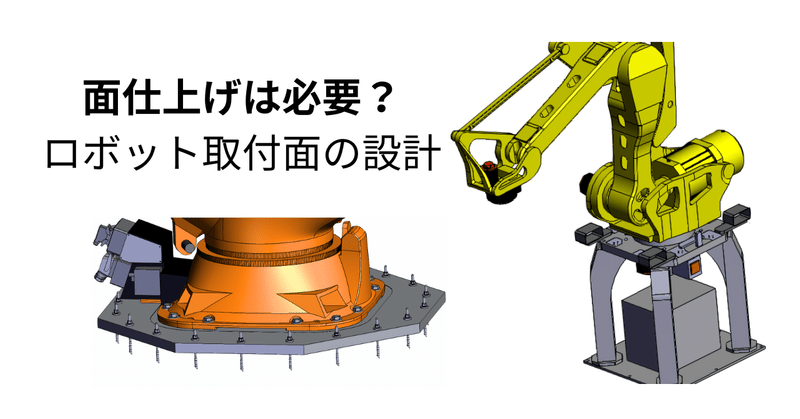
面仕上げは必要?ロボット取付面の設計
こんにちは、あるぱかです。
私はロボットSIerとして産業用ロボットに関する技術情報を発信しています。
今回はロボットベースの設計、特に設置部の仕上げ加工についてメモしていきたいと思います。
最近ロボットベースの製缶モノを設計しましたが、なかなか奥が深いなと感じました。
私はもともとロボット取付面の仕上げ加工はしなくていい派でした。
全面加工していたら加工費が高くつくし、経験上そこまでしなくてもいいと考えていました。
ところが改めて先輩社員に意見を伺うと、設計者によって考え方が様々で、これは深く理解しないといけないと思い、X(旧twitter)でこの疑問を提起しました。
仕上げ加工は必要か?
下記が投稿内容です。
【ロボット取付面の加工】
面仕上げは、基本しなくていいのでは?という話。
メーカの中には取説で面仕上げの指示があるけど、そこまでしなくていいと思うんです。
以前、現場で200kgクラスロボットの取付面が全面ピカピカなのを見たことがあって、 仕上げがとんでもない面積になってて、製作費が跳ねあがってたみたいです。
小型ロボットならまだしも、中~大型になると尚更でしょうね。
「ロボット交換しても精度が維持できるのでは?」
→交換してる時点で教示やり直しは必要じゃないかな。。
仕上げ無の塗装面+ピン穴が現実的じゃないかな。 #産業用ロボット
【ロボット取付面の加工】
— あるぱか (@AlpacaRobotics) May 1, 2024
面仕上げは、基本しなくていいのでは?という話。
メーカの中には取説で面仕上げの指示があるけど、そこまでしなくていいと思うんです。
以前、現場で200kgクラスロボットの取付面が全面ピカピカなのを見たことがあって、… pic.twitter.com/Fd0lS21VlT
ロボットメーカの取説にも仕上げ加工や平面度の指示があることは承知してました。ロボットの据付面の平面度が悪い場合はロボットが変形し、機能を損なう可能性がある、とされています。
例えば以下のロボットでは平面度と板厚35mmに対し仕上げ加工の指示がありました。
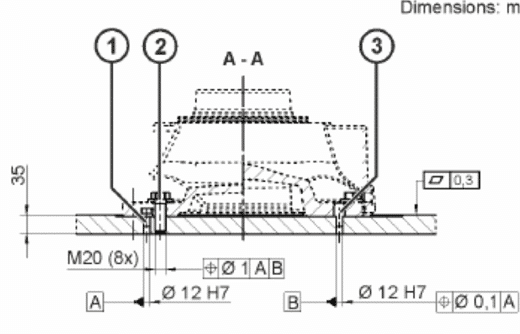
それを厳守することに疑問を感じていたのが正直なところです。なぜなら仕上げ加工による加工費アップを抑えたいからです。
5~10キロ可搬の小ロボットや協働ロボットなら接地面積が少ないので構わないのですが、可搬重量が200kgあたりになると広範囲になります。例えば以下の安川製GP180(180kg可搬)だと800mmx500mmで、おそらくベースプレートは1mx0.8m程度になるかと思います。
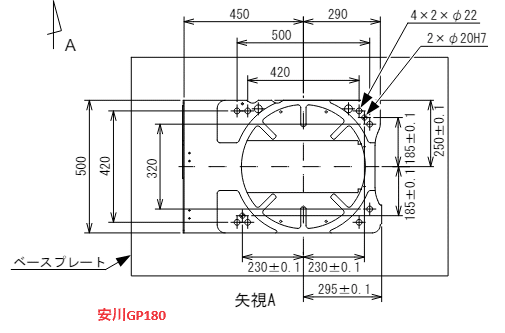
なので全面加工までしなくても黒皮のままで、ピンで位置決めでいいと考えていました。
実際現場でそういう装置を度々見かけますし、実際それで問題が起こったことはありません。
今思えば安易な考えだったと思います。
フォロワーさんの見解と分析
フォロワーさんからの反応をいると、ロボット取付面の加工に関して様々な意見があることがわかりました。
要点をまとめると以下のとおりです。
反対意見(仕上げ加工は必要)
まずは反対意見です。ザックリ以下の項目にまとめることができます。
【面仕上げの重要性】
全体的に取付面の面仕上げは重要との見解が多かったです。
これは以下の理由に集約できます。
・面圧分散
・構造的安定性の向上
・繰り返し精度の確保
特にロボットと取付面が完全に接触するようにすることで、ロボットの負荷トルクや重心移動による問題を防ぐために仕上げ加工が有効です。
ロボットの反力、トルクがどれくらいか確認しましょう。
それらはメーカー取説にまとめられています。下記、安川製GP180の仕様です。
表と図からわかるとおり、「垂直回転時」、つまり2軸目のアームを振り下ろすときのトルクが最も大きいことがわかります。
これに耐えうる基礎の設計が必要です。
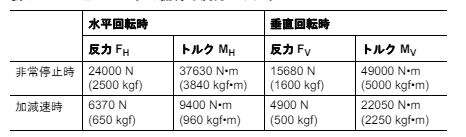
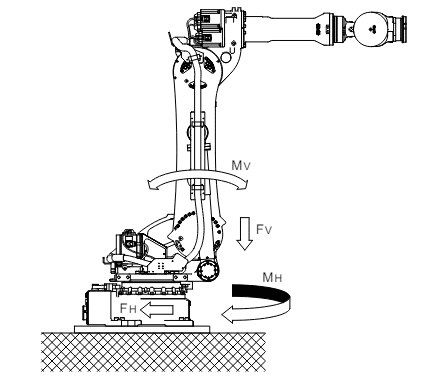
【加工とコストのバランス】
全面を加工するのではなく、必要な部分だけを切削する提案がありました。
コスト削減と加工効率化を目指すものです。
ロボットベースの断面を見れば分かるのですが、大抵はベース全面が設置するのではなく、ボルト締結部周辺のみ設置し、中央は空洞になります。
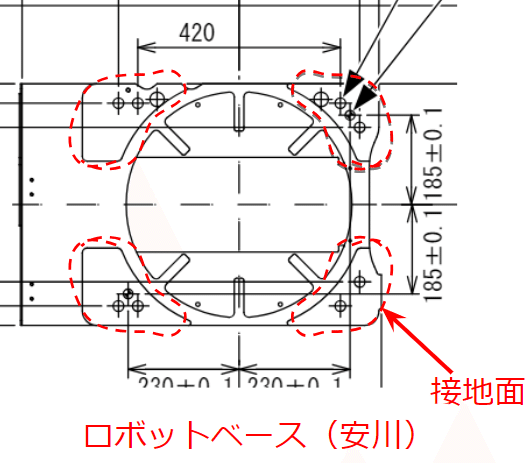
つまりこのボルト締結周辺の4か所さえ設置されていればいいので、最低限そこだけ仕上げ加工すれば加工範囲が絞れる、という考え方です。
ベース部のサイズ形状によっては全面加工の方が安くつく場合もありそうです。
【材料の特性と溶接による歪み】
製缶品などの場合、材料の特性(溶接による歪みや表面の不均一性)を考慮して、荒加工を行うことが提案されています。これにより、安全性を確保しつつコストを抑えることが可能です。
製缶品だとベース板に歪みが生じ、歪んだベースに対して設置させれば隙間が生じます。設置してほしいのにきちんと密着していない状態で、力が均等に分散されないことに繋がります。
【ロボットメーカー指示と承認】
ロボットメーカーの取り付け仕様に従うことの重要性が指摘されました。フォロワーさんの中には、メーカの仕様に従わない場合、承認が得られないことがあったようです。
ここでいう「承認」とは:
設備の納入先、「客先」の仕様によります。
例えばY社の10kg可搬5軸を指定された場合 ロボの設置(架台)に関しては その仕様をクリアしないと承認して頂けない場合が有ります
賛成意見(仕上げ加工は不要)
ここからは仕上げ不要論の意見です。
【コスト意識】
全面的な仕上げ加工は製作費を不必要に増加させます。特に大型ロボットの場合、加工面積が広くなるため、広大な加工面積は避けるべきという主張があります。
【柔軟なメンテナンス】
ロボットの交換時にはどのような場合でも再調整が必要であり、過度な仕上げはしなくてもいいのではないか。
つまり、精度の維持には基本的な平面性と適切な取り付け穴があれば十分という意見です。
【ピンで十分】
仕上げのない塗装面にピン穴を設けることで、十分な取り付け精度を確保できるとされる。という意見です。
総評
いただいたコメントやリポスト30件程度をざっくり円グラフに二分すると、仕上げ有りが6割でした。
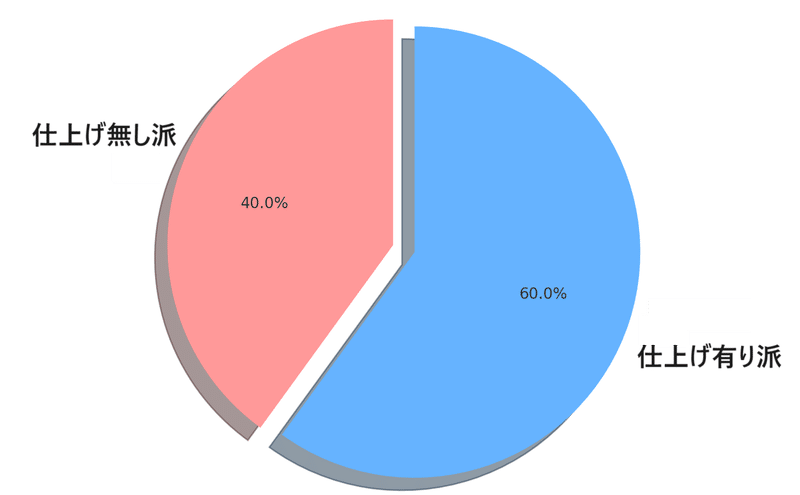
賛成意見(仕上げ無し)は主にコスト削減と実用性に焦点を当て、全面加工の過剰を避けることで効率的な運用を目指しています。
一方で、反対意見(仕上げ有り)は技術的精度、安定性、および長期的な性能維持に重点を置き、高精度の加工がもたらす利点を強調しています。
両者の間で、最適なバランスを見つけることが重要であり、特定の用途やロボットのサイズ、生産環境に応じて加工の程度を調整する必要があります。
私が選んだ最終見解
ロボット取付面の加工に関する議論を踏まえた上で私の現在の結論は、
「面仕上げを行うべきだ」です。
見解と提案
コストと精度のバランスを考慮した結果、接触面のみを仕上げることが最も効率的かつ実用的な解決策と考えられます。
具体的には、ロボットの設置面に溶接プレートを施し、その四面のみを仕上げる方法を提案します。
このアプローチにより、取付精度は保たれつつ、コストも抑えることが可能です。
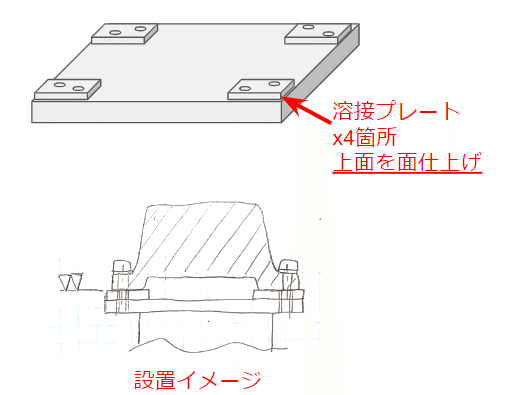
リスクの整理
仕上げ無しの状態でもロボットは機能しますが、繰り返しによる荷重がかかると、時間とともに材料の疲労が進行する可能性があります。
特に、可搬重量が大きいロボットでは、これらの影響がより顕著になり得るため、長期的な安定性を考慮すると、面仕上げはあったほうがいいと思います。
短期的には成立するかもしれませんが、長期的に見れば致命的な不具合が発生するリスクを無視できません。
以下のようなリスクが考えられるのではないでしょうか?
フレームのクラック(ひび割れ)
アンカーボルトが抜ける、破損する
取付ボルトが破断する
それでも仕上げはしなくていいケースとは
盲目的に仕上げ加工が原則というわけではないと思います。
ロボットの負荷トルクをフルマックスで動作させるなら、面圧や繰り返し荷重を考慮して面仕上げすればいいです。
しかし100%スピードではなく50%の想定なら、そこまで接地面精度を求めなくてもいいと考えています。
ただ想定したスピードが想定どおりにいくとは限らない笑
いざ現場で動かし始めるとお客様から「もっと上げて」と言われるのはあるあるです。
最後に
この議論を通じて、取付面の仕上げがロボットの長期的な性能と安定性に大きく寄与することがわかりました。
効率よくコストを抑えつつ、必要な精度を確保するためには、適切な加工方法の選択が鍵ですね。
この記事が設計の手助けとなれば幸いです。
ぜひ、皆さんの経験や意見を教えてください!お待ちしています!
この記事が気に入ったらサポートをしてみませんか?