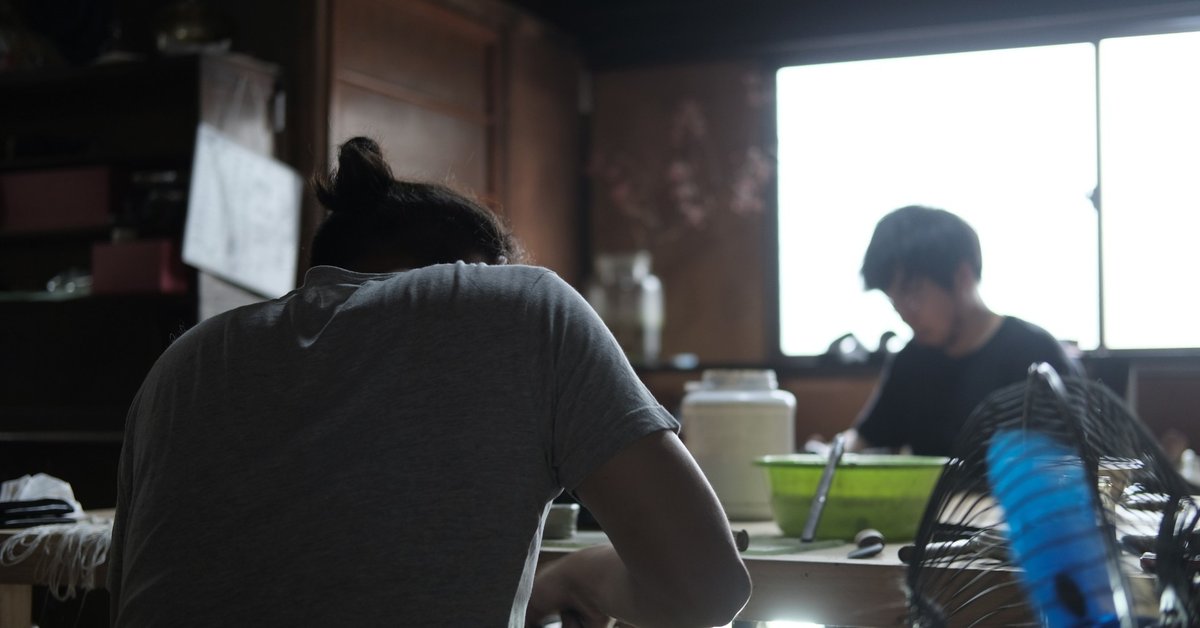
自分の靴ができるまでを見に行った話②
前回の続きになります。ここでは2日目と3日目の工程を説明します。
2日目は初日に成形したアッパーとソールをつける底付の工程です。
お2人は、かつて靴メーカーへ勤務した経験がおありとのこと。そこで底付をメインに担当されたそうです。底付は靴の中でもかなり時間と手間のかかる工程だそうですが、その経験から他の人と比較してもかなりのスピードで行うことができるとのことでした。
まずは釣り込みという工程です。釣り込みとは、簡単にいうとアッパーとソールと言った革を木型に釘で打ち付けていく作業です。ただし、弛みなどが出てはいけないので、専用の道具を利用して、強く引っ張りながら木型に馴染ませつつ、少しずつ釘を打ち付けていく作業です。
ちなみに、釣り込みに使用する道具を「ワニ」というそうです。ちょっとギザギザはしていますがが、ワニっぽくない見た目です。鳥とか恐竜っぽい。
ペンチとハンマーが一体になったようなもので、革を木型に合うように引いた後、すぐに釘で止めるために叩ける作りになっています。この器具でないと、木型に革をなじませることが難しくなります。
このワニ、国によって違いが結構あるそう。竜崇縫靴店は2人とも、ドイツ製と日本製のものを使っています。久保さんのワニは堀場さんからのプレゼント。愛を感じました。
釣り込みをするにあたって、木型に皮を馴染ませるため、金槌でしっかりと芯材をなじませます。アッパーと同じです。
その後、縫い付ける前にアッパーの内側の革、芯材、外側の革を接着剤で一つ一つ止めていきます。
僕の名前を書いている芯材に、塗られていく糊。永遠に表に出ることはない部分なので、少しだけ寂しいようななんとも言えない気持ちになります。
いよいよ釣り込み作業ですが、サンプルで一度実際に試させて頂きました。革のシワを伸ばしながら釘を打って固定させるのがかなり難しく、全然うまくできません。自分では革をしっかり伸ばせていると思っていても、全然伸ばせていないという状態です。
「革がしっかり伸びてシワになっていないかどうかは、目で見る以外にも、指先の感覚で判断しています。その日の湿度や使っている部位によっても革の伸び方が変わり、仕上がりにも影響が出てくるので、一つ一つ丁寧に注意しながら進めていきます。」と堀場さん。
かかとと爪先のような、カーブの強い部分は釘を多く打ち込み、シワにならないように釣り込んでいきます。余った革を削り落として次の作業の邪魔にならないよう、釘を倒してから再び金槌で革を木型になじませます。
ここでの叩きは、釣り込みで引っ張って伸びている革と毛穴を叩いて締めています。革は伸びると変色するのでそれを防ぎ、今後の伸びを防ぐ目的です。
さらにストレートチップの場合は爪先の縫い目のめくれを防ぐ意味だそう。
その他、芯材の端を潰して馴染ませるなど、地味な工程に様々な意味があることを教えてくださいました。
次の工程は掬い縫い。
靴のアッパーとソールを合わせるための、細長い革(ウェルト)があります。紳士靴の縫い糸が見えているあそこです。それをまずはアッパーに縫い付けるための工程です。
靴の製法にはさまざまありますが、多くはこの部分で製法の名前が分かれます。有名なものでは「グッドイヤーウェルテッド」「マッケイ」などが挙げられます。
竜崇縫靴店の靴は「ハンドソーンウェルテッド」という製法です。この手で行う掬い縫いの製法のことで、靴の内部を薄くでき軽いことや通気性がよくなること、返りが良く歩きやすいなどのメリットがあります。
掬い縫いに入る前に、まずは掬い縫いに使用する糸を用意します。
手で撚るところから始めます。
9本で寄られている糸を分解し、糸の先端が細くなるように階層を作って階段状に細くしていきます。根元から先に行くにつれて、9本→6本→3本と順に細くなっていくように分解して糸をちぎり、撚り直すという作業。細かな作業ですが、慣れた手つきで次々に進めていくのは久保さん。堀場さんが使う分も一緒に撚って、「してあげてると次に早く進むし、してもらうと嬉しいでしょ。」と笑いながらも手は止めず次々に進めます。
「靴を作り始めた人は、師匠が使うこの糸を撚るところから始めます。基本の作業みたいなものですね。」
久保さんが撚った糸に、堀場さんが「チャン」と呼ばれるワックスのようなものと、蜜蝋を塗りつけていきます。
「チャン」は松脂などを利用した接着剤と防腐剤を兼ねたもの。靴に縫い付けたコットンの糸が雨や湿気で腐敗してしまわないように、縫い付けた革にしっかりと馴染むようにという目的で使用。油なので、雨や湿気の防止にも使える、各職人さんが自分たちで配合して作るモノだそう。
準備が整ったら掬い縫いがスタート。靴をベルトで固定し、足で挟んで動かないようにします。
先が槍のようになっている工具、掬い針を利用して、一本の長い糸の両端を靴に縫い付けていきます。靴の一部だけ掬い縫いするメーカーもあるそうですが、竜崇縫靴店は全周ぐるっと掬い縫いを行います。糸を通すときは勢いよく、しっかり力を入れて引きます。かなり強く締めています。こうすることで、しっかりと糸を固定することができる上、摩擦熱でチャンが一度軽く溶けます。その間に引き締めるとその部分で冷え、しっかり糸と革が馴染み、固定できるということだそう。
掬い針で開ける穴を大きくすると摩擦が生まれにくくなるので、小さく開けて糸を通す、といった繊細で目立たないけれども大切な工程を進めます。
掬い縫いは横の部分など、おおよその部分は均等な感覚で針を通しますが、爪先などの曲率の大きい部分はどうしても偏りが出てしまいます。偏りが出ると、穴を細かく開けなければならず、穴同士がが干渉すると最悪破れてしまいます。破れにくくするための緩衝剤として、先ほど先ほど久保さんが手ずから撚った糸を使用します。
「無駄なものは入れません。必要なものは、すでにあるものや使っているもので賄います。」革と同様、様々な意味で無駄を出さないものづくりを心がけています。
かかと部分の内部にあたる芯の部分には金属の板を入れます。
竜崇縫靴店の靴の特徴には返りの良さがあります。製法によるものではありますが、反り返りすぎることや靴の捻れなどを防ぎ、安定させることが目的の背骨のようなものです。
竹などでも代用できますが、有機物のため溜まった湿気で腐ることもあり、強度を含めて金属がベターだという効率性も考えたチョイスになっています。
金属の表面は滑らかになっており、糊付けがしづらいというデメリットもありますが、それを克服するため、一本一本やすりで表面を削っていきます。隙間に接着剤が入りやすく、安定させることができためです。
掬い縫いの後は、縫った上から革を一枚貼る。インソールのさらに下の部分にあたる。少し前の工程でくり抜いて凹んだ部分を隠すように貼り付けます。
靴の内部に入っている芯材は、先述の通り強度を持たすために銀面と呼ばれる革の表側を使用しています。履いた際の感覚を損なわないために分厚い革を薄くスライスし、薄くしつつも強度を出すために銀面を使用しています。
では、スライスされて残された銀面のついていない側の革はどうなるのか。それを内部に使用しています。ある程度の厚みがあり、クッション性も出てきます。
先ほどの「必要なものは、既に使っているもので賄う」というポリシー、こういった部分にも現れていました。
その後さらにソールを貼り付け。この後に控えている「出し縫い」の工程のため、まず仮止めとして糊で貼り付けます。乾いたら行うのが、通称「ヒドゥンチャネル」職人さんたちの間では「ドブ起こし」と呼ばれる作業です。
ドブ起こしという名前とは裏腹に、高級紳士靴で仕上げを美しくするための工程です。
靴には「出し縫い」といって、靴本体にソールを縫い付ける工程があります。紳士靴のコバの上から見える縫い目がそれにあたります。この出し縫いは、ソールを貫通しているため、縫い糸が靴底から見える形になります。多くのシューメーカーの靴の裏側も同様に、縫い糸が見られます。ドブ起こしは、その出し縫いの糸を隠し、美しく仕上げるために行われます。ソールの外周を1mmほどめくり、出し縫いの糸を通すための溝を掘ります。縫った後にめくったものを戻し、接着剤で貼り付けて蓋をする、という仕組みです。
見栄えだけでなく、糸の上を革が覆う形になるので糸が切れるのを遅らせるという実用的な意味もあります。
ドブ起こしも他の多くの工程と同様にミスをするとせっかくの今までの作業がダメになる、取り返しがつかない工程です。
革の厚みを均等に薄く薄くめくっていく集中力が必要になります。
久保さんは出し縫いの職人さんの作業のしやすさ、縫いやすさを考慮し、少しだけ深めにめくっていらっしゃいます。
堀場さんへの心配りもさることながら、人と一緒にものづくりをされる職人ならではの思いやり。
ここからが3日目になります。いよいよ靴が完成します。
出し縫い。
竜崇縫靴店は、出し縫いのみ外の出し縫い職人さんに依頼しています。なぜそれだけ外の職人さんに依頼しているのか。
出し縫いのやり方は二通りあり、1つは出し縫い用の機械を使用する方法。2つ目は手でやる方法。
機械は高額でなかなか手に入らないことや、2人とも手縫いの技術を持っていますが手作業では時間がかなりかかってしまうため、靴自体が高価になってしまう。
出し縫い職人さんは80歳ほどの方で、安価で極めて高い質の作業をされており、価格とクオリティのバランスを鑑み、職人に依頼するという選択をしている。
また、大阪で唯一その方が出し縫いをされており、国内屈指の腕前だそう。
けれども出し縫い職人さんは、自分がした苦労を他の人にして欲しくないとの思いから、後継は設けていないそうです。
出し縫い職人さんの作業風景は1足1〜2分でこなすほど速いが、コバからの幅は均一に美しく縫い付けてあります。
綺麗に縫うのは難しく、かなりの修練を必要としています。美しく正確にするのは一朝一夕でできるものではありません。
工房に戻ってきてからは、ドブ起こしの革を戻して、縫い糸を隠す作業に入ります。
戻す前に、コバの角を落とします。これはデザイン上の問題で、コバの丸みをだして柔らかい印象するためです。
ガラスを使用するのも、あるものを使うという工夫。久保さんに、大きなガラスを割って使いやすくするところを見せていただきました。
「割り方のコツなどもあり、毎日やっていることでわかることが増えてきます。靴作りも同じです。」
次はかかと部分の積み上げの作業。
木でできていると思う人も多い部分、厚みのある革を何枚も使用し、文字通り「積み上げる」。ずれてしまうとバランスが崩れたり見栄えに影響が出るため、注意が必要になります。レザーソールの場合は4枚、
竜崇縫靴店がいつも使用しているリッジウェイソールというラバーソールの場合は、積み上げの革を3枚貼り付けてそのうえにラバーを貼っていきます。
積み上げていく革に接着剤を塗り、白熱電球を利用したヒーターにあてて温度を上げることで溶剤であるシンナーを飛ばします。
シンナーが飛んでから接着させるとしっかりと貼りつきます。
事務用品のノリの場合、乾く前に貼り付けなあかん!と考えてしまうので、事務用品を利用している人間からすると逆の手順で面白いなと思いました。
靴の場合は溶剤を飛ばしてから貼り付け、金槌で叩くことでしっかり接着させるという手順です。
積み上げを接着してから、はみ出た革を大まかに革包丁で削ります。そのあと、やすりで断面を整えて滑らかにならしていきます。
これらの作業を繰り返していき、一番底にくる部分を貼り付ける際に、それまでの積み上げに釘をかかとの形に合わせてぐるっと打ち込みます。
これには錆びた釘をあえて使用しており、断面のざらつきが摩擦を生むことで抜けにくくなるという理屈です。
ラバーの場合、凹凸の凹んでいる部分が積み上げの断面に来てしまうと、見栄えが悪くなるために、そうならないように計算して貼り付けます。
貼り終えてからは、底面を全てやすりがけ。つるつるになるまで行っています。そのあと染料で底とコバを染色します。アッパーにつかないように注意しながら縫っていきます。
乾いたら、レザーソールの場合は底を鏡面磨きを。
「鏡面磨きをすると、お客さんがとても嬉しそうで。ドレスシューズではないから本来はしなくてもいいが、喜んでもらいたいからやっている。」と堀場さん
最後に爪先のスチールをつけて熟成。木型に長い時間入れておくことで、馴染ませてからお客さんの足元へ届けます。
ここに書ききれないほど、履く方のことを考えた靴を作るため、本当に細かい調整や作業を繰り返している竜崇縫靴店。
気になる方は、是非私か彼らにご相談くださいませ。
この記事が気に入ったらサポートをしてみませんか?