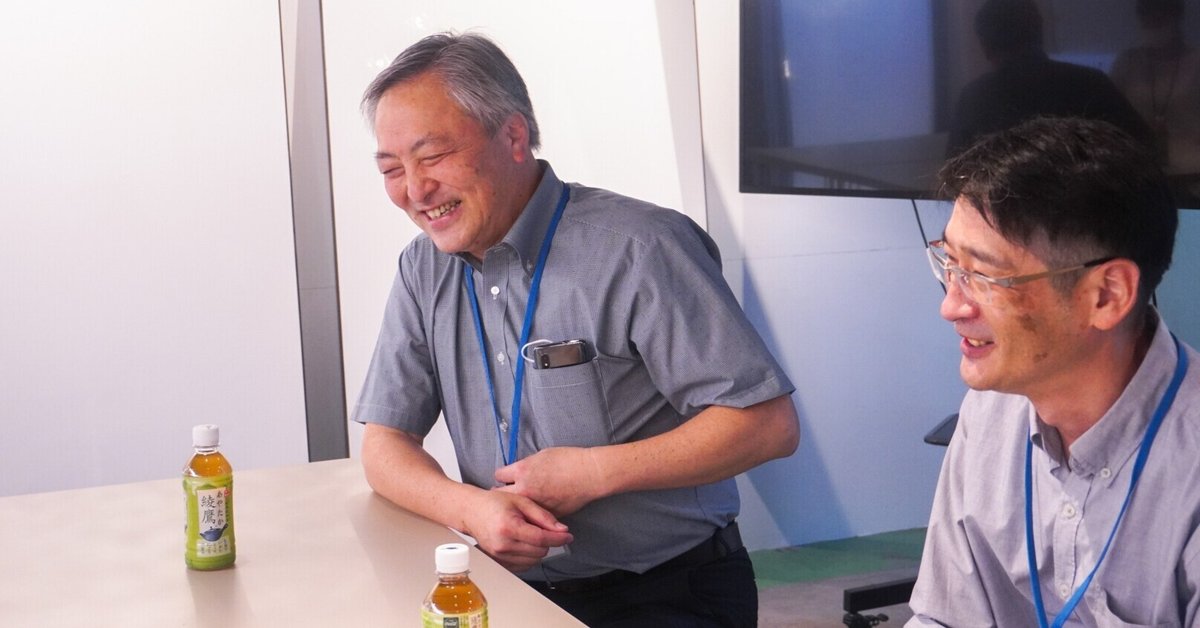
ideaboard® 開発ストーリー連載 #15_外部パートナー編 | トキハ産業株式会社
この連載では、中西金属工業株式会社(以下、NKC)が、2019年に発売した新しいホワイトボード『ideaboard®(アイデアボード®)』の開発に関わったプロジェクトメンバーから広く話を聞き、ideaboardが世に生み出されるまでのストーリーを記録します。
第1〜8回は開発者であるNKC 社長付 戦略デザイン事業開発室 KAIMENの長﨑さんに、第9回以降は外部パートナーのみなさまにインタビューしています。
今回はトキハ産業株式会社 垣尾 幸広さん、大下 裕司さんに、お話を伺いました。
(左) 垣尾 幸広 |Yukihiro KAKIO
トキハ産業株式会社, 開発営業部, コミュニケーター
(右) 大下 裕司 |Hiroshi OOSHITA
トキハ産業株式会社, 製造本部, 購買・外注管理
1. 新しい顧客と製品を共創する!ODMでの生産スタイルへ
ーまずはお二人の普段のお仕事やプロジェクトでの役割について教えてください。
垣尾:もともとトキハ産業は大手メーカーの製造のみを請け負うOEM生産(Original Equipment Manufacturing)が多かったんです。小売部門などはあるものの、ほぼ製造部で持ってるような感じでした。でもちょうどNKCさんとお会いする2018年頃から、OEMだけでなく、設計も含めて商品を立ち上げていくODM生産(Original Design Manufacturing)もやっていこうという流れがあり、ideaboardもそのひとつになりました。私は営業として、そういった新製品やお得意先の新規開拓を担当しています。
大下:僕はこのプロジェクトが始まった頃、和田山工場の副工場長からいったん営業部に異動という話が出ていた時期でした。新しいお得意先の新規開拓をちょうどやり出した頃ですね。工場サイドとしてウレタン製品の説明や、製造についてサポートするような役割でした。
その頃はホームページからいろんな問い合わせがあったりして、ideaboardに関しても、営業部を通して垣尾と僕がお付き合いしていくということだったと思います。
ーはじめて会ったときの、聞いたときの印象は?
垣尾:まず大きさが3尺×6尺(約900mm×1800mm)という大きいサイズで、すでに軽量化の話もあった。ちゃんと強度があって、その薄さ・重さでその大きさ。そんなことが実際できるのかなというところから始まったと思います。
大下:確か重量が5-6キロ、サイズは3尺×6尺、しかも厚みが10-12mmとか。厚みに関しては15mmまでいくと分厚いという話もされていたと思います 。うちは普段、商材としては天板がメインなので、天板だと厚みは20-25mmくらいが普通。軽くするならメラミンの下に発泡材なり、紙のハニカムポアなりを挟んで強度を出しつつ軽くするというのが常識なんです。それが10mmとかの薄さで、5-6Kg以下、しかも大きいサイズとなると、今までの常識が全部すっ飛ばされる。どれかをクリアすればどれかが引っかかってしまうような状態でした。これはまぁー…どうしようかなあと(笑)。
ー複雑に影響し合う要件を前に、どのように取り組まれたのでしょうか?
大下:実はたまたま別のプロジェクトの関係で、発泡材屋さんとの付き合いがあり、ideaboardについても一回考えてみようってなったんです。
あのタイミングじゃなかったらできていなかったかもしれない。NKCさんがもうちょっと前に来られてたら、私たち側にまだ知識がなかったし、例えば発泡材に直接表面剤を貼るなんてことも案にあがってきていないと思いますね。やっぱり天板屋なので、表面の仕上がりや強度を意識すると、強度が低いとか割れちゃうとかそうゆう理由で、試す前にやめちゃってると思います。
垣尾:確かにタイミングが良かった。接着剤も、ちょうど他のプロジェクトで検討をしていたから、練り合わせがちゃんとできる特殊な接着剤が使えるようなこともありました。たまたま材料・素材メーカーとの出会いがすごくうまく重なり、これならいけるかもというところまでたどり着いたって感じですね。
大下:接着剤も本来うちでは使わない剤なんです。酢酸ビニル系という木質と樹脂系をくっつけるような樹脂は普段から使っていますが、今回のように樹脂と樹脂をくっつけるものは普段使っていない。たまたま他社さんで開発をしていたので、ちょうど使えたということもありました。
2. 強度、軽さ、精度のバランスを実現する発泡材の追求
ー様々な課題があったと思いますが、プロジェクトを通して最も苦労された点は何ですか?
大下:発泡材の精度を高めることについてが一番苦労したと思います。
最初は発泡率20倍くらいから始めて、少しでも軽い方がいいということで発泡率を少しずつ落としていきました。普通よくある発泡材だと発泡率は大体50倍くらい。でもそれだとどうしても、たわんでしまうし強度も落ちるので、20倍くらいから試していったんです。
強度と、軽さ、誤差の精度のバランスがすごく難しくて、ここが一番苦労したんですよね、ほんとに。発泡材屋さんから今にも電話がかかってきて「できません」と言われるんじゃないかって、僕は毎日ドキドキしていました。本来1-2mm違っていても全く問題ない業界に対して、せめて誤差0.5mm以内に抑えてくださいという要求を出しているわけなので。
垣尾:発泡材って本来、建材の一部として壁の中に充填するとかそういう取り扱いで、こんな風に表面に影響するような天面に使うという想定ではないからね。
ー発泡材屋さんとの間では、具体的にはどのような検討がありましたか?
大下:発泡材製造は東北の会社に製造パートナーとして協力を得ました。量産の前に工場に一度説明に行かせてもらったときにいろいろ見せてもらって、そこの社長さんがすごく意欲的というか、前向きだったんですよね。
発泡材って例えば数センチ切り出すにも、機械にセットして大体でカットしてOKみたいな業界なんですよ。でも今回は15mmでカットしてくださいってお願いしたとき、わざわざ社長がノギスを持ってきて測って対応してくれた。ノギスなんて普段使うような業界じゃないんです。その姿を見たときに、この社長ならきっとやってくれるだろうと思いました。
でもやっぱり実際には難しくて。試作段階ではうまくいったものが量産のときにうまくいかなかったんです。厚みの均一性や平面性が悪かった。その原因を調べてほしいとお願いしたときには、確か1週間以上何の返答もありませんでした。
その間に社内では、そこだけでなく他の発泡材を探した方がいいなどの意見もあり、正直厳しい状況でしたね。僕は製造パートナーの社長と直接話をして、その社長だったら任せたいと信頼してる部分があったので待ちたいと。とはいえ内心は本当に、断られたらどうしようっていうことが一番気が気でなかったです。僕たちが求めているトキハ基準では「やっぱり難しい、できません」と言われると、また一から探さないといけないし、恐らくそこまでの精度出せる会社はなかったと思うんです。
ー量産時に発生した課題について、どのように解決したんでしょうか?
大下:試作段階では材料を使うのも少量なので、工場にある在庫から必要分を切り出して使っていたんですね。それが量産で100枚、200枚を生産するとなった時には、とても大きなブロックから切り出すことになる。そうなるとどうしても中がきっちり乾燥していないんです。
ブロックは熱線でカットするんですが、中に少しでも水分が残っていると表面がちょっと溶けたりそこだけ厚みが変わってしまうんですね。
そこまで追求してもらって、結果、ideaboard向けの発泡材だけは特別に寝かせて乾燥させたものをカットしてもらうようにしました。本来ならそこまでしないんだろうけど、逆にそこまでするとちゃんとした精度でカットできることがわかった。そこまで突き詰めてやってくれたんですね。
製造パートナーの社長も同じ製造業なので、曖昧な答えはできないと思ったから時間がかかったんだと思います。きっちりした答えをつくるためにいろいろ試行錯誤して、これならいけるだろうという段階まで追求してくれた。その時は本当にほっとしたし、社長がそこまでやってくれたというのが嬉しかったです。
3. 今後は新しい業種とのコラボレーションに意欲
ーNKCの長﨑さんはインタビューにおいて、トキハさんが複雑な課題に対し、常に前向きに取り組まれていたおかげでプロジェクトが前に進んでいったとおっしゃっていました。
大下:僕は工場に30年以上いたんですが、昔の上司から、お客さんと話をするときには、『「できない」と言わず「こうしたらできます」と言え』と教わりました。
「できない」というのはもちろん事実ですが、製造側の人間としてプライドを持てということだと思います。半分は無理とわかっていても、こうしたらできるかもというアイデアを絞り出さないと話が終わってしまう。どうにか前に転がすことは昔から言われていました。
垣尾:最後まで試行錯誤して、いろいろやって断念する場合と、最初からできないと言うのとは全く違う。できることはないかということを常に追求してもらうというのは営業の立場からしても、製造側にお願いするところですね。断ることは簡単なんですが、新しいお客さんを取り込むということも大変なのでやれるところまでやってほしいという思いです。
今私たちは新しいこと、新しい分野にチャレンジしていくという方針になっているので、製造側にもそれを理解して固定概念に囚われず、どんどん新しいことを考えてもらっています。いい感じで動いているのかなと思います。
ー今後の取り組みや展望があれば教えてください。
大下:例えば今回ideaboardをトキハオリジナルで作っていたとしても、こんな風に世に出ていないと思うんです。実際、これまで簡易テーブルやオフィス家具を作ってきてはいるものの、これがウレタンで作られたものだということを知っている人って少ないですよね。結局世に出てない、知られてないんです。
軽くて強いものはこれから需要があると思うし、今回のように外部とコラボすることで、また次につながっていけばおもしろいですね。
垣尾:KAIMENの方達ってとても破天荒で、おもしろいアイデアを持っているなあといつも驚かされます。そんな刺激を受けながら私たちができることを一緒にやらせてもらえたら、うちの会社にとってもプラスになるのかなと思います。
(取材・文・撮影 / (株)NINI 西濱 萌根、行岡 恭子 )
▼Click below to see the English version / 英字版はこちら
この記事が気に入ったらサポートをしてみませんか?