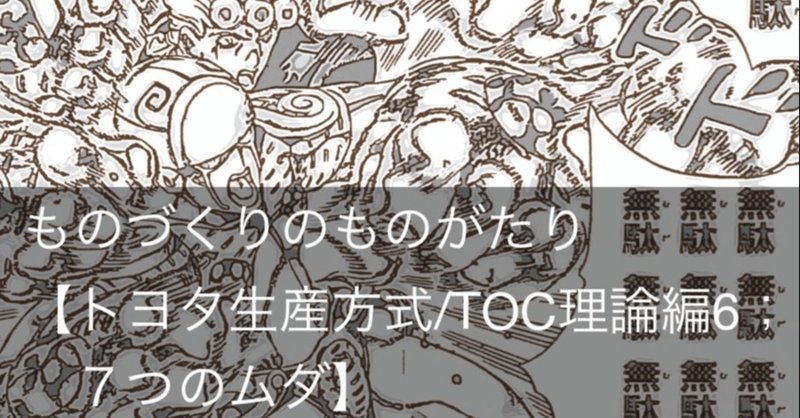
【トヨタ生産方式/TOC編6;7つのムダ】
*前回までの投稿は上のマガジンに入れています。
大卒で大手素材メーカーの工場に配属された若手の紫耀(しょう)と同じ工場に転勤してきた別部署の中堅社員の管理者の健(タケル)との会話です。(もちろんフィクション?)
先輩に指導を受けながら、トヨタ生産方式について学び、自部署の課題を解決に挑戦するようです。前回の投稿までで、ジャストインタイムとニンベンのついた自働化、かんばんの運用について学び、今回はそれらを使って改善するべき7つのムダについて学ぶようです。今回がトヨタ生産方式の理論説明の最後になります。
・・・・・・・・・
👱🏼;おはよう。
🧒;おはようございます。今日は7つのムダの学習ですね。
👱🏼;そうだ。今日は、これまではトヨタ生産方式の改善方法自体を説明したけど、今日はそこに潜むムダについての解説だ。“ムダを分解するとこうなるよ、ここに目をつけましょうね”という内容なんだけども、このムダの改善は、JITと自働化の目的であるんだ。そして、7つのムダは改善を実施する際の問題の対象を整理するために非常に重要な見方になる。次のTOC理論に行く前に抑えておくポイントだよ。
🧒;わかりました。
7つのムダについて
👱🏼;7つのムダは、次の通りだ。
(カコウ)加工のムダ
(ザイコ)在庫のムダ
(ツクリスギ)造りすぎのムダ
(テマチ)手待ちのムダ
(ドウサ)動作のムダ
(ウンパン)運搬のムダ
(フリョウ)不良・手直しのムダ
カイゼンベースさんのHPでは頭文字を取り、飾って豆腐(カザッテドウフ)と覚えると忘れないと記載されている。それでは、それぞれのムダについて詳細を確認していこう。
🧒;飾って豆腐。。。ひねり出した感じですが、覚えやすい。さすがプロのコンサルです。
加工のムダ
👱🏼;まずは一つ目は加工のムダだ。加工とは、熱処理加工、機械加工、溶接作業、仕上げ作業、検査作業等のことを言うんだ。
🧒;検査作業も加工に入るのですね。
👱🏼;そうだ。単純に加工自体の生産性阻害のムダもあるんだけど、わかりにくい検査のムダについてちょっと話そう。加工(検査)のムダは、標準が決まっていないことによる過度な仕上げ作業や、本来不要な検査等が該当するんだ。従来からのやり方だからと言って、やみくもに考えず、本当に必要かどうかという視点でムダを探すことがポイントだよ。
🧒;ありますよね。過剰な品質。。検査のしすぎ。。。でも検査しないでクレームになるのも怖いし、、、そりゃトヨタのように品質を工程で作りこめる仕組みを作るのが重要なんですが、なかなかそうもいかないと思うんですよね。
👱🏼;その通りだけど、そこを言い訳せずにやりきるのがトヨタ生産方式だし、その文化を作っていくということが重要なんだと思う。ここはブレてはだめだ。でも、そのカイゼン過程の中で、規格や基準を作成の際に判断に迷うことはあるのはわかる。QAと議論するだろうけど、これNGかな?OKな基準かな?ということは、どうしても現場ではあるよね。もちろん、性能値等で明確数値で出るものは決められる。ただ、製品に対する薄い傷であったり、後でとれる薄い汚れであったり、明確に決めずらい場合があるよね。
🧒;そうなんすよ。やっぱり多かれ少なかれあるんですよ。もちろんコンプラ違反は絶対にしないですよ。
👱🏼;そういうときは、まず基準を可能な限り決めることが必要だと思う。それでも難しかったら、OKかNGか一度判断してそれを特別記録・管理しておく。そして、ある一定の期間を決めてクレームが来れば基準は厳しくすべきで、ない場合はそれを事実として継続していくんだ。ただ、これも俺の10年の経験では、悩むレベルのものがクレームになっても、大事になることはない。クレームって多くが、え?こんなものが出たの?そりゃだめじゃん。というものだ。だからこれの方法で決めていくことが重要だ。決めないと現場が混乱する。
🧒;なるほど、仮説検証ですね。私もクレーム品が返ってきたときには、“こんなものを出してしまったのか・・”というものばかりです。
在庫のムダと造りすぎのムダ
👱🏼;次に、二つ目在庫のムダだ。これは、三つ目の作りすぎのムダとつながるんだけど、マジでやばい。一番やばい。
🧒;そんなにやばいんすか?
👱🏼;うん。やばい。まず、在庫は、材料、部品、仕掛品、完成品など全てが対象という前提ね。全ての在庫にはそこに存在する理由(目的)が必要で、なぜ今そこに置いてあるのかを説明できない在庫は、全てムダな在庫と判断するんだ。つまり、標準在庫量を前工程の生産可能数量から、最大と最少を決めて管理が必要になる。そしてそれに順じた置き場もね。最少は、後工程の最小ロットより在庫が少ないとが欠品して後工程がモノ作れなくなるから必要だよね。そして、最大は余裕を持つといいことないから設定が必要なになるんだ。
🧒;いいことがないとは?
👱🏼;一見、安全目で多く作っておけばいいと思うけど、これが落とし穴。造りすぎると、在庫(キャッシュ)のムダ・場所のムダ・動作(探す)のムダ・運搬のムダを発生させてしまうんだわ。
在庫増えて、探すとか最悪ね。5Sの基本に戻りましょうってところになる。それと製品も置けなくなって、無法地帯になって置き場も決められないことにもなる。
🧒;確かに、在庫多いとすべてが悪循環になりますよね。
👱🏼;それと、基準のない多くの在庫により、問題が隠れてしまうことが一番注意しなければならない。不良が起きたり、生産性の低下が起きても、結局後工程に迷惑かけてなかったりすると問題視されないのよね。だらだら時間かけて作る文化もできてしまう可能性がある。それと反対に、きちんと在庫管理していると、必要以上に作る必要なく手待ちが発生し、次に話す、手待ちのムダや人員配置のムダも見えてくるんだ。
🧒;恐るべし、在庫管理の光と闇。。
👱🏼;製造をよくわかっている顧客やうちの会社のトップも5Sと在庫管理のレベルでその工程のレベルを判断しているといっても過言ではないと思う。でも、簡単に見えて、なかなか管理できないんだ。生産計画の頻度とも連動してくる。実践の時に必ずぶつかる壁だ。
長くなるから、どこかで具体例で製造としての在庫管理の仕方を説明するよ。
🧒;わかりました。
手待ちのムダ
👱🏼:4つ目は、手待ちのムダだ。これは、その名の通り作業をすることが無く、手が待ち状態のことを言う。当然、手待ちは付加価値を生まないよね。でも、気を付けなきゃいけないことは、手待ちは作業者が作業スピードを調整することで簡単に隠れてしまうということだ。
🧒;確かに作業をゆっくりにすれば、手待ちにならないですね。
👱🏼;そうだよね。これには標準作業・標準時間を決めて手待ちを見える化できる状態にまずすることが重要だ。ちなみに経験では、やっぱり歩く量が多い工程が潜在的な手待ちが多いと思う。何か仕事を探してうろうろしていまうというか、仕事してる風になってくる。ただ、勘違いしてはいけないのは、これは現場の作業員の問題でなく管理の問題であるということだね。うろうろしてしまうということは、標準が決まっていない。もしくは標準が正しくない(人が多い含め)という可能性が高いんだ。
🧒;ですね。サボろうという作業者って実際そんなにいないですもん。
動作のムダ
👱🏼;5つ目は動作のムダだ。探すムダは動作のムダの一つ。さっき少し話したね。ほかに動作のムダは、しゃがむ、持ち替える、調べる等の人の動きの中で付加価値を生んでいない不要な動きのことも指すよ。これは多くの場合、標準作業が誰でも同じように出来るようになっていない場合や訓練不足等で発生する。常日頃から動作を観察し、付加価値を生んでいない動きがないか探していると、必ず動作の中にムダが存在していることに気付くはずである。
🧒;すません。多分俺わからないっす・・。鈍感なんですよ。
👱🏼;いや、まだまだ若いし直観で理解してくのは難しいよ。そういう時は、MMC(マンマシンチャート)、ワークサンプリングなどをすると定量的に動作のムダがみえてくるよ。これは長くなるからここでは話さないけど、IE(インダストリアルエンジニアリング)と呼ばれる分析手法で、単位時間区切って記録をとりで各々が何をしているかということを見える化する手法だ。これをやると動作に関しては、だいぶ観察ができる。
🧒;そうなのですね。わかりました。
運搬のムダ
👱🏼;6つ目が運搬のムダだ。運搬のムダとは、必要以上のモノの移動、仮置き、積み替え等のことを言う。工程のバランスが崩れていたり、モノの流れが決まっていない等のことから発生する。特に、造りすぎのムダから発生する運搬のムダに要注意なんだ。
🧒;ここまでくると私わかります。例えば、作りすぎてしまうと、奥から製品を取り出すために、その前にある在庫を別場所に置きますよね。ただ、作りすぎてるんだから置き場所がなく、遠くに運ぶ。そして、奥のものを取り出した後に再度遠くにとりに行って元の場所に置くということが起こる。明らかにムダですね・・。
👱🏼;そうだ。でも、それならまだいい方だ。実は、これを繰り返していくと、遠くに置いたものを元の場所に戻さないという現象がどうしても起こる。そうすると、遠くから製品を運搬することが起きてしまったり、探す作業がより増えてしまう。
🧒;あちゃー。。ですね。このムダは意識しておかないといけないですね。
不良・手直しのムダ:
👱🏼;最後7つ目は不良・手直しのムダだ。不良・手直しのムダとは、不良品を廃棄、手直し、造り直しすることだよね。これは分かりやすい重要なムダだ。標準を守らなかったり、標準が決まっていないことでも発生するし、管理の甘さでも発生する。不良・手直しを発生させないためには、各工程で品質を作りこむ自工程完結の考え方が大切だ。でも、これはなかなか難しいよね。歩留まり改善なんて永遠のテーマだからね。ただ、ここで考えなければいけないのは、不良・手直しはコストアップではもちろんあるんだけど、工程をストップさせてしまうリスクがありそのことの方が大きなインパクトになるということなんだ。
🧒:どういうことですか?
👱🏼;不良を作るとさ、もちろん一番最初の工程からやり直しじゃない?そして、同一のものをひたすら作り続ける製品であれば、バッファ分を作っておけばいいんだけど(これもそもそもムダだが)もし、一品一様のような製品であったとしたら?その一品一様の束が揃わなければ後工程が組み立てや製造できないような製品だったらどうなる?
🧒;また、その不良を起こした工程まで部品が届くのを待って、生産して、そして揃ったら後工程に送らなければいけなくなりますね。
👱🏼;その通りだ、後工程もそんな受け取っても作れないものを受け取らないよね。場所も取られるし。そうなるとどうなるさ?
🧒;はい。そうなると。。。すべての工程の生産が遅れる。そして欠品リスクが生じる。。結果、欠品しないようにリードタイムを長く客先に提案する。特に後工程の歩留まりが低いと実際の生産日程より倍かそれ以上のリードタイムが必要になる・・。
👱🏼;その通り、そうするとその企業の競争力が落ちていくんだ。不良っていうのは、一つの工程で数%歩留まりが減ったくらいで大きなインパクトを与えるようなコストアップにはならないと解釈する場合が多い、(ほぼ事実)そして、ある程度までいくと、この程度でいいやとなる。でも、バッファをとるための全工程のリードタイムの増加につながってしまっている。
🧒:それは顧客の購買行動に影響を与えます・・。
👱🏼;そうなんだ。だから不良や手直しを減らすのは本当に大変なんだけど、考えるときはそれほど重いものとして改善活動を徹底的にやっていく必要があるんだ。
🧒;ですね。そう思うととことん改善の意味がわかってきます・・。
まとめ。最大の問題となるムダ
🧒;不良問題怖いっすね。
👱🏼;とはいえ、対策の順序はあるよ。まず最も大きい問題といわれているのは、造りすぎのムダだ。これを、叩かない限り大きなムダが発生し続けるし、結局、造りすぎを改善しようとすると不良のムダの改善にもつながる。一部、上でも説明したけど、作りすぎてしまう理由は、人や設備を余分に持っているからで、造りたくなってしまう理由は、設備故障や不良等に対して、安心をしたいからだ。
🧒;はい。すごくわかります。
👱🏼;しかし、現在は、売れない可能性を持つモノを造り在庫になると、たちまちキャッシュリスクになるよね。また、さっきで話してきた通り、造りすぎを容認してしまうと、運搬車・リフトの増加、倉庫・保管スペースの増加等、どんどんどんどん新たなムダが発生するよね。
更に、在庫が多すぎることにより、問題が隠れてしまい、本来潰すべきことが中々表に現れず、改善が進まないことにもなるよね。造りすぎのムダが発生している限り、原価が継続的に下がる体質にはなれないんだ。
🧒;というか、結局、造りすぎのムダから派生する、すべてのムダを抑えるためにJITと自働化があるということですね。それを達成するためにカンバンもそうだし、平準化も対応しなければならないんだ。
👱🏼;そうなんだよ。トヨタ生産方式の本質はムダの削減だって最初にいった話に戻ってきたね。
🧒;おー、なるほど、、つながりました。
👱🏼;ここまで来たところで、トヨタ生産方式の基本の説明は終わりだ。
🧒;ありがとうございます。トヨタ生産生産方式は、ほんと多岐にわたる活動でどこからやるべきかっていうのはやはり考えないといけないですね。まさに問題から始めないと迷宮入りですね。
👱🏼;そうだ。そこまでわかれば今のところはOKだね!では次回からはザ・ゴールのTOC理論について学ぼう。同じようなことを言っているんだけど、不良や動作云々の個別の話は少なくて、全体の最適をどう作るか、JITをどう作るかということに焦点を当てた話なんだ。そんなつもりで聞いてくれ。
・・・・・・・・・・・・・
今回は7つのムダについて説明しました。文章ばかりですみません・・。さて、このムダは多岐に渡りますが、結局造りすぎのムダから発生してくるものが多いです。これをどう抑えるかがトヨタ生産方式の肝になってくることは、くどいくらいわかったかと思います。そして、JITと自働化がそのために重要な役割を果たすということも分かったかと思います。あくまでも基本ポイントでしたが、ここでトヨタ生産方式の説明は終了です。次のお題は、ザ・ゴールでお馴染みのTOC理論です。より収益向上に対してアプローチしたJITの概念が出てくると思っています。
理論編が続きますが、我慢してお付き合いよろしくお願いします。
次の記事は下記です。
#製造
#現場
#理論と実践
#ものづくり
#トヨタ生産方式
#リーン生産方式
#改善
#かんばん
#7つのムダ
この記事が気に入ったらサポートをしてみませんか?