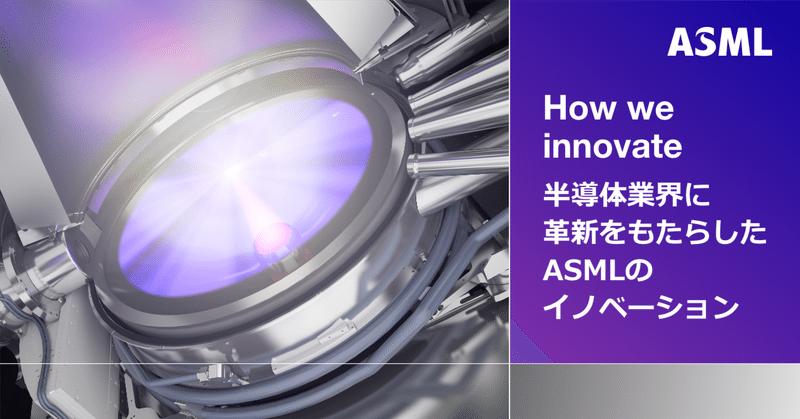
【How we innovate】03:半導体業界に革新をもたらした、ASMLのイノベーション
こんにちは、エーエスエムエル・ジャパンです。
この記事では、ASMLに興味を持ってくださった読者のみなさまへ、
「私たちが生み出してきた”イノベーション”を知っていただきたい。」
「より深くASMLのことをご理解いただきたい。」
そういった思いから、半導体の歴史や私たちが作る”露光装置”について、解説する内容となっています。半導体がどのような仕組みで、どんな工程で作られているのか。そしてASMLは半導体業界にどのようなイノベーションを起こしてきたのかについて、3部に分けてご紹介していきたいと思います。
過去の記事はこちら
第1回「半導体はなぜ微細な構造を必要とするのか?」
第2回「半導体の製造プロセスとASMLが誇る露光技術」
第3回は「半導体業界に革新をもたらした、ASMLのイノベーション」についてです。ASMLは半導体露光装置において世界No.1のシェアを持ち、半導体の進歩に大きく貢献してきました。そこには20年以上かけて開発に取り組んだASML独自の技術が関わっています。今回の記事では、ASMLの露光装置が選ばれる理由とも言える”3つのイノベーション”についてお話しします。
今回の記事は、ご自身も半導体業界でご活躍されながら、半導体関連の著書『「半導体」のことが一冊でまるごとわかる』(共著、ベレ出版)も出版されている蔵本貴文氏に執筆いただきました。
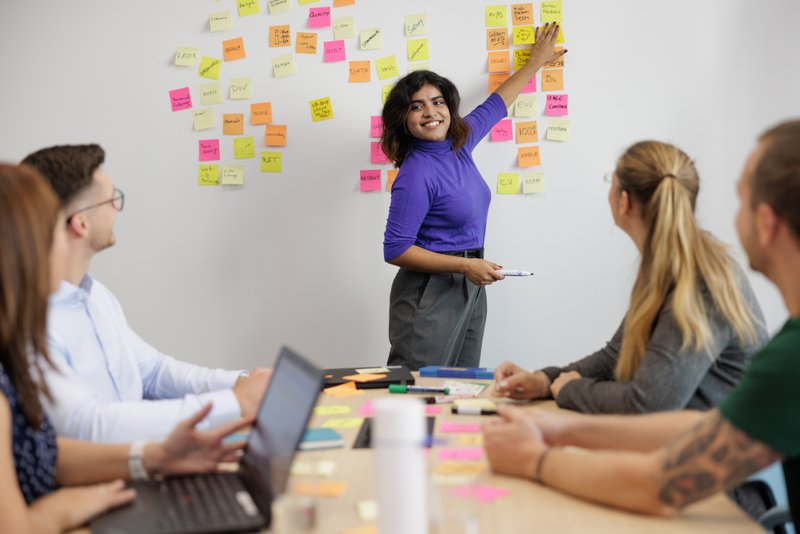
3つのキーイノベーション
ASMLは半導体露光装置において世界No.1のリーディングカンパニーです。ただ、その地位は簡単に築けたものではありません。1990年代までは他社に遅れをとっていたこともあります。しかし2000年以降のイノベーションにより、一気に今の地位を確立しました。
それらの中でも、特にASMLにとって重要な3つのキーイノベーションについて紹介いたします。その3つとは、TwinScan(ツインスキャン)技術、Immersion(液浸露光)技術、EUV露光技術の3つです。
最初はTwinScan技術です。これは露光プロセスの効率化を目的とした技術で、1台の露光装置に2つのステージを使用して生産性を向上させます。一方のステージでは露光処理を行いながら、もう一方で露光に必要な測定や位置合わせを行います。この技術で、露光系の稼働率を上げて、露光装置の処理能力を高めています。
次に、Immersion(液浸露光)技術の導入です。これは、露光中のウェハとレンズの間に水を入れることで、解像度を高める技術です。解像度は光源の波長が短いほど、レンズの開口数が大きいほど高くなります。Immersion技術以前は主に光源の波長を短くすることで解像度を上げてきました。しかしASMLがImmersion技術を導入し、開口数を上げることで解像度を高くすることができるようになりました。
そして、最後にEUV(極端紫外線)露光技術です。これは13.5ナノメートルという短い波長の光を使用し、さらなる微細化を実現する技術で、現在の半導体製造の最先端です。EUVリソグラフィーは従来の光源よりもはるかに微細に露光できるので、集積度向上に大きく貢献しています。ASMLはEUV技術を採用した露光装置の製品化に成功した唯一の企業になりました。
今回はこの3つの技術の背景について、詳しくお伝えしたいと思います。
飛躍的に生産性を向上させたTwinScan
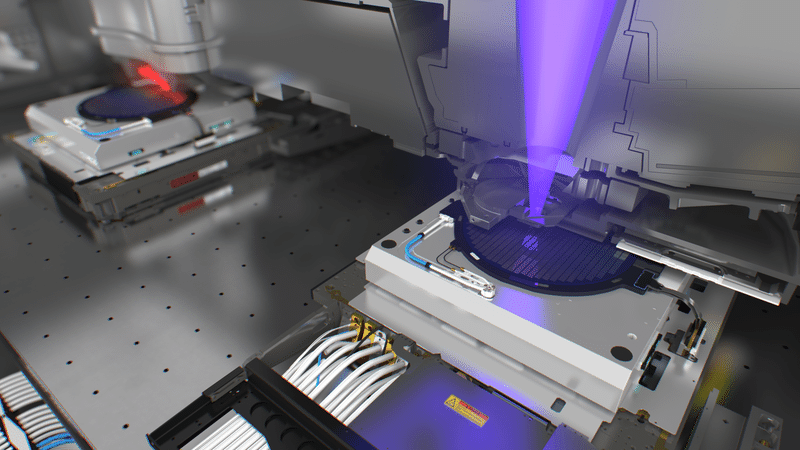
TwinScanが生まれた背景
露光装置は前工程の半導体工場において、もっとも高価な機器の一つです。というのも、レンズなどの光学系が精緻でどうしても高価格となってしまうからです。ですから露光装置の台数は、常に装置を稼働させるために、工場の生産能力の必要最低限にせざるを得ません。
従来の露光装置では、1つのステージでウェハを計測し、ウェハの凹凸など必要な情報を取得した後、レンズの下で露光が行われていました。しかし、計測している間は光学系が使われていません。つまり、装置を効率的に利用できていなかったのです。
そこでASMLが開発したのがTwinScanです。これは、1台の露光装置で2つのステージを使う技術です。つまり1つのステージでウェハを露光しながら、もう一方のステージで次のウェハの計測を行えます。ですから、光学系を常に稼働させられます。もちろん、装置の価格は高くなりますが、それを上回る生産性の向上を実現し、顧客(半導体メーカー)のコスト削減に貢献しました。
TwinScanによる生産性の向上
この技術の導入前は、1時間当たりの露光枚数はウェハ200枚にも大きく届きませんでした。しかし、TwinScanやその他の生産性向上の技術開発により、現在のASMLの露光装置は1時間に295枚のウェハを露光できるようになりました。これは300mmのウェハ1枚、96ショットを約10秒で露光していることになります。露光中はステージが15G(重力加速度の15倍)の加速度で動作し、しかも0.17nm以下の位置精度を保っているのです。
前述したとおり、TwinScanを使うと露光と計測を同時に行えます。つまり、より計測に時間をかけることができるため、より多くの計測点を設定するなど、計測精度を高められます。
例えば、ウェハが持つ歪みやデコボコといった特性を事前に計測し、露光前の状態を詳細に把握できます。すると、横方向だけでなく、高さ方向のズレも補正され、露光装置の性能を最大限に引き上げることができるのです。
TwinScan開発の技術的課題
TwinScanのメリットは生産性向上ですが、2つステージを持つとその分コストは増大してしまいます。ですから、その上昇分を補って余りある効率性のメリットを出すことが開発の課題でした。
この開発においては、計測情報を正しく引き継ぐことが1つの課題でした。TwinScanでは計測と露光を別々のステージで行います。露光装置のステージの位置はレーザー干渉計を使って計測しますが、ステージや干渉計により測定結果が異なることが一般的です。開発初期の段階では、そのデータをうまく引き継ぐことが大きな課題でした。しかし、ASMLはその問題を解決し、TwinScanの技術を確立することに成功するのです。
このTwinScanの技術は2000年代初頭に確立され、生産性と精度の両面で性能を向上させました。その経済性が評価され、多くの半導体メーカーにASMLの露光装置が導入されるきっかけとなったのです。それまでは競合他社もそれなりの競争力を持っていたものの、このTwinScanにより、ASMLが一気に露光装置のトップサプライヤーとなり、No.1の地位を不動のものにしました。
光源を変えずに解像度を高めたImmersion(液浸)技術
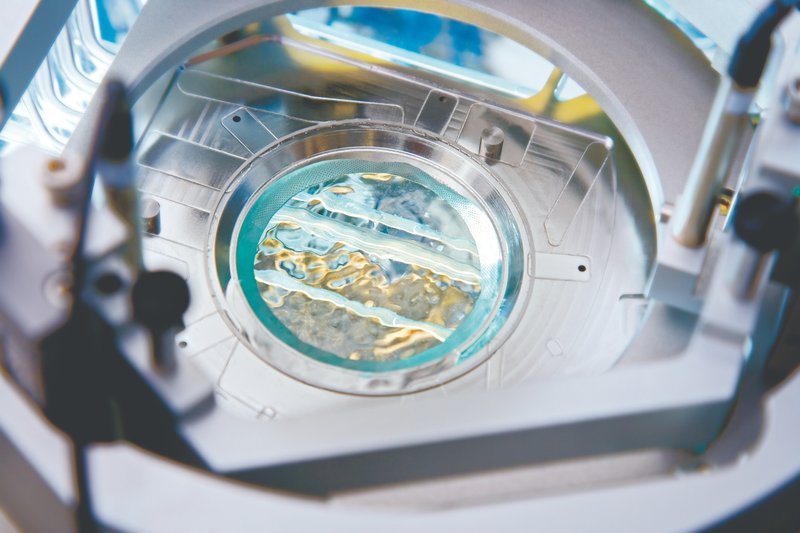
Immersion技術の必要性
露光機の解像度の限界は、光源の波長によって決められます。ですので、半導体の進化の歴史において、光源はどんどん短波長化されてきました。具体的にはg線(436nm)、i線(365nm)、KrF光源(248nm)、ArF光源(193nm)と進化してきたわけです。
ArFの次も、波長の短いF2光源(波長157nm)の導入が検討されていました。しかし、技術的な課題の大きさやマーケットのニーズを含めて検討し、ASMLは別の解決策を探ることにしました。
そこで浮上してきたのがImmersion(液浸)露光技術です。これはレンズとウェハの間に液体(水)を入れて露光する技術です。レンズとウェハの間に何もない場合は、空気の屈折率は1ですが、水の場合は1.44となります。水を入れると下の図に示すように、より多くの光を焦点に集めることができます。結果、解像度を高められるのです。
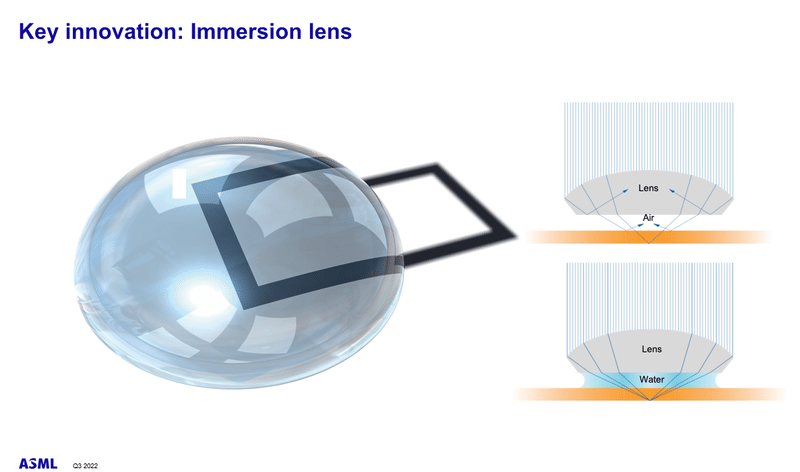
このImmersion技術により、理論上は水の屈折率である1.44倍に解像度を高められます。いい方を変えると、ArF光源(193nm)の場合、193nm/1.44≒134nmの光源と同等の解像度を得られることができ、F2光源(157nm)は不要となりました。
ASMLはこのImmersion技術を他社に先駆けて実現し、先端の露光装置における優位性をゆるぎないものにしたのです。
Immersion技術開発の困難
このImmersion露光技術の開発には大きく分けて2つの課題がありました。
1つ目は水の管理に関する問題です。Immersion技術では、レンズ下に水を保持しながら、露光系を高速で動かす必要があります。その際に水がこぼれてしまうと、ウェハに欠陥を引き起こす原因になります。ですから、水がレンズの下にのみ存在するシステムの開発が求められました。また、水の中に空気が混入し気泡が生じると、これも欠陥の原因となります。そのため、水をこぼさず、かつ気泡が入らないようにすることが重要でした。
これを解決するために、まず水をレンズの下に速やかに流し、吸い上げる仕組みを開発しました。また、水の周りの環境は二酸化炭素で満たしました。二酸化炭素は水に溶けやすいので、仮に気泡が発生しても、露光エリアに到達する前に消失するのです。
2つ目は気化熱による問題でした。水が蒸発すると、気化熱でウェハが冷えます。すると、ウェハがわずかに収縮します。そんな微妙な変化でも、重ね合わせの精度に無視できない影響を与えるのです。この問題は、ヒーターでウェハの温度を均一に保つことで解決しました。これで局部的な冷却を防ぎ、ウェハの収縮を起こさない仕組みが実現したのです。
これらの課題は困難なものでしたが、エンジニアの工夫により、少しずつ問題を解決していきました。最終的に信頼性の高い現在のシステムとなり、Immersion技術は多くの半導体工場で使われる技術となったのです。
TwinScanがあったからこその有利さ
このImmersion技術の開発において、先ほど説明したTwinScanのメリットがありました。ASMLはTwinScanにより、露光と計測のステージを分離していたことが有利に働いたのです。
液浸リソグラフィーでは、露光に使うレンズの直下でのみ水を使用します。一方、計測プロセス中に水が存在すると、計測の精度を下げる原因になります。TwinScanを持つASMLは、計測ステージと露光ステージが別々なので、計測時には水はありません。ゆえに、計測に悪影響を及ぼさないのです。TwinScanのおかげで、ASMLは露光における水の管理だけに集中できました。計測は既存技術で対応できたのです。
一方で他社は、計測と露光を同一ステージで行っていました。ですので、レンズの下に水がある状態での計測を正確に行うことに苦労したようです。ASMLのTwinScanは、計測の課題を回避し、液浸技術の開発における有利なポジションを確立していたのです。
世界でASMLしか保有していないEUV露光技術
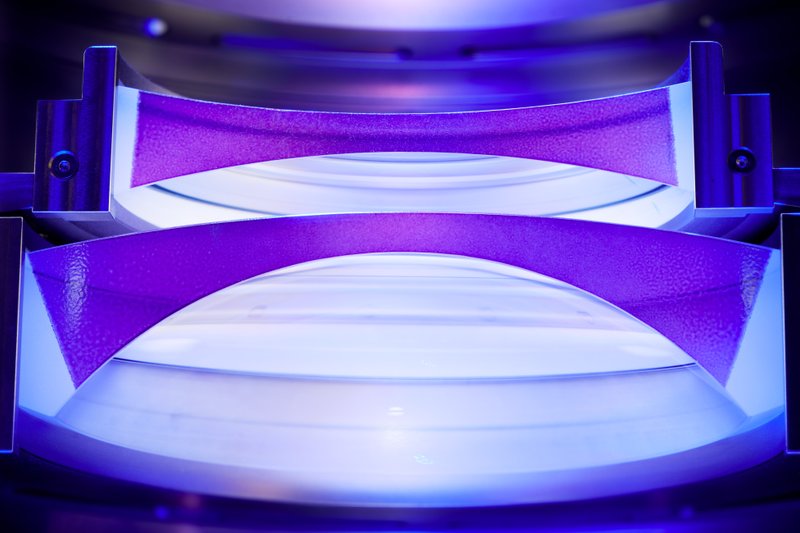
高い精度が求められる鏡
Immersion技術により、ArF光源(193nm)の技術が延命されました。しかしさすがに7nmといった微細な世代になると、Immersionの延命では対応できません。短波長の光源がどうしても必要です。そこで、ASMLが選んだのはEUV(極端紫外線)光源でした。これは光源の波長をArFの193nmから一気に13.5nmまで短くする技術です。これほど短い波長の光になると、ガラスのレンズを通過できずに吸収されてしまいます。したがって、光学系は反射を利用したもの、つまり鏡を使った、従来とは全く違う技術が必要とされたのです。
鏡の反射率は最大でも約70%程度と限られています。つまり、鏡を一枚追加すると約30%の光が失われるわけです。光を効率的に伝達するためには、鏡の数を最小限にしつつ、その精度を高く保たねばなりません。
この鏡は、カール・ツァイスという会社に製造を委託しています。現在のEUV露光装置の鏡では、数pm(1pmは1兆分の1m)レベルの加工精度が必要です。これは直径1mの鏡の凹凸を、設計値からわずか50pm以内に抑えることです。この精度は、日本の国土ほどの面積に対して、表面の凹凸を、人間の髪の毛の太さ程度に抑えることに相当します。
開発に困難を極めたEUV光源
EUV光源の開発においては数多くの困難がありました。その中でも、とりわけ大きな課題が、光源のパワーの強化でした。この技術開発に想像以上の時間がかかってしまいました。
EUV光源にはレーザープラズマ発光という技術を用います。これはスズの液滴にレーザーを照射して、発光させる方法です。
十分な発光強度を得るためには、レーザーの出力を高める必要があります。このため、従来の工業用レーザーより、はるかに高出力のレーザーが必要でした。CO2の工業用レーザーは0.3kWから5kW程度ですが、EUV光源には25kW程度のレーザーが使われています。
発光効率向上も重要です。スズの液滴にレーザーを照射した際の、EUV光の発光効率を高めるわけです。この効率化のためには、複雑な動作が必要でした。最終的に使われた方法は2ステップの方法です。まずスズの液滴に、弱いレーザーを当てて拡散させます。その後、強いレーザーでプラズマを発光させます。このプロセスを1秒間に5万回という速度で実行し続けます。
この過程で、スズが鏡を汚す問題も起きました。汚染された鏡は、取り替えなくてはなりません。しかし鏡は高価な上に、交換に時間がかかります。もちろん交換中は露光装置を使えません。これを防ぐため、液滴のサイズを小さくしました。その他にも、どんどん改良を加えています。初期のEUV露光機は鏡を頻繁に交換していましたが、現在では1年に1回から2回で済むようになりました。
競合する他社や研究グループはこれらの課題を解決できず、EUV露光装置の開発を諦めました。ASMLだけが、諦めずに問題を解決し、EUV技術を実用化させたのです。それがASMLの先端露光装置における高いシェアにつながりました。
パートナー企業を巻き込んだ開発
これだけの難しい開発ですから、1社が担うには荷が重い挑戦でした。そこでASMLはEUV露光技術の開発を他の企業と連携して進めました。先ほど鏡の話をしましたが、鏡はカール・ツァイスに製造を委託しています。
その他にも、ASMLは米国のサイマー(CYMER)を買収しました。サイマーはレーザーを手掛ける企業で、EUV露光機開発には、サイマーの技術を自社内に取り込むことが必須と判断したのです。
さらに、ASMLはEUV技術のための巨額な開発資金を集めるため、インテル、サムスン、TSMCといった主要なユーザーからの出資を募りました。これは業界では異例の試みでしたが、彼らの出資を得ることに成功しました。この出資はASMLに資金を与えただけでなく、EUV露光装置の開発にユーザーを巻き込むことに成功しました。このように、ASMLは他社や研究機関と、上手に連携しながら開発を進めたのです。
露光装置だけでなく、ソリューションを提供するHolistic lithography
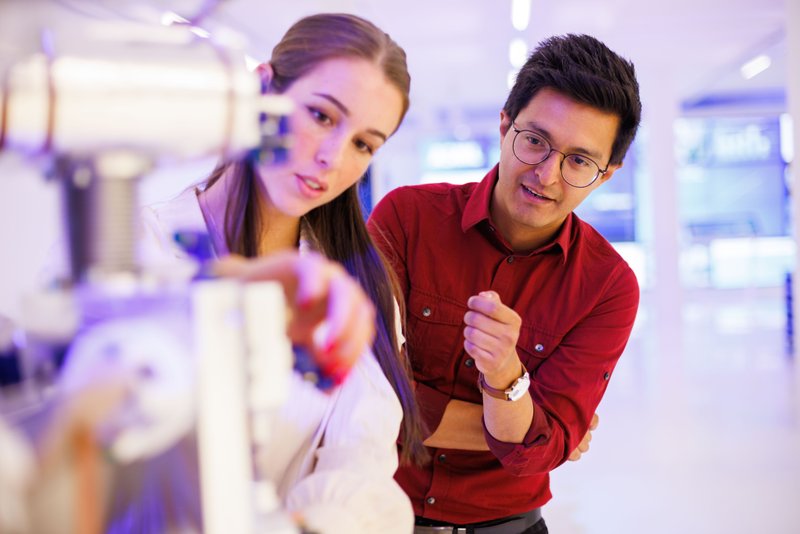
Holistic lithographyを構成する3つの柱
ASMLは装置を提供するだけのサプライヤーではありません。露光技術を進歩させるために、周辺技術を取り込んで、顧客の価値を最大化すべく努力しています。
その考え方がHolistic lithography(ホリスティックリソグラフィー)です。下の図に示されているように、Image(リソグラフィ)、Model(計算機リソグラフィ)、Measure(検査装置)を3つの柱を組み合わせ、包括的なソリューションを提供しています。それぞれの柱について、詳しく説明します。
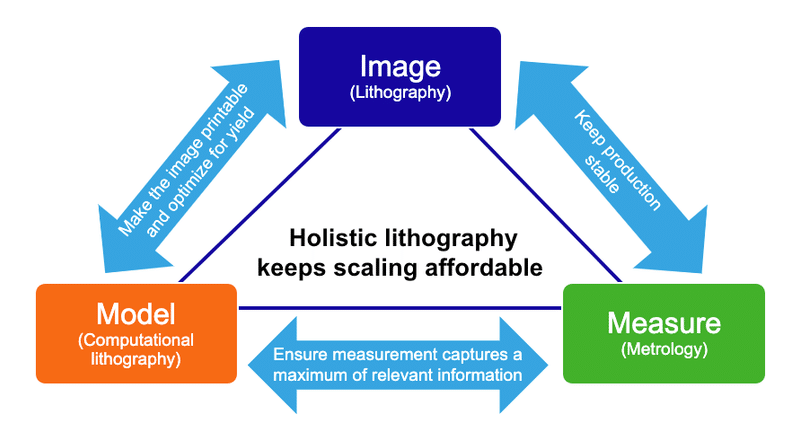
Image(リソグラフィ):リソグラフィは、電子回路図が描かれたマスクに対してレーザー光を照射し、レンズを通すことで縮小された回路図をウェハ上に描写する(露光する)技術です。これまで説明してきた、TwinScan、Immersion、EUV露光もこのリソグラフィに大きく関わっています。
Model(計算機リソグラフィ):計算機リソグラフィは、実際にウェハ上に露光する前の段階で、露光結果をシミュレーションする技術です。コンピューター上で予想を立てることで、最適な露光条件やプロセスを導き出し、露光を行うことが可能になります。
Measure(検査装置):ASMLの露光装置は、露光と計測の2つのステージに分かれていて、計測ステージでは露光前のウェハを検査します。そこで取得した情報を、露光装置や計算機リソグラフィにフィードバックしています。
これら3つが一体となり機能するHolistic lithographyを提供することで、生産性の向上を実現しているのです。
Holistic lithographyによる露光の最適化
では、Holistic lithographyによって実現できることとは、具体的にどのようなことなのでしょうか。その1つが半導体の歩留まり向上です。
下の図において黒が不良品(Dead die)を表しています。左の製品ではウェハの外周に不良品が多数発生していることがわかります。(左下の写真を見ると、断線していることが確認できます)。
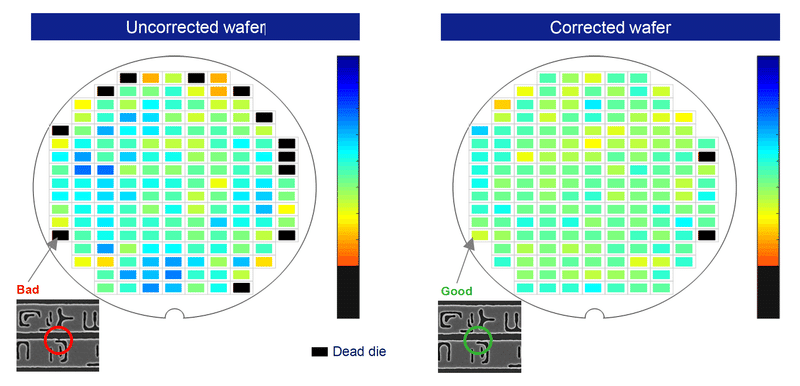
半導体工場では、この不良品をできるかぎり減らし、生産効率や良品率を向上させることが求められます。しかし、実際に露光を行ってから、不良品が発生した原因を探り、次の露光にフィードバックしていては、効率的な生産とは言えません。
そこで、計算機リソグラフィが大きな役割を果たします。使用するウェハや外的要因などにより、常に同じ条件で最良の露光ができるわけではありません。露光毎に「この条件で露光すれば、より良い結果が出る」というシミュレーションを行い、その予想結果を露光条件にフィードバックすることで、右の製品のように良品率を改善することが可能になるのです。
あくまで、これは計算機リソグラフィにより歩留まりが向上した一例です。Holistic lithographyは、計算機リソグラフィと検査装置をリソグラフィにうまく融合させることで、最高のパフォーマンスを発揮できるよう、アプローチしています。
ASMLは半導体チップメーカーにとって、理想のソリューションを提供するサプライヤーとしての地位を築いてきました。顧客のために、できることは全てやっていく。その姿勢こそが今のASMLの成長の原動力になっているのです。
エーエスエムエル・ジャパンでは、年間を通してエンジニアの採用を行っています。興味をお持ちになった方は、ぜひ弊社HPをご覧ください。
■ エーエスエムエル・ジャパン採用情報
■ ASML日本法人サイト(エーエスエムエル・ジャパン)
■ ASMLグローバルサイト