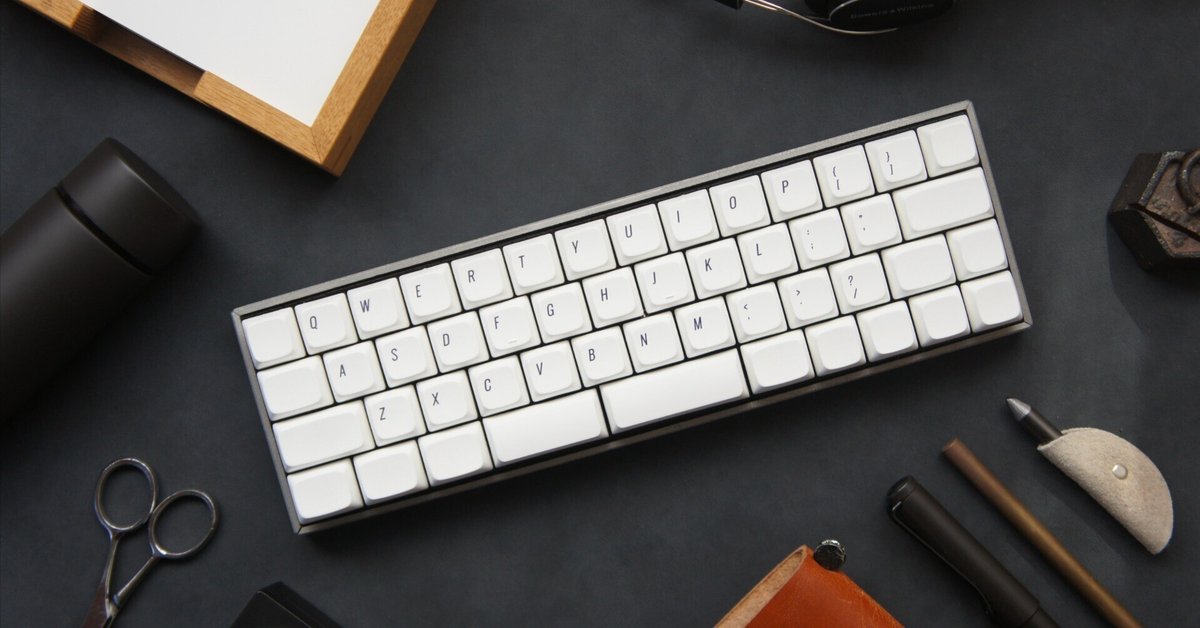
金属3Dプリントでケースを作ったら渋い自作キーボードが生まれた
(追記1) 前回記事から左側のモディファイアキーを整理した配列の画像を追加
これまでに50キー・50%サイズの自作キーボード「inn(アイエヌエヌ)」についての記事を2つ投稿しました。
今回は2つ目の記事の最後でも予告していた通り、金属3Dプリントによるケース製作についての顛末をまとめています。PCBの形状も変更を行いましたので、その際に発生した発注時の注意点にも触れていきます。
なお記事中に出てくる写真に関して、作業の都合上さまざまな時間帯に撮影しています。そのため色味等安定しておりません、その点ご容赦ください。
※ この記事で発注・製作したPCB等はJLCPCBさんに提供頂いております。新規ユーザー向けに、PCB・PCBA・3Dプリントで利用できるクーポン$54分が配布されていますので利用を考えている方はリンク先より入手してください。
ケースデザインについて
こちらが今回金属3Dプリントで制作するケースのデザインとなります。
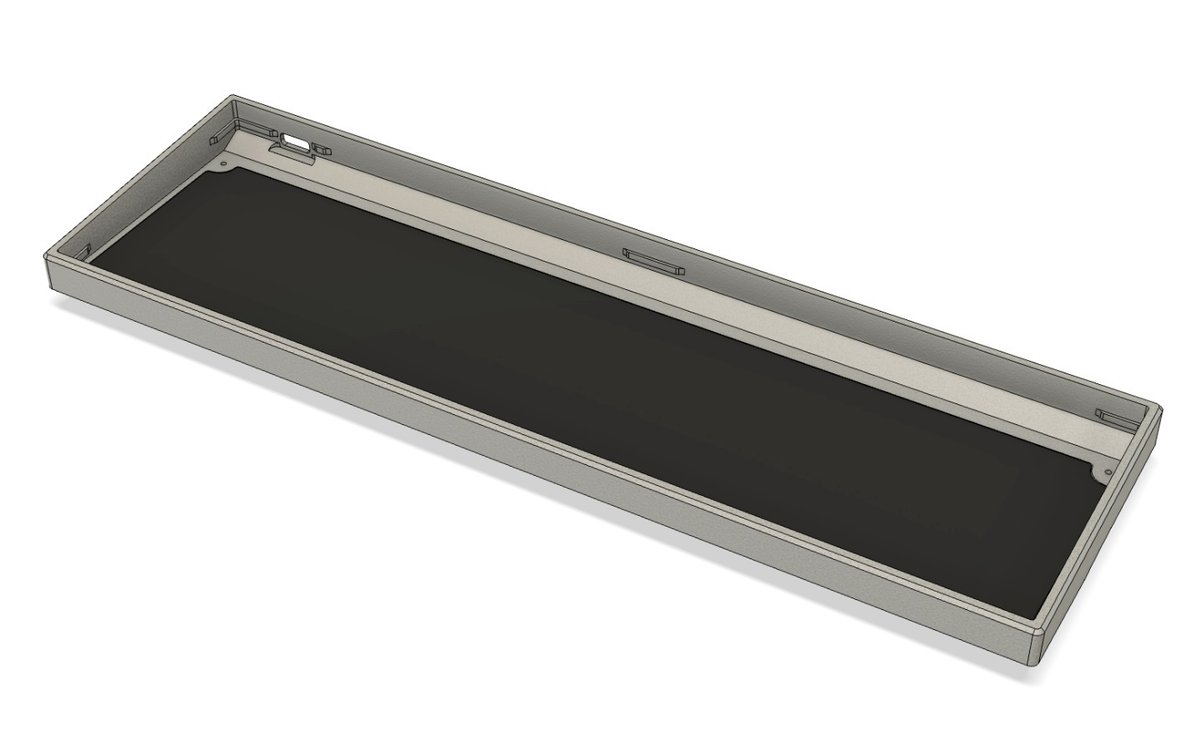
前回レジンで作ったケースはベゼル幅の太さが個人的に気になってしまったので、今回はなるべくベゼルが細くスリムな見た目となるようにしています。加えてキーボード全体の高さを抑えるためにマウント方式を変更しています。結果的に上下分割ケースではなくボトムのみの一体型形状となりました。
以前の記事でも書いていますが、最終的にはアルミ切削によるケースの製造が目標なので切削可能な形状を意識してデザインしています。ただ3Dプリントは出力物の体積で料金が変わるので、機能的に問題ない部分は削ったりして発注データの形状を調整しています。
さらに今回は予算の都合もあり、底面部分を開放しFR-4(ガラスエポキシ。基板で使用しする素材)で蓋をする方式を採用しています。底面を出力すると料金が倍以上になりますので思い切ってこの部分を削りました。このフレーム形状への変更が後々問題となるのですが、それは後述します。
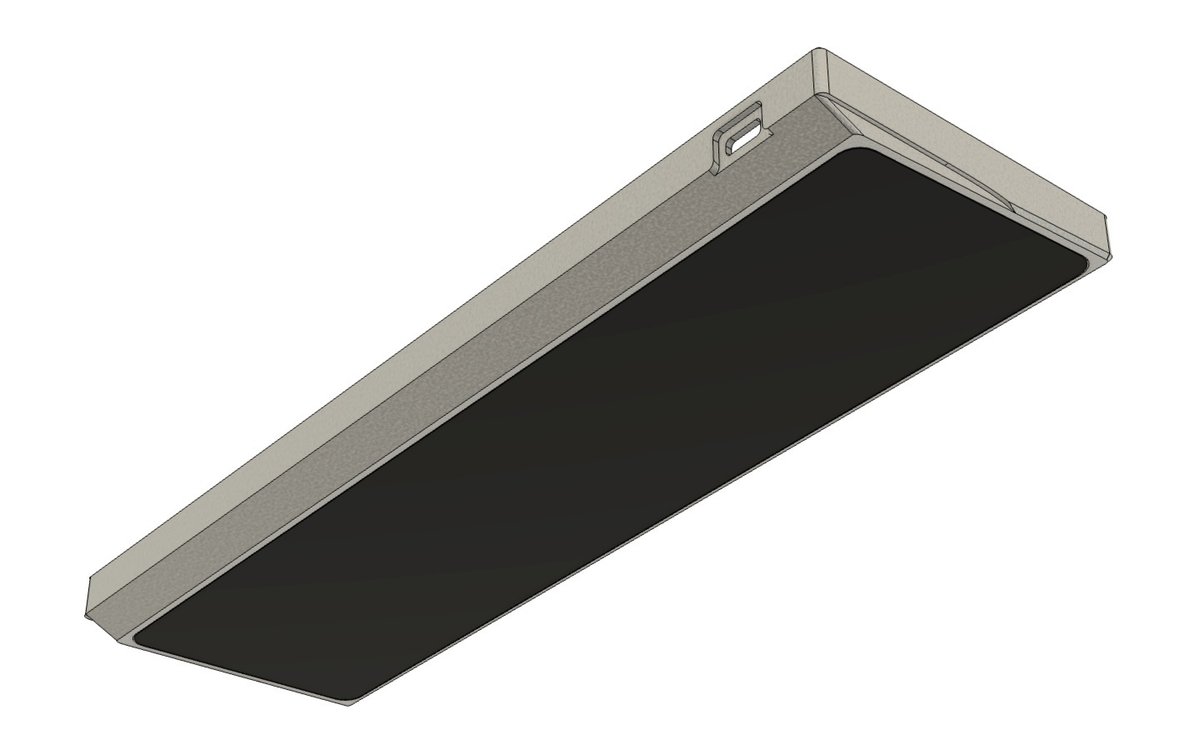
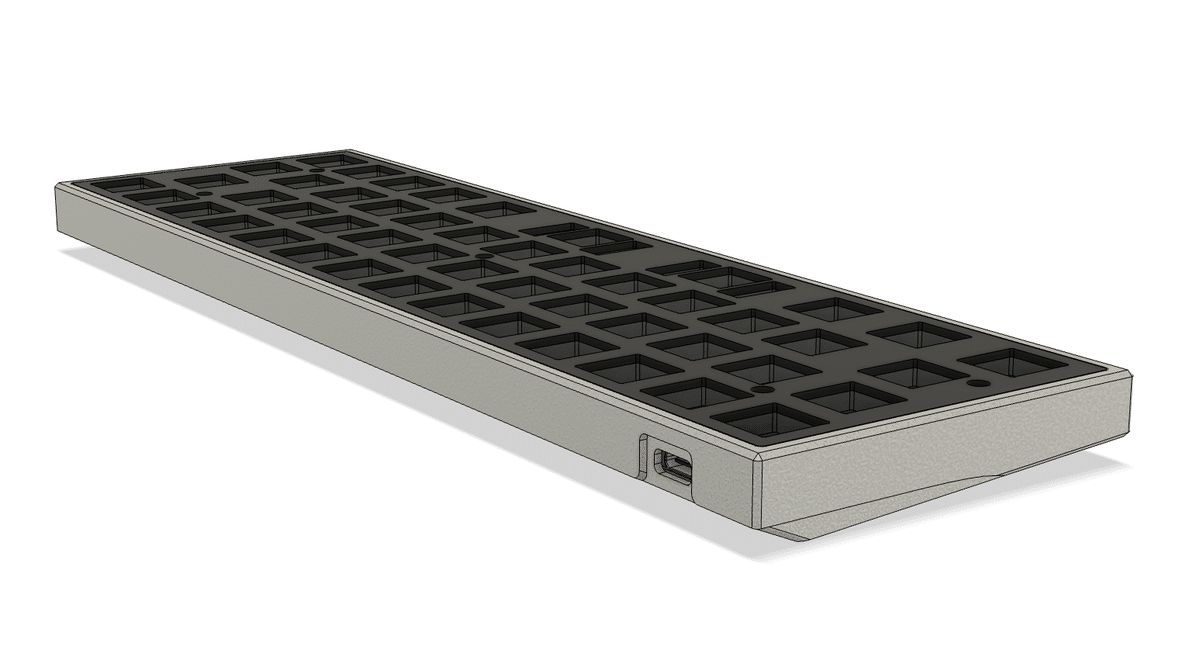
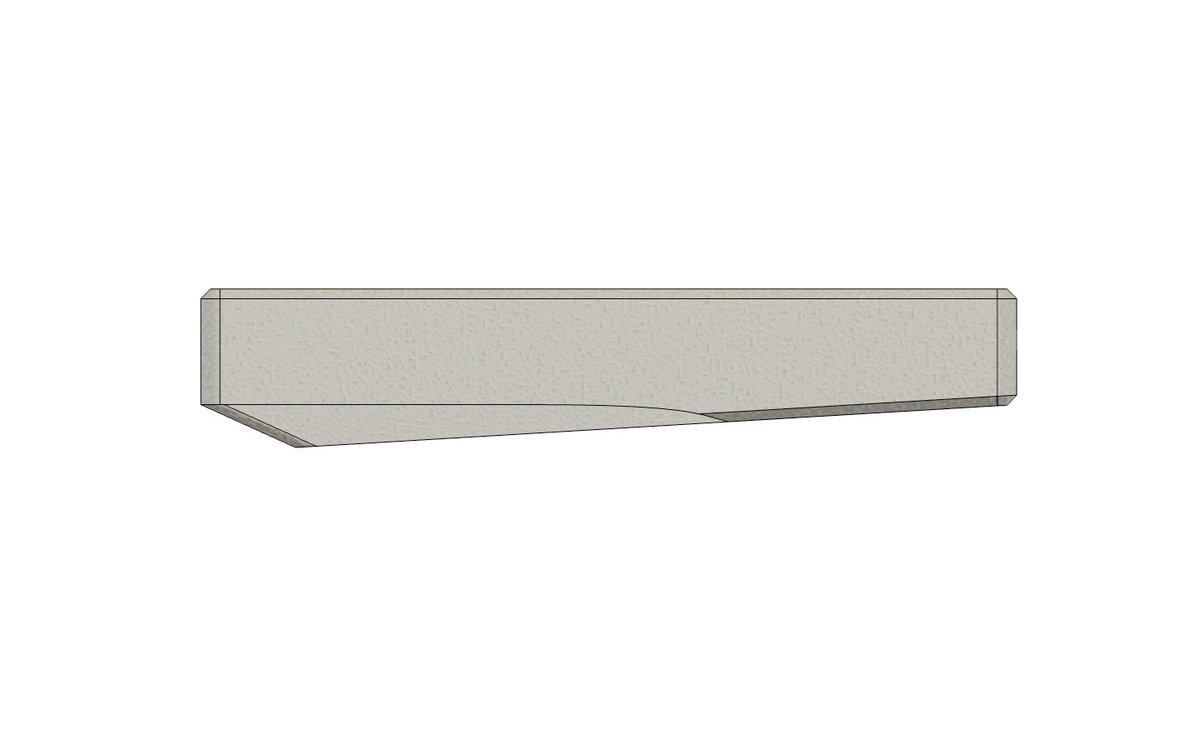
マウント方式の変更に伴う基板の設計変更
以前のレジン製ケースはウレタンフォームと上下に分割したケースでFR-4製スイッチプレートを挟んで固定するガスケットマウントを採用していました。
そのためスイッチプレートの外形に「耳」がついておりましたが、今回はマウント方式をOリングマウントのような固定方式に変更したため、挟み込むための耳部分は不要となります。
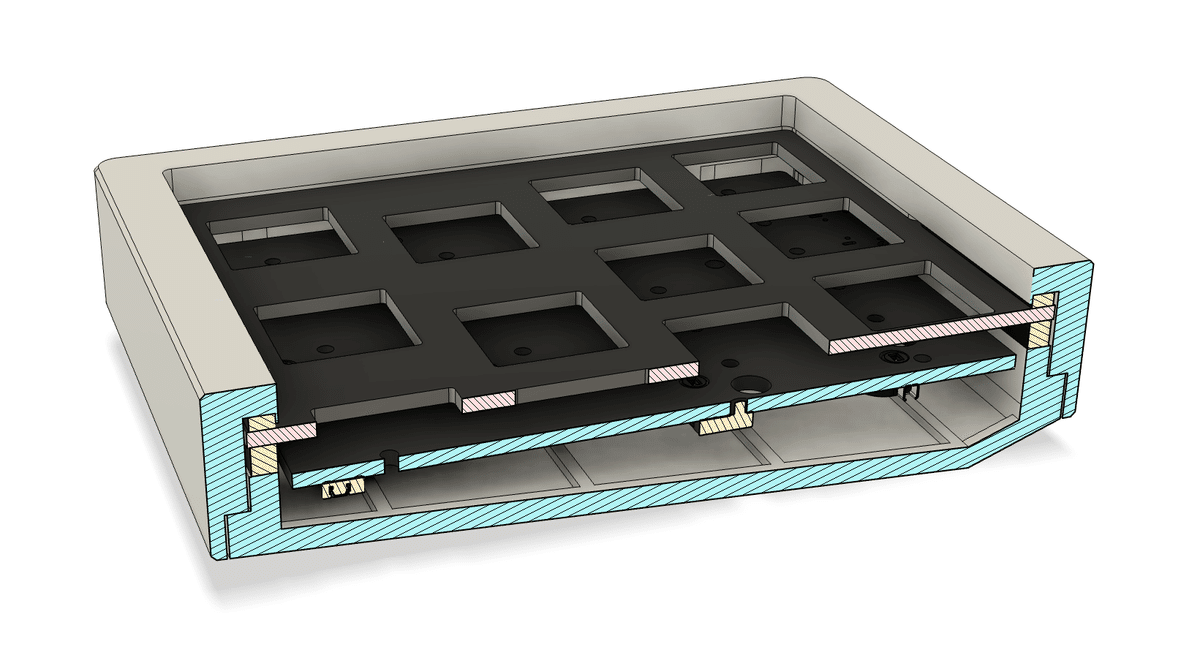
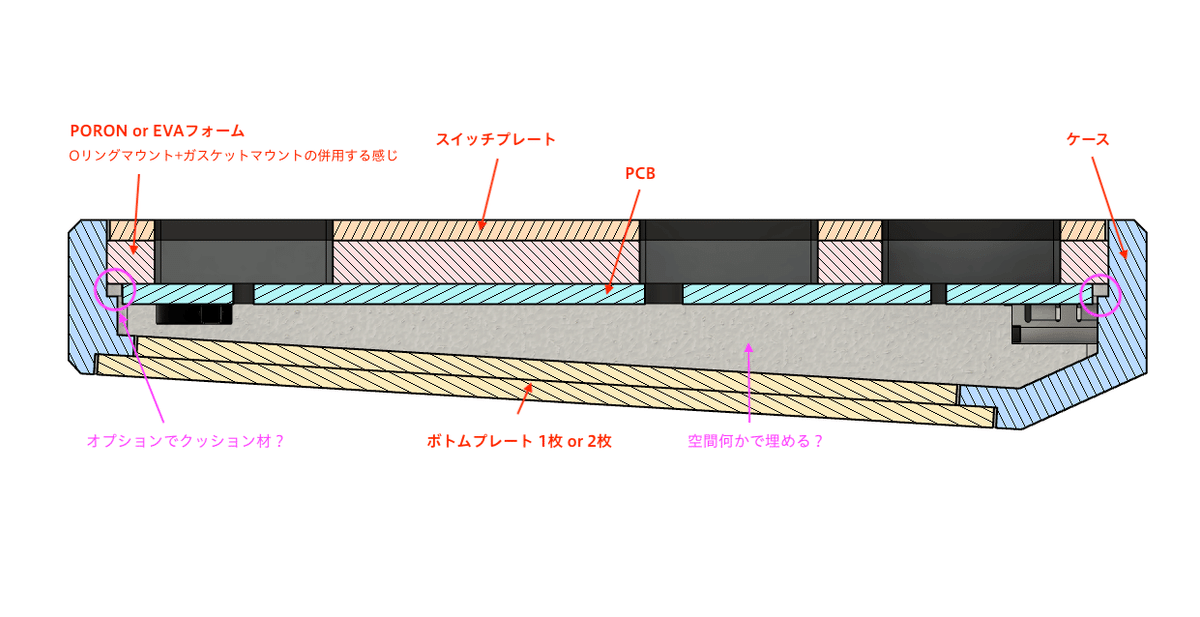
スイッチプレートの耳が不要になったことによる形状変更に関してはPCBを再発注せず、前回発注したFR-4製スイッチプレートをカッターで切断、断面をヤスリで整えることで対応します。
実は最初の発注をした時点で、幾つかのマウント方式を試せるようにネジ穴等も含めて形状を決めていたので、今回はそれが生きた形です。
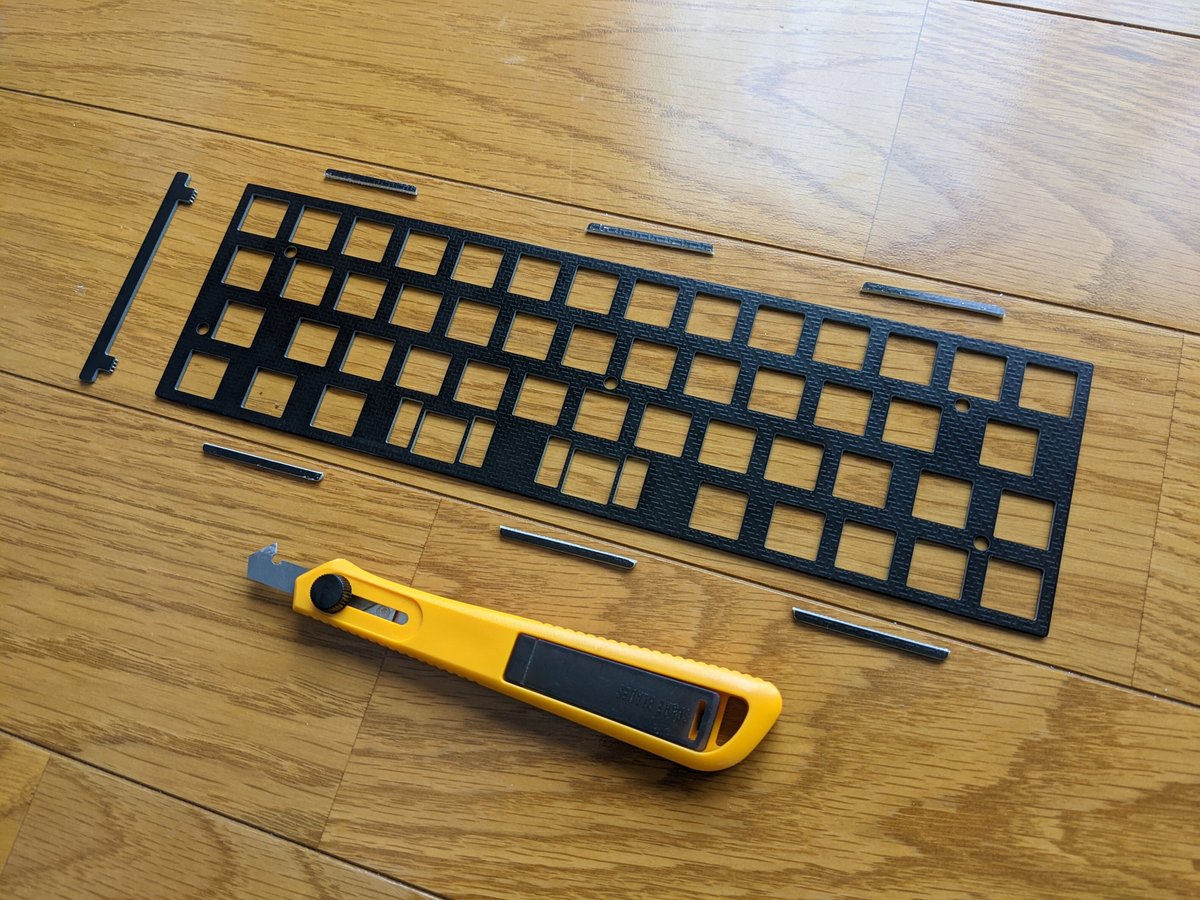
本体のPCBにも形状変更があります。以前のケースはベゼルにある程度厚みがあったため、PCBはUSBコネクター部分を凸状に飛び出させていました。
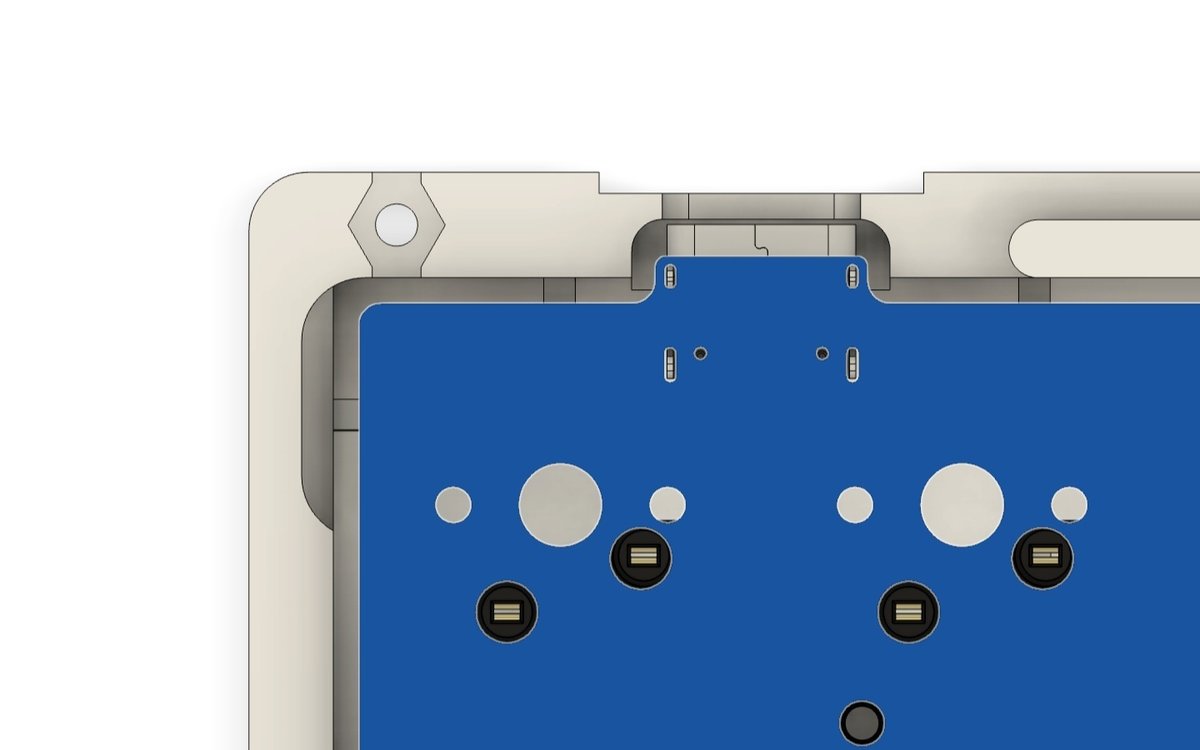
今回はベゼルが薄く、なおかつケース上部からPCBを挿入するのでこの凸状の形状をなくす必要があります。
※ 出っ張りがあるとケース上部から挿入する際に干渉する & ケース内側の形状を凹ませる必要がある。
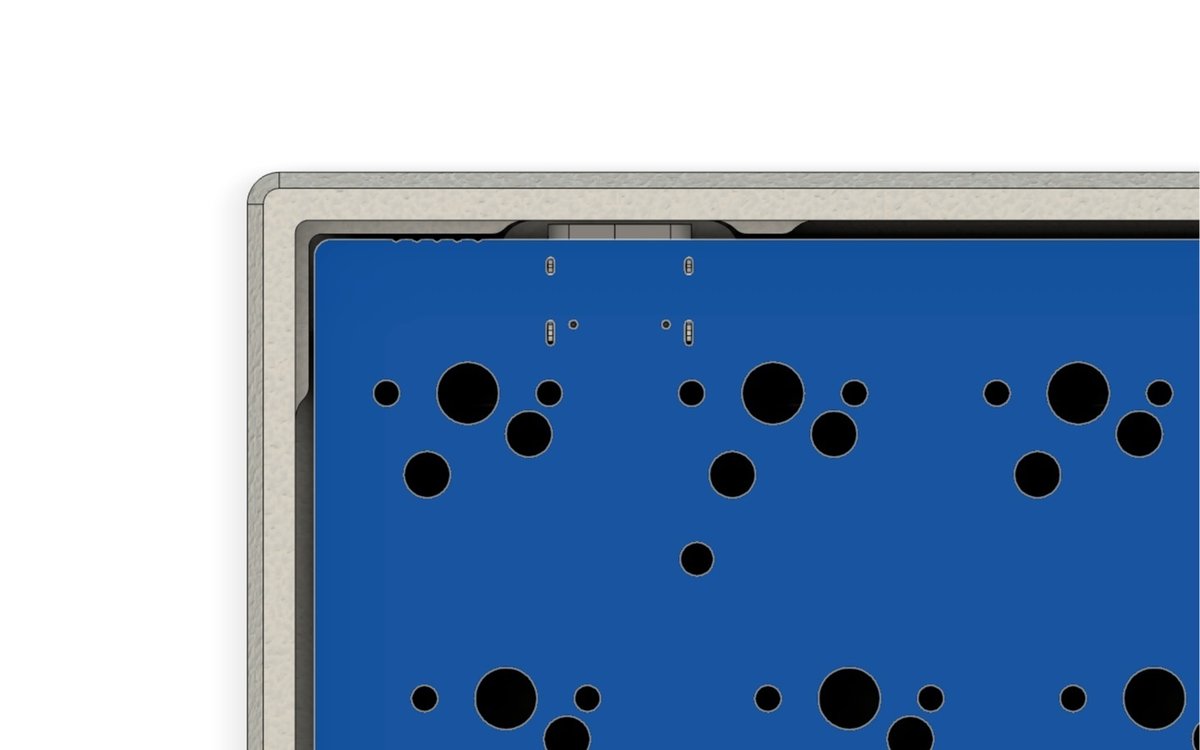
MCUをATmega32U-MUへ変更
今回のケース形状変更とは直接関係ないのですが、MCUをATmega32U-AUからATmega32U-MUに変更しました。機能としてはATmega32U-AUとATmega32U-MUは同等の部品なのですが、次のような特徴の差があります。
MU(7mm*7mm)はAU(10mm*10mm)に比べ部品サイズが小さい
MUははんだ用の足が出ていないので手ではんだ付けするのは困難
JLCPCBのPCBAサービスにおける部品単価がAUに比べて圧倒的に安い 。一つあたりAU: 約$20、MU: 約$4(注文時の価格で時期により変動する)
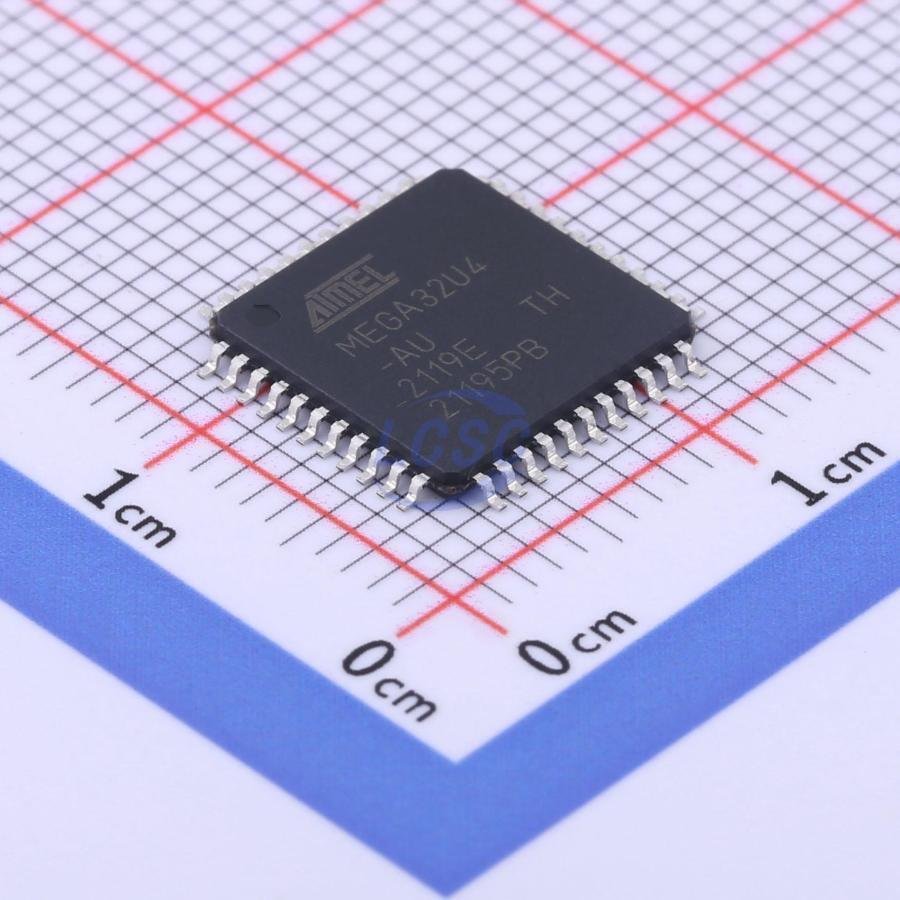
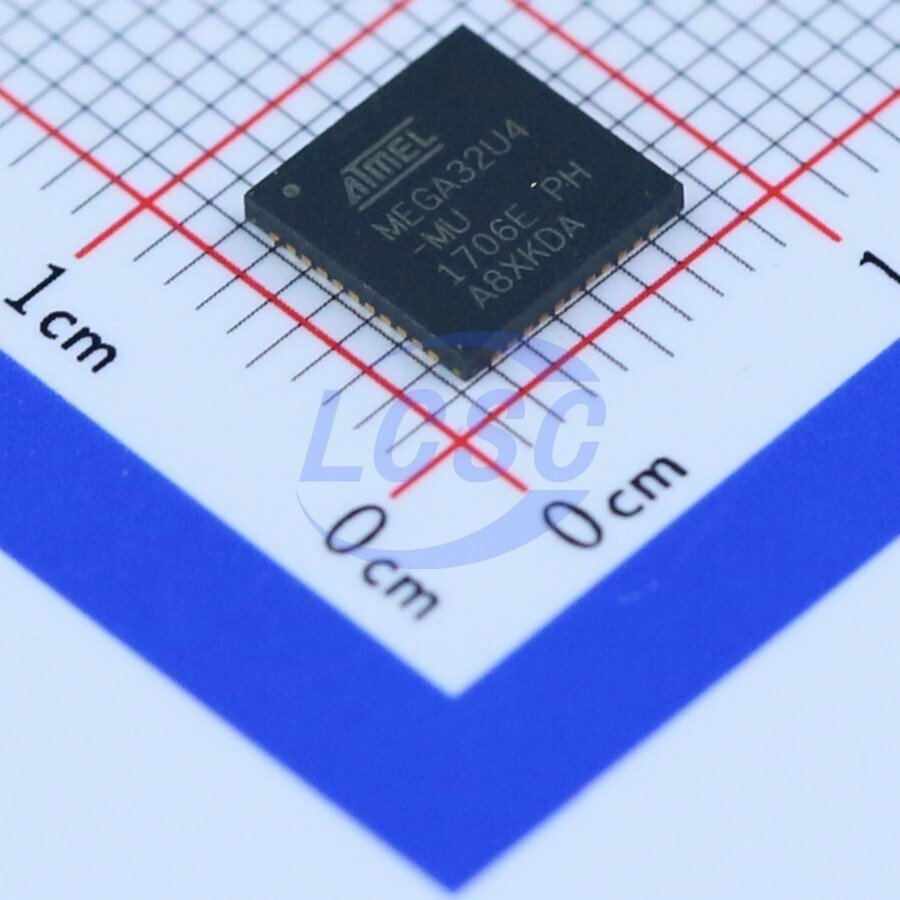
実は最初の基板発注でもATmega32U-MUでPCBAによる発注・実装を予定していたのですが、注文時にJLCPCB側でちょうど在庫切れとなってしまったので、急遽設計データを変更しATmega32U-AUを自分ではんだ付ける方針に変更しました。再発注にあたって在庫が復活していたので再度設計をデータを元に戻した次第です。
基板発注時の注意点
今回の発注では基板の装飾を試してみたのですがJLCPCBの発注画面でガーバーデータをアップしたところ、右側の面(裏面)の黒いレジストが消えた状態でプレビュー表示されて困惑しました。設計データの不備かと思い何度かデータを変更してアップしてみたのですが同じ現象が発生しました。
※ 画像左側の面(表面)の中心が円形上に黄色くなっているのは正しい状態です。
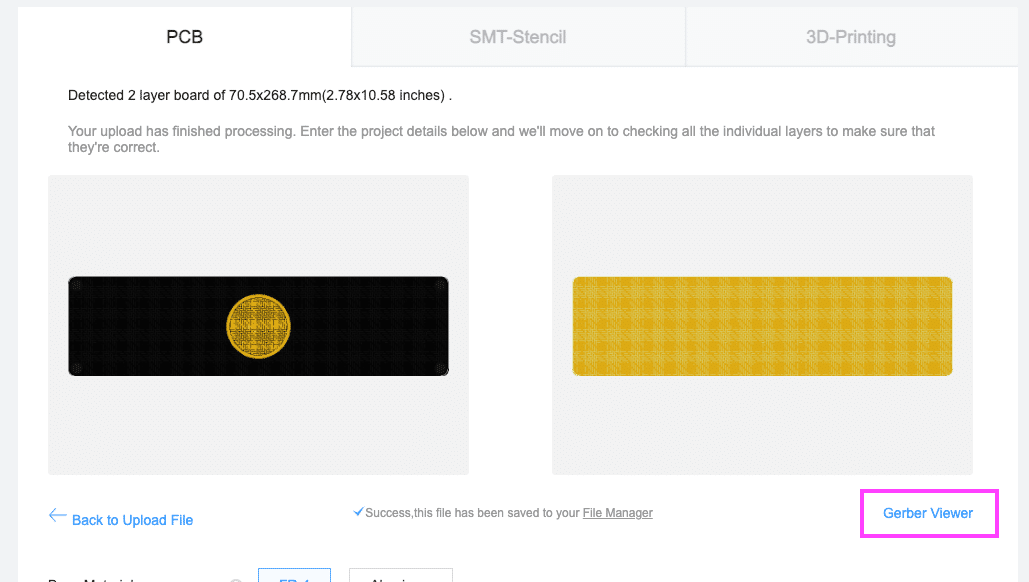
しかし、JLCPCBのGerber Viewerを開き確認してみると、レジストのレイヤーが非表示になっていることに気づきました。詳しい原因はわからないのですがCu(銅箔)レイヤーが細かい形状で全体に配置されているとこのような現象が起きました。
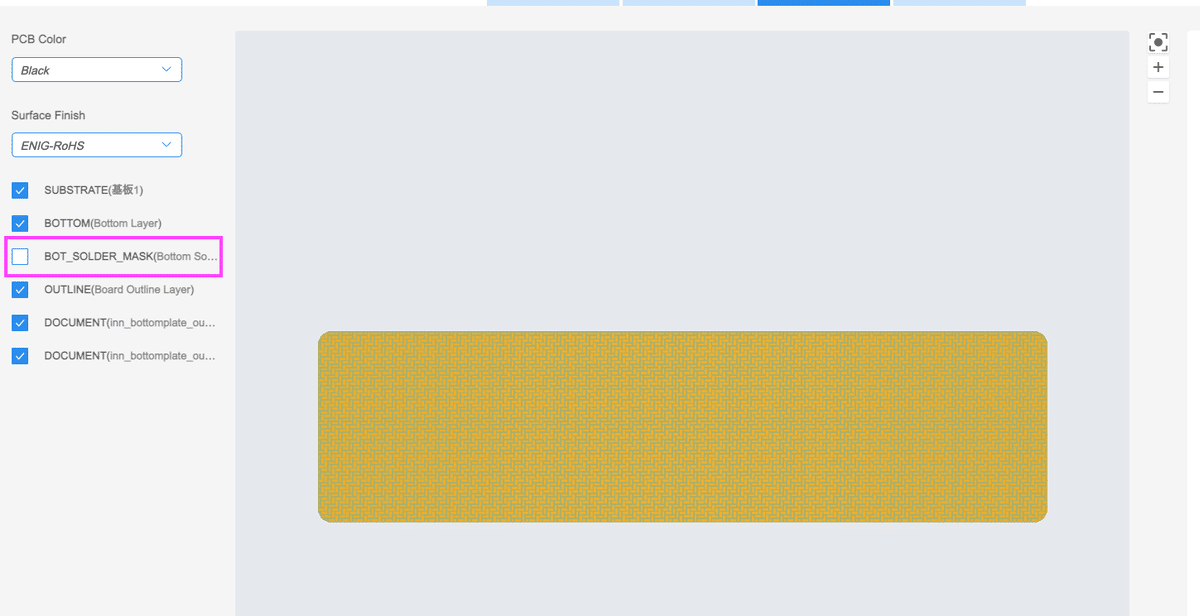
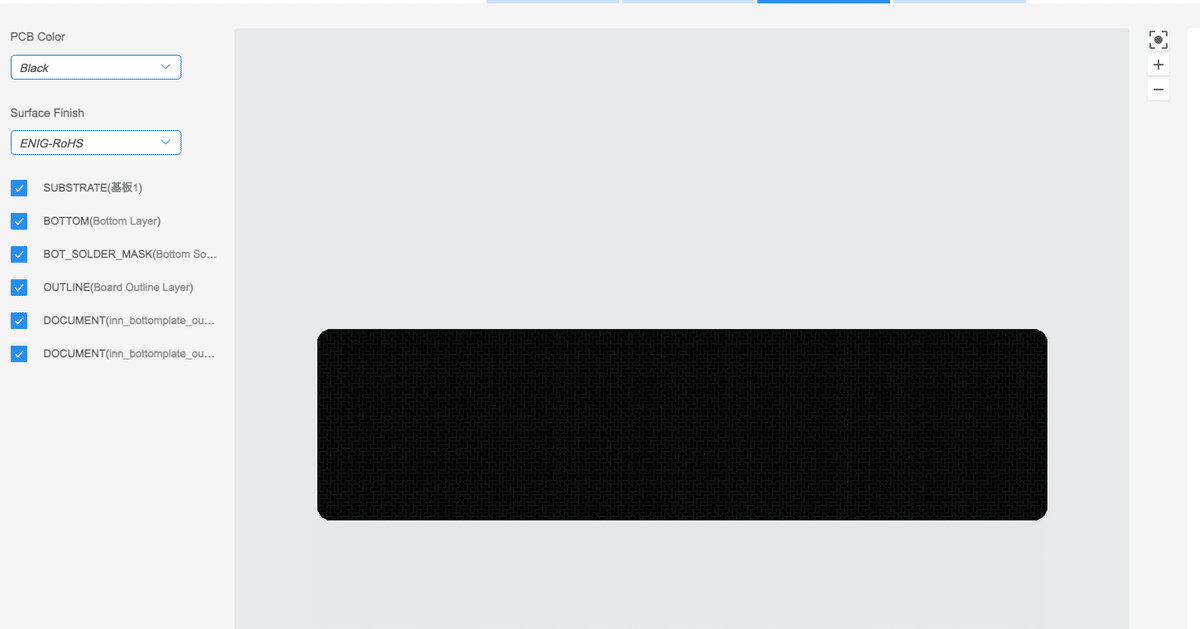
念のため、Gerber Viewer上でレイヤーの表示を有効化しておきます。発注画面のプレビュー画像はレイヤー表示を有効化しても変化がありませんでしたが、データ上は問題がないことが確認できたので、この状態で発注しました。
実物写真は後ほど載せますが、届いた基板は設計通りで問題はありませんでした。ただ発注データによってはプレビューが正しい(発注データが間違っている)こともあるので、どうしても解決できない場合や心配な場合は問い合わせてみるのが良いかもしれません。
金属3Dプリントの発注とデータの修正
さて本題のケースの金属3Dプリント発注です。
冒頭のデザインデータを3Dプリント用に最適化したものをアップ後、データ確認担当のエンジニアから出力物が歪む可能性があると連絡が来ました。レジン出力の時も同様の連絡があり、多少の歪みは許容範囲なのでこのままのデータで出力してくださいと返信をし生産手続きに入ってもらいました。
しかしその後、改めて工場のエンジニアからこのフレーム状の形状は大きく歪みが出ることが予想されるとの懸念を頂きました。この連絡で歪みが許容できるような程度のものではないと理解し、この時点で一旦オーダーをキャンセルさせていただきました。
歪みの原因に対する考察
エンジニア曰く底面部分が少なくフレーム形状になっているので、中心部分に向けて出力物が収縮する(または反対方向に広がる)ような歪みが懸念されるとのことでした。レーザーによってステンレス粉を溶かし固めるレーザー溶融法(SLM)は、高温部分と冷えた部分の温度差によって造形物が多少歪みます。光造形のレジン出力でも同様の懸念はありますが金属プリントの場合はレジンとは比べ物にならないぐらいレーザー照射による温度が高いので、形状が適切でないと歪みも大きくなってしまうのでしょう。
※ 形状が適切であれば大変精度の出る出力方式ではあります。
ここからは私の推測ですが許容以上の歪みが発生する原因としてもう一つ考えられるのが 、造形物の出力方向です。
JLCPCBの金属3Dプリンタは出力エリアが250x250x300mmです。今回のケースは長辺が250mmを超えているため、ステージに対する設置方向は次の2方向いずれかの向きでないといけません。
ケースの右 or 左側の側面を下にした縦置き状態
USBコネクタ(背面)側の長辺方向を下に、ステージに対して対角線上に接地
いずれの設置方法とも、ステージに対する設置面積が小さい上に底面の開放部分がフリーな状態で印刷することになります。結果的にこのことが歪みが大きくなる原因なのではと想像しています。おそらく中心に向けた収縮の他に捩れなんかも発生するかもしれません。
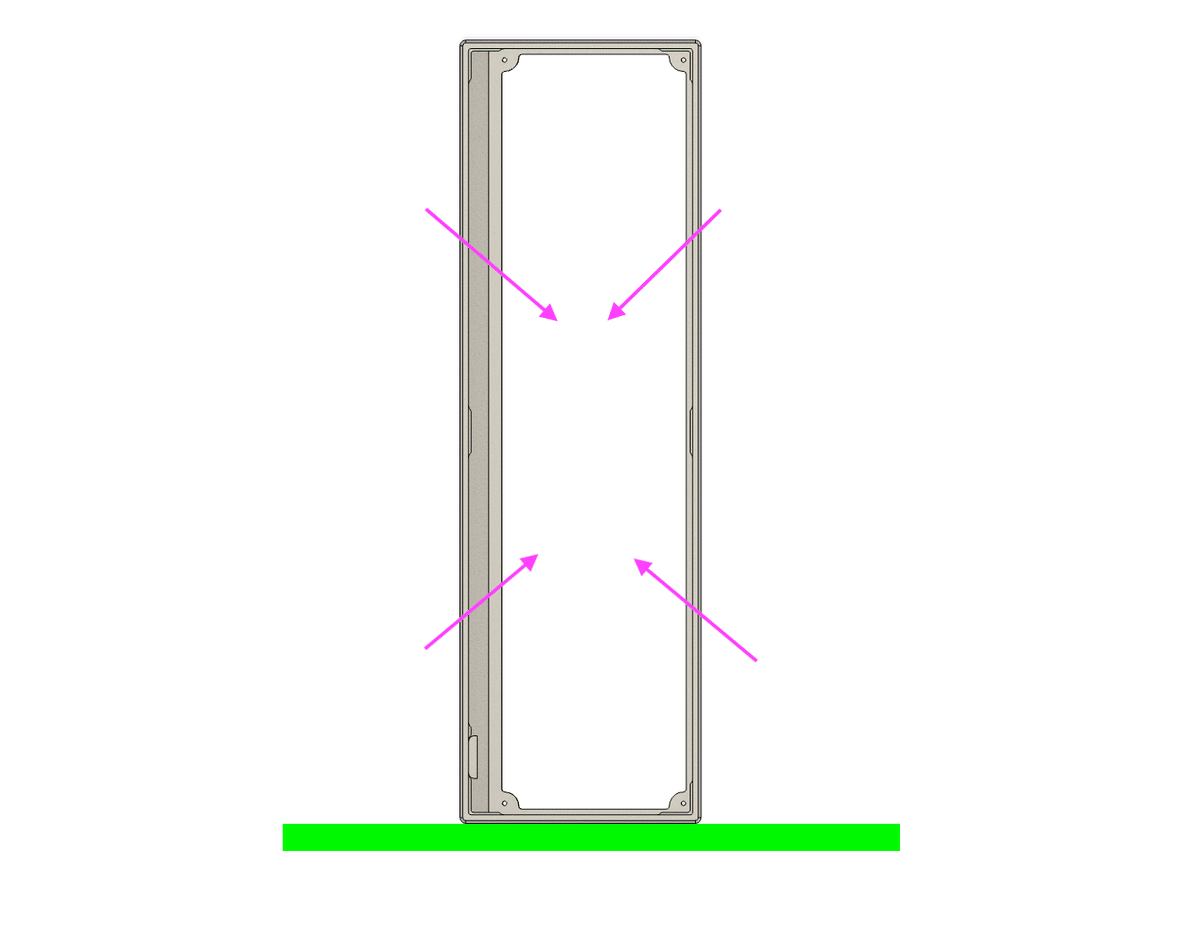
データを修正して対応
一番の解決策は適切な厚みをもった底面部分を除去することなく一緒に出力することですが、予算の都合でフレーム状にしているのでそれはできません。
最終的な解決策として額縁状の形状を4分割し、それぞれの辺ごとを一つのパーツとして出力するようにしました。各辺は届いてからネジ山を切って止めネジで組み合わせるようします。ちなみに料金はあくまで出力物の体積で計算されるので分割しようが変わりません。むしろネジの下穴分少し安くなりました。
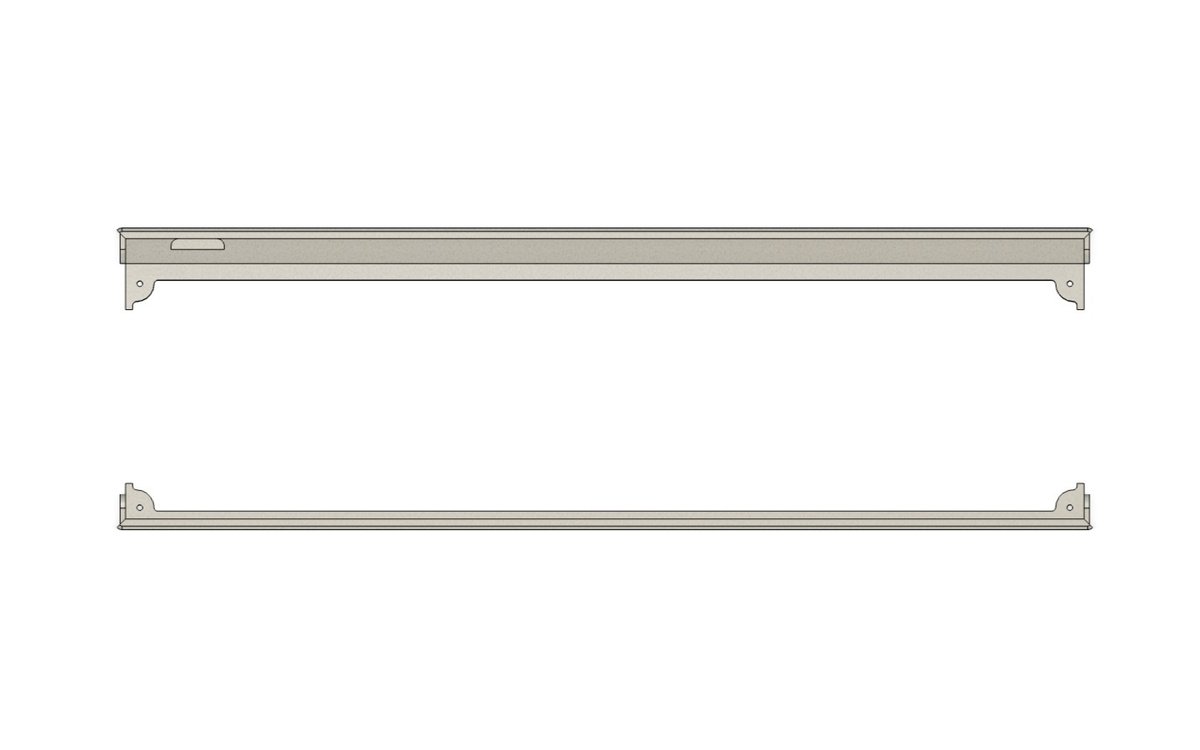
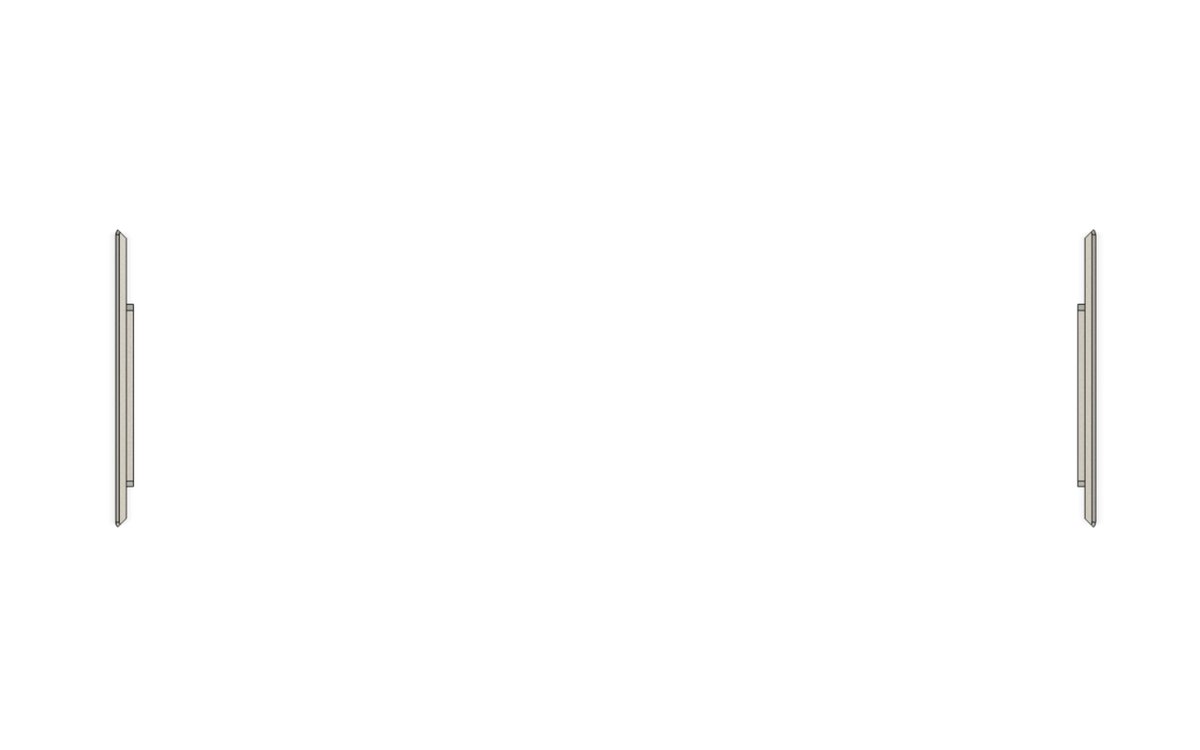
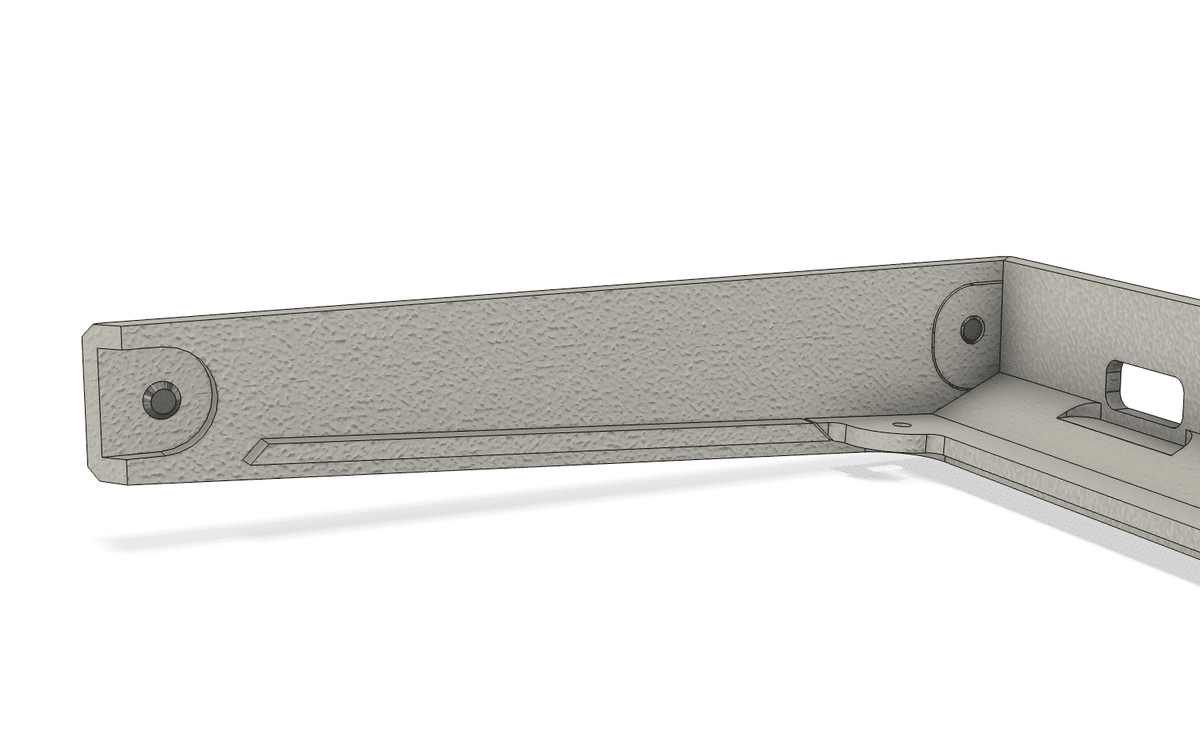
このように分割したデータを改めてアップしたところ、今度は特に問題なくデータが承認されました。画像中の警告マークは斜めに分割した部分が薄肉と判定されたことに起因するもので、懸念する箇所ではなかったのでそのままのデータで発注いたしました。
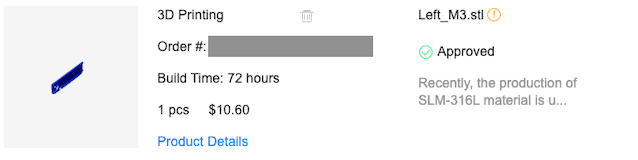
ちなみに1辺だけのパーツで出力すると造形時に歪む(反る)かもしれないと考え、念のため2辺をサポート材でつなげた次のようなデータをアップしていました。
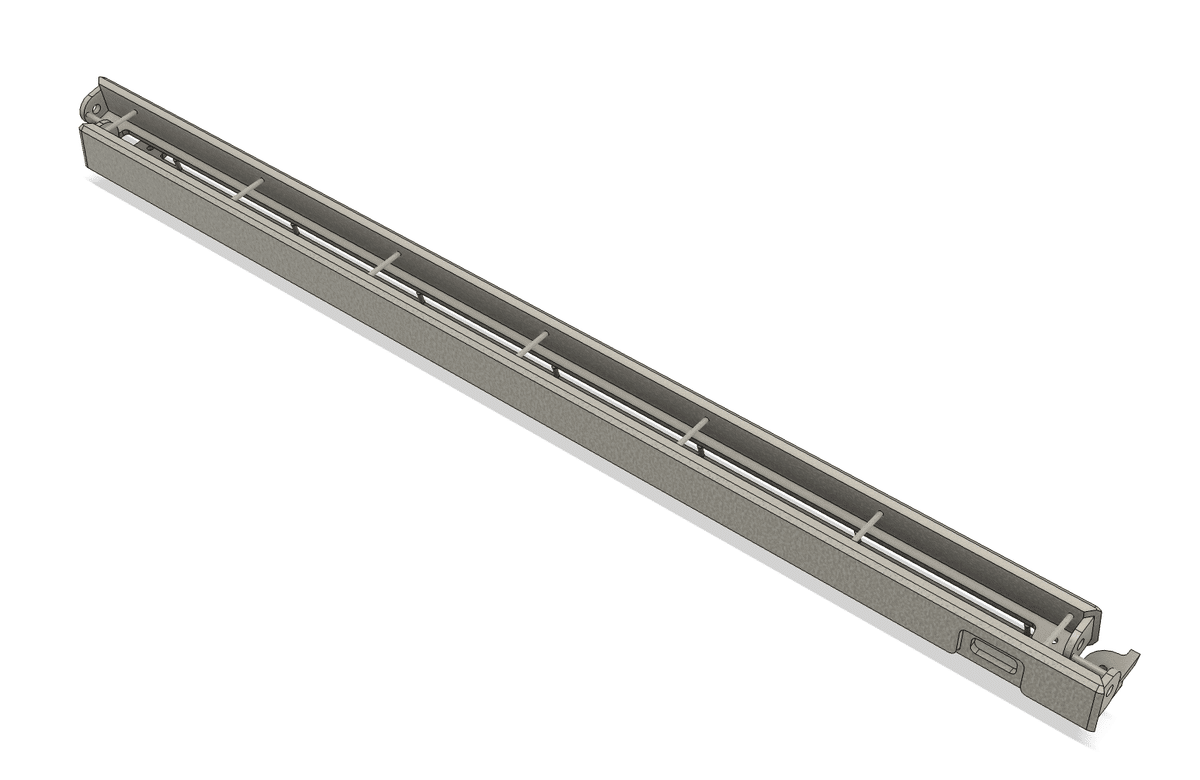
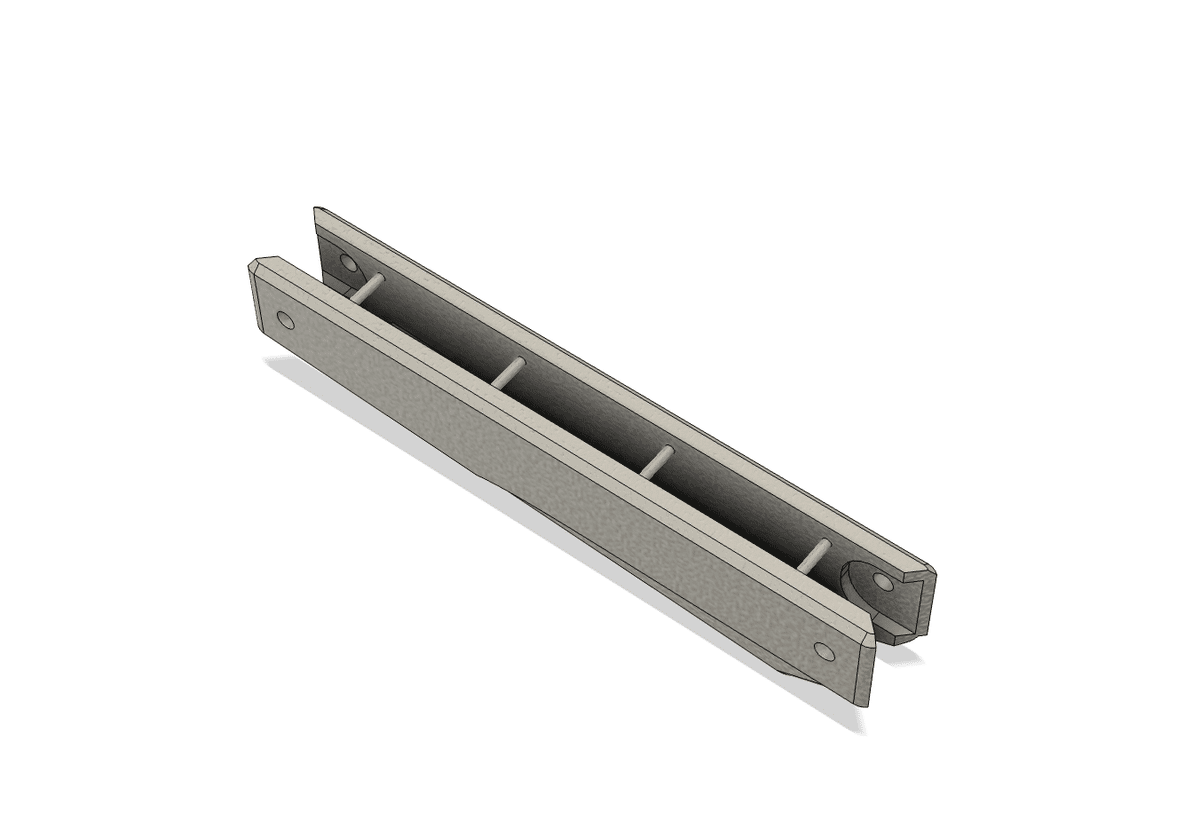
が、これらは製造審査に通りませんでした。
というのも、こちらのプリントガイドラインにもある通り金属プリントは複数パーツをサポート材等でつなげた状態でプリントすることは対応外とされているからです。事前にきちんと条件を確認しておきましょう…
Please kindly note: FDM with ABS material and SLM with 316L material are not supported in this way.
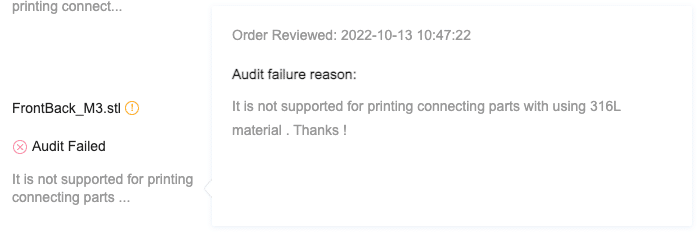
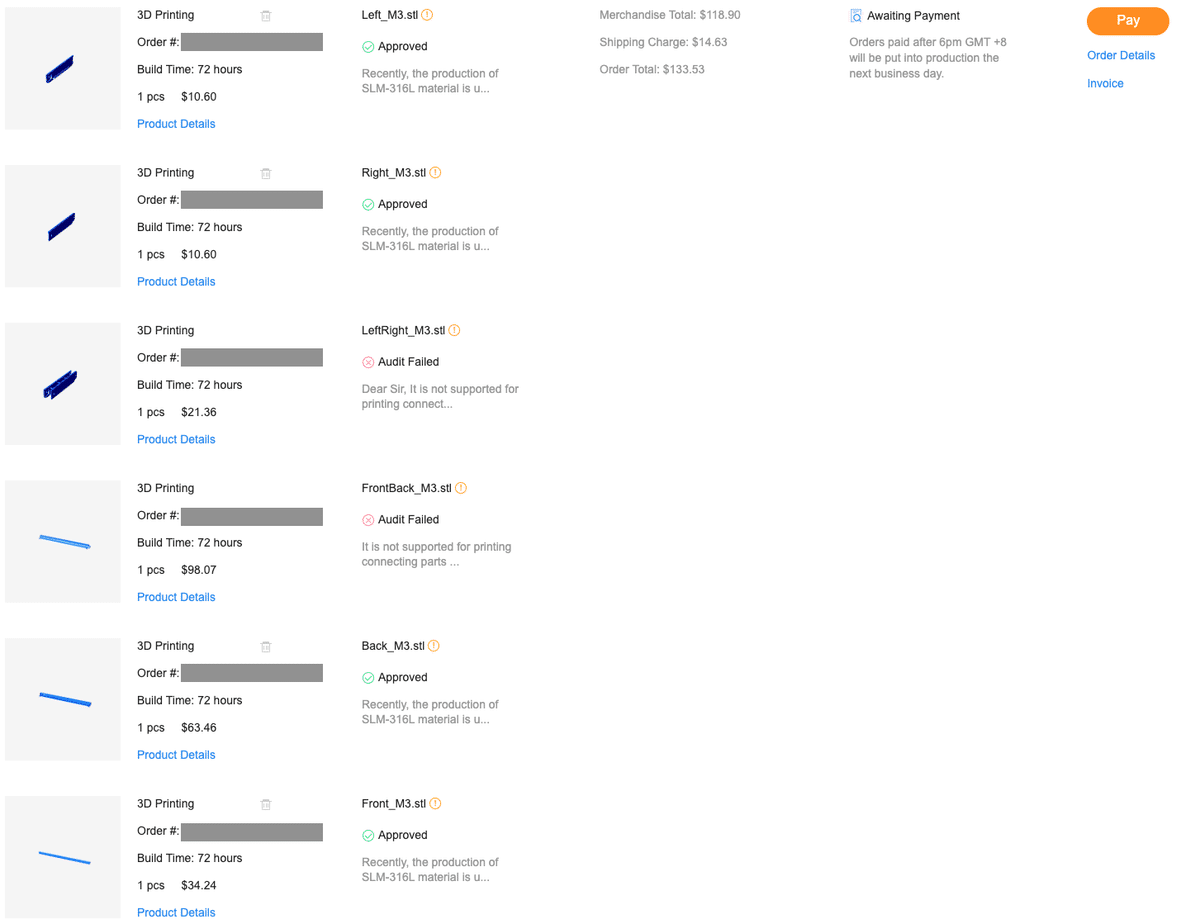
製造
これでようやく製造開始だと思った矢先、注文画面に次のようなテキストが表示されておりました。予定より納期が伸びる旨が書かれています。
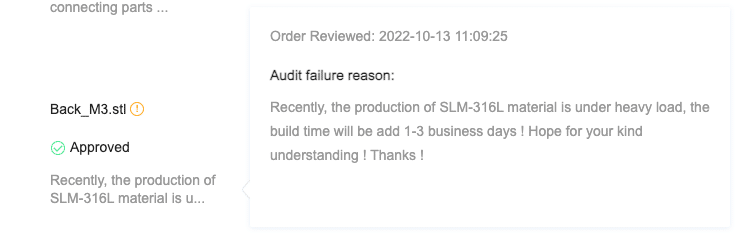
Recently, the production of SLM-316L material is under heavy load, the build time will be add 1-3 buisiness days ! Hope for your kind understanding ! Thanks !
次の動画の通り大量の3Dプリンターを持つJLCPCBでも、金属を出力できるプリンタは1台しか保有していないので、注文が重なるとこのようなことも起きるのでしょう。のんびり待ちます。
数日するとステータスがIn Productionに変わり製造が開始されました。
ただ、製造の進行状況を表す表示が2日ぐらい最初のステップ(Data Processing)で止まっていたので、もしかしたらエンジニアが忙しくてWeb用のステータス更新ができていないのかなと思いながら、表示が変わるのを引き続きのんびり待っておりました。
どうもこの予想が当たっていたようでステータスが突然発送待ちに代わり製造が完了したことが通知されました。レジン製のパーツ製造時はステータスが随時更新されていたので、金属製の出力品の場合(忙しい場合?)はこんなこともあると事前に把握しておくと良さそうです。
次の進捗状況は、発送連絡が来た後に更新されて確認できるようになっていました。
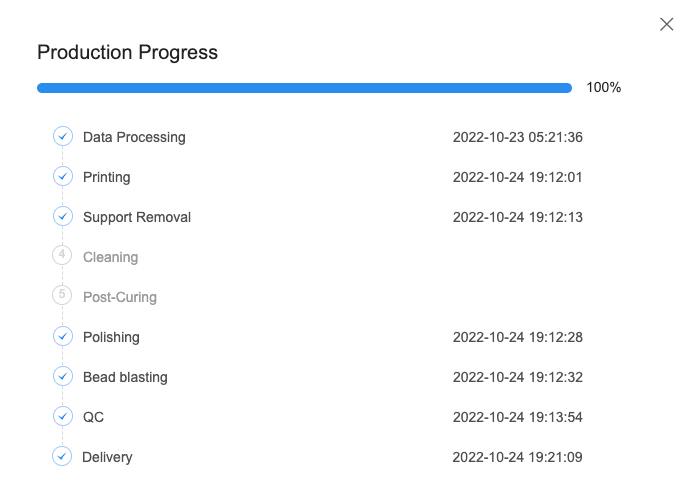
仕様変更後の基板の到着
金属3Dプリントは発注データの作り直しや前述の通り納期の遅れがあったこともあり、先に仕様変更した基板が手元に届きました。発注した基板は次の3種です。
※ ちなみに基板と3Dプリントは同梱して発送してもらうことはできません。
ボトムプレート x 2種
キーボード本体となるPCB
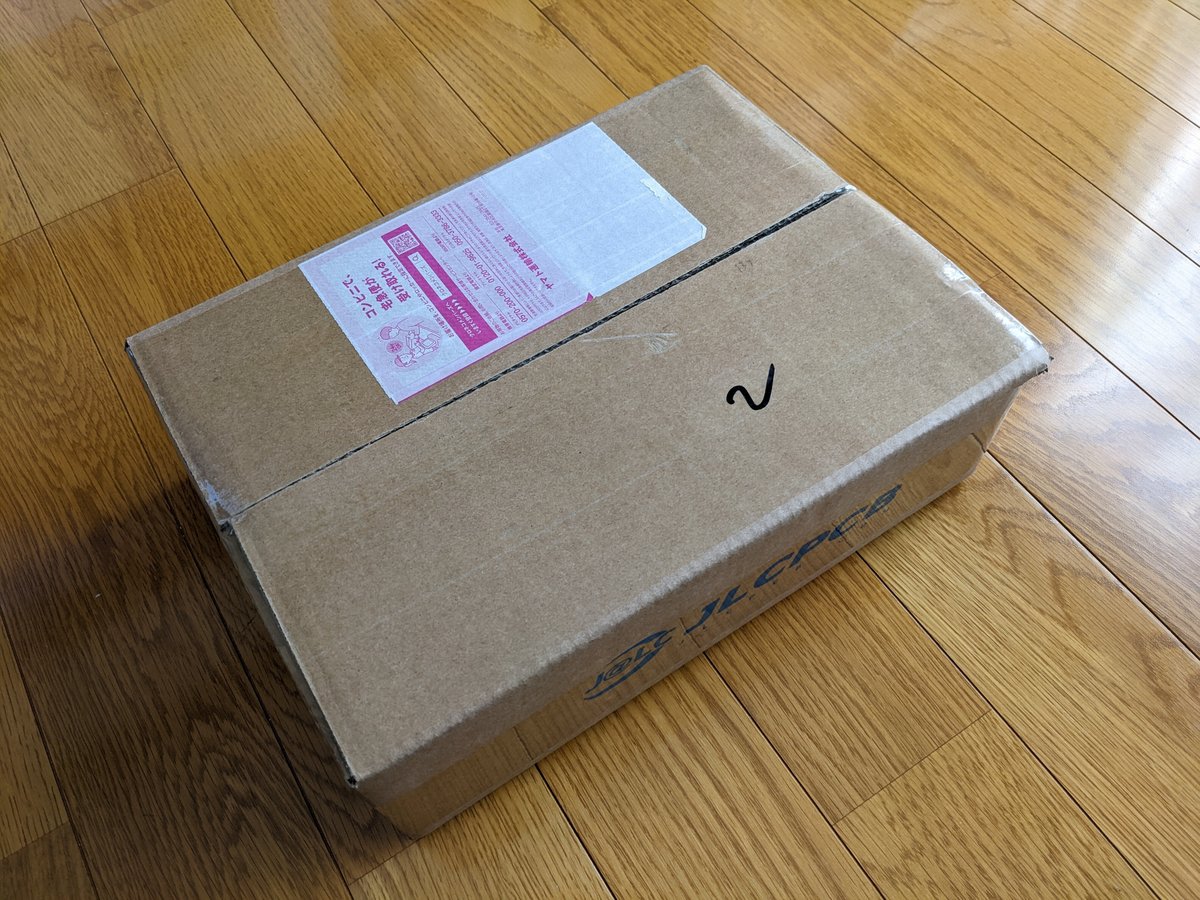
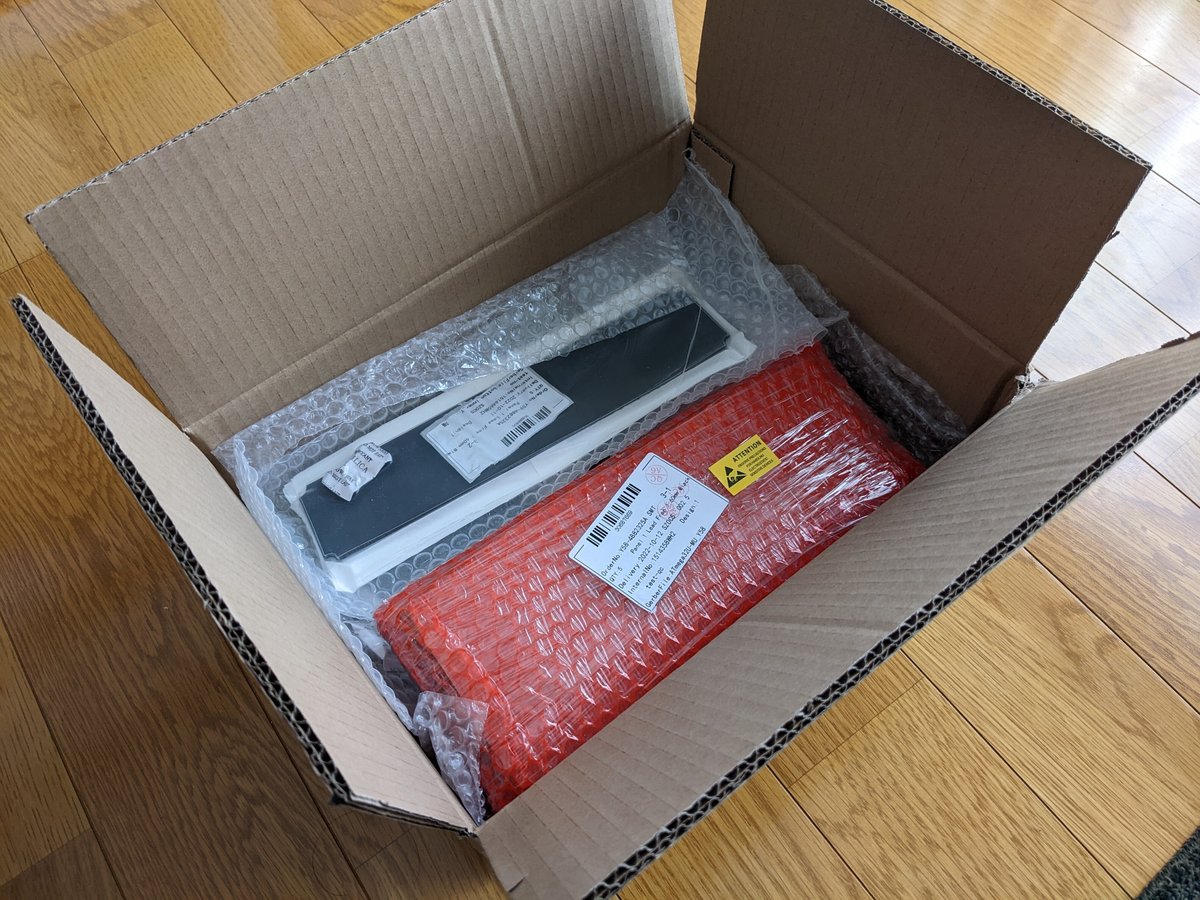
以前の発注時には利用しなかったオーダーナンバー除去オプションと、基板納品時の傷防止用の紙を挟んでもらうオプションを利用してみました。
パーツによって凹凸が生まれるのでPCBAを利用した基板に対しては紙を挟むオプションが利用できないのでその点はご注意ください(そもそも注文画面で選択できなくなる)。
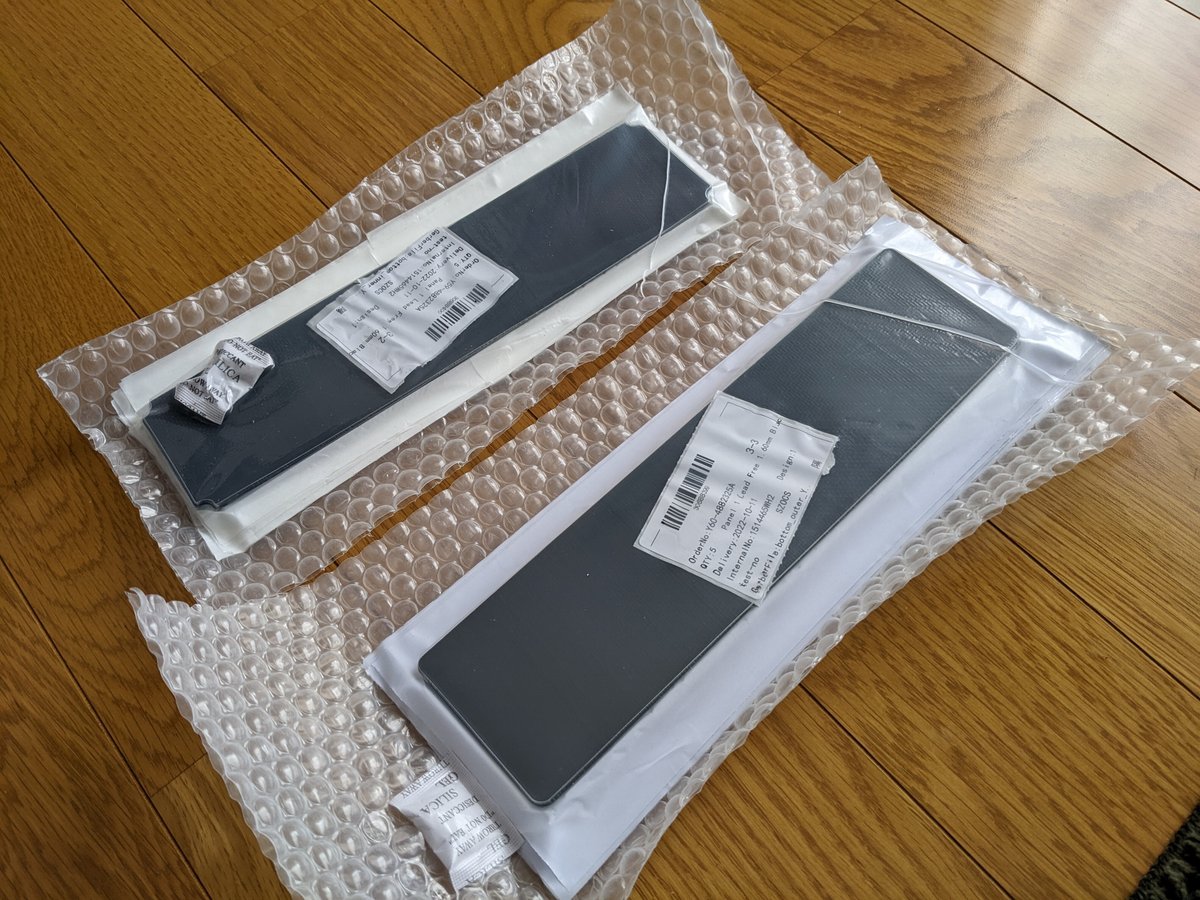
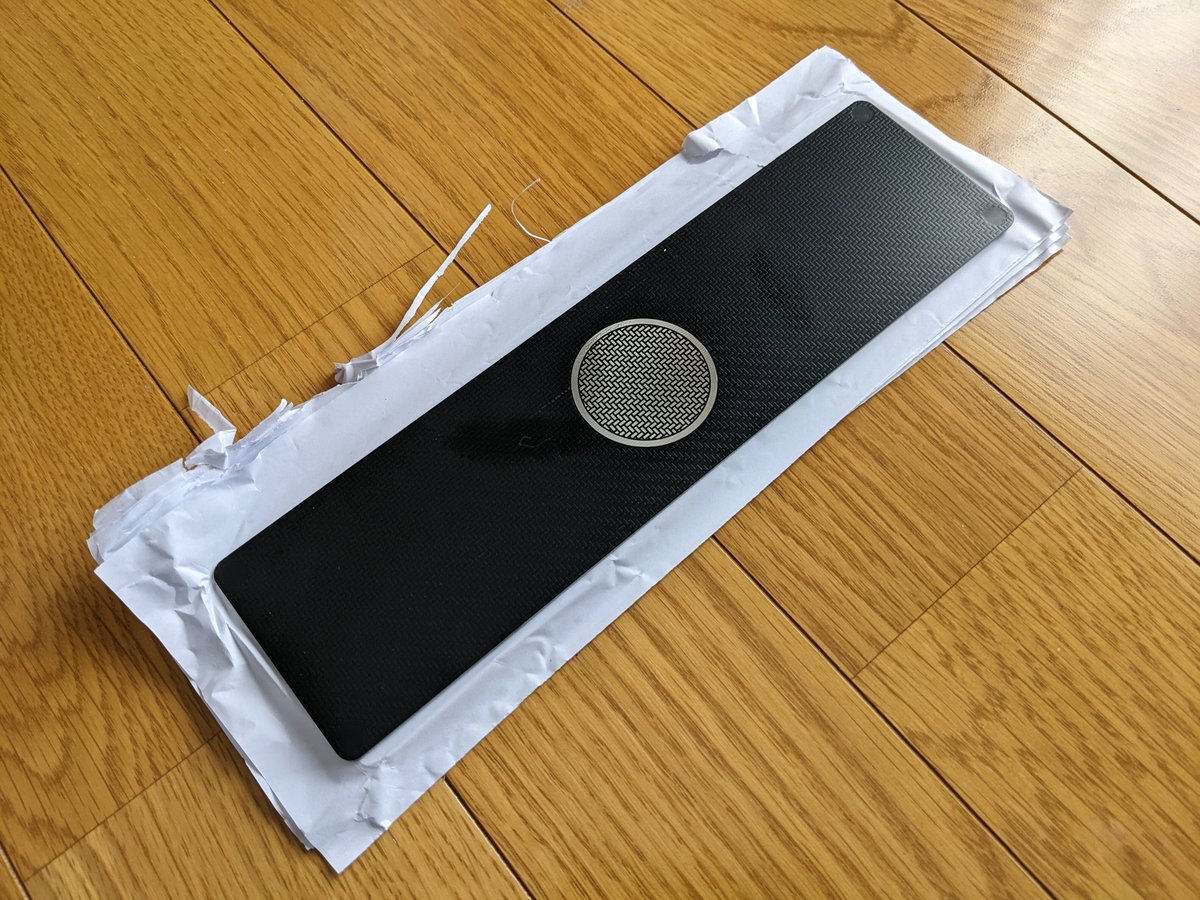
装飾するための一要素として銅箔(Cuレイヤー)を利用していますが、鉛フリーなどの表面仕上げによって銀(HASL wit Lead)、銀色(LeadFree HASL)、金色(ENIG)となります。ENIGは無電解金メッキと呼ばれる処理方法で、高価なので自分は試したことがないですが調べる限りは金色ということで間違いなさそうです。
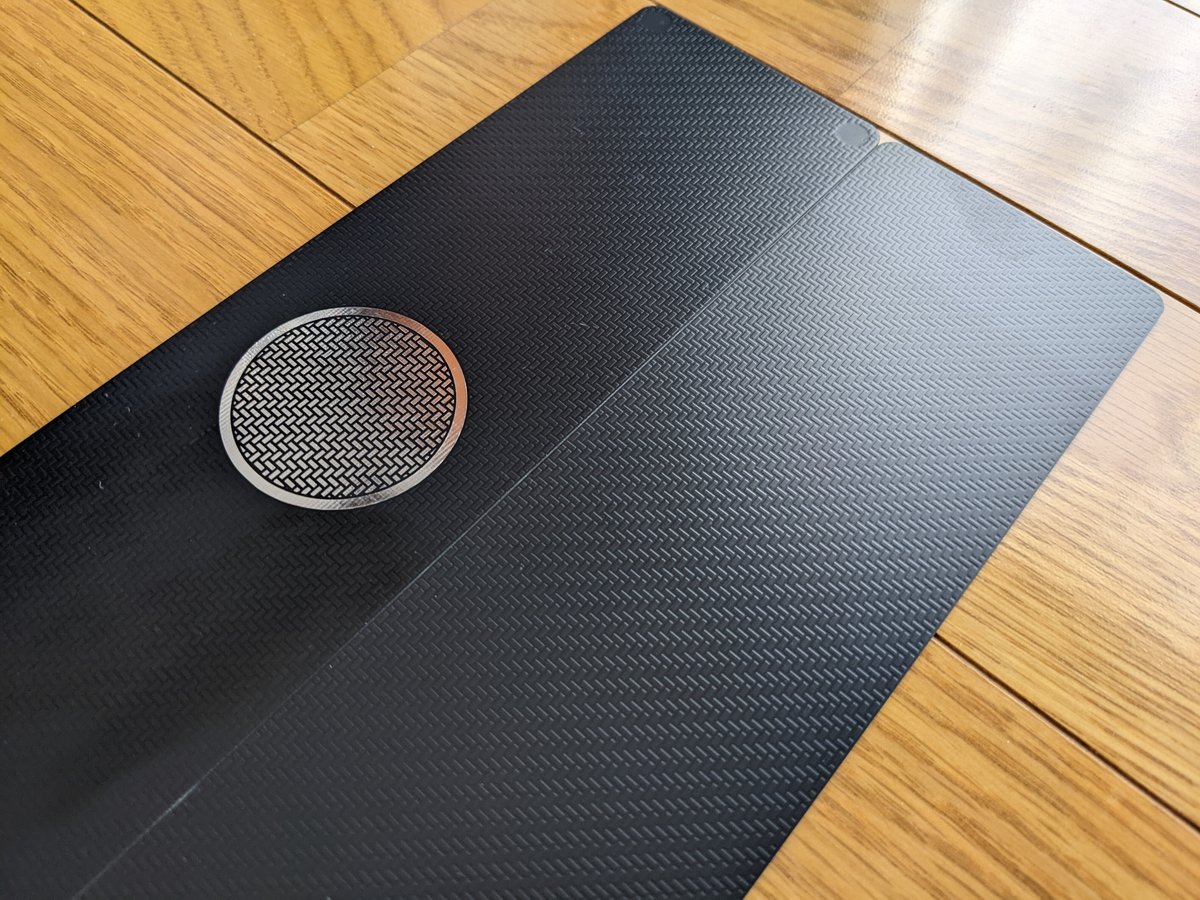
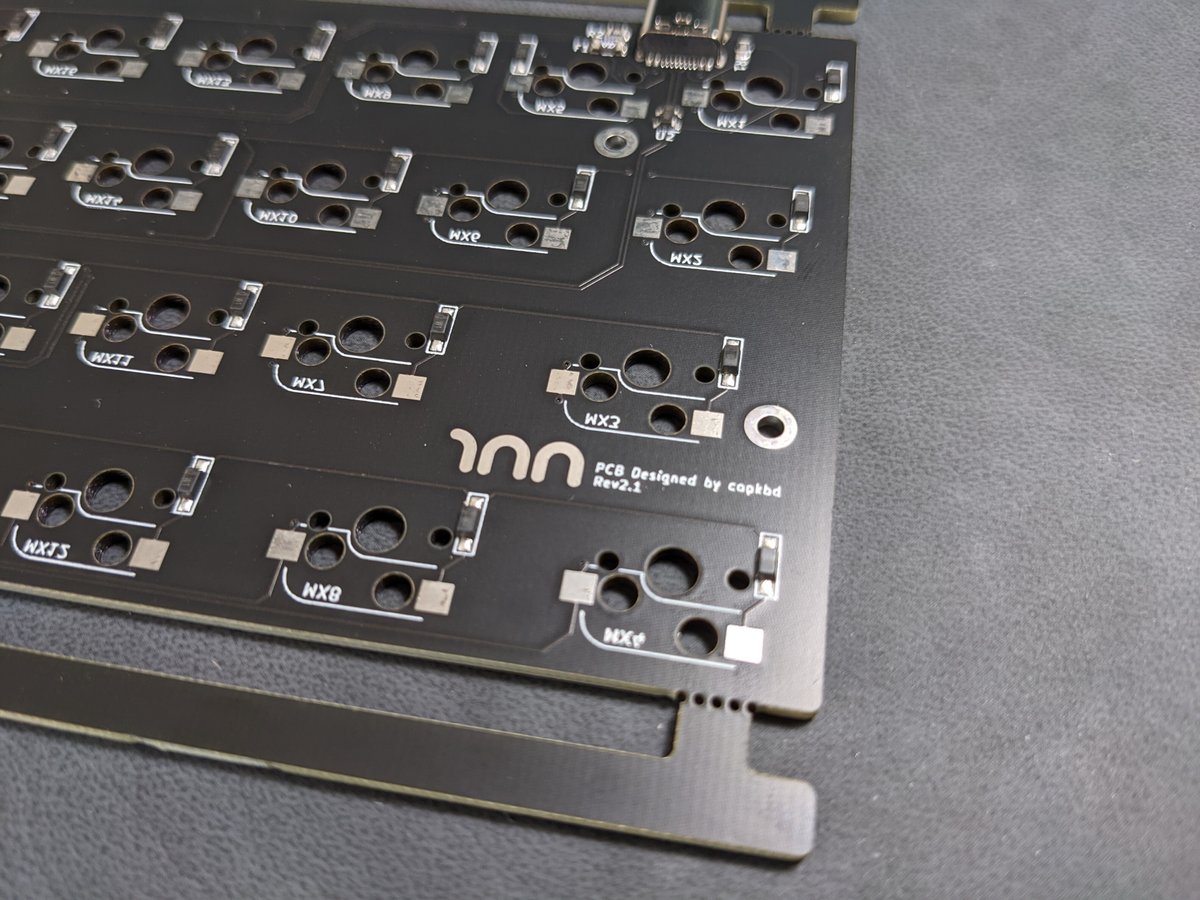
USBコネクター部分の形状変更も意図した通り製造されております。
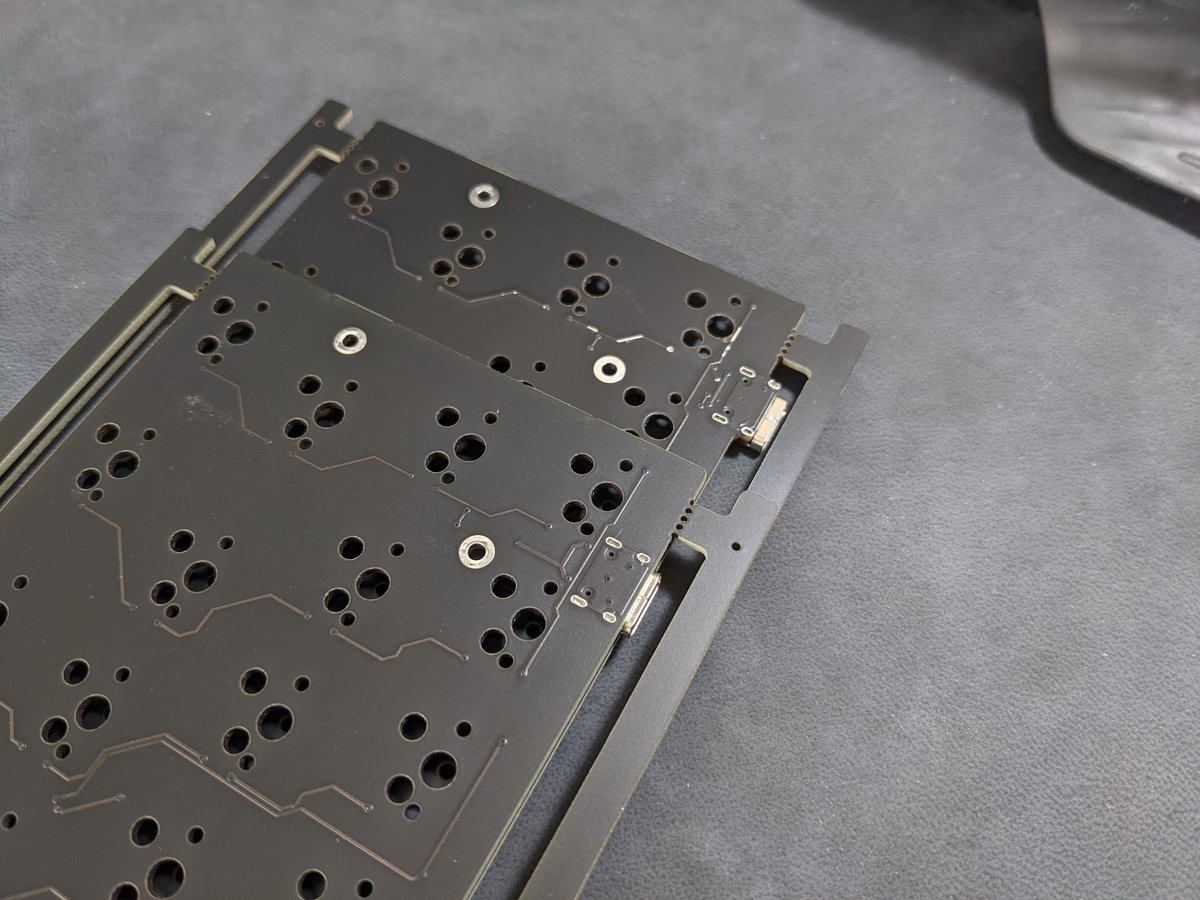
次の写真の通りATmega32U-AUに比べてATmega32U-MUは部品サイズがかなり小さいので、基板の部品レイアウトに余裕がないキーボードの場合には有効な選択肢になるかと思います。
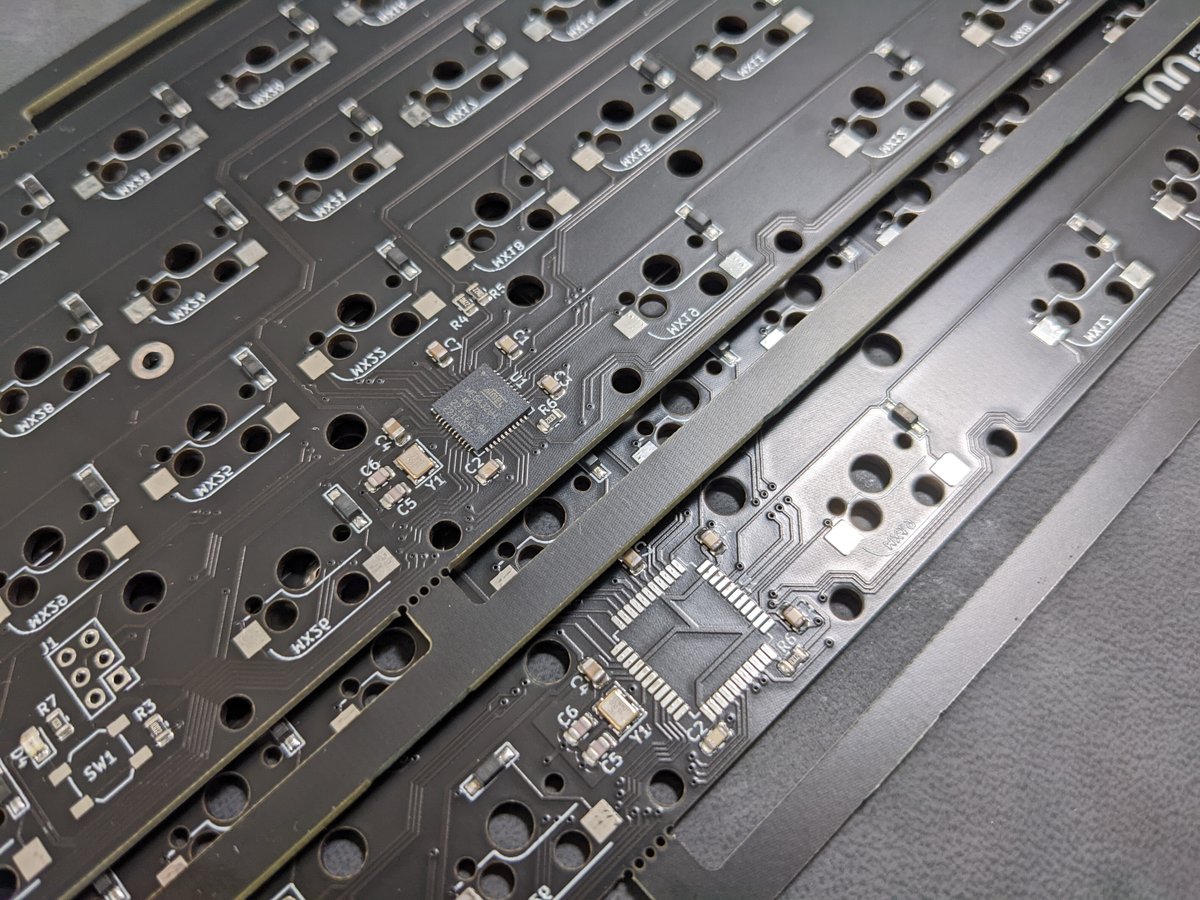
3Dプリント製ステンレスケースの到着
今回、なるべく早く受け取りたかったこともあり、OCS Express(4~8営業日で配送。格安)ではなくFedEx International Packet(3~6日で配送)を使ってみました。比較として配送料はOCSでは約8ドル、Fedexは約15ドルでした。
10/24日に配送通知を受け取り、手元には10/28日に到着。手元には国内代行業者としてゆうパックで配送されました。
関税・消費税については後日払込用紙が送られてくるようです(円安でなければ関税がかかるような金額ではなかった…)。
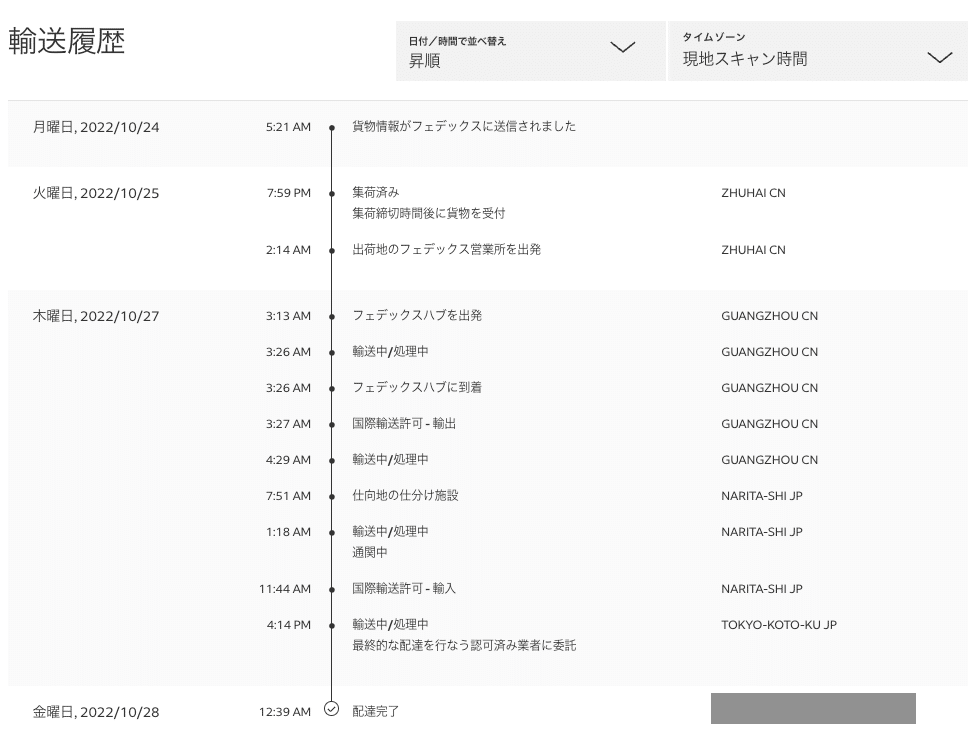
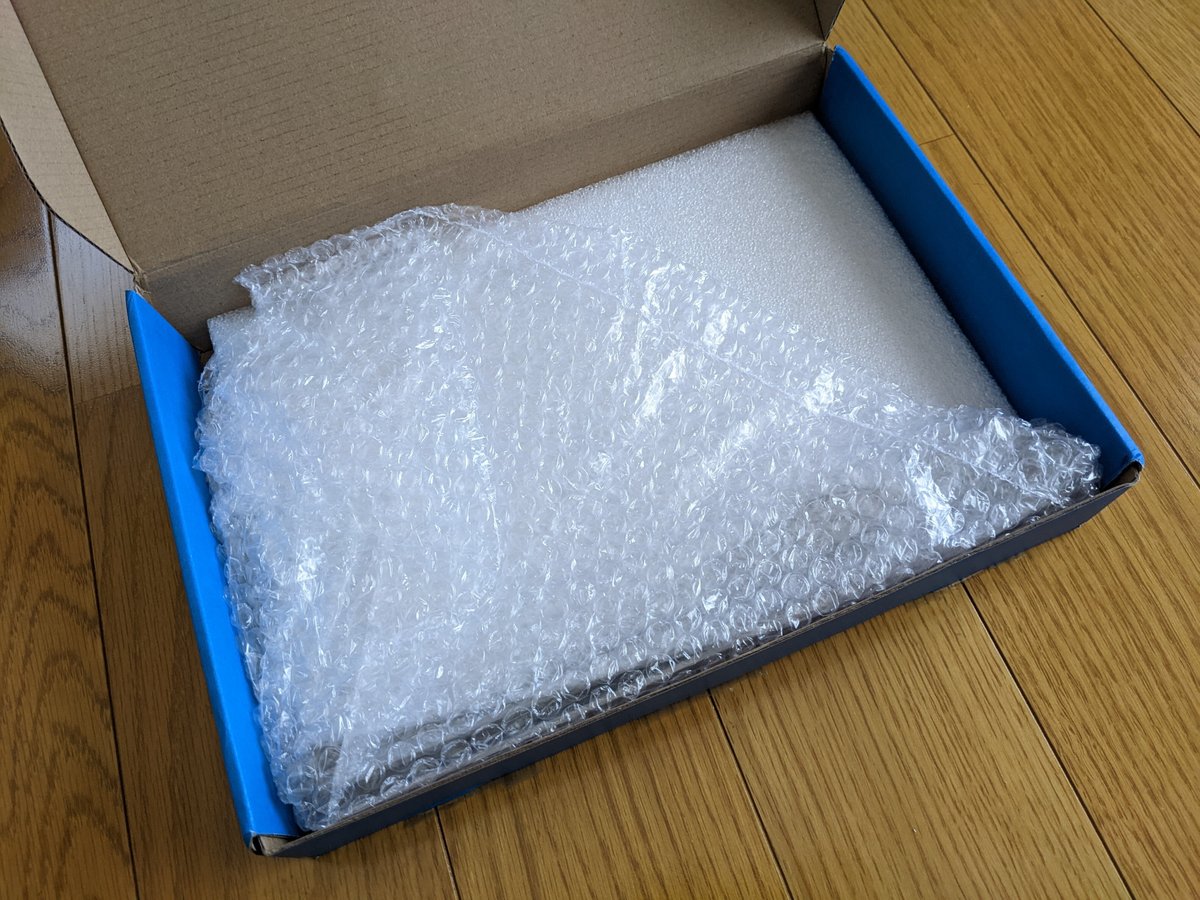
造形物の確認
届いた造形物がこちらです。
想像以上にずっしりとした重厚感があり、さすがステンレスの塊といった印象です。この316Lはサージカルステンレスと呼ばれ、腐食や錆などが発生しづらく金属アレルギーを起こしづらいためジュエリーなどにも利用されます。
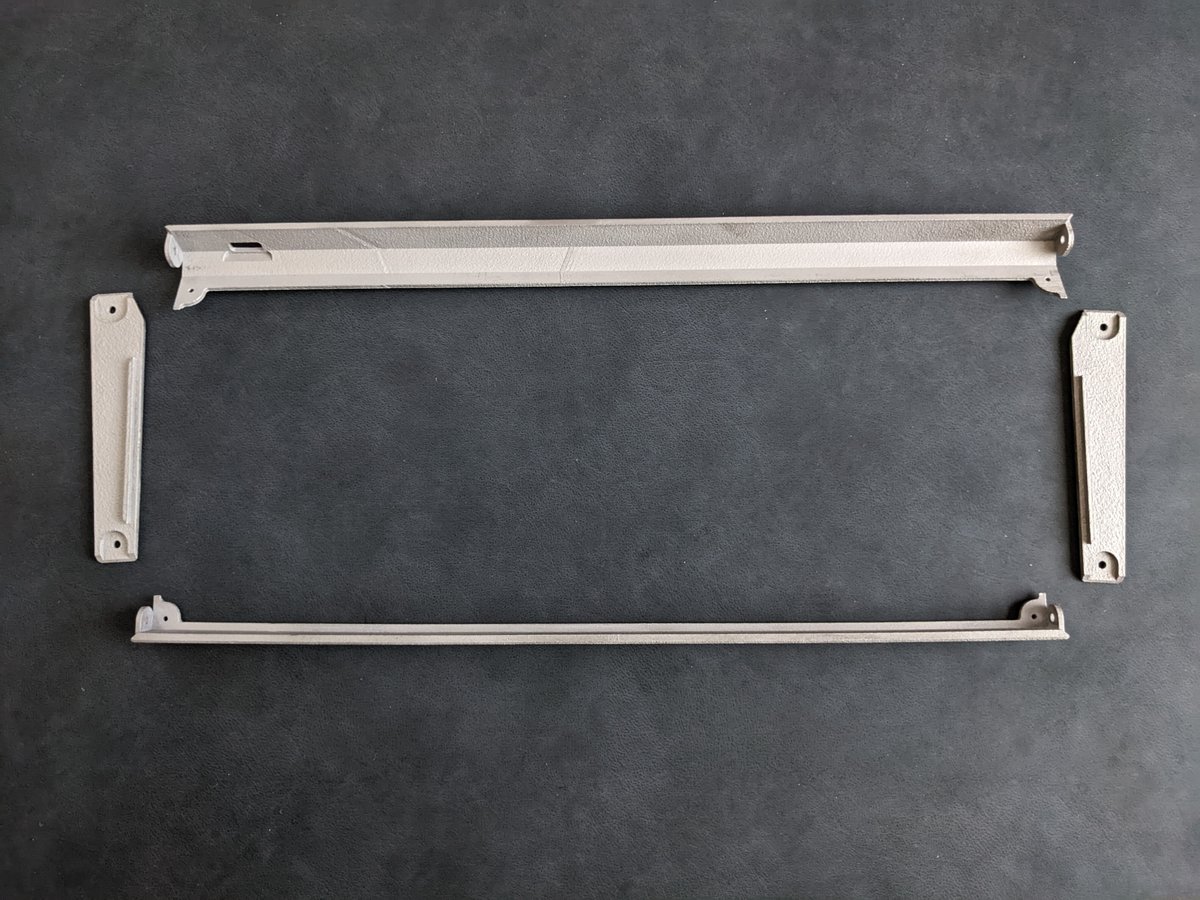
懸念していた歪みもほとんどなく、大変精度高くプリントされていました。
写真では明るいグレーですが、実物の印象としてはApple製品のラインナップにあるスペースグレーの色味に近い感じでとてもかっこいいです。おそらく表面を研磨すれば銀色に輝くと思いますが、このマットで暗い色味が気に入っているのでそのままにしています。
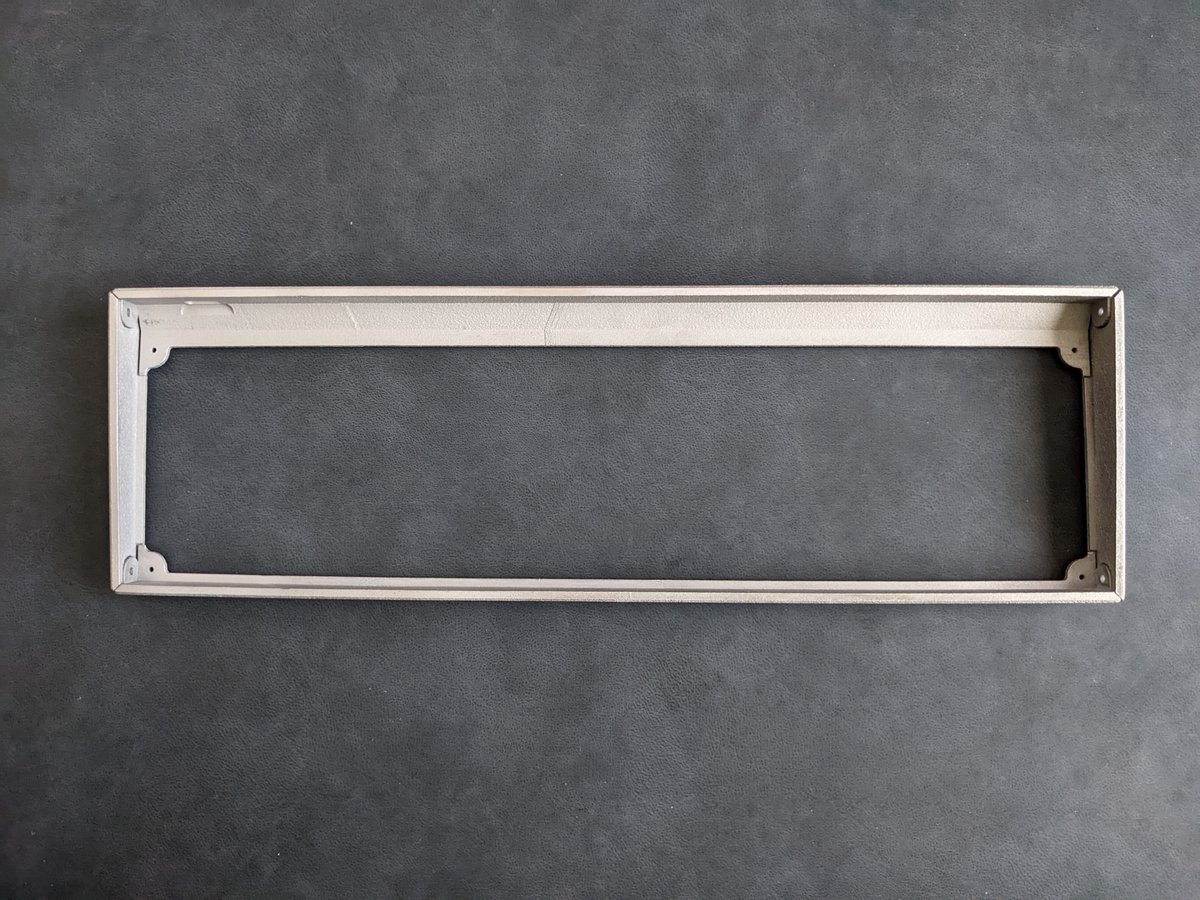
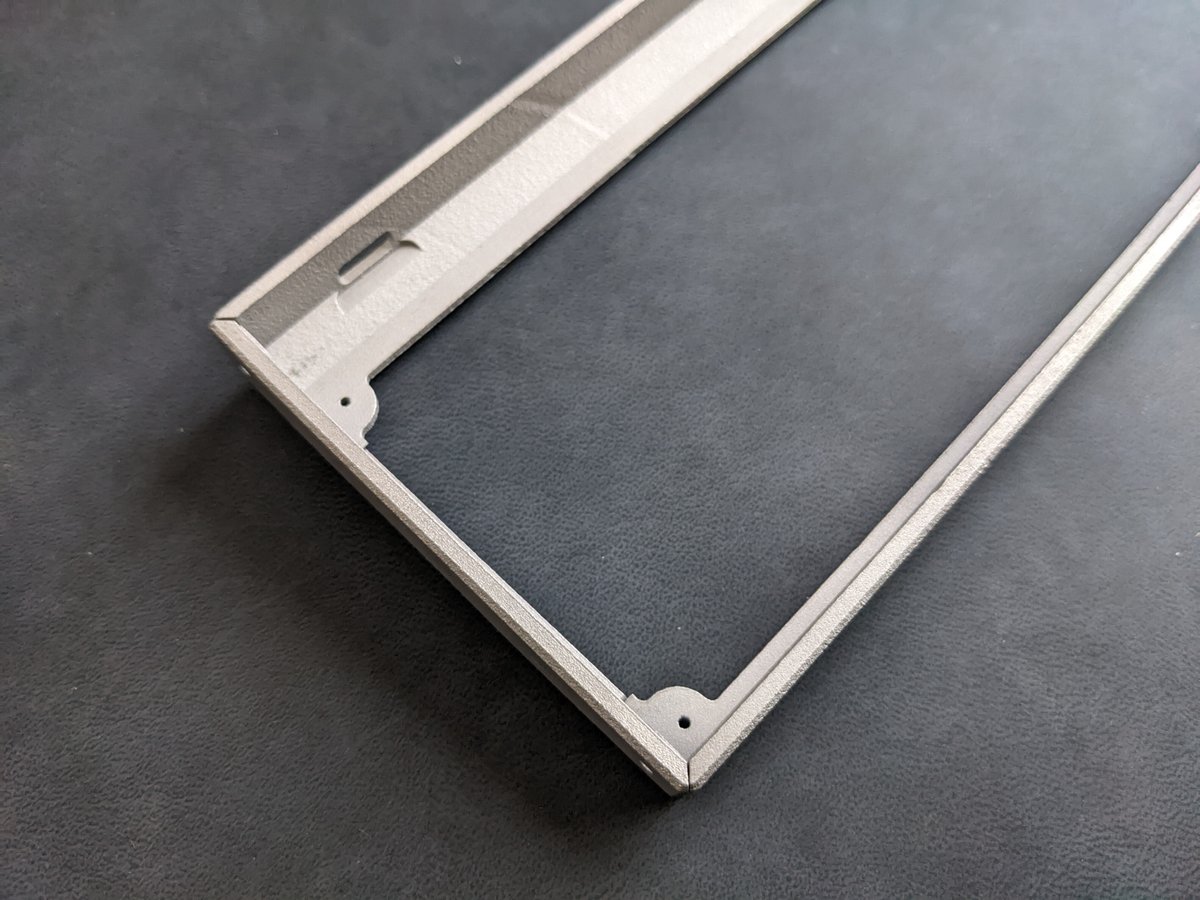
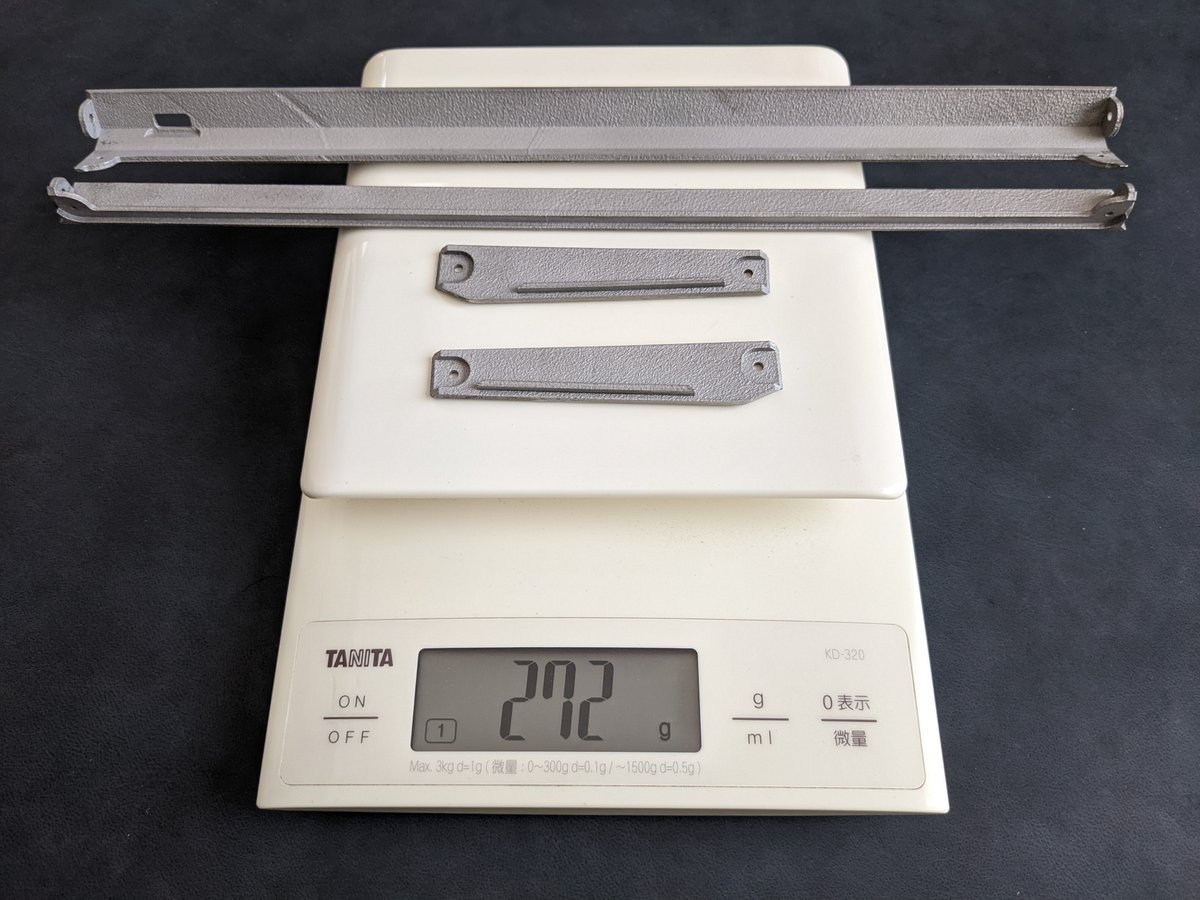
金属3Dプリントの場合、ステージから造形物を切り離す際には放電加工が利用されます(ワイヤ放電加工)。そのため、プリント時にステージと接地していた面は次のように鋸の歯のような跡が発生します。ただカット後に表面処理を施しているためかぼこぼこしているという印象はそんなになく、割とサラッとしています。
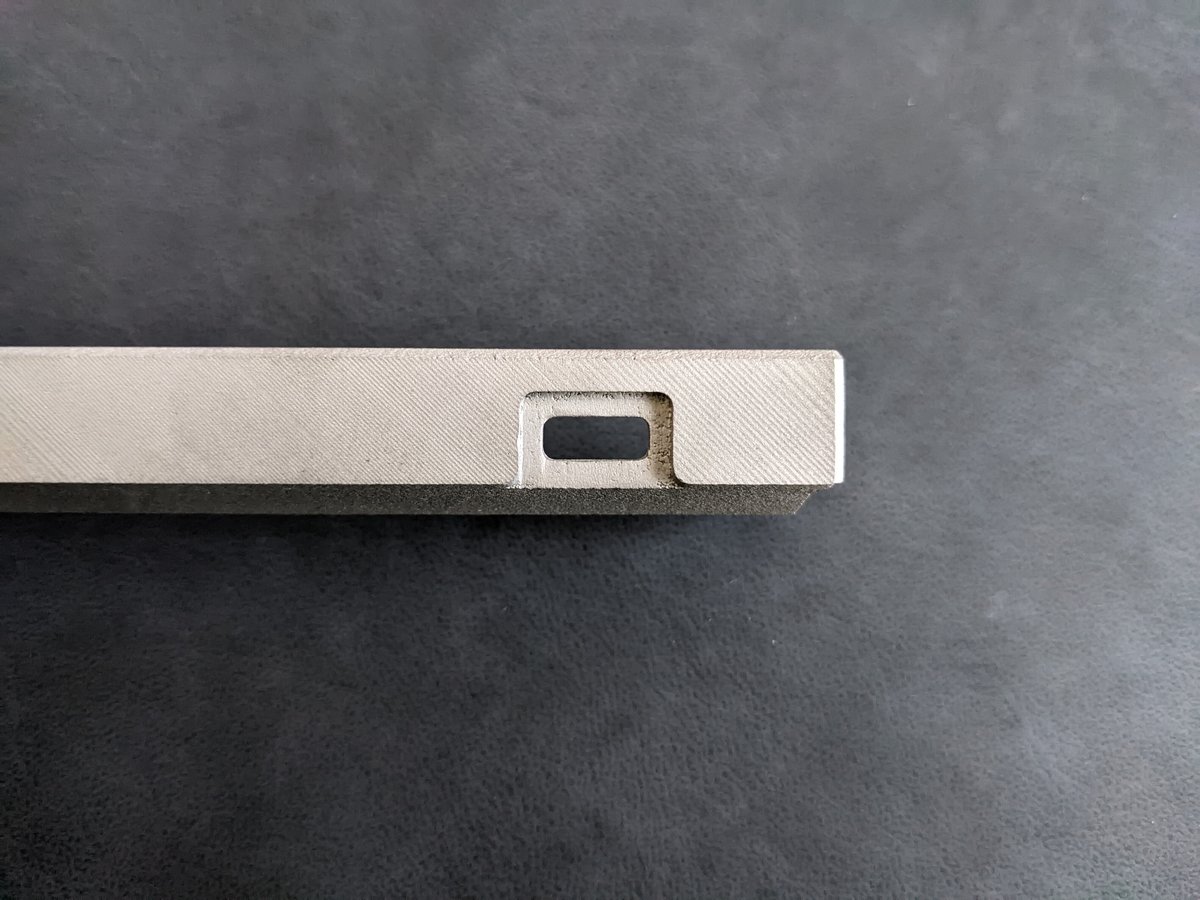
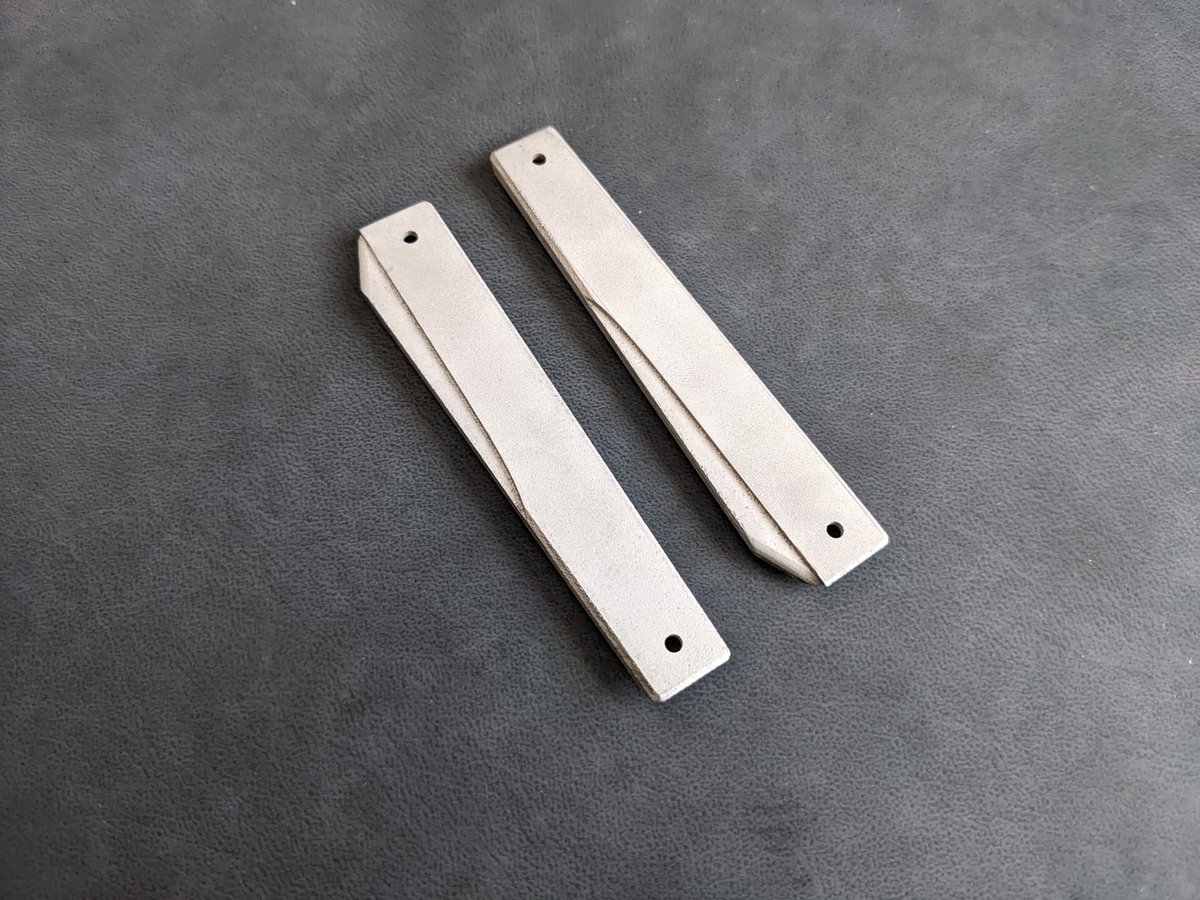
ステージに対して斜めに設置されていた場合この跡は斜めになり、直角 or 水平に設置されていた場合には造形物に対して直角 or 水平の歯の跡が残るようです。
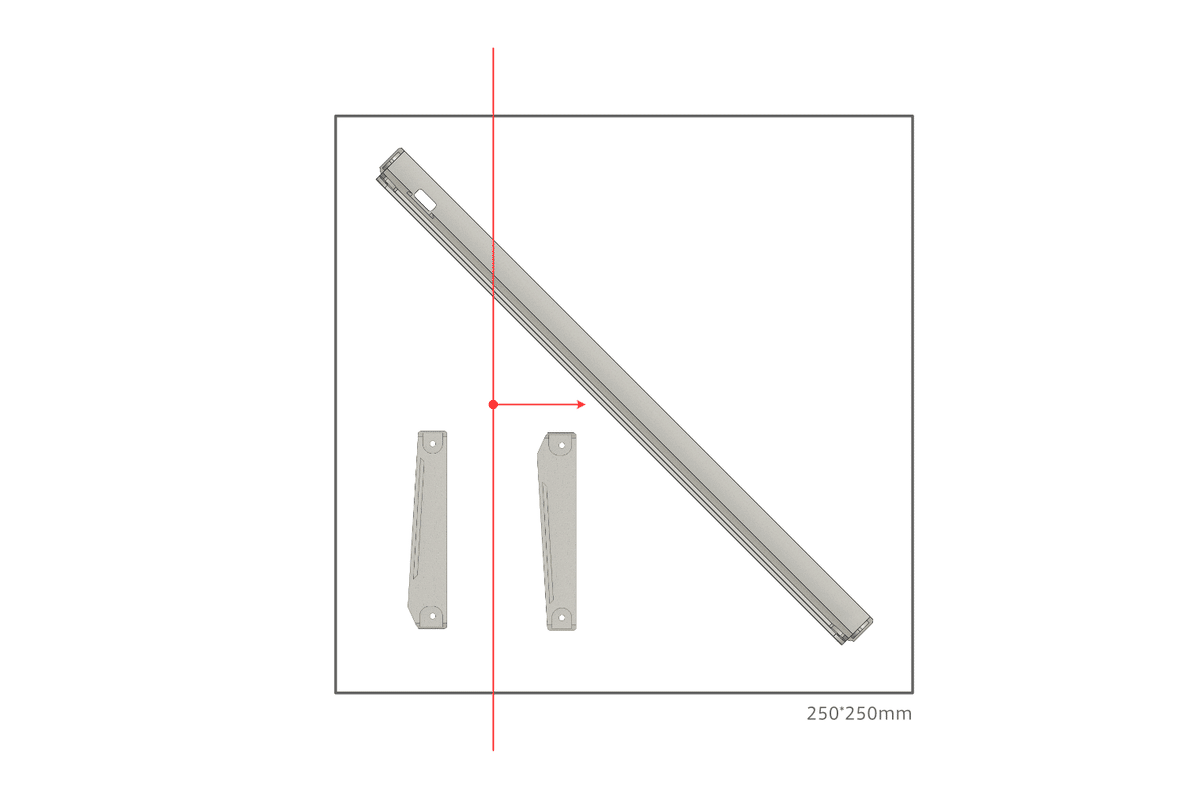
その他の面は鋳物のような質感になっています。レーザーによってステンレス粉が溶かされ固められるのでこのようになるのでしょうか。
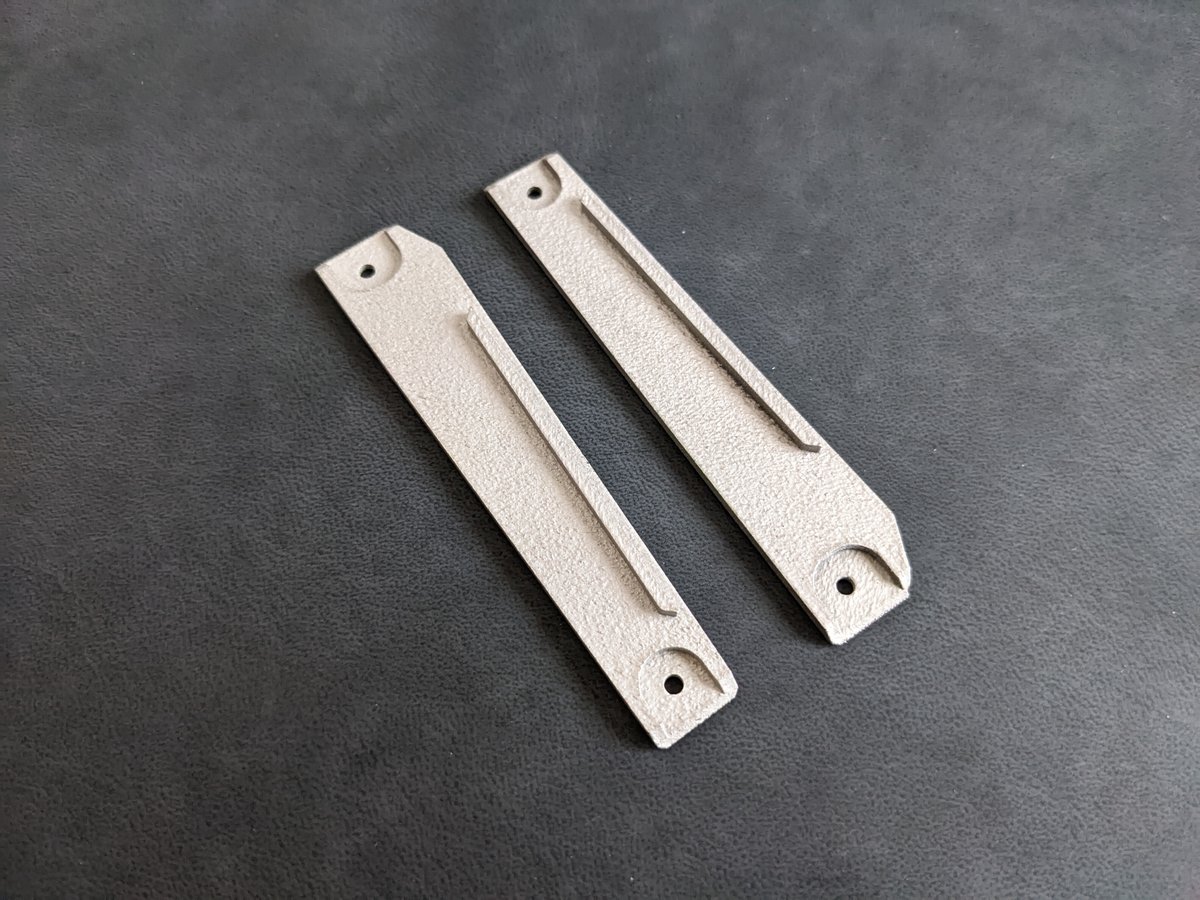
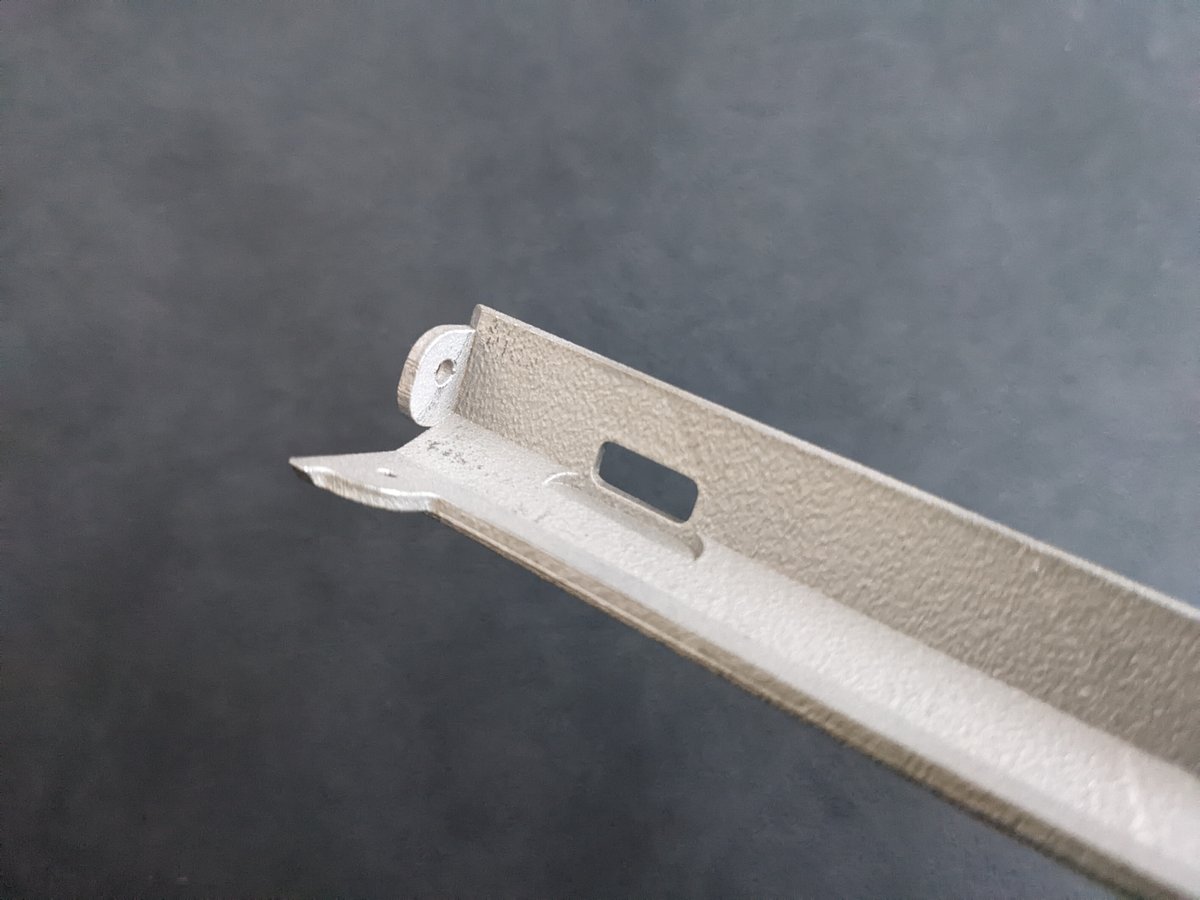
追加工と組み立て
各パーツの確認が完了したので組み立てていきます。
各辺はM3の止めネジで組み合わせ、さらにFR-4製のボトムプレートでフレーム全体を固定して剛性を出します。
下穴としてφ2.5の穴を発注データに設けていましたが、精度がバッチリ出ていたので簡単にM3のタップを切ることができました。
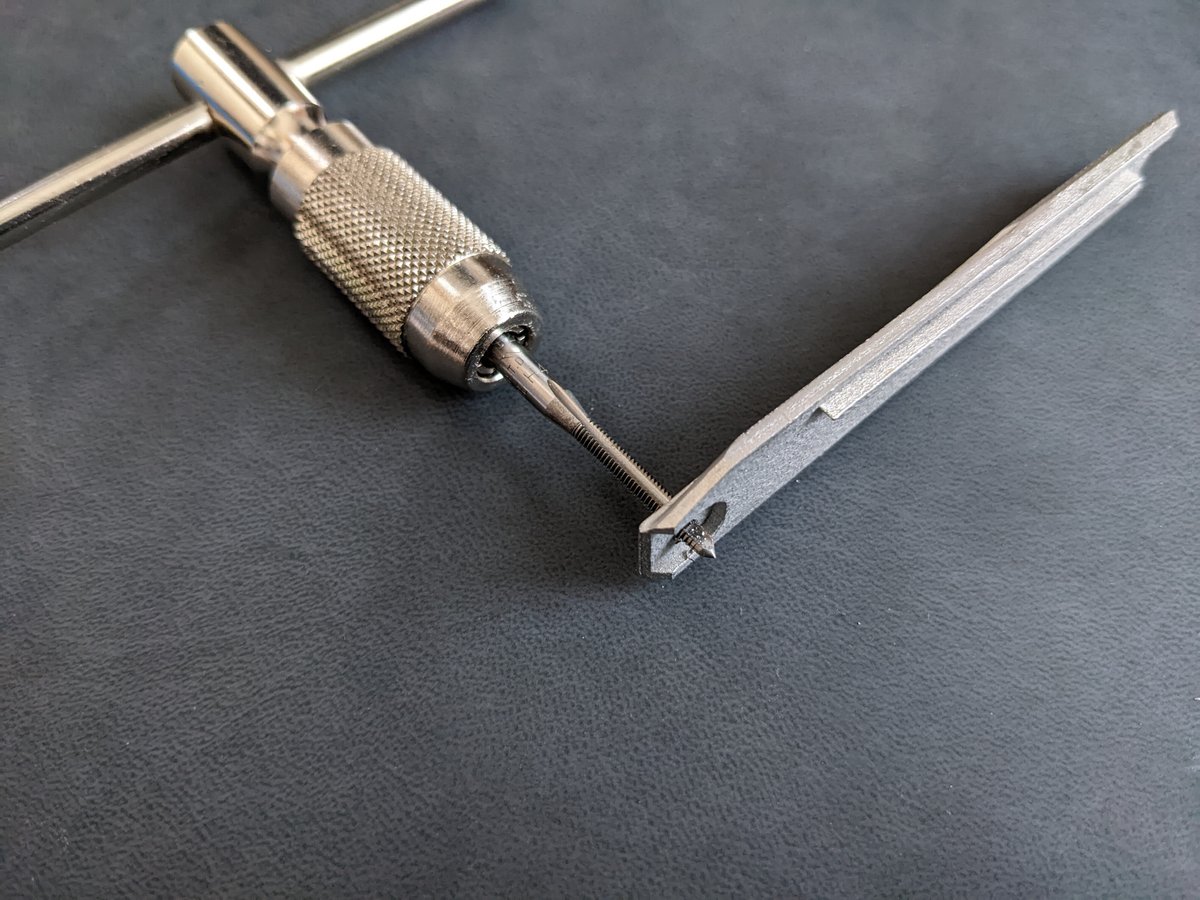
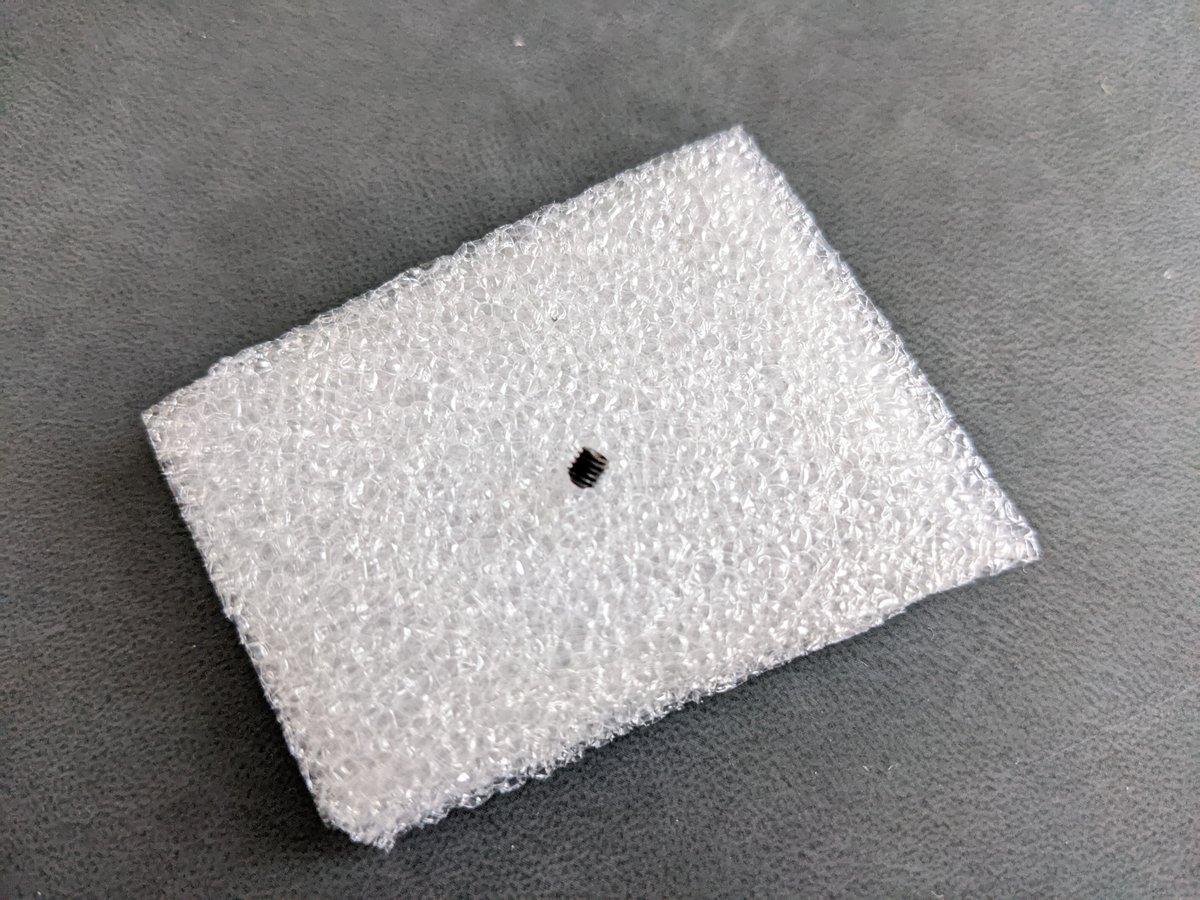
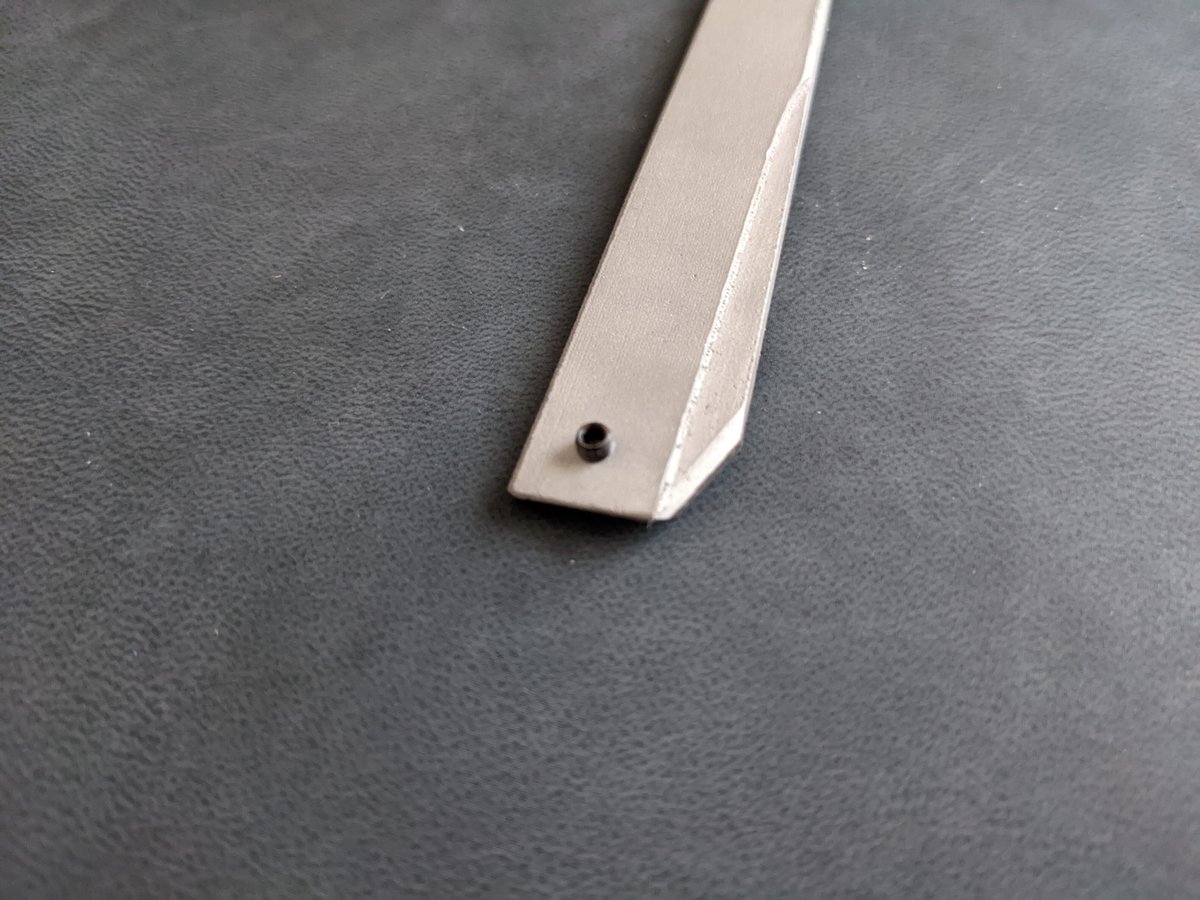
止めネジは4つと必要最小限しか使用していないので、これだけだとフレーム全体にグラ付きが発生します。そのため3Dプリント以上にきっちり精度が出ているFR-4製のボトムプレート2枚と組み合わせてフレーム全体を固定し、剛性を出します。
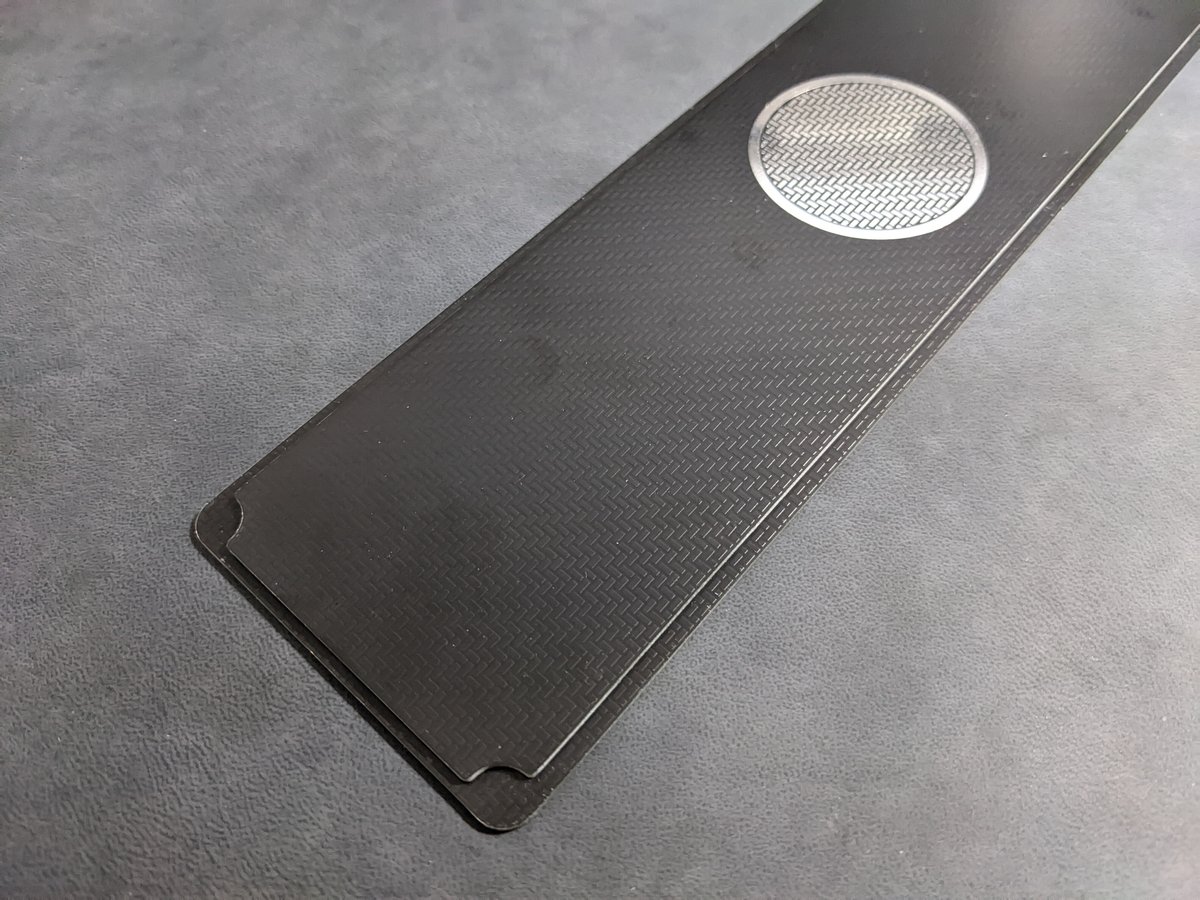
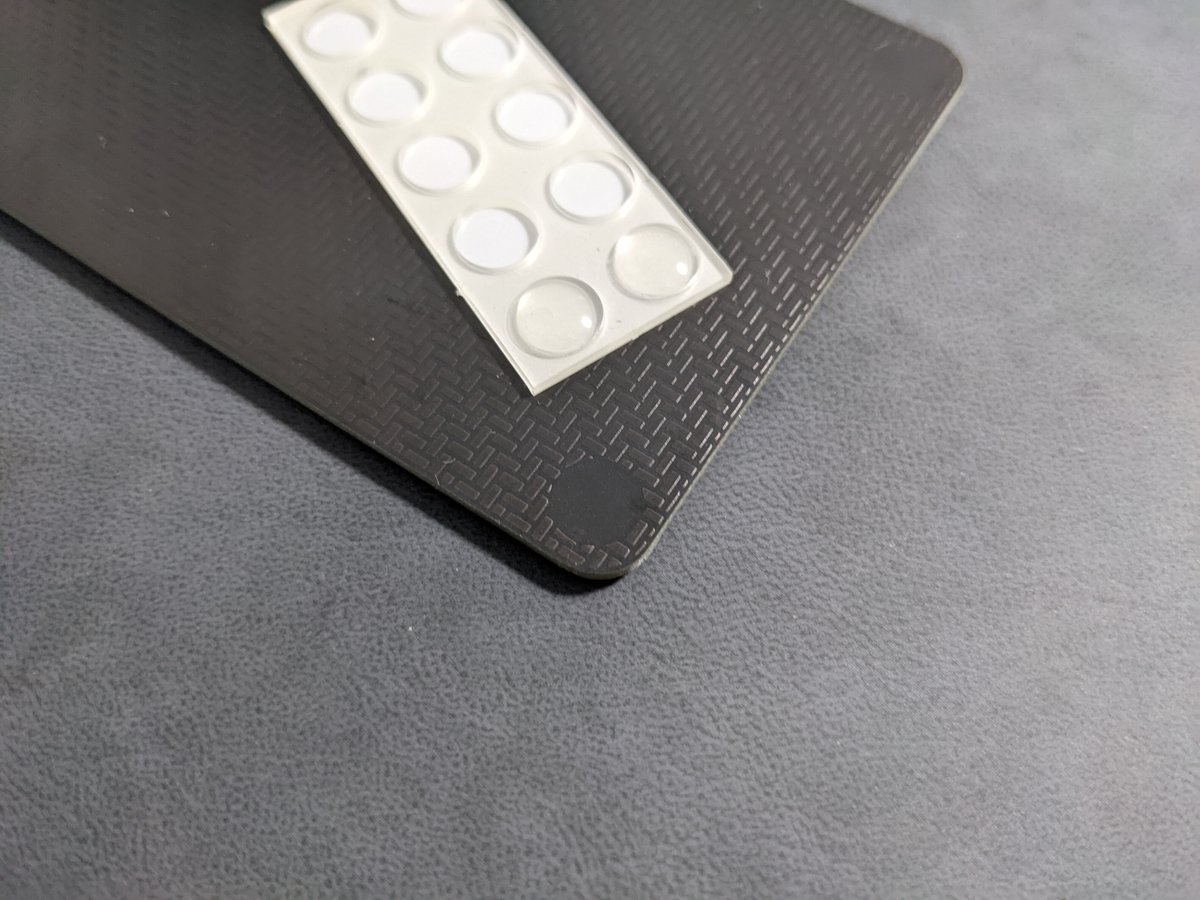
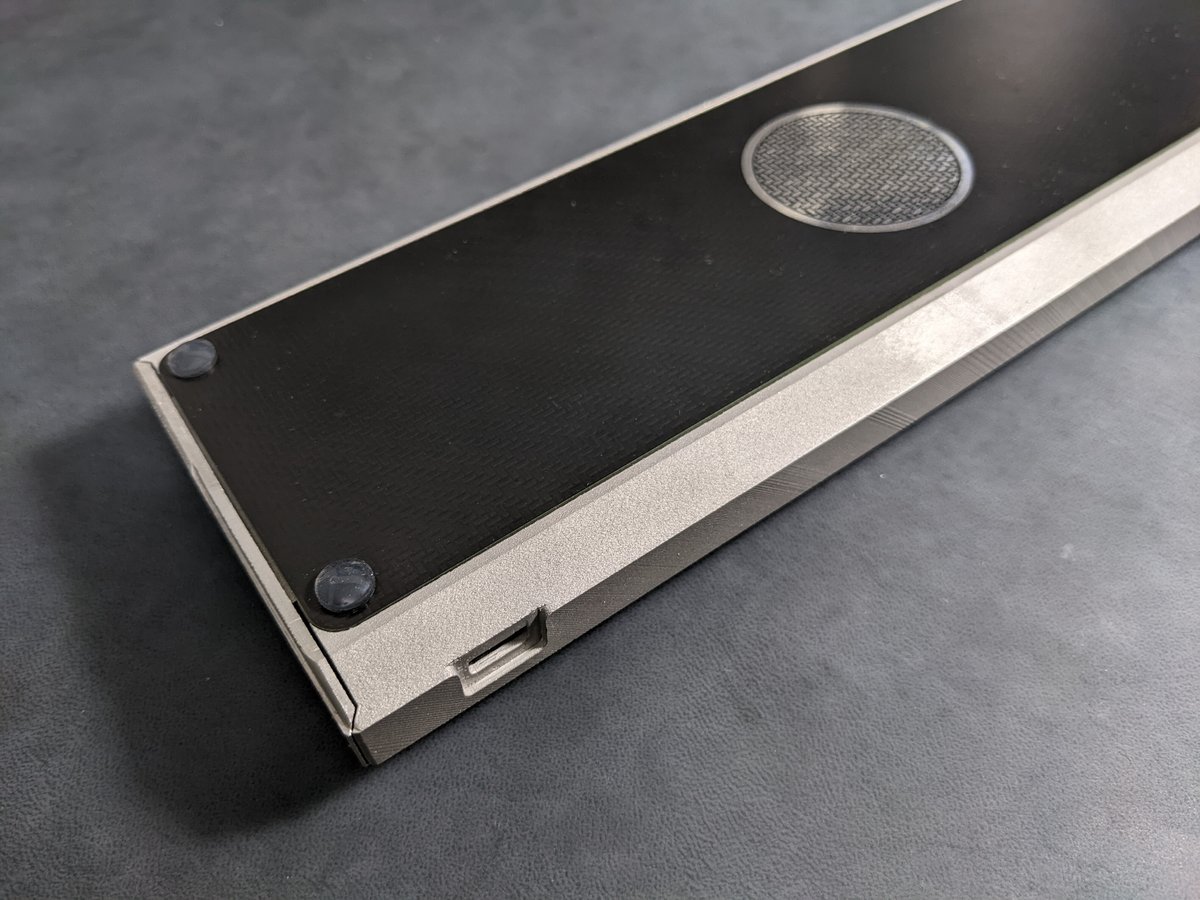
これでケースとしての組み立ては完了です。止めネジ4つだけだとグラついていましたが、プレートと組み合わせたことで剛性も確保できカチカチになりました。
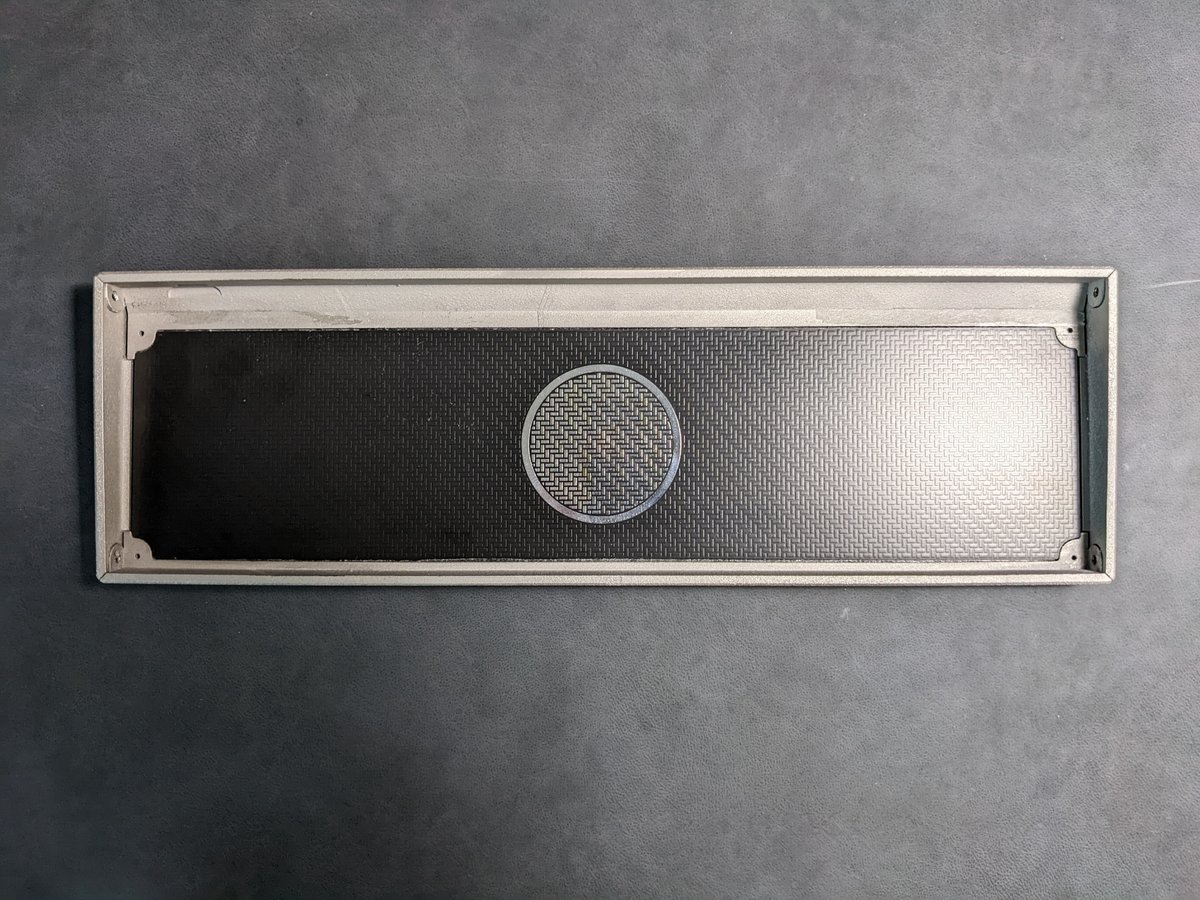
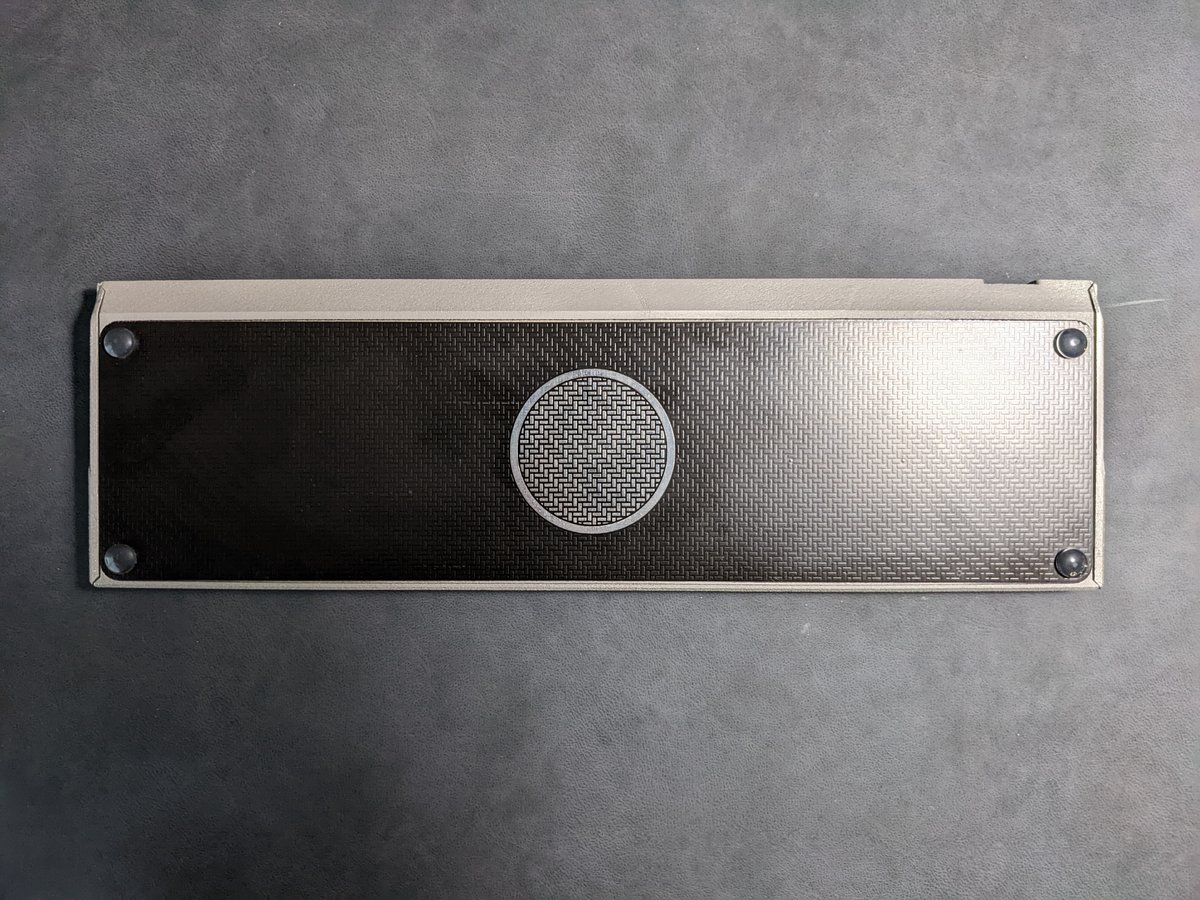
重量はステンレスパーツ単体の時より100gほど加算され、さらに重くなりました。
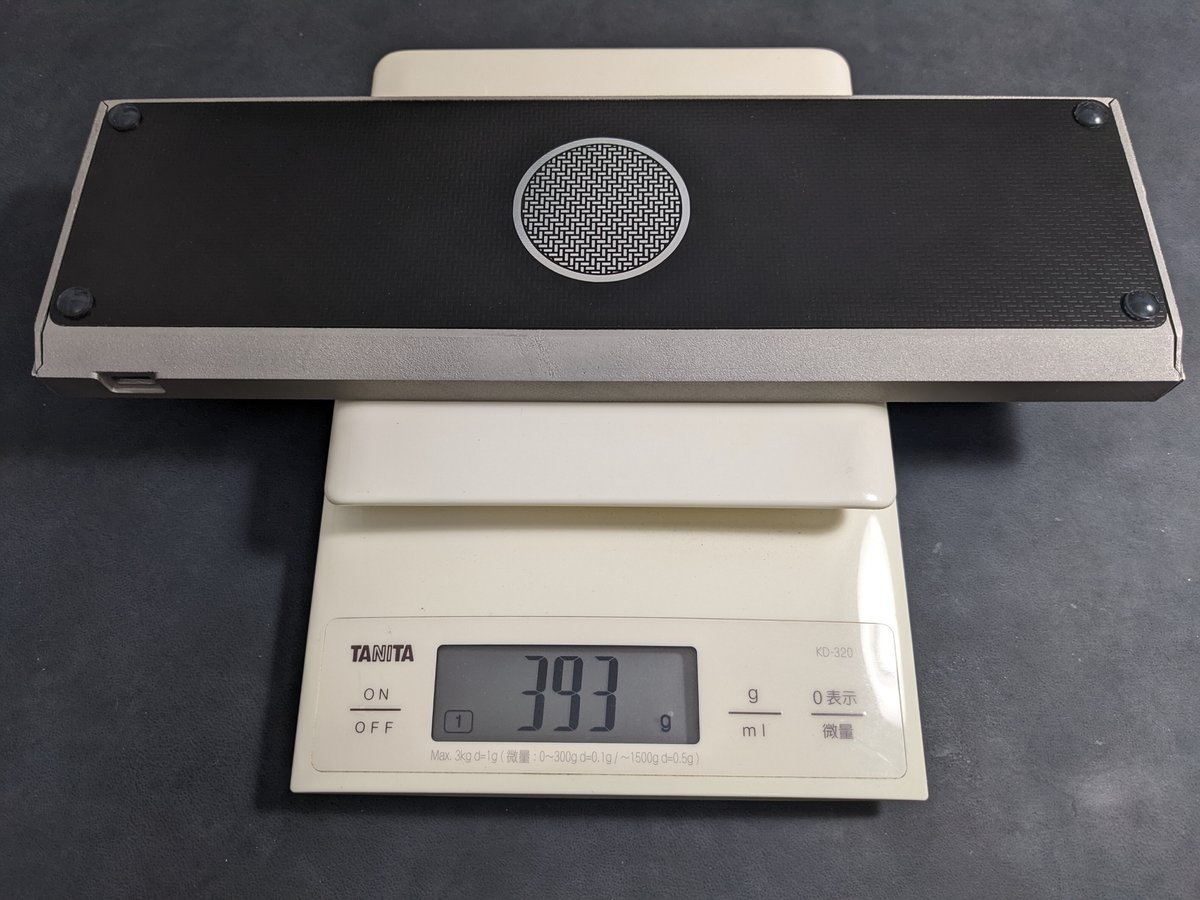
ケースとキーボード本体を組み合わせる
続いてケースとキーボード本体を組み合わせていきます。
今回はなるべく薄型化するため内部構造を簡略化しています。そのためマント方式としてOリングマウントを採用したケースを設計しました。通常は次の商品のようなOリングをスイッチプレートとキーボード本体のPCBの隙間の外周に巻き付け、Oリングとケースの摩擦等によってキーボード本体を固定します。
参考: Oリングマウント - Self-Made Keyboards in Japan
ただ今回、たまたま近所のホームセンターをぶらついてた際に網押さえゴム(網戸を枠に固定するための商品)と呼ばれる激安商品を見つけました。これがOリングの代替になるんじゃないかと考え試しに購入してみました。
網押さえゴムにも直径のバリエーションがありますので、アクリル製のスイッチプレートを使用している場合やロープロファイルのキーボードとかでも使えるかもしれません。
今回はCherry MX互換のキースイッチを使用し、1.6mm厚のFR-4製のスイッチプレートを使用しているため3.5mm径のゴムを使用します。
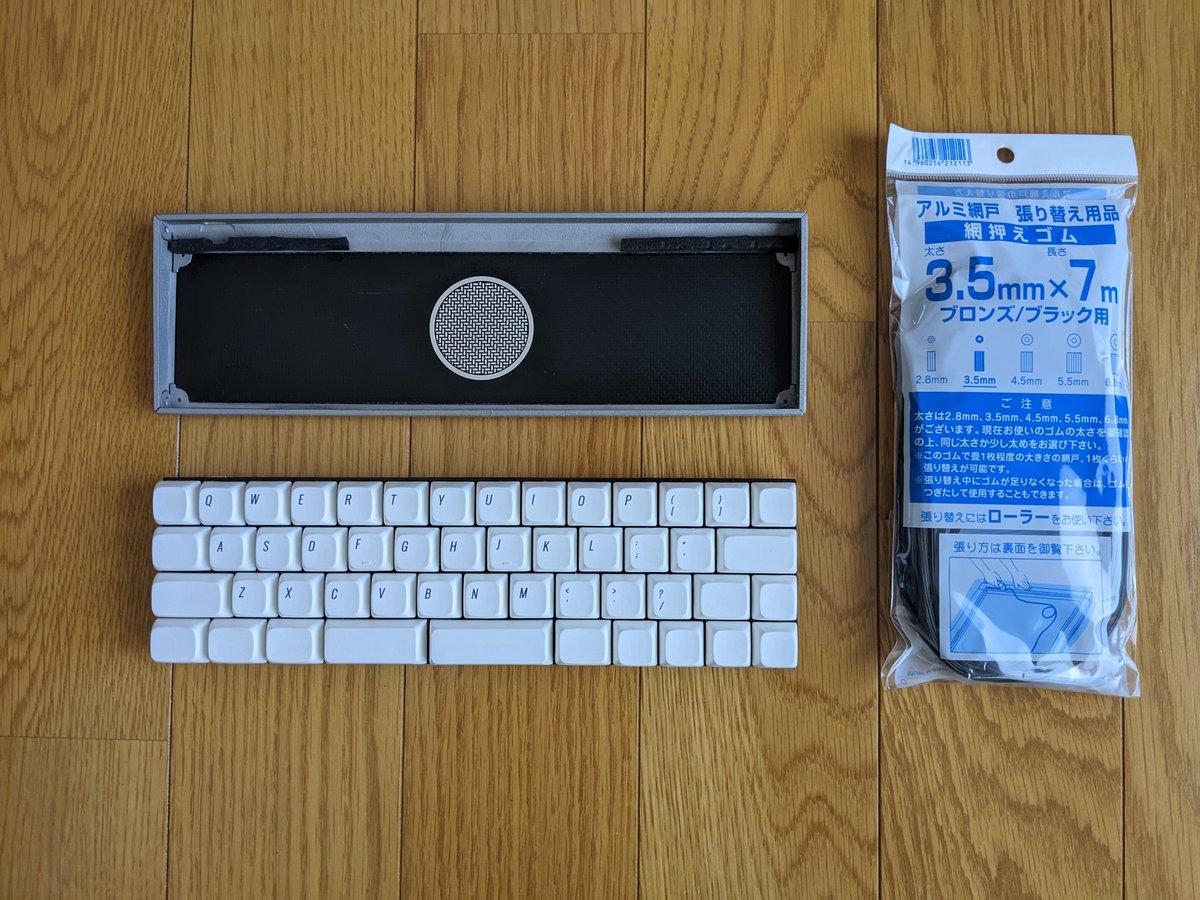
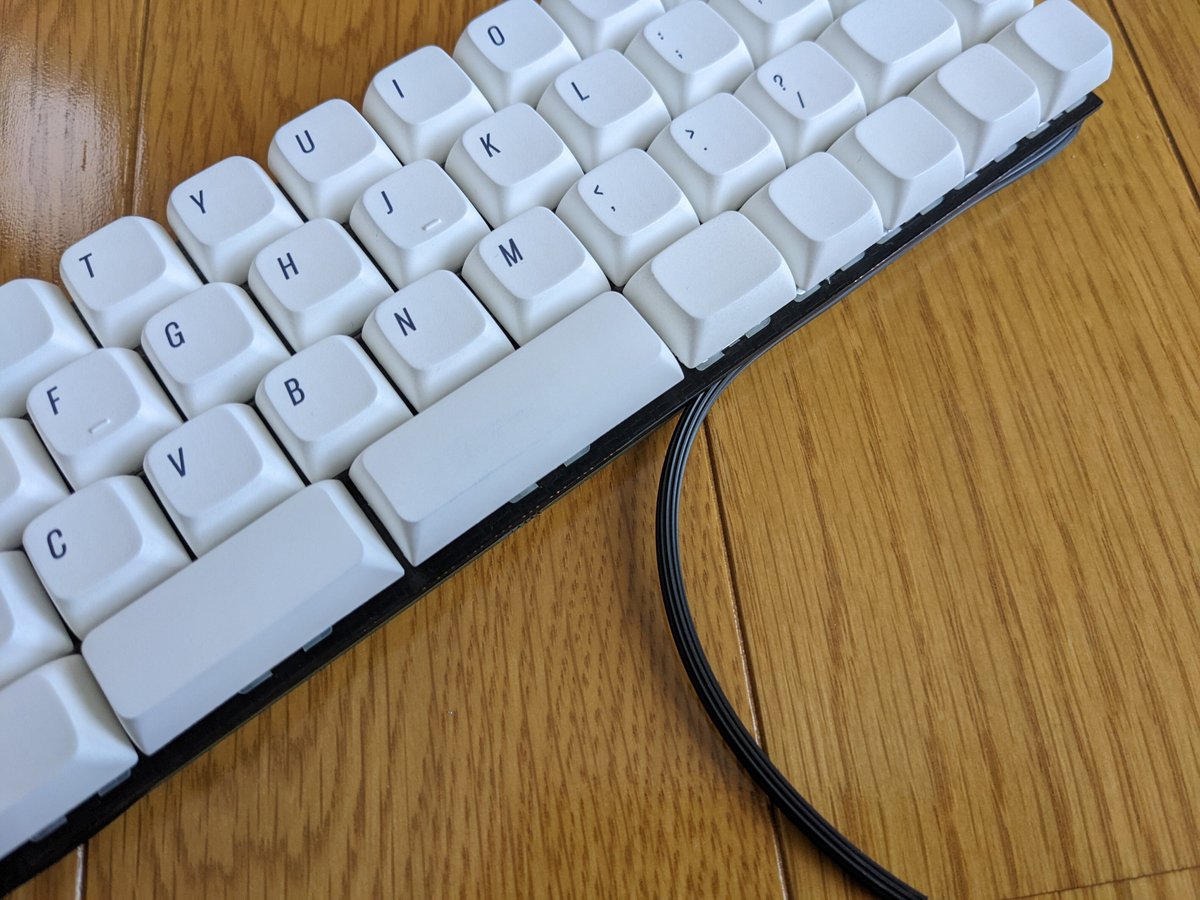
そのまま巻くと中空構造でゴムが潰れ過ぎるのか、3.5mm径のゴムだと基板の外周に適度にはみ出さずケース側にうまく接地しませんでした。
そこで、家に転がっていた太めの水糸(凧糸)を2周ほど巻いてかさ増しした上からゴムを巻き付けることにしました。
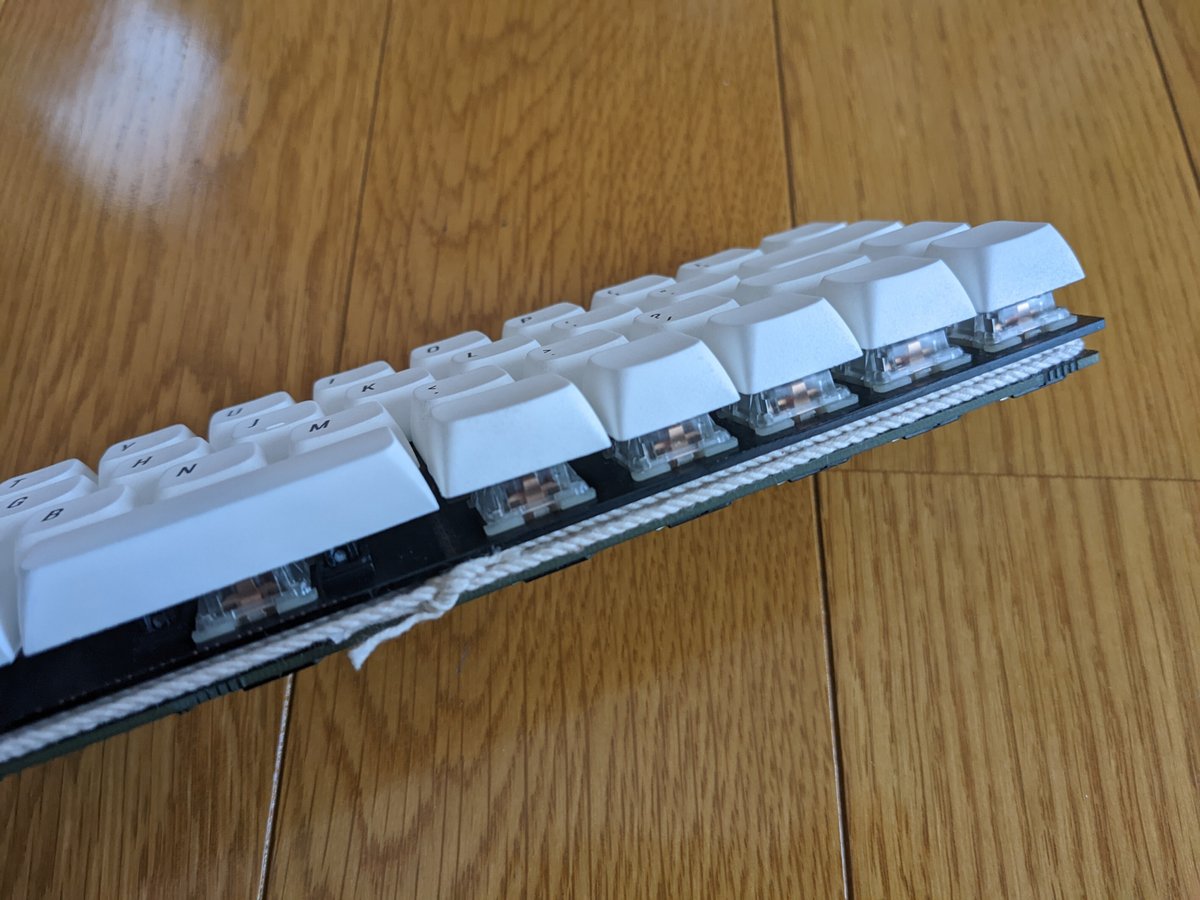
これで適度にゴムがPCBの外形からはみ出し、ケースに固定できるようになりました。ケースの内側にしっかり均等に配置できており、打鍵したりひっくり返してもずれることはありません。キースイッチの交換作業も問題なく行えます。
まだ実験していませんが、4.5mmや5.5mmなどの太めの押さえゴムであれば水糸を巻き付ける必要なくケースに接地できるかもしれません。
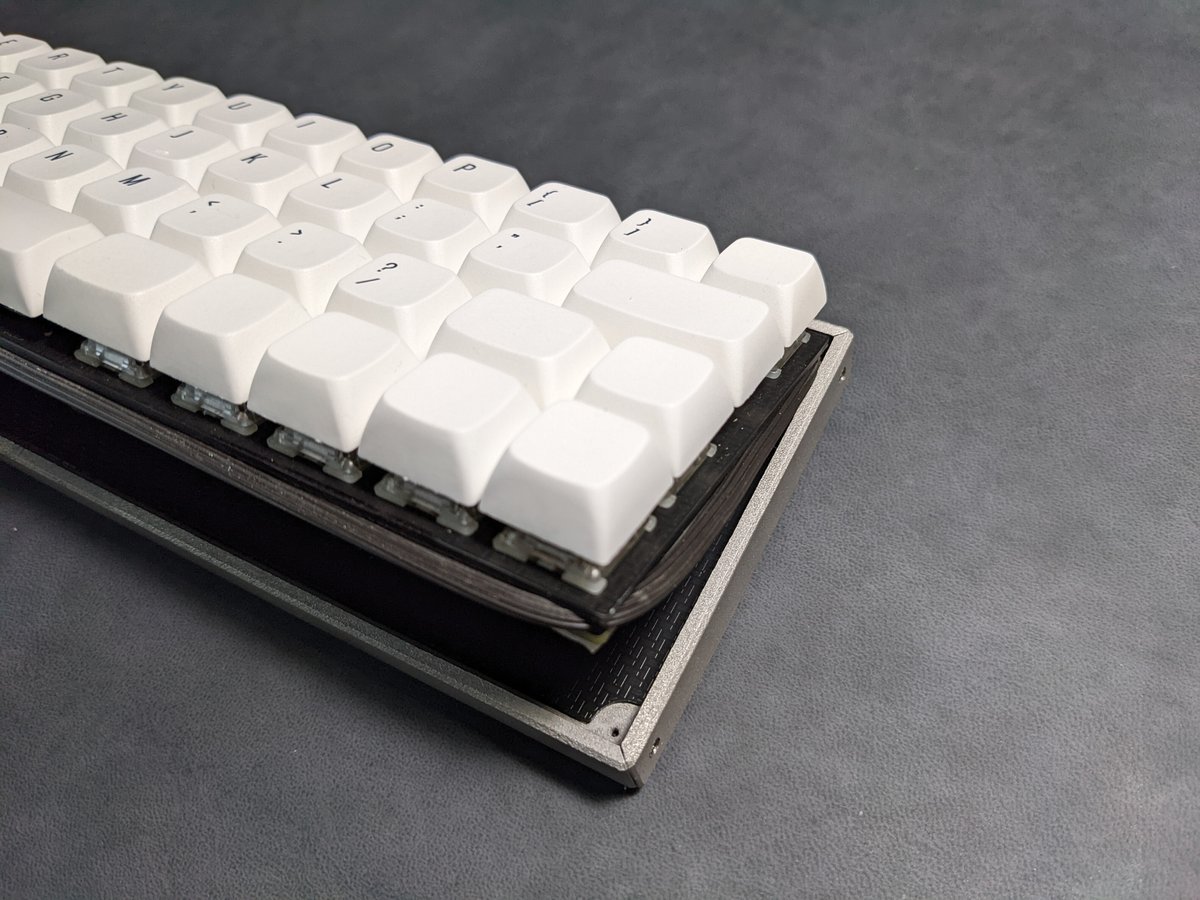
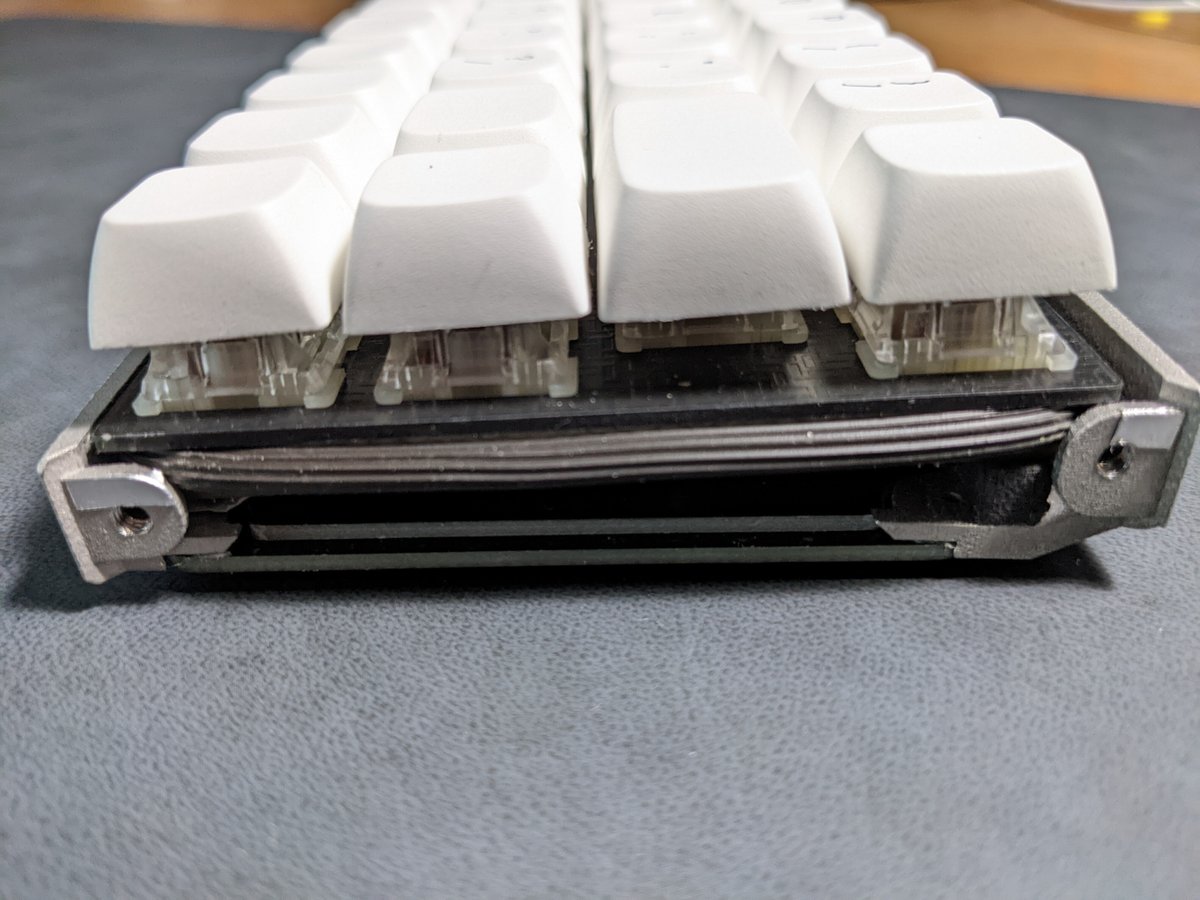
完成したキーボード 「inn v2.1」
外観
完成したキーボードの全体像は次の通りです。ベゼルの幅も好みの薄さになり、変更に至った以前のケースの不満点を解消できました。ステンレスの色味に関しては予想外にとても渋く、めちゃくちゃ好みで気に入っています。
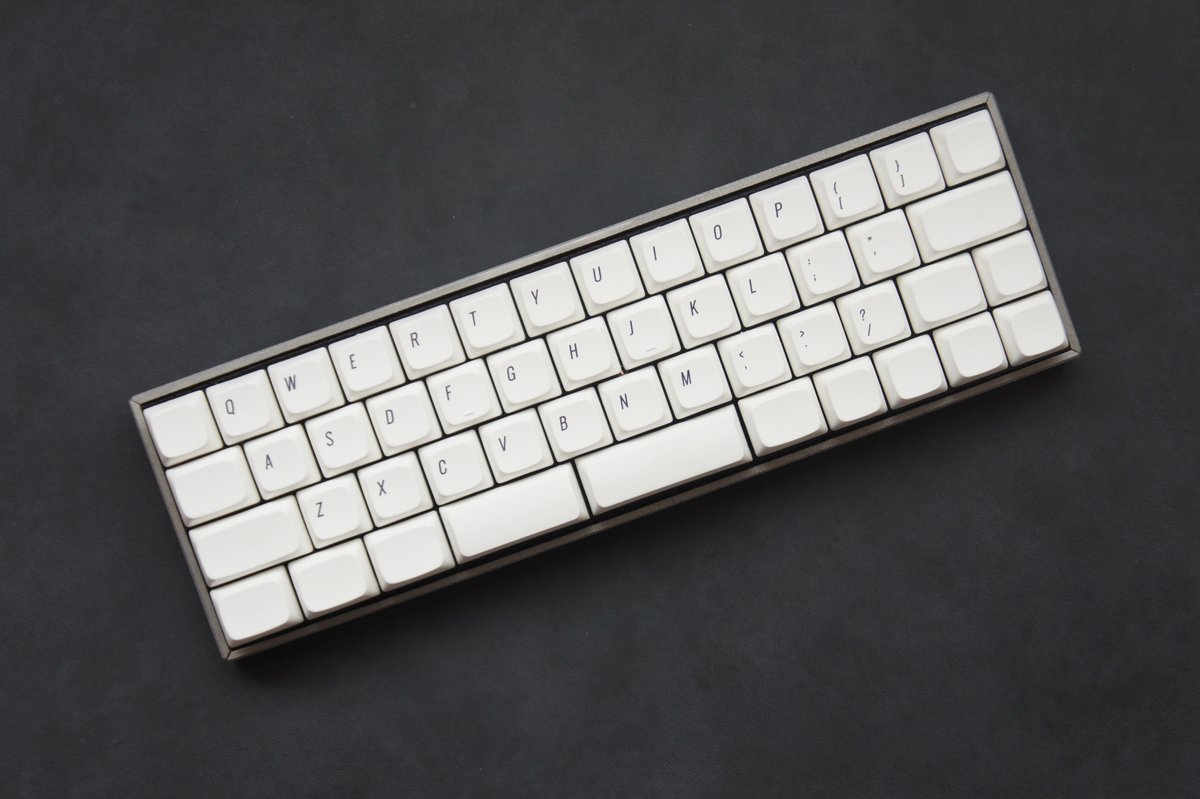
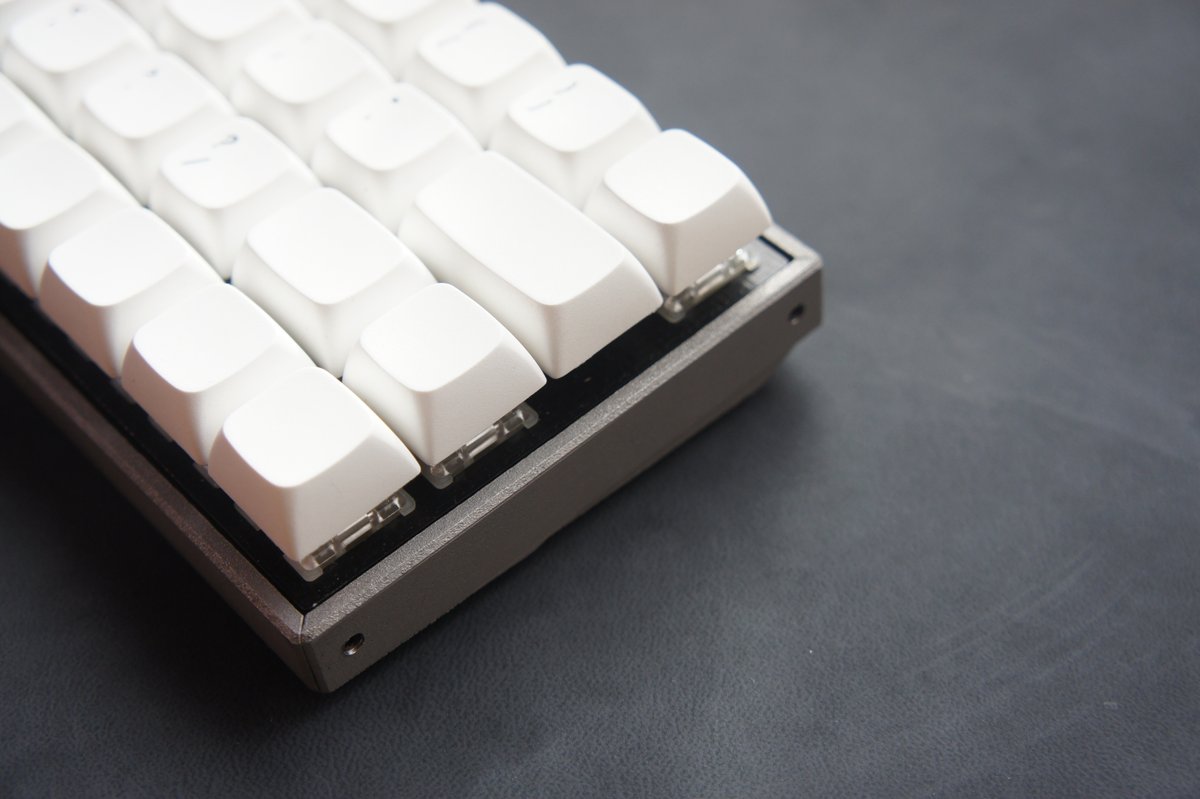
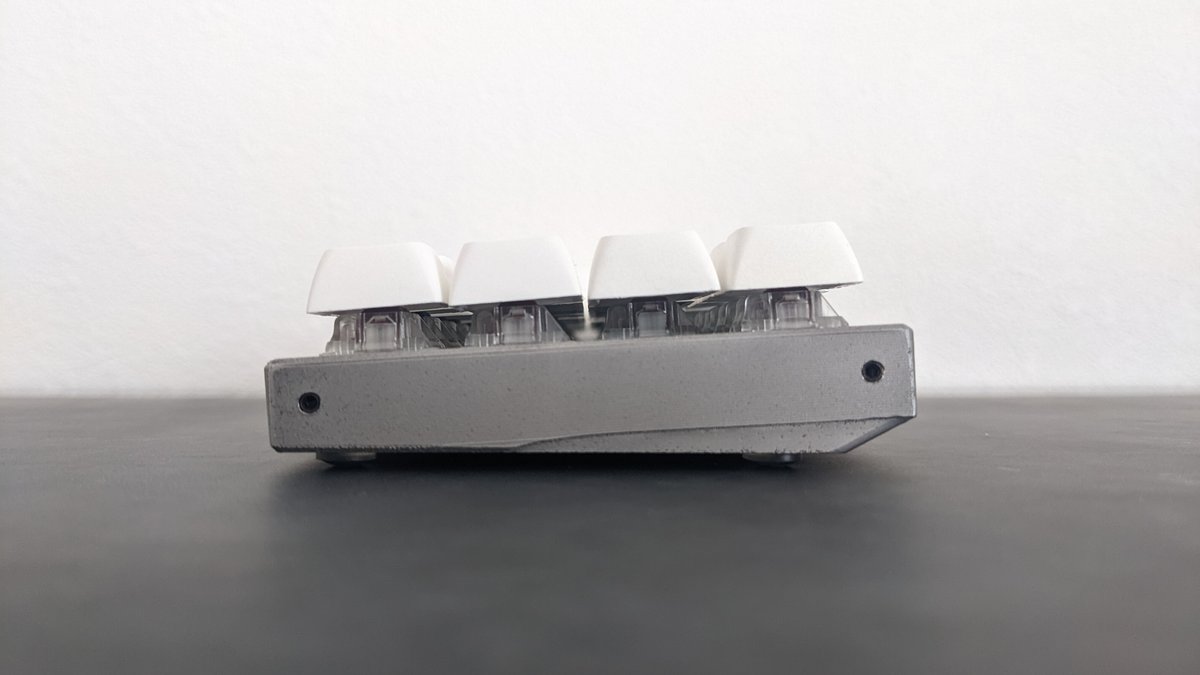
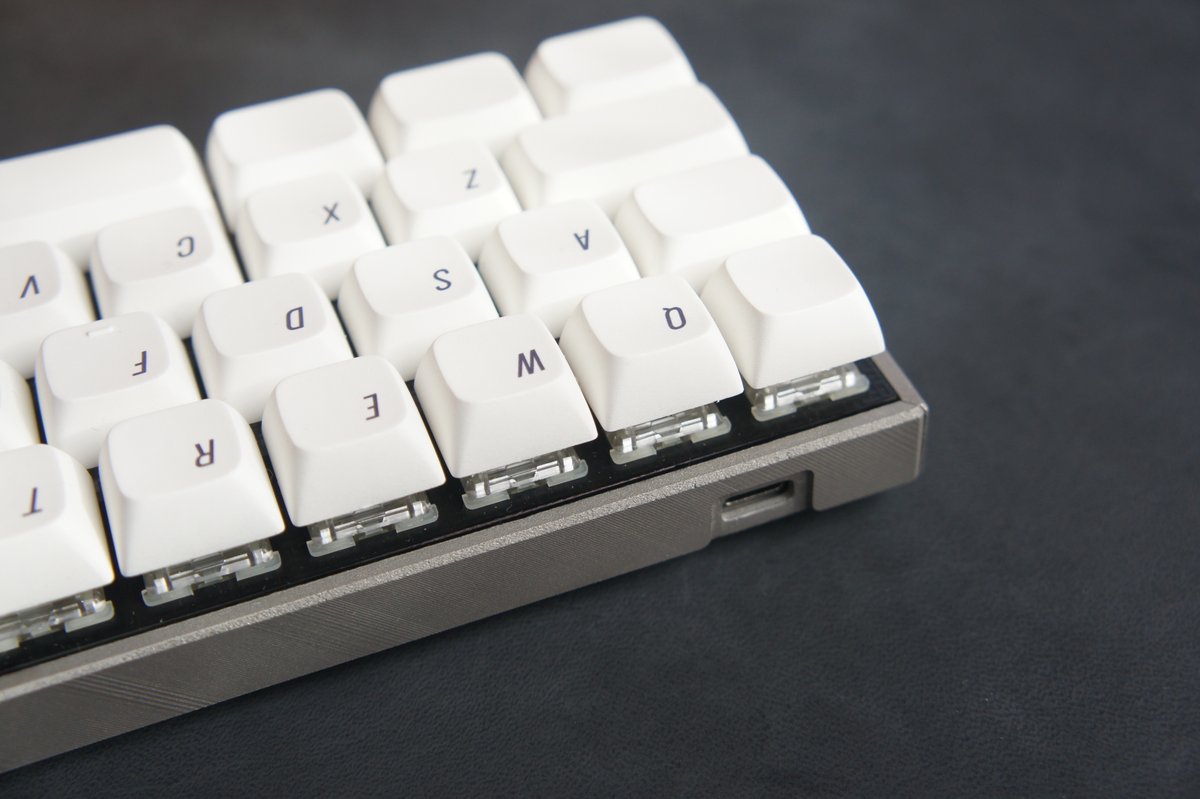
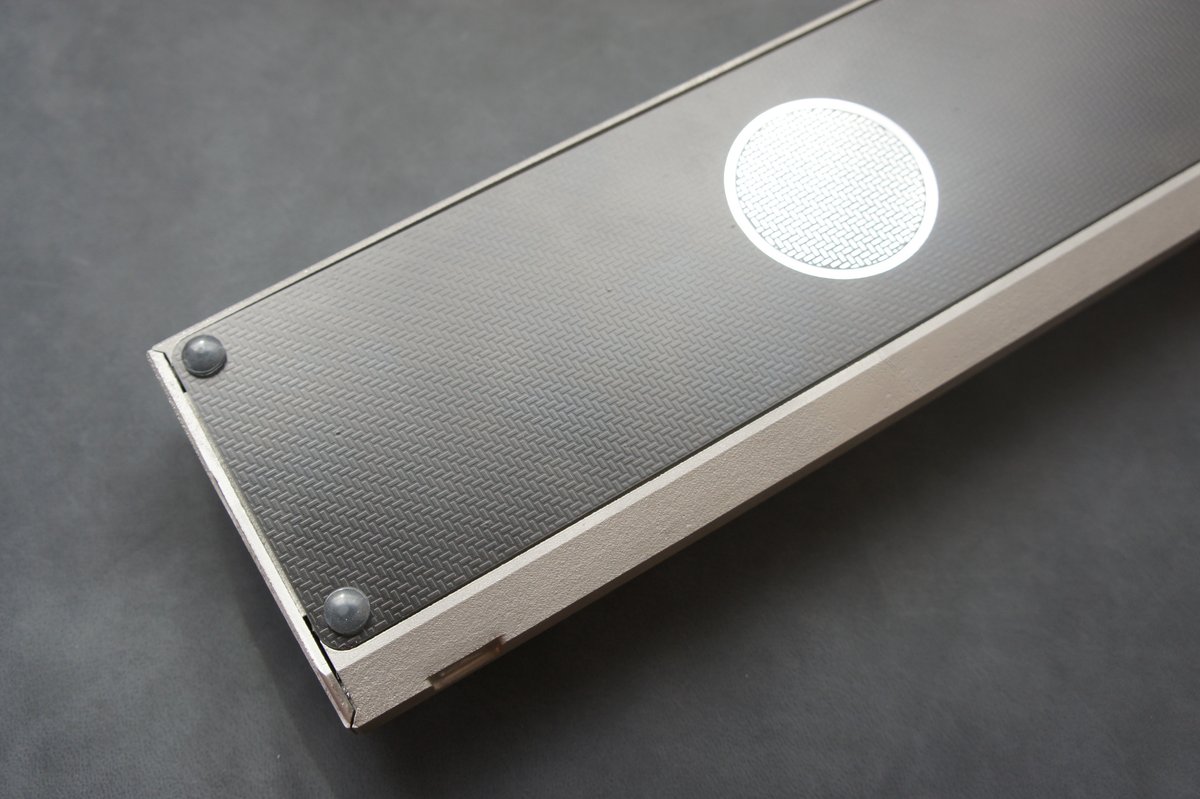
(追記1)配列は次のようになっています。意図や狙いについては前回の記事にまとめてありますので気になった方はチェックしてみてください。
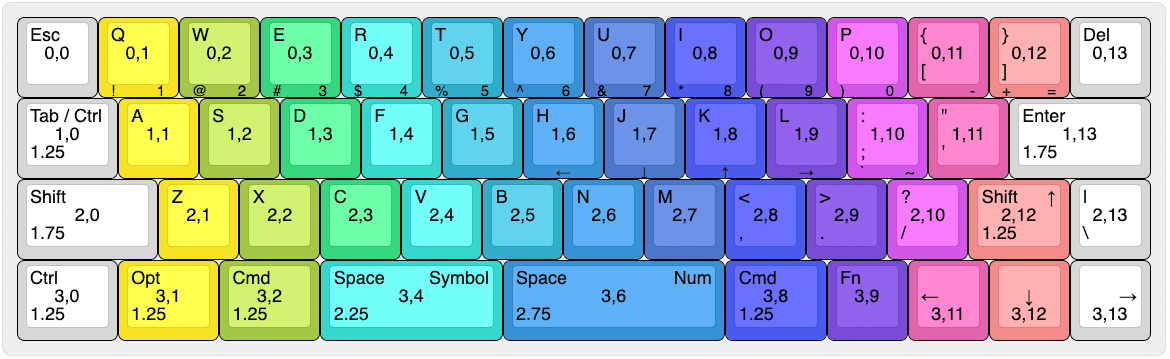
完成後の感想
今回のケースはアルミアングルを加工して作った最初の試作ケースのサイズ感をベンチマークとしています。結果的にはほぼ同じサイズで重量の大幅アップを果たし、安定感と剛性を獲得することができました。
材料は5mm*15mm*1820mmのL字アングルを一本買ってきて、手前側と側面のフレームを適宜カットすればチルトしたフレームになるというお手軽仕様(加工に伴う体力消費は無視するものとする)👨🔧 pic.twitter.com/6HfS1jYz8d
— copkbd (@copkbd) August 22, 2022
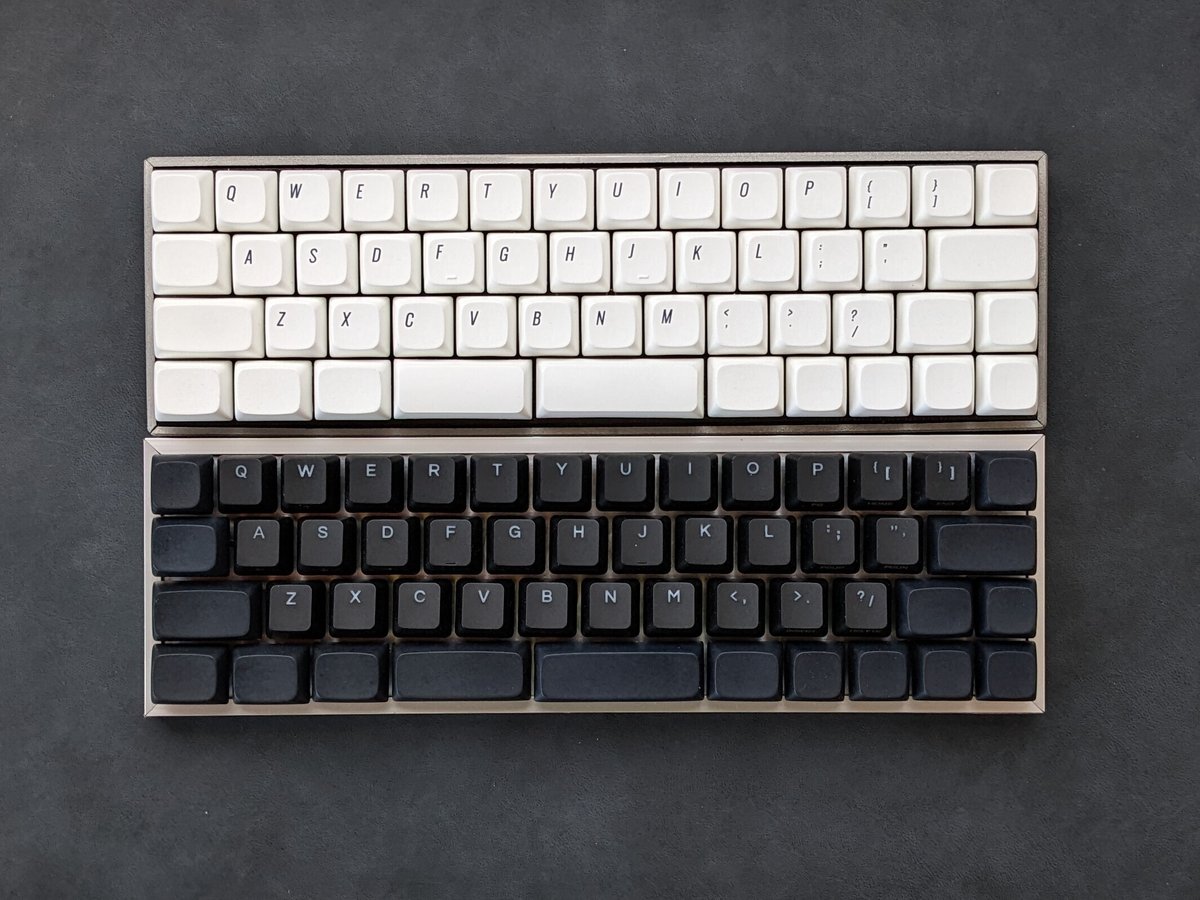
私個人としてはアルミ切削によるケース製作が最終目標ではありますが、販売目的がなく、完全個人用途であれば金属3Dプリントによるケース製作で十分であると感じました。
何よりもベゼルが薄く高さも押さえたコンパクトなこのキーボードですが、比重の関係でここまで重量のあるものに仕上がったのは想像以上の満足感につながりました。案外アルミ削り出しでこのデザインのまま作ってしまうと重さに不満が出てしまうかも、というのは発見でした。
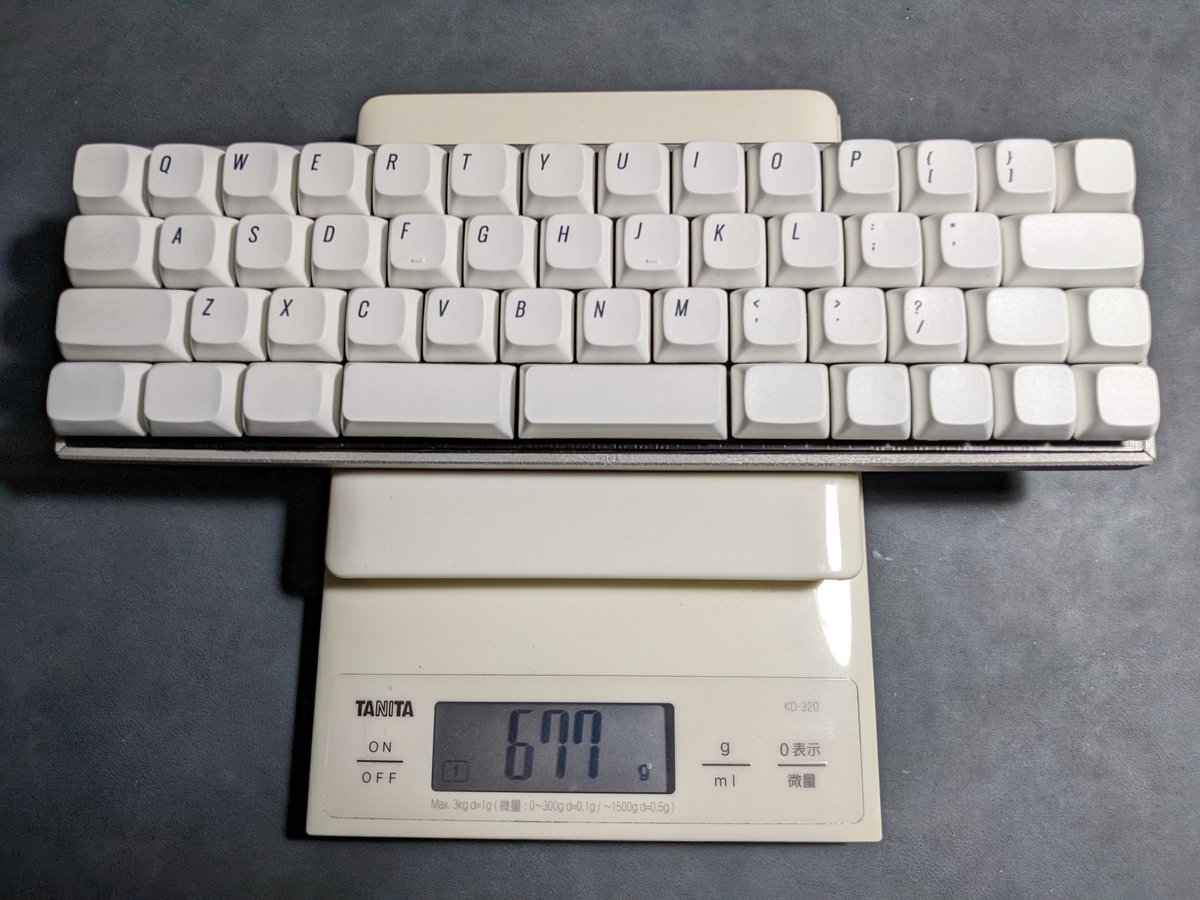
今回は予算の都合もあり底面を開放したフレーム状のケースにしたため分割プリント+組み立て作業が発生しましたが、一体で出力が可能なのであれば精度・剛性・重量全てのクオリティがアップすると思います。
ただ出力エリアの都合上、長辺がZ軸方向300mm もしくは 250 x 250 mm のステージの対角線サイズまでが限界になるので、分割しない場合は65%くらいまでが限界になるかもしれません。
もし興味のある方は金属3Dプリントによるケース製作にチャレンジしてみてはいかがでしょうか。
今回私がPCB製作と3Dプリントを行なったJLCPCBでは新規会員向けの総額$54クーポンも配布しています。是非利用してみてください。
次はこのケースのチルト角度(3.4°)に合うキーキャップ作りをしようかな…?
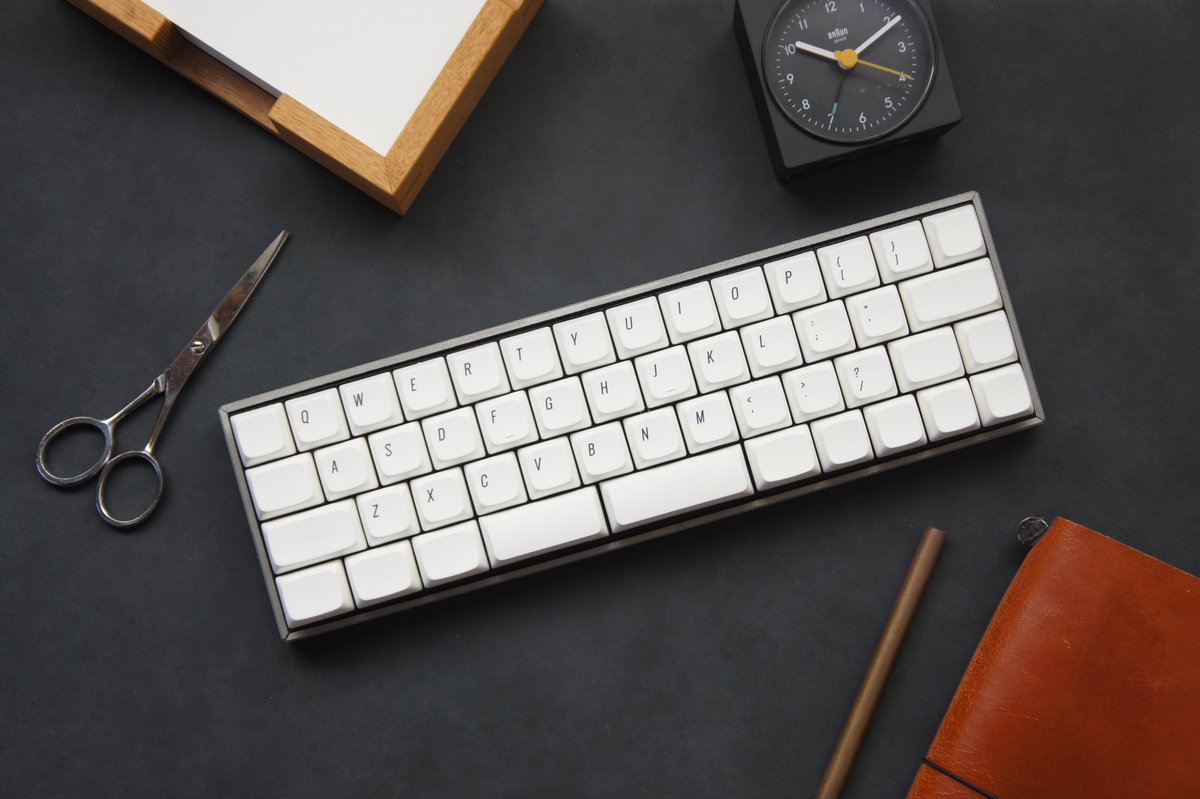
この記事が気に入ったらサポートをしてみませんか?