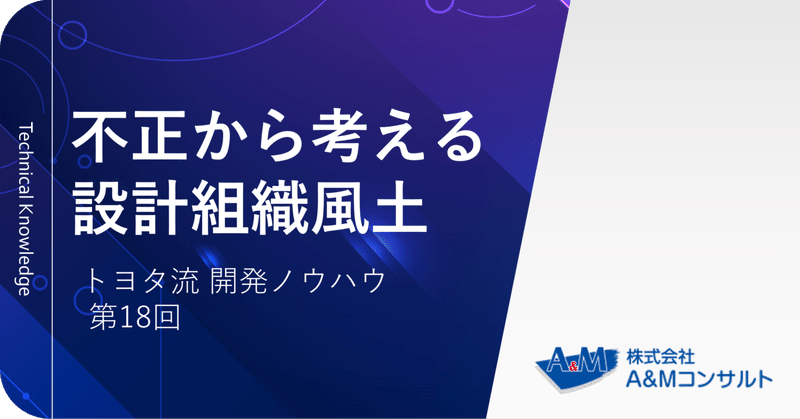
不正から考える設計組織風土|トヨタ流開発ノウハウ 第18回
近年、自動車メーカーによる不正が多く報告され、元自動車メーカーの技術者として非常に残念に思う一方、なぜこのような不正が多くなっているのか疑問に感じています。
不正を実施してしまったのは、技術者自身ですが、不正をはたらくに至った背景から、組織的な問題ではないかと考えます。
今、技術者がおかれている状況は、多くの業務をこなさなければならず、ただ単に設計をしていればいいわけではありません。
設計業務(構想検討、シミュレーション、評価、試作、生産性確認など)に加えて、フロント側(商品企画部や営業部門)のサポートや情報提供、さらにはEOL対応、製造段階での検査内容の確認や製造工程での機能や性能部分の確認、取り扱い説明書の作成、市場不具合の現地確認や対応など、製造業のインプットからアウトプットまで全ての業務に関わらなければなりません。
もちろん大企業の場合、その内容が細分化され、担当する技術者が異なる場合がありますが、製品設計のマネジメントの全体像をコントロールするのは、限られた技術者です。
上記のような多くの業務に関わり、実行しなければならない技術者だけに不正の責任を押し付けるのはお門違いです。
不正を行った技術者が追い詰められた背景を確認しなければなりません。
その背景を確認してみましょう。
ポイント①:目標遵守
技術者にとって、目標は必ず守らなければならない事項です(技術者だけではありませんが)。
目標が未達になってしまうと、お客様に価値を提供することができず、販売したとしても、お客様は見向きもしないでしょう。企業が生き残るためには製品やサービスをお客様に買ってもらわなければなりません。
そのためにも掲げた目標、もしくはお客様から要求されている内容は確実にクリアしなければならないのです。
しかし、ここに落とし穴があります。
目標は目標でも必達目標と努力目標(チャレンジ要素を含む)を設定し、設計開発をスタートしなければならないのです。
これが多くの企業では、いつの間にか努力目標が必達目標となってしまっており、ある決められたリードタイムの中でクリアするように仕向けていませんでしょうか?
近年の不正では法規に絡むことから、必達目標に対しての不正が行われていると想定しますが、ただ単に法規を満たす事だけではなく、将来的に変更されるであろう法規の内容についても必達目標の中に入っていませんでしょうか?
そのような設計方針を立案してしまうと、難題である将来の法規対応の検討に時間がかかってしまい、現状の法規対応の設計が疎かになっている可能性があります。
このように高い目標を掲げることは、会社全体の成長にも繋がっていきますが、技術者に無理をさせてしまった結果、追い詰められている技術者が多く存在します。
不正をしない仕組みも必要ですが、まずは目標設定の考え方について見直し、今の技術者の負荷状況で実行できるのかどうかをマネジメント層がしっかりと判断していく必要があるでしょう。
ポイント②:問題を言い出せない組織風土
設計業務において、問題は必ず発生します。ミス、問題のない設計開発はありません。その際に問題を問題として正しく組織に報告できる風土であることが重要です。
問題には、ミスや失敗など人が起こしてしまった内容と、未知の内容など様々あります。
失敗学を研究されている畑村洋太郎東京大学名誉教授によると失敗は3つに分類されます。
①織り込み済みの失敗。ある程度の損害やデメリットは承知の上での失敗。
②結果としての失敗。果敢なトライアルの結果としての失敗。
③回避可能であった失敗。ヒューマンエラーでの失敗。
この3つの中で人間は③のヒューマンエラーを隠す方向にあります。
それは組織の中で今の自分の立場や関係性を崩したくないからです。
小さい不正はこの③で行われるでしょう。
しかし、近年の不正の内容からすると②の失敗である可能性が高いと考えています。
小さな失敗という内容ではなく、ポイント①で解説した高い目標をクリアできずに失敗に失敗を重ね、とうとう言い出せなくなったという状況に陥ったのではなないでしょうか?
②の失敗は、企業として価値のある失敗であり、その事実をしっかりと認め、今後に活かせる風土が重要になってくるでしょう。
トヨタ自動車では先人たちの教えで次のような内容があります。
「失敗は視えるところにおけ!」
これは失敗を失敗として認めた上で、その失敗を会社全体の財産にしようとする考え方です。このような考え方がなければ、失敗を言い出せませんし、技術者自身の中だけで解決しようとしてしまいます。
また、失敗が視えなければ誰も助けることができません。
これからの組織風土は「失敗を失敗として認めることができる」状態でなければならないでしょう。
ポイント③:組織体制
ポイント②で解説した「技術者自身で解決しようとしている」。ここに多くの組織体制としての問題があります。
技術者が考えた構想内容を評価するタイミングで、構想を検討した技術者自身が評価を行っている文化です。これは自分を自分で評価するのと同じことであり、ストイックな人間でない限り、多少の甘えは発生してしまうでしょう。
この甘えをなくすためにも構想検討などの設計者と、評価をする設計者は分けるべきです。
他人が設計した内容を正しく評価することができる、また、他人に評価してもらう上で曖昧な部分を残すことはできないなど、両者ともに正しく業務をこなすことができるようになるでしょう。
この内容には1点、注意点があります。
評価する技術者もスペシャリストである必要があります。
設計の業務についてまったく知らないメンバーが評価したとしても、言われた通りの評価を実行していくだけで、それでは意味がありません。
評価する製品内容について、設計者の意図や考え方をしっかりと把握しておく必要がありますし、さらには、製品構造や部品特性、制御内容など幅広い知識が必要となってきます。
不正が発生すると再発防止策として「第3者機関が確認する」といった対応策が立案されることがあります。
第3者が確認すること自体悪いことではありませんが、この第3者がしっかりと知識を保有した上で、第3者自身で判断できる状態になければならないのです。
皆さん、いかがでしょうか?
特にマネジメント層の皆さんは技術者が追い込まれて不正に走らないよう風土を見直してみませんか?
この技術部門の組織風土改革によって、不正が行われない組織になるだけではなく、技術者全員が楽しく、明るい顔で業務を遂行できるようになります。
今からでも遅くはありません。
将来の入社するであろう技術者のためにも、風土の改革を検討してみてください。
講師プロフィール
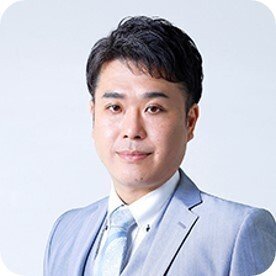
中山 聡史 |株式会社A&Mコンサルト 取締役専務 経営コンサルタント
2003年、関西大学 機械システム工学科卒、トヨタ自動車においてエンジン設計、開発、品質管理、環境対応業務等に従事。ほぼ全てのエンジンシステムに関わり、海外でのエンジン走行テストも経験。2011年、株式会社A&Mコンサルトに入社。製造業を中心に自動車メーカーの問題解決の考え方を指導。2015年、同社取締役に就任
主なコンサルティングテーマ
設計業務改善/生産管理・製造仕組改善/品質改善/売上拡大活動/財務・資金繰り
主なセミナーテーマ
トヨタ流改善研修/トヨタ流未然防止活動研修/開発リードタイム短縮の為の設計、製造改善など
※2023年9月現在の情報です
近著
この記事が気に入ったらサポートをしてみませんか?