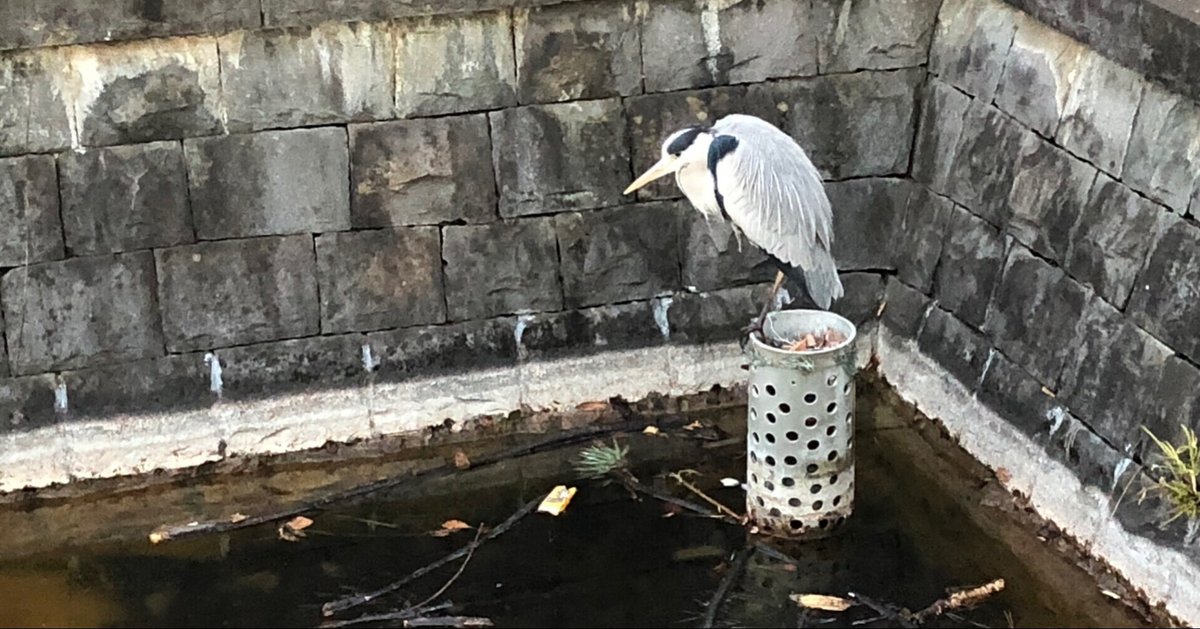
待ち工場になっていませんか?
こんにちはコスモブレインズの宮本です(@eijimiyamoto01)。生産財業界でマーケティングコンサルタントをしています。あまり感じの良くないタイトルですみません。この記事はコツコツと品質向上に取り組む製造業の人に読んで欲しくて書きました。
共感とともに尊敬できることが多い日本のものづくり。でも、好きだからこそ、このままではいけないと感じています。今は令和の時代。物を作れば売れていた時代を知る人はいなくなりつつあります。バブル景気すら知らない人が会社を引っ張る時代です。昔の成功体験は通じません。「いいものを作れば売れる」はもはやファンタジーなのです。今はそういう時代ではありません。QCDが良くても知ってもらえなければ、存在しないと同じなのです。
技術偏重の弊害
たしかに技術力は製造業の競争力の源泉です。しかし、「技術力」一本で勝負できるのは一部のオンリーワン企業だけにできること。日本中すべての製造業がオンリーワンを目指すなんて非現実的だし、そうする必要もありません。「技術」「販売」「サービス」をバランスよく総合力で勝負してもいいのです。製造業でも「サービス」や「営業」を強化し成長する中小製造業も増えつつありますが、まだまだ全体的に見ると技術偏重の体質は変わっていません。製造業ではQCDに磨きをかけ競争力を高めています。製造ラインの課題を見つけ改善を進めるのです。しかし、原価率を下げて利益に貢献することはありますが、それだけで売上がアップするとは限りません。今、製造業に必要なのは製品を売ることです。実際、2020年の中小企業の倒産原因の73.70%が販売不振であることからもそのことが窺えます。
2020年の中小企業の倒産原因の73.70%(中小企業庁「倒産の状況」より引用)
「技術」「販売」「サービス」これらの総合力が求められるのです。自社のボトルネックがどこにあるのか?見極め手を打つことが大切です。
技術:9点(10点満点)
営業:1点(10点満点)
サービス:5点(10点満点)
もしあなたの工場が上のスコアだとしたら・・・技術で10点満点を目指すより、営業を伸ばしたほうがインパクトは大きいですよね。だから、工場内だけでなくビジネス全体を通した現状把握が大切です。全体のボトルネックはどこか?それをつかんだ上で改善ポイントを絞りこむべきです。改善ポイントは工場内だけに留まりません。慣れ親しんだ改善手法でQCDに磨きをかけるだけではなく、幅広く現状を把握して最も効果的な改善ポイントを見つけることが大切です。
全体を俯瞰して最適化する
TOC(制約条件の理論)は製造にかかわる人には有名な理論です。一般的にはTOCは生産管理の手法として理解されています。製造工程の中でもっとも生産能力の低い(遅い)工程のスピードでしかものづくりは出来ないことに注目し、生産性向上に活用されます。制約条件=ボトルネックといわれます。大きく分けるとその方法は2つです。
●ボトルネックの生産能力を高める: もっとも遅い工程の速さでしか物はつくれません。だからボトルネックの工程改善によって工場全体の生産能力を引き上げます。
●ボトルネックのスピードに合わせてものをつくる: ボトルネックの工程の速さにあわせて物をつくることで、中間在庫を削減し作りすぎの無駄をなくします。
工場が最適化を実現できても、それは部分最適です。販売がボトルネックだったり、宣伝がボトルネックでは「作りすぎのムダ」につながります。また生産が追いつかないときに宣伝しても意味がありません。営業が足りないときに宣伝して引き合いを増やしても、かえって信頼を損ねることになりかねません。宣伝がボトルネックのときが最も宣伝効果が高いのです。工場の中だけで改善してもそれは部分最適。コツコツQCDを磨いても効果は限定的かもしれません。
ボトルネックは販売力じゃないですか?
なんだか回りくどくなりました。日本の製造業は販売力を高めればいいのです。お客様に働きかけて需要を創るには、行動することが大切です。自社の製品を見てもらう。技術を説明する。 どうしたら売れるのか?上手くいくまで何度も繰り返します。まるで品質などの改善活動のように・・・ものづくりにかける情熱と同じようにあなたの技術や製品を伝えることにも情熱を注いで欲しいと思います。
QCDが良くても知ってもらえなければ、存在しないと同じなのです。販売力を高める第一歩はユーザーに自社の技術や製品を知ってもらうこと。1日も早く取り組んで欲しいなと思います。
この記事が気に入ったらサポートをしてみませんか?