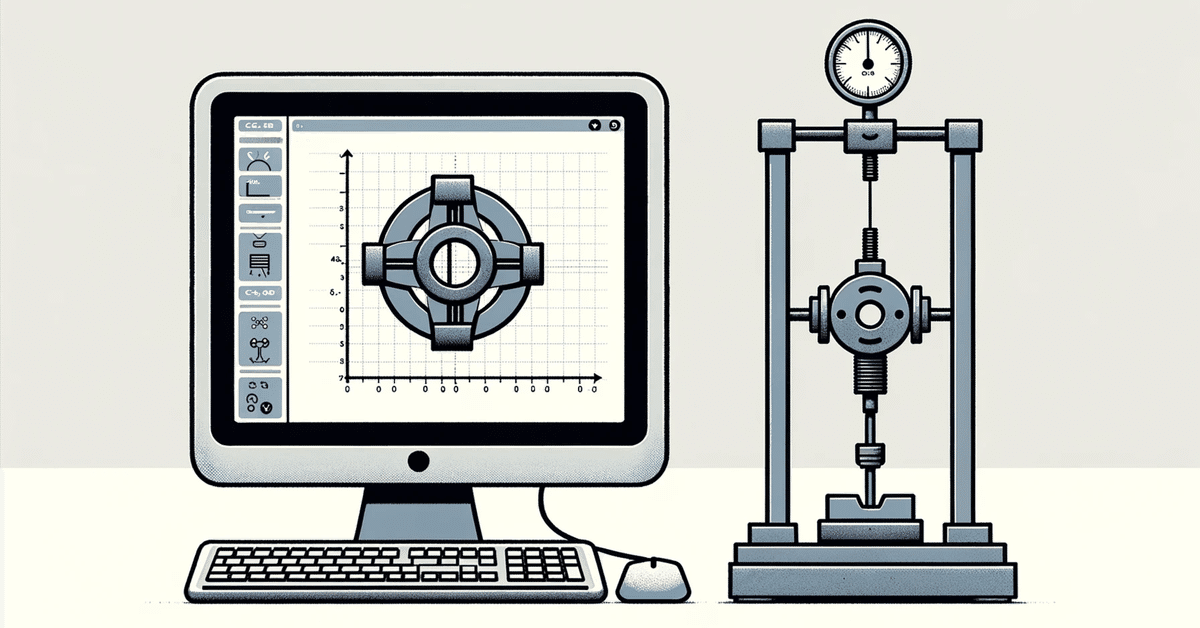
CAE解析の精度
CAEはコンピュータを使って製品の挙動をシミュレーションし、その性能や信頼性を評価する手法です。しかし、CAEで得られる結果と実際に行われた試験結果がいつも完璧に一致するわけではありません。構造解析の場合、この一致度は大まかに以下の3つの段階に分けられます。
精度の分類
評価不可能:
解析結果と実験結果がまったく異なり、形状や条件を変更した際の傾向も一致しません。
相対評価可能:
結果が大まか(最悪の場合でも30%くらいに収まる程度)に一致し、形状や条件の変更による結果の傾向も合致しています。絶対値での評価はできませんが、設計案の選択や原因分析に基づく設計の改善が可能です。
絶対評価可能:
結果の差が数%以内に収まり、傾向も一致しています。実験を解析に置き換え、実験回数を大幅に減らすことが現実的になります。
精度に影響する要因
この問題は通常、"CAEの精度"という言葉で議論されますが、この精度は単にCAE解析の手法選択や数値計算精度だけでは決まりません。言い換えると、ソフトウェアに精通したCAEのエンジニアがメッシュを細分化するだけでは精度は向上しないのです。
解析では、モデル化の際に結果に影響する要因を考慮しきれないことがあります。例えば、繰り返し荷重による材料の変化や、温度や摩擦の影響がそれにあたります。これらを全て考慮したいと思っても、ばらつきを排除した正確な繰り返し荷重下の材料データや、温度ごとの材料データ、摩擦係数データを取得することは困難であり、モデルも複雑化します。そのため、主要な要因だけを考慮したモデルで解析が行われ、無視された要因が誤差の原因となることがあります。実験にも誤差は存在します。寸法や材料のばらつき、固定部のすべりや荷重方向のずれ、ひずみゲージの大きさによる応力勾配の平均化や較正の問題など、測定の誤差も考慮する必要があります。特に、塑性や摩擦などの非線形現象を含む解析や実験では、これらの誤差が顕著に現れます。
精度の向上
これらの問題は改善可能です。精度に影響を及ぼす現象を正確に把握し、必要なデータを適切に取得し、誤差を考慮した統計的なアプローチや工夫された解析方法や実験治具、精度の高い非接触測定方法などを導入します。しかし、これらの改善策を実施するには時間とコストが必要です。特に、非線形性が強い場合には、絶対評価を目指すことは効率が悪く限界があるので、相対評価がよく利用されます。
適切な利用
相対評価の場合でも、誤差の原因を推定し、可能であれば特定しておくことが望ましいです。これにより、モデルの適切な適用範囲を見積もることができるだけでなく、今後の精度向上の必要性や方向性の判断ができます。"CAEの精度"に対する不満はあっても、その限界を理解して適切に利用することが、効率的な製品開発に役立つのではないでしょうか。
この記事が気に入ったらサポートをしてみませんか?