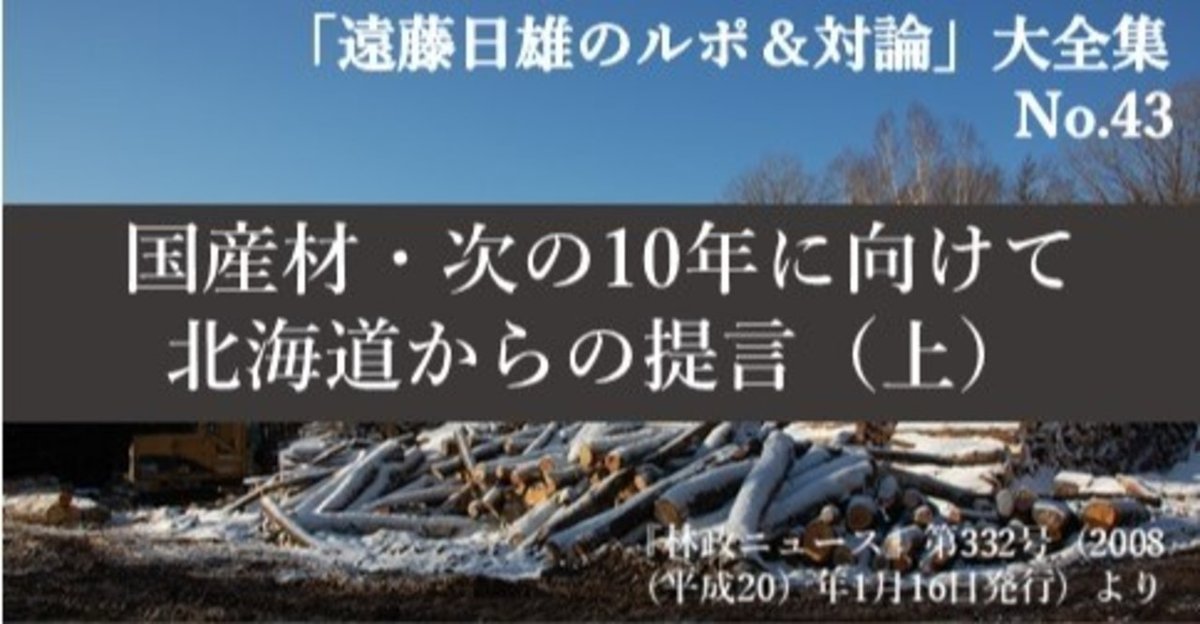
国産材・次の10年に向けて北海道からの提言(上)
数年前には「カラマツ亡国論」まで叫ばれた北海道の林業が息を吹き返している。外材の輸入減と合板・集成材への利用拡大でカラマツ等の需要が増加。しかし一方で、伐採跡地の造林が進まないなど、新たな問題が浮上している。道産材の需要拡大と森林の持続的管理をどう両立するか――これは日本林業全体が直面しているテーマと共通する。そこで、次の3氏に、今後10年のビジョンを語り合ってもらった。
秋元紀幸・株式会社サトウ代表取締役社長
山田壽夫・林野庁北海道森林管理局長
遠藤日雄・鹿児島大学農学部教授(司会進行・ルポ報告)
カラマツに過伐の不安、丸太価格は1万円で低迷
遠藤
この鼎談では、北海道の現状と課題にスポットをあてながら、今後10年程度を睨んだ日本林業の進むべき方途を考えていきたい。まず、昨年4月に九州森林管理局長から北海道森林管理局長に就任した山田局長(第314号参照)に、九州と対比した北海道林業の現状について解説してほしい。
山田
北海道と九州の人工林面積はほぼ同じだが、㏊当たりの蓄積量は全く違う。北海道の126㎥に対して、九州は283㎥と2倍以上の蓄積量がある。とくに、8齢級以上の人工林蓄積量を比較すると、九州のスギが2億974万㎥(㏊当たり421㎥)、ヒノキが5859万㎥(同313㎥)であるのに対し、北海道のカラマツは4663万㎥(同200㎥)、トドマツ・エゾマツは4291万㎥(同146㎥)という水準だ。
山田壽夫・林野庁北海道森林管理局長
ところが、全国の人工林の蓄積量当たり素材生産量(比率)をみると、北海道が1.360%で最も高い。九州トップの宮崎県でも1.193%、全国平均は0.586%だ。とくに最近は、道内のカラマツを伐りすぎているのではないか、植林が追いつかず資源が枯渇するのではないかという不安が出ている。
遠藤
道産材の伐採量が多いのは、それだけニーズがあることを現しているが、丸太(原木)価格には反映していないのか。
山田
九州のスギの価格がha当たり1万2000〜3000円で推移しているのに対し、北海道のカラマツは1万円弱、トドマツ・エゾマツも人工林材は1万円程度で取引されている。スギ丸太の価格は世界一安いと言われているが、北海道のカラマツ、エゾ・トドはそのスギよりも安い。今のような安い丸太価格では、素材生産業者は皆伐しないと採算がとれない。また、安い価格で売った森林所有者は、跡地造林ができない。一刻も早くトータルなコストダウンと製品の付加価値向上を図り、サステイナブルな資源循環へ転換する必要がある。
10年前に世界最先端の工場、常に世界を意識
遠藤
九州では、スギの国際競争力を高めるために、国産材製材工場が積極的な規模拡大に踏み出している。北海道ではどうか。
秋元
率直に言って、製材工場の設備投資は低調だ。後継者もいないし、外材も入ってくるから、将来に向けての投資意欲が希薄になっている。このため、製材・加工工程のコストが下がらず、丸太価格にしわ寄せがいっている。北海道は国有林や道有林のウエイトが高いので、製品価格が下がったら役所にお願いに行って丸太価格を下げてもらうということも行われてきた。だが、このままでは今後10年のビジョンは描けない。北海道の業界関係者は、早急に意識変革と体質転換を図らなければならない。
秋元紀幸・株式会社サトウ代表取締役社長
遠藤
そのモデルとなるのが「から松のサトウ」の工場だろう。まさに、世界レベルの工場と言っていい。
山田
これだけ生産性の高い工場を、今から10年も前に稼働させていたことに驚かされる。当然、その2〜3年前から、新工場の構想を練っていたのだろうが。
遠藤日雄教授
秋元
我々が恵まれていたのは、海外の先進的な工場を視察する機会が少なからずあったことだ。外国に何回も行くうちに、円高になれば外材は安く入ってくる、製材システムを海外と同じレベルにしないと競争にはならないという考え方を強く持つようなった。
山田
平成9年頃、フィンランドの製材工場を九州の関係者と一緒に見に行ったことがある。原木年間消費量100万㎥と最新鋭の無人化工場で、その生産性には圧倒された。当時、日本でそれと競争できる工場がつくれるか検討し、さすがに躊躇したのだが、「から松のサトウ」では同じ時期に新工場建設を決断されていたことになる。
秋元
我々は、まずアメリカ西海岸の工場を研究した。ウェアハウザー社の素材生産現場にも行き、これだけの物量で勝負をしかけられたらどうなるかと非常にショックを受けた。西海岸だけでなく、南部の製材工場も調べたが、どうもアメリカの機械メーカーは大ざっぱすぎて日本には馴染まないという結論になった。そこで、ヨーロッパの工場を研究し、フィンランドの製材ラインを輸入することに決めた。フィンランドの機械メーカーは、顧客の要望にあわせた改良にある程度応じてくれる。総投資額は12億円程度になった。
山田
それだけの投資が、現在のコスト競争力につながっている。その競争力がベースとなって、次の投資目標が出てくるのだろう。その際には、川上・川中・川下の各段階でコストシミュレーションを行い、世界レベルで競争できる北海道林業・木材産業全体の新しいモデルを描いておかなければならない。
秋元
確かに、今は国産材にはフォローの風が吹いている。しかし、これから世界経済がどのように変わるかわからない。また安い外材が大量に輸入されるようになって、国産材が使われなくなってしまうことを一番心配している。だから、今のうちに各段階でのコスト縮減を徹底的に進めていくことが重要だ。
国際レベルの効率生産を追求し続ける「から松のサトウ」
2004年8月、日刊木材新聞社が日本の製材工場ベスト社30を公表したことがある。ここで堂々第7位にランクされたのが(株)サトウ(北海道帯広市、通称「から松のサトウ」)だ。道産カラマツ約15万㎥/年を原料に、パレット、梱包用材、ラミナを製材している工場である。「から松のサトウ」が国産材製材のトップランナーに躍り出た背景には、ラジアータパイン梱包材との産地間競争に勝ち抜いたという輝かしい戦歴がある。ラジアータパインがレディメード(既製品)で日本市場に参入したのに対して、サトウは徹底したオーダーメード(受注品)のジャスト・イン・タイム納入方式でこれに応戦した。その製品種類たるや200種類に及ぶという。原料は末口径1㎝刻みの丸太で対応。しかもこれだけの商品を扱いながら、その日の夜6時には原価がわかるというコスト管理体制をつくり上げている。サトウがトップランナーを維持しているのには、まだ理由がある。それは時代の変化を読み取る目だ。市場を見据えながら商品構成の変化に対応し、10年単位で製材ラインを見直してきた。現在の工場に姿を変えたのは平成9年。北海道拓殖銀行などの金融破綻で、北海道経済界は嵐が通り過ぎるのを待つかのように投資には消極的だった。この時期に、スピード重視のフィンランド(HEINOLA社)製製材ラインを導入。ラミナで1日470㎥、小径木を合わせると1日550㎥の丸太を消費する。しかも、加工ラインそのものは3人のオペレーターで管理できる。徹底した効率化と省力化が、サトウの工場では達成されている。全自動のハイスピードラインが高い生産性を実現その先端的製材ラインも、導入して10年がたった。当然、秋元社長は、「次の10年」を見据えた「新たな一手」を考えている。
(『林政ニュース』第332号(2008(平成20)年1月16日発行)より)
この記事が気に入ったらサポートをしてみませんか?