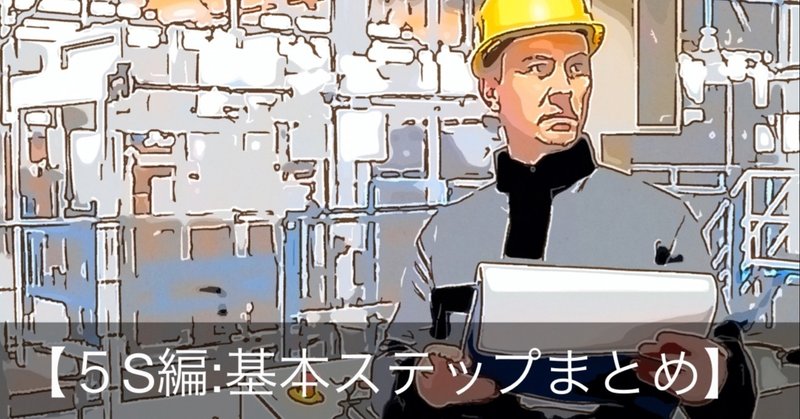
【5S編:基本ステップまとめ】
これまで記載してきた上記マガジンで投稿し5Sの基本ステップのまとめです。
手っ取り早くポイントを確認したい方は、これだけ読んでもらえればと思います。細かく読む気力がある方はマガジン内の投稿をぜひ。対話型にしているので比較的読みやすいとは思います。
下記では、対話の中のポイントとなるコメントを抜粋しています。
STEP0;心構えと理解。真の5Sとは
まず、「5Sとはなにか」をきちんと理解することが重要です。
・・・・・・
-5Sは絶対にキャンペーンでやってはいけない。
-5Sをするっていうのは、その現場の仕事の質そのもの改善。
-とどのつまり、利益に影響する活動。
-スーパーや食品工場に行ったとしてそこの5Sできていなかったらどう思うか。
-工場に来るお客さんも同じ目で見るだろうし、上司や工場長も同じよう
にみて、仕事の質を判断する。
・・・・・
5Sとは一過性のものではなく、モノづくり現場の仕事の基盤となる永続的な活動なのです。
まず、ここを抑えてほしいです。
STEP1;整理
整理は何を残すか、捨てることをどう決めるかがポイントです。これは次の整頓に向け重要な最初のステップです。
・・・・・
-整理は“不要なものを捨てて数を絞る”こと。整列ではない。捨てること
が重要。
-始め方
・A,何から捨てていくか決める。
いらないもの=使っていないもの
・B,捨てるものの基準を決める。
-いつか使う・・もの=使わないもの。
-整理には曖昧さが大敵。機械的に捨てていくルールを作る。
-優先順位を決めて捨てる。
(何を捨てないか?そのものの価値は?自分が使うか?)
・C,社内の廃棄ルールの事前確認。
(固定資産になっているものを捨てる際は要注意。経理に活動を事前に
伝えておくこと。)
-現場での活用
・現場のメンバーに5Sの真の目的を説明
・ポストイットを使っていないものに端から貼っていく。
・使っているもの(青)、使っていないもの(赤)、使うかもしれない
もの(黄)でポストイットの色を分けて区別。
-捨てるか迷った時の判断
もし必要とわかった時にそれを注文・制作して、間に合うものなら捨てる
べき。
・・・・・・
これを通して、残ったのものは必要と判断して、次の整頓に進みます。
STEP2;整頓
整頓は、見える化が重要になってきます。
・・・・・・・
-整頓は、“必要なものを使いやすい場所に置いておくこと”と定義。
-実際の仕事の質を上げるのに、重要なのが検索性だ。使いやすい場所に置
いて、かつ探し易くするのが基本。
-肝となるのは3つの「定」。
A:置き場所の“定”める(定置)
使用頻度で場所を決める。
B:置き方を“定”める(定品)
常に同じものがあること
(そのものの形をくりぬいておいておく方法がある。)
C:表示方法を“定”める(定量)
発注点を決めておく。
*30%程度の置き場の余裕をもって整頓をするといい
-実際の進め方
①置き場自体のマップとリストを作成して、
②その置き場ごとに対象物のリストを作成。
③各職場メンバーに対象物に3定を実施
-整理と整頓は相性がよく、整頓をすることで整理の不十分さが見えてくる。
-発注点管理による整理整頓の習慣化
発注点というのは、発注しなければいけない在庫量の点。つまり最少の管理点。でも、整理の概念を取り入れると、”在庫をどれだけに抑えるか”ということも考えないといけない。つまり、最多点も表示する。
・・・・・・・
整頓は、見える化とセットです。何がどこにあるか、どれだけあるかを発注点管理と共に進めます。
STEP3;清掃
清掃は、きれいにすることに意味はもちろんありますが、異常の見える化、改善のネタにもなります。
・・・・・・
- broken window theoryについて
軽微な犯罪も徹底的に取り締まることで、凶悪犯罪を含めた犯罪を抑止できるとする環境犯罪学上の理論。アメリカの犯罪学者ジョージ・ケリングが考案した。「建物の窓が壊れているのを放置すると、誰も注意を払っていないという象徴になり、やがて他の窓もまもなく全て壊される」との考え方からこの名がある。
*小さいことでも一度ほころび始めると全体に波及するということ。
-清掃には、整理・整頓ができているかの点検する役割もある。
-そもそも清掃すると周りを気持ちよくすることができる。
-清掃ポイント
A;清掃方法を決める。どんな道具で、どのように清掃するか。きれい
である状態を一度作り出し、それを掲示しておく。少ない労力で、
一番きれいになる方法を決める。
B;清掃道具を準備する。全員分の掃除道具を準備する。
(シフト制の場合、最も人数の多いシフトに合わせる)
C;清掃を全員で実施する。
D;その上で、ルール表とチェック表を作成する。
*道具購入において変にお金をケチらないこと。
-実際の清掃;
①整頓の時に作ったマップに清掃ポイントも追加して見える化。
②その上で最小単位のグループのリーダーに清掃の方法を決めても
らい、毎日時間を決めて清掃を実施。
-一部の場所の清掃頻度を上げるということはよいことでもあり、悪いこと
でもある。汚れている原因を探って、解決するという思考を止めてしまっ
ている.
-異常に汚れている個所は生産上の不具合リスクがある場合が多いため。
-清掃に時間がかかるところは“なぜ汚れるのか”を考え、改善することで仕事
自体の効率を上げることができる。
・・・・・
整理・整頓・清掃をすることによって、大分仕事の質は上がってきます。これをどう維持していくかが次の課題となります。
STEP4;清潔
整理・整頓・清掃の維持の位置づけになります。
・・・・・
-清潔は“整理・整頓・清潔を維持すること”と定義できるんだ。汚い空間に
しない、使ったら戻す。これが基本。
-やらなきゃいけないではなく、気を付けるという意識付けが重要。
-小さなことの積み重ねが肝。
-重要なことは作業員の身だしなみ。5Sができていない職場はやはり服装
も乱れている。「初頭効果」といって、6秒で印象が決まってしまう。
-清潔のポイントは、①これまでの3Sを維持。②身なりを整え、印象を意
識する。③見える化で異常がわかる状態にする。である。
・・・・・
清掃と重なる部分はありますが、維持について言及しているのが清潔になります。
STEP5;躾
清潔と共に維持と習慣づけに関して言及します。
・・・・・
-躾とは、“当たり前のことを自然にやり続けることができる状態にする
こと”
-まず礼儀。あいさつであったり、礼儀作法を身に着けさせることは絶対に
必要。
-躾は、整理・清掃・清掃・清潔の維持と習慣づけだが、とにかくトップ
(リーダー)が率先して実践・指導を行うことが重要。
-5Sがキャンペーンで終わってしまう理由のほとんどがリーダーの責任
-定期的に褒める仕組み(コンテスト等)や顧客の工場訪問の際のコメントを
フィードバックする仕組みも作っていくことも一つ
・・・・・
躾は、4Sの習慣化への意識づけの言葉だと思っています。上から目線ではなかなか現場には浸透しません。まず自分が率先して実施して、根気強くメリットを説明し継続していくことが重要です。
番外編①;5S+α:5Sショールーム
各ステップの確認も含め、実際に私が現場で継続的に続けている活動です。
・・・・・・
-自動車メーカーのショールームはこはいつもきれいで、製品がわかりやすく
て、いったらワクワクする。
-お客さんが工場に来たとき、この工場ワクワクするって思ってもらう現場に
する。
-自分たちの作っている商品を格好よく見せたり、造っている人の物語もビデ
オや現場で魅せる。
-モノだけでなく俺たちの製造ストーリーもお客さんにわかってもらう。5S
を武器に。
-通常の5Sの活動と同じで2週間に1度、現場を回って5Sの指摘やショー
ルーム化のアドバイスをするんだ。ただ、常にこれはお客さんがワクワク
するか?という問いを現場メンバーにしていく。そもそも、モノがあふれ
ていて、整頓ができてなくて、汚れていたら、お客さんワクワクなんてす
るわけない。
・・・・・
一つ新しい観点をいれるとマンネリから脱却できます。
番外編②;ツール紹介
現場でメンバーとコミュニケーション共有が簡単にできるツールを紹介しています。会社から配られたもの、持ち込み許可されたiPadがある前提です。
・・・・・・
-Good Noteアプリがお勧め。
-ノートアプリで、メモはもちろん出来るが、その場で撮った写真の編集やコ
メント付与が簡単にできる。さらに、そのメモはPDFになり、すぐに現場メ
ンバーや関係者にシェアできる。
-それともう一つiPadから映像を出力するLightning - Digital AVアダプタの購
入もお勧めする。
-会議室の大画面でフィードバックできる。
・・・・・
その場のメモを瞬時にフィードバックできる仕組みを自分で作っていくとやりやすくなります。
最後に
今回は5Sを説明してきましたが、内容のほとんどは、言われれば当たり前のことと思うかもしれません。でも、きちんと自分で体系化していたり、実践できないないことってあります。そして、この当たり前のことが継続できないのが多くの組織の実体です。思っている以上に当たり前のことを続けるって難しいんですよね。でも、それはやり方や目的をリーダーが明確にしていない、理解していないというのがほとんどの原因です。5Sあくまでも基盤ですが、仕事の質を決めます。これが出来て、初めてトヨタ生産方式やTOC理論。製造戦略の構築に進むことができます。ぜひチャンスがあれば、ご自身の仕事場を見直してみてください。
*このマガジンは原マサヒコ氏著 「トヨタ流5S最強のルール」を参考にして、実体験踏まえて投稿しています。
#製造
#現場
#ものづくり
#理論と実践
#5S
#改善
この記事が気に入ったらサポートをしてみませんか?