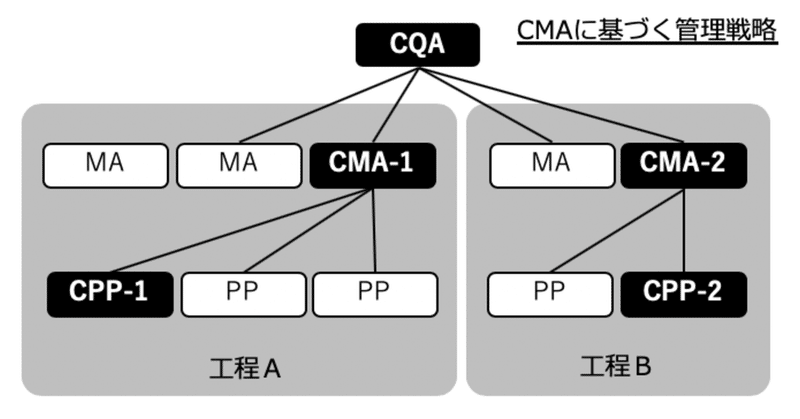
データ解析視点で見た医薬品連続生産の管理戦略
最終製品の品質を確実に保証しなければならないという点で,バッチ生産と連続生産との間に違いはないが,生産方法が異なるため,バッチ生産で実績のある管理戦略をそのまま連続生産に適用できるわけではない.
連続生産の特徴は,その名の通り,原料を連続的に製造プロセスに供給し,中間製品を工程間で貯蔵することなく連続的に次工程に移送し,最終製品も連続的に取り出すことである.このため,ロットごとに中間製品の特性テストを行い,合格したものを次工程に送るという,バッチ生産で実績のあるQuality by Testing (QbT)は,連続生産プロセスの有効な管理方法とはなりにくい.それよりも,近年採用が進んでいるQuality by Design (QbD)が有効な管理方法になると考えられる.つまり,製剤の重要品質特性(CQA: Critical Quality Attribute)への影響が大きい物質特性(MA: Material Attribute)や工程パラメータ(PP: Process Parameter)を管理する方法が有効であると考えられる.
医薬品のバッチ生産におけるQbDについては,ICH Q8/Q9/Q10としてガイドラインが示されている.連続生産を対象としたガイドラインについては,ICH Q13の策定に向けた活動が進められている.このような流れを踏まえて,データ解析技術の視点から,連続生産プロセスの管理戦略構築についてまとめたのが下図(2020.6.24改訂)である.
制御のためのプロセスモデル構築
原料特性や製造環境が変動した場合,それらが外乱として中間製品や最終製品の特性に影響を与える恐れがあるが,CMAを事前に決めた値(設定値)に固定することで,外乱の影響を抑制することができる.
CMAを制御するためには,CMAと強い関係のあるCPPを特定した上で,CPPを変化させたときにCMAがどのように応答するかを把握する必要がある.推奨されるのは,CPPを入力(操作変数),CMAを出力(制御変数)とするプロセスの動的モデルを構築することである.
プロセスモデルを構築できれば,それを用いて,フィードバック制御系やフィードフォワード制御系を設計できる.制御対象の動特性が単純であれば,古典的なPID制御で十分な制御性能が実現できると期待される.一方,干渉が強い場合や,むだ時間が長い場合には,モデル予測制御などより高度な制御方法の採用が望まれる.
仮想計測・ソフトセンサー
CMAのフィードバック制御を実現するためには,CMAをリアルタイム測定することが望ましい.このため,バッチ生産と同様,Process Analytical Technology (PAT)が重要な役割を果たす.例えば,近赤外分光スペクトルを測定し,それを入力変数,CMAを出力変数として統計モデルを構築する.ほとんどの場合,モデル構築にはPartial Least Squares (PLS)が用いられるが,Just-In-Time型モデルの一種である局所PLSを用いることで,推定性能を大幅に向上できることが報告されている.
CMAをリアルタイムに推定する方法としては,PATの他に,仮想計測(ソフトセンサー)が有用である.仮想計測とは,リアルタイム測定が困難な変数を,リアルタイム測定が容易な変数から推定する技術である.医薬品連続生産においては,リアルタイム測定が困難なCQA/CMAを,リアルタイム測定が容易なMA/PPから推定する仮想計測は有用であると考えられる.
デザインスペースの設計
QbDアプローチを採用して,最終製品の品質を保証する場合,CQAへの影響が大きいCMA/CPPを管理することになる.このとき,要求されるCQAを確実に実現することができるCMA/CPPの範囲を明確化するために,デザインスペースが有用と考えられる.
デザインスペースの構築には,応答曲面法が使われることが多い.特に,その簡便さから二次多項式の応答曲面が多用されるが,単純なモデルであるが故に,実際の変数間の複雑な関係を正確にモデル化できない恐れがある.加えて,入力変数の数が多い場合には適さない.応答曲面の精度が低下すると,デザインスペースの信頼性も損なわれるため,適切なモデル構築方法を採用すると共に,予測値の信頼性も評価することが望ましい.
さらに,デザインスペースは非常に保守的に設計されることが多い.それぞれのCMAに独立に上下限を設定できて,その上下限内にCMAを維持している限りCQAを保証できるという「わかりやすいさ」を重視するためである.しかし,デザインスペース内でCMAを柔軟に設定することによってCQAを保証しようとするとき,保守的なデザインスペースを採用すれば,みずから柔軟性を制約することになり,本来なら対応できたはずの外乱に対応できなくなるというデメリットがある.今後は,モデル構築にも制御にもより高度な手法を用いることを前提に,製造プロセスの能力を最大限に活用できるデザインスペースを設計するのがよいだろう.
プロセス監視・異常検出
生産プロセスに何かしらの予期しない変化が生じていないかを確認することも有用であろう.例えば,CMAを仮想計測によって監視する場合,そのモデルの入力変数の変化はCMA推定値に反映されるが,入力変数ではないMA/PPが変動してもCMA推定値には影響を及ぼさない.入力変数ではないMA/PPの変動が小さければ恐らく問題はないが,変動が大きくなればCMAがその影響で変化することも考えられる.また,CQA/CMAには直接関係しなくても,装置の異変を早期に検出したいという要望が生産現場にあるかもしれない.そのような場合に,CMAのみならず,MA/PPを監視することが有用となる.
古典的な管理図の弱点を克服し,変数間の関係をモデル化した上で異常検出を行う方法として,多変量統計的プロセス管理(MSPC: Multivariate Statistical Process Control)が知られている.1990年代以降,連続生産プロセスおよびバッチ生産プロセスの双方において,MSPCは様々な産業で活用されている.ただ,主成分分析を用いるMSPCは変数間の線形な関係しかモデル化できないため,非線形性が強いプロセスに対しては別の方法を採用する必要がある.
簡単なまとめ
連続生産プロセスで製造された医薬品が国内外の規制当局によって承認されるようになり,連続生産への関心が高まっている.既にバッチ生産で医薬品の品質管理を実施してきたのであれば,多くの技術は連続生産にも適用できる.QbDアプローチ,デザインスペース,PATなどがそうである.一方,バッチ生産プロセスにはない連続生産プロセスの特徴も存在する.連続生産プロセスの管理戦略を構築し,実装するためには,そのような特徴を把握した上で,適切なアプローチを採用する必要がある.
© 2020 Manabu KANO.
この記事が気に入ったらサポートをしてみませんか?