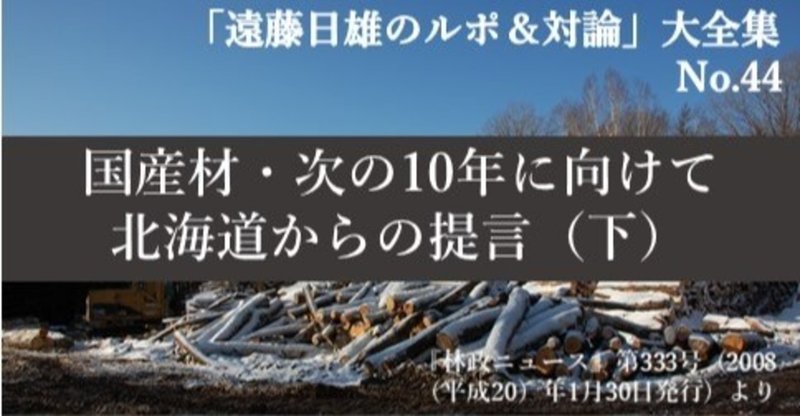
国産材・次の10年に向けて北海道からの提言(下)
国産材の国際競争力を高めるためには、川上から川下に至るトータルコストダウンが不可欠である。だが、国産材の供給には様々な関係者が関与しているだけに、総論的にコストダウンを叫んでいるだけで、現状を打開するのは難しい。地域の森林資源の特長と、市場の最新動向を分析した上で、現実的な戦略を構築する必要がある。何よりも求められるのは、現場からの発想だ。
秋元紀幸・株式会社サトウ代表取締役社長
山田壽夫・林野庁北海道森林管理局長
遠藤日雄・鹿児島大学農学部教授
中間拠点で原木を効率仕訳け、3人で年10万㎥
国産材原木の新しい供給モデルを求めて、秋元・山田・遠藤の3氏は、足寄町にある素材加工流通センターを訪れた。同センターは、秋元氏が理事長をつとめる協同組合フォレスト十勝が運営している。8・5haに及ぶ広大な貯木場だ。その中を、最新のホイールローダーが動き回って原木を運搬、自動選木機による効率的な仕訳け作業が行われている。
中間土場の活用策を話し合う(右から)秋元、山田、遠藤の3氏
遠藤
このセンターは、中間土場の役割を果たしているようだが。
秋元
個々の山林で伐採された原木を一旦ここに集積し、製材工場の用途に応じた仕訳けを行って、効率的な供給に努めている。また、製材用にならない小径材は、ここで円柱に加工して出荷している。つまり、原木の付加価値を高める中間拠点という位置づけだ。ちなみに、原木を仕訳ける際の径級区分は、1㎝刻みにしている。
山田
1㎝刻み! 通常、14以上の径級区分は2㎝刻みであり、日本農林規格(JAS)もそうなっている。1㎝刻みとなると、相当きめ細かな仕訳けになる。
秋元
以前、採算が厳しいときに、径15㎝や径17㎝で選木してみたことがある。そうしたら製材工場の採算性が全く違った。これから集成材用のラミナを効率よく挽くには、径級や長さ、曲がりの程度など原木の管理が厳しく問われるようになる。新しいニーズに応えられる原木仕訳けにしていかなければならない。
遠藤
きめ細かな仕訳けができるのは、高性能の自動選木機があるからか。
秋元
そうだ。ここの選木機のラインスピードは、毎分150mに達しており、約20種類に自動選別できる。オペレーター3人で年間10万㎥を処理している。
合板工場向けへ山元でカット、1人15㎥以上可能
次に3氏は、陸別町の伐採現場に移動した。約12haの町有林が風倒被害にあったため、部分皆伐による伐出事業が行われている(請負事業者は(有)菊地林業)。30〜35年生のカラマツ林から約2700㎥の原木を伐り出す計画。作業は、チェーンソーで伐倒→ブルドーザーで集材→ハーベスタで枝払い・玉切り→トラックで搬出という流れ。緩傾斜地という作業条件にも恵まれ、1日1人当たり15㎥という高い生産性をキープしている。
遠藤
独特の採材をしているようだが。
秋元
径24㎝以上の原木を1m90㎝にカットし、合板用材として約40㎥離れた丸玉産業(株)の工場に直送している。山元土場から工場に直接搬送することで、㎥当たりの物流コストは従来の3000円から2000円に下がった。
山田
合板用は一般製材に比べて、曲がりや欠点の許容範囲が広い。そういう山だと思ったら、最初から合板用の採材を徹底するというのは1つの考え方だ。これから素材生産のコストダウンを進めるためには、従来の採材方法などを柔軟に見直して、より付加価値の高い採材にしていく必要がある。例えば、全幹材(長材)のまま搬出し、フォレスト十勝のような中間土場でカッティングする方が効率的な場合もある。
秋元
今後は、加工技術の進歩にあわせて、合板工場と一般製材との棲み分けもできて、山元の採材も変わっていくことになるだろう。
遠藤
作業システムの改善にも取り組む必要がある。
山田
1日15㎥は立派だが、ここの現場ならば、それを上回る生産性を目指せるのではないか。緩傾斜地の多い道内では、ブルドーザー集材が広く普及しているが、このブルドーザー部分が全体の効率を制約しているようだ。もっと合理的な集材方法を模索するため、今、国有林と民有林が連携して効率的な集材手法をテストしている。
秋元
現状以上の出材量にしようとすれば、山元土場が狭すぎる。したがって、中間土場をどう確保し、工場への加工・流通システムをいかに構築するかなど、川上・川中・川下を通じた総合的なコストダウンの手法も必要になる。
山元土場でカッティングされ、積み込まれた丸太。合板工場に直送される。
戦略製品はカラマツラミナ、乾燥技術の向上不可欠
現場から(株)サトウの本社に戻った3氏は、北海道産材を中心とした国産材の国際競争力向上策について論じ始めた。
遠藤
世界の大手木材企業は、資源基盤を天然林から人工林にシフトして、品質・性能の高いエンジニアード・ウッドの安定供給により市場シェアを高めようとしている。こうした動きをどうみるか。
秋元
北海道の林業・木材産業も、エゾマツ、トドマツといった天然林への依存から、人工林を活用する時代に移っている。当面、道内の人工林ではカラマツの有効利用が課題だ。カラマツは捩れやすいなどの欠点があるため、主に梱包材やパレットなどに加工してきたが、建築材、とくに集成材用ラミナに加工することを戦略的なターゲットにするべきだろう。
山田
道内におけるカラマツの用途別製材割合(17年度)をみると、梱包材やパレット用で7割を占めており、ラミナ向けは1割強しかない。ちなみに、最近の相場はどの程度になっているのか。
秋元
工場出荷時の㎥当たり価格は、梱包材が2万7000〜8000円、パレットは、それよりも1000〜2000円高。ラミナは3万円〜3万2000円というところだ。
山田
再生産可能な立木代金を確保するためにも、できるだけ付加価値の高い最終製品を供給していかなければならない。やはり、ラミナの供給量を増やすことが目標になる。その際、品質・性能の確かな住宅部材が求められているという市場ニーズをきちんと踏まえることがポイントになる。
秋元
当社としても、ラミナ専用乾燥工場を今年2月に新設することにしている。新工場が竣工すると、当社全体の月間原木消費量は自動的に上がり、生産コストをさらに引き下げることができる。
そこで重要になるのは、乾燥技術の向上だ。カラマツは、旋回木理等があって乾燥が難しい。また、一口に乾燥といっても、初期含水率の高低によってやり方もコストも全く異なる。木の特性が複雑かつ微妙に関係してくるので、当社なりの乾燥マニュアルを作成し、社員の意識を共有化したい。乾燥が利益を左右することになる。
競争力のある国産材製品を輸出する時代に
遠藤
国内の住宅市場は100万戸規模に縮小すると予測される一方で、中国やインドの台頭が著しい。世界の木材貿易がダイナミックに変貌する中、国産材のビジョンをどう描くか。
山田
国内市場とともに、海外への輸出にチャレンジしていくことが重要だ。九州の場合、輸送面だけをみれば、東京に持って行くより上海に持って行く方が近くて安い。中国、インド、中東といった市場で、欧州材や米材と戦えるようなコスト意識を国産材業界全体で持つことだ。そうすれば、国内市場でも生き抜いていける。
秋元
北海道は今後、トドマツの人工林も本格利用の段階に入る。計画的に人工林を利用できることは、世界的にも強味になる。かつては、道産のインチ材をイギリスに輸出していた。次の10年で、競争力があり、完成度の高い国産材製品を輸出できる力をつけたい。
(『林政ニュース』第333号(2008(平成20)年1月30日発行)より)
この記事が気に入ったらサポートをしてみませんか?