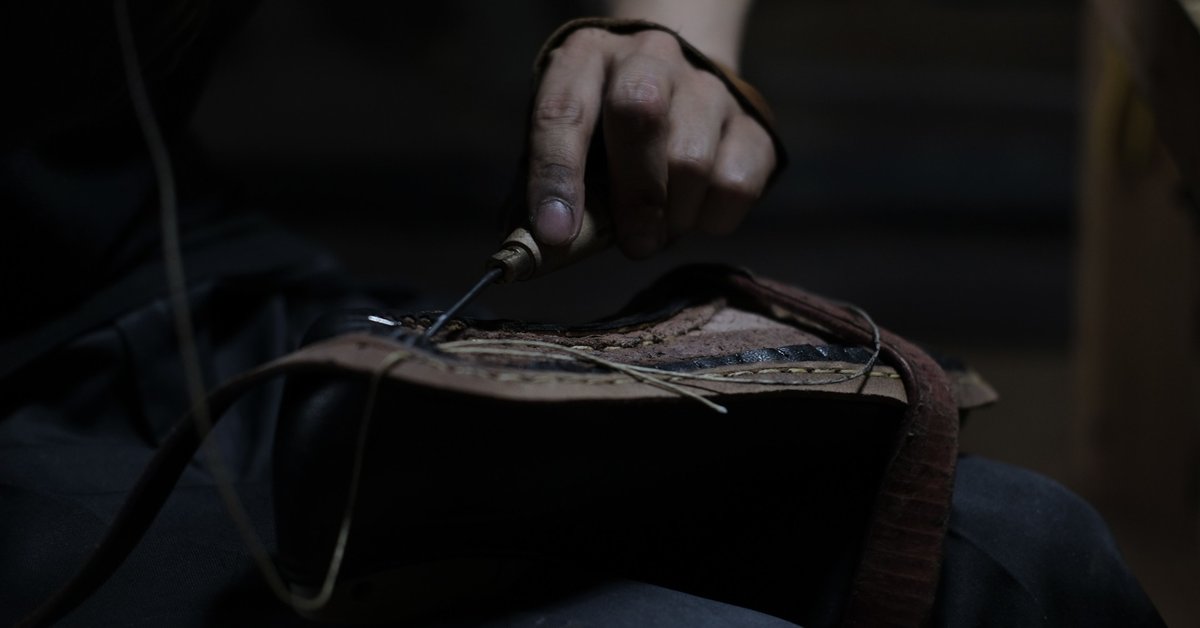
自分の靴が出来るまでを見に行った話①
セレクトショップの存在意義は、ただただ物が置いて在るという訳ではないと思っています。
お客様に良いものを届けるということは前提としてありつつ、作っている職人さんや作家さんのものを本人以上に理解し、伝えることが求められますし、それを望んでいるお客様も多いのではないかなと感じます。自分が消費者としてお店に向き合ったときも、そういったことを知りたいと思います。
僕の拙文で伝わるか不明ですが、もしよかったら気になることはご連絡ください。頑張ってお伝えします。
僕のお店では様々な職人さんがイベントを行ってくださいます。
その中で定期的にオーダー会を開催している「竜崇縫靴店」(https://ryusouhoukaten.com/)という靴の職人がいます。
堀場崇夫さんと久保竜治さんの2人組靴職人です。2人ともまだお若く、30代前半です。
堀場さん
久保さん
大阪の製靴塾を卒業後、それぞれメーカーに勤務しつつオリジナルブランドとして竜崇縫靴店として活動を行なっていたそうです。
彼らに「靴作ってるところみせてくれ〜」とお願いしたところ、二つ返事で「いいよ〜」と快諾され、文字通りお邪魔してきました。
「君が来たときだけ君の靴の作業をするから、来ないと永遠に完成せんようにするよ!」と堀場さん。
お話しする中で、「知り合いもお客さんも、僕らが靴作ってないとおもってんちゃうか。」と笑いながらおっしゃっていました。
たしかにぼくも完成した靴を見ただけで、実際にどんなふうにできているのかということはもちろん、他の人が作っててもわからんな。ということで、しっかり見させて頂きました。
靴の用語もふくめて、ざっくりとお話できたらと思います。
場所は大阪の某所。何度かお邪魔した工房ですが製作風景を見るのは初めてでした。
お邪魔すると堀場さんと久保さんが出迎えてくださり、雑談を交わしつつ靴の製作の説明がスタート。
今回は3日に分けて工房にお邪魔し、靴の製作を見学。3日間の工程を大雑把に流れを説明すると
(1)アッパー等、部材の準備
①革の切り出し(アッパー、芯材、インソールなど)
②縫い合わせ
③木型へのフィッティング
(2)底付(アッパーと底をくっつけます)
①釣り込み
②掬い縫いのみぞ掘り
③掬い縫い
④出し縫い
⑤積み上げ(かかと部分)・仕上げ
(なんとなく個人の感覚として、こう言う工程になるのかなと思い表現しているので、まちがっていたらすみません。)
(1)で大まかに靴に必要な革をまとめ、(2)で木型に革と底を貼り付けて完成させる、と言う流れかなと見ていて思いました。
実はこの中に出てきていない部分で重要なものがあります。木型の作成です。竜崇縫靴店は木型は事前に作成して受注会に臨み、その木型をベースに個々人の足へフィットするよう調整しています。木型は靴の個性や履き心地を左右する重要なポイントの1つになっており、かなり時間をかけて製作されているそうです。
工程の説明に入ります。
まずは革の切り出しから。
中底とアッパー、ライニングの切り出しへ。
アッパーとは、簡単に言うと靴の顔の部分。よく見ると表の革と内側の革は違います。分厚い表側と薄い内側というような感じです。詳しくないと、意外と一枚の革でできていると思っている方が多いかもしれません。表をアッパー、裏をライニングと言います。アッパーがトップスでライニングが肌着見たいものです。中底はインソールという、足に直接当たる底になります。
切り出しは型紙を利用して、型に沿って切っていくのですが、アッパーを切る前に重要なことが2つあることを久保さんに教えていただきました。
1つ目は無駄のない配置で革を切り出すこと。単純にもったいないということ以上に、「生き物の命を頂いている以上、無駄にしてはいけない」という精神。
日常の中ではレザーは当たり前に使用していると同時に、生活と切り離せないものになっています。それらが他の生物の命の上に成り立っていることなどを考えさせられました。
2つ目は傷のチェック。
光を当てて目視し、革を伸ばしながらアッパー部分の傷の有無を確認します。靴に使用すると裂けてしまう可能性があるため、そう言った部分は避けて使用。また、革の伸縮の方向を確認。靴には伸びて欲しい方向と、逆に伸びてはいけない方向があるそう。
それら革の伸びる方向を確認しながら切り出ししていきます。実際に手で皮を引っ張らせていただくと、確かに伸びる方向と伸びない方向が存在していました。
それらの向きを鑑み、切り出しを行います。
最近では、革の表面をレーザーで読み取り、自動でカットするような最新鋭の機械が出ているそうです。
しかし、細やかな傷の読み取りや、伸縮を読み取るなどの作業はオートメーション化されたものではできず、人が作るからこそできるものだそう。
機械の場合は、靴が完成してから不良品を廃棄するそうで、革やその他の部材が無駄になってしまいます。
そう言った部分をきちんと一点一点確認し、時間をかけてチェックします。
また、インソール部分には銀面(※革の表皮)のついた革を使っています。大部分が見えない部分になる上に、コスト的にも高くなるので使用しない方も多いそうですが、銀面の有無で強度が大幅に変わるため竜崇縫靴店では銀面のあるものをかなり分厚く使用しています。繊維を1枚のテープで貼り付けているようなイメージをしていただくとわかりやすいかもしれません。テープ(銀面)で固定されるので強度が増します。
加えて、革の中に入れる芯材も同様に銀面のある薄くスライスした革を使用。現在では「シナ玉」という、繊維にシンナーをしみ込ませ固めた樹脂を使用するのが主流になっていますが、これでは踏めば破損してしまいますし、凹むと元に戻らないそう。経年の劣化もかなり大きく、永く使用するには向いていないそうです。
一方、革の場合は経年劣化が少なく、シナ玉で生じるデメリットを解消することができます。
これもインソール同様に、コストはかかりますが、耐久性や修理の観点など、長く使用することを意識してこの製法になっています。
芯材、基本的に一生表に出ることのない部分です。じつはお客さんの名前がここに書かれています。みなさんが竜崇縫靴店の靴を履いているなら、じつは芯材に彼らの手書きの名前が書かれているのです。
型に沿って切る際も手を止めてしまうと綺麗に切り出しができないため、丁寧にしつつも手を止めず、素早く切り出していきます。
「靴は減点方式。皮の切り出しなど、前半の工程での妥協やしくじりは、後半の工程に悪い影響しか与えない。ミスが以後良くなることはないので、すべての工程をきっちりとやる。」と久保さん。
切り出しの後はインソールと芯材を水につけてしばらく置いたのち、木型に合わせて釘でうち、チューブで圧迫し、金槌で叩きます。こうすることで、木型の立体感をそのまま再現することが可能になります。木型の立体感を再現することで足へのフィット感が増すためです。
芯材についても同様に、木型に沿うように金槌で叩きます。こうすることでより木型にフィットし、履き心地もよくなります。
並行して、アッパー部分。内羽の部分に靴紐が通るホールの金具を入れていきます。
今回見学させていただいたHI−01は特殊な作りで金具が表から見えなくなっています。強度や見た目の設計も深く考えているからこそ、こういった靴の制作が可能になります。
また、切り出した革をミシンで縫い合わせていきます。強度のことも踏まえ、必要な部分は何回か縫い合わせたり、強度の強い太い糸を用いて手縫いにしたりなど、工夫を凝らされていました。設計上、力のかかる部分はこのような工夫を行なっています。
縫い合わせた後、糸と革をなじませるために塗った部分をハンマーで叩いて慣らしていきます。これもやはり、足馴染みや強度に関わる作業。こうすることで、5〜10年先の靴の状態が変わり、長く履ける靴になるそう。
「こう言った細かな作業はお客さんには見えません。短いスパンでの靴の仕上がりにも影響は少ないです。でもこれをするのとしないのでは、10年先の靴の状態が大きく変わってきます。お客さんに永く使用してもらうためには欠かすことができないと僕らは思ってます。」と久保さん。
縫い合わせた後、端の余分な革を削ります。削りすぎると廃棄の上、最初からになるのですが、丁寧に、それでもスイスイと削っていきます。
その後は革包丁という器具で、掬い縫い用の糸を通すための溝を掘っていきます。内側の部分だけきれいに削り取っていきます。
こちらも削りすぎたり、貫通してしまうと破棄しないといけないそうですが、正確丁寧にすごいスピードで削っていきます。
3日間の工程のうち、初日はここまででした。かなりゆっくり進めていただいている中、それでもかなりの作業量です。
この後引き続き2日目3日目と、元々は平面の、二次元だった革が三次元に変わっていく様子が見えて、とても面白く見させていただきました。
この記事が気に入ったらサポートをしてみませんか?