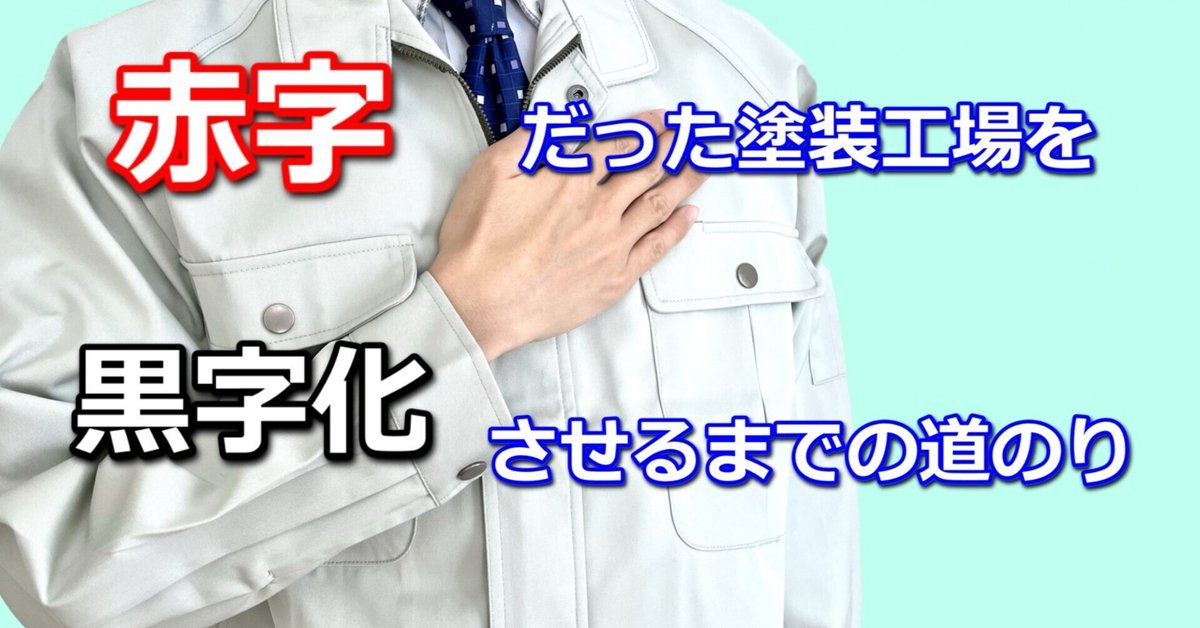
赤字だった塗装工場を黒字化させるまでの道のり②
対策のはじまり
当時トラブっている製品が約50部品ほどありましたが
話し合いの末、一番問題のある部品を10部品を見る事になりました。
その部品は、良品率が極端に悪い。
検査データーを見ると良品が3割位しか取れない、
しかも手直しをしての出荷しているレベルのものでした。
まあ何もしないと1個も良品が取れない状態でした。
数字だけを見ても力が抜けるような状態でした。
最初はやっぱり三直三現
現場で見たのは、驚くべき光景
なんと、製品のバリ取りラインが誕生していたのです。
(昭和初期の仕事かよ)
と 突っ込み満載
20人位の従業員がニッパ片手にバリ取り作業をしている。
現場の管理者がバリ取りのやり方を指導している。
(おいおい)
やる事が違うだろう
生産工程を見て
対象の製品の生産工程を見てまず判ったのは
もう既に手のつけられない状態だった
その製品は、携帯電話で使用してたコネクター部品でした。
生産開始から2ヶ月程度しか経っていなかったが、
金型が既にポロポロだで、少なくとも数年使い込んでいるような状態だった。
関係者に言われたのが、型メーカーと修正の仕方について話し合って欲しいとの事だったが、構造的にも欠陥があったため
修正は不可となった。
ミッションは新型
そんな事で、自分のミッションとして、新型からのスタートとなった。構造的な欠陥を修正して、新たな型作りに入った。
新型は2ヶ月ほどかけて順番に仕上がっていった。
当初、例の欠陥だらけの型メーカーを使って欲しいとの要望があったが
5人規模の小規模な型メーカーで
そんなメーカーに、数十型を発注していた。
失敗するのも当たり前との事で、
自分は別のメーカーを指定した。
出来上がってきたものは、予定通りのもので、
その型で作った商品によって、バリ取りラインなるものが消滅
100人近くいた派遣社員を解雇する事に繋がった
良品率は上がり、関係者は喜んでくれたが、
後に気がついたが、機械とのマッチングに問題があった事を
当時はマッチングが出来ている前提で進めていたため気がつかなかった。
只、誰もそれについては、指摘は無かった、気がついた人はいなかったのかもしれない。
やっぱりこうなったか
3ヶ月ほどして、自分の係わっていた製品はなんとか、安定生産に入っていた。
当然かも知れないが、結局出来ないと断った製品の面倒を見る事になっていた。
まだ生産途中でトラブルが継続しているものや、これから量産になるものなんかもあったがそれぞれについて、進捗管理をしていった。
この時の問題は共通していたが、塗装のレベルが安定しない事だった。
これは実は解決に繋がるまで数年を要したが、この時点では原因が判明していなかった事で、生産条件での対応のみであった。
ここからかなりダラダラとした対策が続いていった。
気がつくと、既に半年が過ぎていた。
工場プロジェクト
工場の改善に係わりだして、半年が過ぎた頃、工場の改善プロジェクトなるものが誕生していた。
工場製品の改善に係わっていたとの事で、自分自身もいつのまにか、改善プロジェクトのメンバーとなっていた。
そこで提案したのが、組織の再合成でした。
当時工場は、商社機能の1つの部署でした。
自分は技術担当ではありましたが、スムーズな組織体では無い事から
子会社化を提案しました。
赤字会社を子会社にするのは、セオリーに反するが
その方が工場に取って最善と思ったからでした。
その後提案が承認され、まさかその組織の一員になるとは、この時は思いませんでした。
この記事が気に入ったらサポートをしてみませんか?