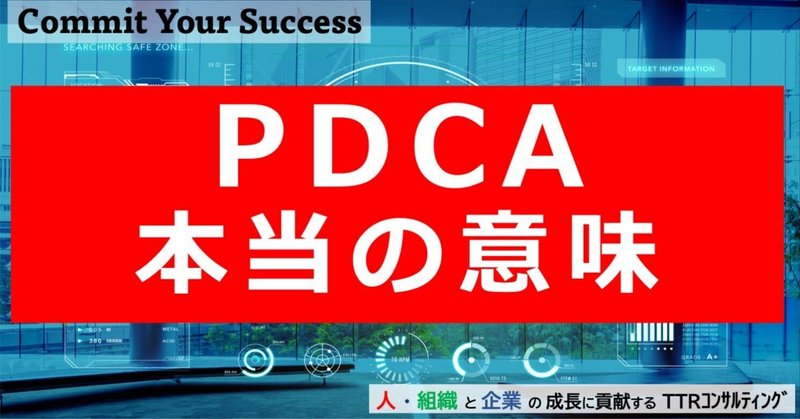
みなさんは、PDCAをご存知でしょうか?
ビジネスの世界でよく聞く言葉なので、知っている方も多いと思います。
それを説明してって言われると、どう説明されますか?
PDCAってどうなの?って聞かれたら、どう答えますか?
あなたの仕事、ビジネスにPDCAっていう考え方は役に立っていますか?
結論から言うと、
成果を出したいのなら、PDCAは必須です。
本当の成果を出すには、出し続ける自走状態にするには、PDCAしかありません。ご自分のためにも、間違った理解を捨てて、PDCAの本当の意味を知って活用してください。
ビジネス、仕事において、PDCAは、もっとも基本となる考え方であり、成果を上げる重要な手法です。
本当に成果をあげたいのならば、PDCAの意味をしっかりと理解して活用してください。
私たちは、正しく理解していただくために、
PDCA ではなくて、R-PDCA としてご説明しています。
本来のPDCAには、作業として含まれていましたが、ものづくりの現場から一般ビジネスに適用範囲を広げる時に、文字通りのPDCAで理解されたため、誤解が生じています。
ということで、私たちは、本来の意味で含まれていたRを明示するように、頭につけました。もともとのPDCAと中身は同じです。
PDCAの前に重要でどんな仕事にも必須のR(Research)をつけています。
これは、単なる情報収集ではなくて、目的(不良撲滅)達成のために行う情報収集→(仮説)→分類→分析→仮説→補足データ→仮説確立などの流れを言います。ポイントは、何のためにの意味を持って作業することと、それが達成できると思えるところまで情報を追求していくことです。
詳細を説明していきます。
まず、正しく理解して活用しましょう。というのが、今回の目的です。
時代と共に本来の意味が変わってくることは、多くあります。
時代の変化に合わせて、元々の目的達成を変えずに意味を変えていく。
それは間違っていません。
私たちの会社は、働くすべてのみなさんの努力(作業)が確実に成果につながるコーチングをしています。
多くの企業様で、このPDCAの誤った理解が邪魔になることがありました。
今回、その当初の目的も併せて、このメソッドの原理を知ることで、確実に活用できるようにしていきたいと思います。
もともとは、戦後の復興に向けて、アメリカが日本のものづくりに危惧を抱いたことが始まりです。
戦後、先を走っている西欧諸国の工業製品(技術)を一生懸命に真似して同じようなのを作ったのですが、なにしろ品質が悪かった。
日本人の器用な手先、細かなところも見落とさない繊細さ、そして少しでも良いものをという真面目な勤勉さなどの特徴で、真似して作ることができました。真似して作ること、これだけでもすごいことだと思います。
ただ、品質が悪く、アメリカでは、安かろう悪かろうと言われてしまいます。
日本の復興のためには、この品質をどうにかする必要がありました。
そこで、先生になったのが、デミング博士です。
だから、PDCAは、ものづくりの場から出た考え(メソッド)です。
目的は品質を上げることです。
このやり方は、ビジネス一般にも使えると言うことで、ものづくり以外でも広まっていきました。
そもそもコンサルの起源は、ものづくりの生産性向上でした。
PDCAも、作業を成果に繋げるという仕事の本質と言う意味では、ものづくり以外でも使えるのは当然だと思います。
今回のテーマ、本当は、このデミング博士の初代のお弟子さんたちにご説明していただくのが一番良いとは思います。もし、ご覧になっている方がいらっしゃいましたら、ご連絡ください。ご指摘ください。補足してください。
私は、その初期の日本側の対応した大学の研究室のメンバーで、のちに小西六写真工業(→コニカ→コニカミノルタ株式会社)の社長になられた米山さんに教わりました。
(デミング賞も受賞されています)
私は、複写機開発の部署に配属になりましたが、入社後すぐに品質委員(当時はQC委員と言って、多くの企業でQCサークル活動が盛んにやられていました)となりました。もちろん製造のメンバーが多いのですが、私は、開発で最初のQC委員でした。
設計品質/製造品質/市場品質、製造品質から着手して設計品質に取り掛かる頃だったのだと思います。全社活動として全員参加でした。
そこで、まだ社長になられる前の米山さんに、ニコニコと、でも厳しく徹底的に教えていただいたことをお伝えしたいと思います。
さて、PDCA、PDCAサイクルとも言われますが、これってなんでしょうか?
P(Plan:計画)→D(Do:実行)→C(Check:評価)→A(Action:改善)
と一般的には、言われています。
私たちは、少し違っていて、C の Check は、『評価』ではなくて、『検証』としていました。理由は、後で説明します。
そして、A の Action は、『改善』でいいのですが、口酸っぱく言われていたのは、『対応』でした。すぐ対応、です。そしてその対応の結果をもって決定し、改善に繋げます。詳しくは、のちほど、、、
ここで整理すると、PDCAは、こうなります。
P(Plan:計画)→D(Do:実行)→C(Check:検証)→A(Action:対応)
ただ、PDCAは、これで終わるのではありません。
PDCAって、違う言い方で、PDCAサイクルって言いますよね。
PDCAとだけ言っている場合でも、説明のなかでは、『回せ』と書いてあります。そうなんです。
PDCAって、一回で終わらせるものではなく、何回も回すつもりでやります。(結果的に一回で終わることは、あります)
なぜなんでしょうか?
ここで、もう一度、PDCAの目的に戻ってみましょう。
PDCAは、品質を上げるためでした。
では、品質を上げるとはどう言うことでしょうか?
それは一生懸命に心を込めて作ったものが、品質不良とならないことです。
言い換えると、その決められた作業をちゃんとすると良品になると言うことです。
ここで、一つだけ補足すると、
品質には、ここで取り上げている製造品質とは別に、設計品質というものがあります。設計とは、製品設計(私は商品設計の言葉の方が好きですが)と製造設計(作業工程や治工具、ツールや機械、レイアウト、環境などを含めたもの)があります。多くの場合、製造設計も、製造品質の中に入ります。
多くの場合とは、製造方法そのものも考慮して商品設計するのが、本当の設計なので、開発する側から言うと、製造設計も基本設計のところは開発責任だと思っています。
製造は、人や機械がただ作業することだけをいうのではありません。
で、今回は、製造品質(作業だけではなく、ツール、治工具、機械、作業者、環境、など全てを含んでいます)の全体でお話しします。
製造部門は、決められたやり方で作ったら良品になる。
これを目指しています。
つまり、最終的には、絶対に良品しか作れない『OKレシピ』を完成させることを目標にしています。
製造業の目的は、その商品によって、お客様に幸せを届けることだからです。つまり、届けたものは、お客様と明示的の有無に関わらず合意した品質を発揮することが絶対だからです。
そのOKレシピを作り上げるために、改善していくことになります。
量産できるレベルまで検証された方法で作っていても、工程の途中や、検査工程で、不良を見つけることがあります。
お客様との約束なので、それらは出荷しません。
ですが、製造業は、お客様との約束をその一つの商品だけで見ていません。
あるお客様に対して、不良品を出さないのは絶対ですが、そのつもりはなくても不良品を作っていると言うことは、作業の無駄を発生させていると言うことです。お客様が自分では作れないから、自分で作る時間がないから、で代わりに工場でプロがお客様が作るよりももっと良いものを、もっと工数少なく作る。
だから、製造業は、不良品を工場から出していない言って、そのままにしているのは、プロではありません。お客様たちに対しての責任放棄です。
と言うことで、最終工程での検査を強化するのは、品質向上のための作業や対策ではありません。市場に対する責任ではあります。
工場内での不良につながる要素を徹底的に排除する必要と責任があります。
一つの不良を見つけた時に、どう改善しますか?
例えば、ネジの締め忘れ、ちゃんと締まっていなかった場合です。
品質をあげられない工場は、これを現象だけでとらえます。7
ネジの締め忘れ、、、
作業者は誰だ? ちゃんと閉めろ! 締めた後に確認しろ!
属人性だけで、現象を対応しようとします。
人って、1日の間に何十もの失敗、ミスをすると言われているそうです。
気を付けるようにすると、確かにミスは減ります。
しかし、無くなることはありません。時間が経つと元に戻ります。
不良を本当に撲滅したいのなら、現象だけで捉えてはダメです。
ここで、必要なのは、『原因』です。
そしてポイントは、原因って一つじゃないことです。
日々のミスを例にするとわかりやすいと思います。
カフェでコーヒーをこぼした時、確かにずっと注意していればこぼさなかったと思いますが、、、
紙コップだったから、、、通常のものなら意識せずに持てた
思ったよりも熱かったから、、、スマホ見ながら持とうとして
パソコンを動かしたら、、、見えないところに置いていた
玄関の鍵をかけ忘れた
出る時に電話がかかってきて、+〇〇〇
出る時に今日の会議のことを考えていて、+〇〇〇
QC活動では、発表会を基本とした活動をしていました。
そこで徹底的に言われたこと、そして、発表のフォーマットに落とし込まれたそのキーワードは、『原因は一つじゃない』です。
不良撲滅の手順は、こうです。
(QC活動での流れです)
1. まず、無くしたい不良を選びます。 例:欠品(部品のつけ忘れ)
2. 現状を調査します。(1の選ぶ時にやっている内容とかぶります)
3. 現状調査は、その発生頻度、影響度(損失)と特徴。
特徴とは、他の不良、発生時期、発生頻度の変化、環境(5M+E+M)
4. 原因の仮説を立てます。対策の仮説ではなく、原因の仮説です。
その原因を確定するために、対策を仮定することはあります。
5. 仮説検証します。実際の量産での検証の前にシミュレーションします。
この仮説検証で、対策と思えるものを選びます。
または、原因を特定できない時は、幾つかの推定原因ごとにその特徴を整理して、特定するための作業案を考えます。
6. 5の結果から、P(実行計画)を立てます。
原因を確定するための実行計画、もしくは、その原因の起こるための原理を確定する実行計画(=対策も決定できる)、この2つに分類できます。
7. 実行計画には、その実行によって、結果を判断に使えるだけの根拠をもてるようにして、実行します。つまり、5M+E+Mの中で意図せずに変化しているものを排除しておきます。簡単に言うと、実行計画で意識的に変えたもの以外は、検証できるように発生時と同じ環境で実行するということです。
8. 結果を検証します。
検証は、原因、原理、対策、有効性、効果、展開、および関係性可視化となります。
9. 検証した結果が、完全にゼロになっていない時は、追加でデータから原因を推測し繰り返します。
原因には、直接原因、間接原因、複合原因、いろいろな原因があります。
原理を見抜いて、この原因キーワードを意識して完全解明を目指します。
10. で、PDCAのPに戻ります。
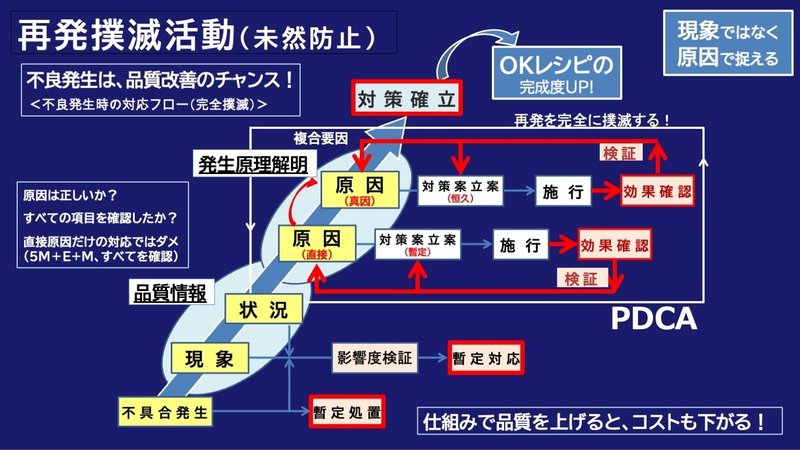
というように、現象を潰していくには、現象ではなくて、原因を解明して潰していく必要があるので、PDCAを回すと言います。
言葉の上っ面だけを見て、作業だけしか見ずに回しているつもりになっていると、達成できません。
PDCAを回すのは、不良撲滅のための原理解明・確定した上での対策決定のためです。
だから、改善は、一回のPDCAでできるのではなくて、(一回でも少しは改善しますが)何回か回した上で、対策(つまり5M+E+M決定)を決定することにより実現します。これをOKレシピと言います。
PDCAを回すの本当の意味は、不良撲滅の目的達成にための原因・原理・対策確定のためでした。
推測したときの考えの根拠と検証がとても大事です。
全て、有無を言わさないデータで語ることが重要です。
PDCAでもうひとつ誤解されているのが、
Pの前にDだろう!って言うものです。
もともとのPDCAの本当の意味を知らないとP(計画)を最初に作らないと行動できないと思ってしまいます。
そして、人の本能として、『何もしない』と言うのがあります。
何もしないというのは、文字通りにじっとしていると言うのではなくて、やらなければいけないことではなくて、成果につながらないことをやってしまうと言うものです。
テスト前の夜に、勉強しようとして、思わず本棚を整理してしまうようなことです。
やる人だけではなくて、リーダーや推進者がPDCAを正しく理解していないと、文字通りの最初のP=Plan(計画)を真面目にやっていくことになります。
PDCAは、もともと製造の現場で発生している不良、不具合をなくすために使われていた手法です。発生している不良をなくすための手法であるので、すでに発生している、その時の情報がある、だから、推測すること=P(計画)の前に、必ず情報収集と戦略・戦術、実行計画へつながるフローがあります。
そして、量産は、毎日あるので、そんなに時間をかけてられません。
P(計画)を立てるための作業を実地で行います。
机上の作業で延々と計画を立てるのはPDCAのやり方の中ではありません。
ポイントは、行動です。
計画後の実行は、もちろん重要ですが、計画前の行動が重要です。
情報、データも、意味のあるものでなければ使い物ではありません。
また、今ある情報を整理するために、足りない情報を取るために、すぐに行動します。時間がもっとも重要な要素です。
不良の原因を探るために、前工程、前々工程、次工程、、、通常は入れていない検査作業を行ったり、作業時間や撮影をしたりして、初めて計画を確定します。
計画を立てる時に机上だけでやることはありません。
そして、計画完成した時は、それを計画通りに実行します。
計画の立て方を誤解されています。
これらを全てのビジネスに当てはめられると思った方々が活用していきました。最初に活用された方々は、もともとの意味を理解されていたと思いますが、PDCAの表面上の言葉の意味だけを説明して、ポイントの一つである『回す』をその意味がわからずに広げていったからです。
PDCAの正しい作業フローを理解して、すぐに行動しましょう。
成果を出せないのは、PDCAの手法が間違っているのではなくて、正しく理解せずに上辺だけの作業しかしないためです。
少し補足が必要なのが、製造の現場で使うのではなくて、いろいろなビジネスの現場で使う場合の必要な対応です。
新規事業や新規プロジェクトのような場合は、この製造業で使われていたPDCAとは少し意味が異なりますが、本質は同じです。
成果を出すには、次の三つの要素が必要です。
成果=ストーリー ✖️ 行 動 ✖️ スキル
このストーリーが間違えていると絶対に成果(不良撲滅や新規事業たちあげなど)は出せません。
ストーリーは、よく言われている『やること』ではありません。
成果を出すには、やること、ではなくて、失敗する条件を全て考慮することです。やってはいけないこと、やらないといけないこと、失敗する条件、これらを明確にし、対応策を考慮したものがストーリーです。
映画やゲームの脚本のように、うまくいく前提で工程を繋げてはいけません。
うまくいかない時を想定して、それを潰し込むようにストーリーを作り上げます。
計画の段階で、あたり検討などを行い、確立します。
不良発生の原理を掴んで活用します。
ビジネスでは、仮説を立てることがとても重要です。
間違っていてもいいので、根拠となるデータとともに仮説(つまり原理)を立てましょう。そして、いろいろなデータを突き合わせて仮説検証を行い、時には追加データを取って検証します。
その時に、辻褄が合わないようなデータが出ることがあります。
その属性、それらのいろいろな環境情報を見比べて特性を掴みます。
失敗する条件がわかれば(想定でも)、それを考慮したストーリを作ります。一筆書きのようにやることを繋げていくのは計画とは言いません。
成功させるためには、失敗する条件を考慮して作ります。
キーワードは、課題、制約、前提、方針、、、などです。
場合によっては、法令や各国の認可条件、特許なども含まれます。
最近では、環境問題などもあります。
これらを明確にしたストーリなので、実行途中でも常に検証できます。
検証しながら進めるので、対応も迅速に行うことができて、成功に繋げられます。
このビジネス成功の極意としてあるものって、
大きく言えば、R-PDCAです。
最終的にOKレシピ、つまり、その作業をやれば必ず想定している成果が得られる、その状態にします。
そうすれば、作業に落とし込んだことになり、時間の読めない考える行為と切り離せます。
成果を出すには、失敗をきちんと分析し、原理を見つけストーリに落とし込みます。
勝ちに不思議の勝ちあり、負けに不思議の負け無し。
知っている原理を考慮して、R-PDCAを活用し、成果を出してください。
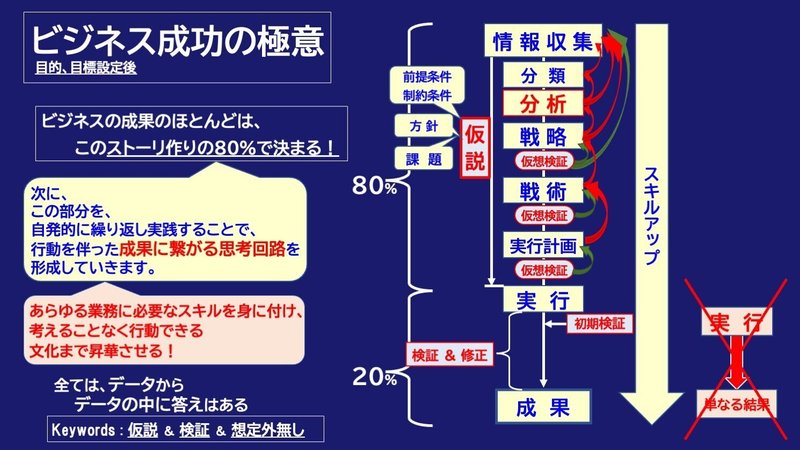
PDCAをまとめると、
1. 計画は、根拠を持って作る。
その根拠は、不良発生時の生の情報。この時、スピードが大事。
まずはすぐに着手する。計画を作るために行動する。
2. 回すのは、目的達成のために全ての原因(原理)を確定するため。
だから、単に回すのは、囚人の穴掘りと同じで、意味もなく、徒労だけが残ります。確定できたら、OKレシピも完成しています。
3. 何度か回したのちに原因を確定したらOKです。
その時の対策が、『改善』と呼べるものです。
その改善が、その時点でのOKレシピです。
色々な手法に惑わされずに、人の心理、物事の因果の原理、行動の原理、これらをしっかりと見て仕事をしてみましょう。
自分のために、自分の労力を無駄にしないために。
このやり方で、社内外で成果を出せない案件ばかりを引き継いでいますが、
成果を出せなかったことは一度もありません。
ぜひ、ご活用ください。
成果を出したい方、ご質問、ご指摘、できる限り対応させていただきます。
この記事が気に入ったらサポートをしてみませんか?