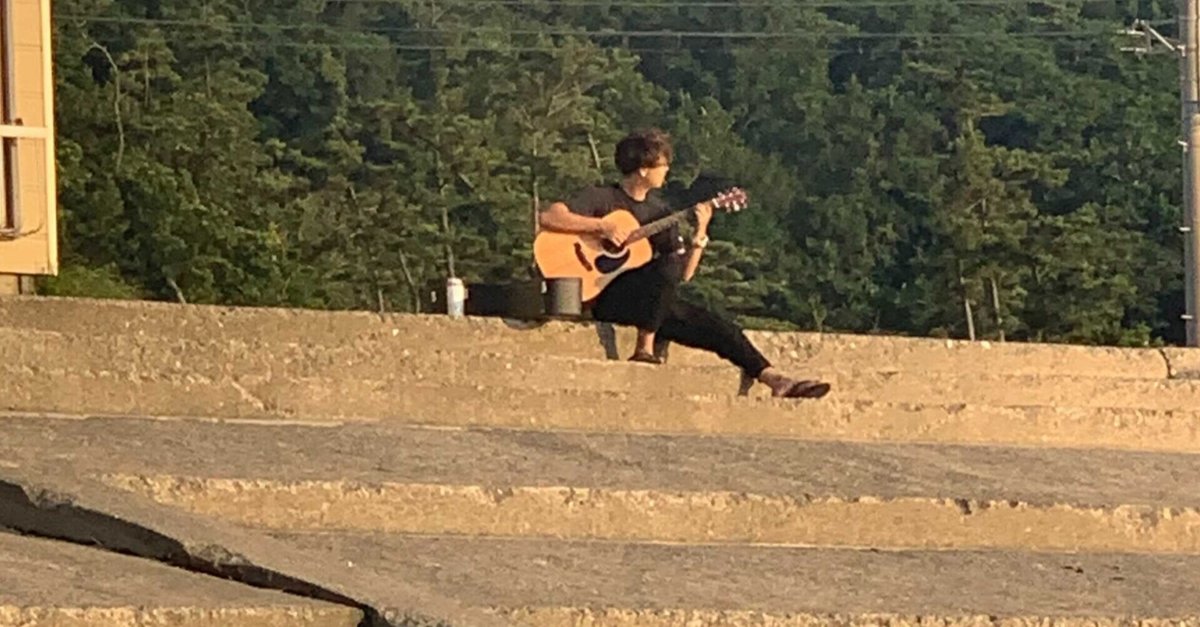
新しいギターとの邂逅
ピンときた.気づいたら1時間で買っていた.
中古で2万7千円.
しかし,そうとは思えないほどに素晴らしい音色だ.
思わず,作り手を調べた.
30人の職人で 1日に”20”本の本物を作る.その名も,ヤイリギター.
その響きの秘密が知りたくなって製造方法も調査した.
[製造工程]
1,乾燥 2~3年 長くて10年
2,接合 表板 裏板を万力で接合(合板の場合)
3,板の選定 木目 コシを見て.
4.骨組みの加工(ブレイシング・スキャロップ)
弦の振動をボディに伝える
5,サイド材の曲げと接合 万力でひょうたんがたに曲げる
6,ギターボディにトップとバック材の接合
7,トップとバック材の接合部を細長いひもみたいな部材でくくる(バインディング)
8,装飾部品を埋め込む.貝殻など(インレイ)
9,ネックの調整,接合.ボディ側を凹ませ,ネック側を凸にして組み合わせる
10,ネック形状の調整.
奏者がよく触るので,工具でなめらかになるように削る.
11,塗装の前加工 .サンドペーパーでの研磨,マスキング
12,塗装.響きを邪魔しないように,できるだけ薄く.
研磨しては塗るを繰り返して美しく.
13,フレットの打ち込み.高さのばらつきが出ないように打ち込む.
14,シーズニングルームで寝かせる(→ここポイント!!!)
湿度・温度を一定にした部屋で大音量の音楽を聞かせる.ギターへの胎教.♫
15,バフ
盛り上がった塗装面を布で磨く.艶を出す.
16,ナット(ネックの先端で弦を固定する部分) サドルやペグ(回す部分),弦を取り付け
17,サウンドチェック
弾き心地,ピッチ
18,検品
各工程の確認
木材の節やシミもそのギターの個性.100%きれいじゃなくても適材適所で活用するの素敵.
○ギター調整の話
低音の響きが足りないので内部を削って調整.削りすぎるとボディが弱くなるので,繊細な作業が要求される.奥深い.
力木(骨格)に当たる部分を小さなかんなで削り取った.
○かつて日本はギター大国だった. 1971年には200万本が作られた
やいりさんは,やすさではなく質の良さで勝負することにした.
まず何をしたか?
先を言っていたアメリカのギターを研究して,真似することにした.
お手本にしたくても,写真に取ることはできなかった.なので,米国に渡って頭を下げて,工場の内部を見させてもらったときに,ギターの内部の構造を頭に焼き付けた.
それを帰国後に,再現することを試みた.
失敗に失敗を重ねた.試行錯誤した.
1950-1970年にかけてヤイリギターの評価は高まっていったが,決して生産量を増やさなかった.
質を落とさないために.
たとえ客をまたせても「良いものを作ろう」というポリシーを貫き通そうとした.
しかし,アジア,中国等では超安いギターが出回っている.
だがしかし,職人から見るとそれはいただけない作りであった.
ボディ,ネックの歪.チューニングがよく狂ってしまう.
木材はしっかりした木を使っているのに,いい加減に作られてしまっているので,質が悪くなってしまっている.
それを知ったヤイリギターの職人が一言.「せっかく,使わせてもらっているのに,木に申し訳ない」
○廉価品を作ろうとしたが,質は落としたくないじゃあどうする?
人件費の安い中国に出してしまうと品質低下は免れない.
地元の木材加工業者に頼むことにした.
地元であれば,目が行き届き品質を保てそうだから.
しかしながら,一般業者の木材の加工は一筋縄ではいかなさそうだった.
例えば,木を曲げてボディの曲線を作る.
ササクレを出さないで木を加工するなど.
ささくれはギターの振動を阻害する原因になる.
ネックの削り方も難しい.ガタガタしてしまうと弾き心地の低下になる.
品質の追求,コストダウンの両方を満たすためには多少の妥協は許されない.
それが難しいところ.
やがて,部材の外注業者から試作品第1号があがってきた.
検査する.
高音部の音程がずれていた.
原因はフレットの位置が若干ずれていたから,音程に狂いが生じていた.
長年培った職人だからこそ拾った問題だった.
結果,最初の100本は品質不足で出荷はできなかった.
「いいものを安くつくる」という難しい課題に挑戦し続けている.
2004年7月時点
実際に弾いた.
甘い響き.その音色で世界を塗り拡げている.
オール単板なのでこれからもどんどん成長していくのだろう.
これから先が楽しみだ.
この記事が気に入ったらサポートをしてみませんか?