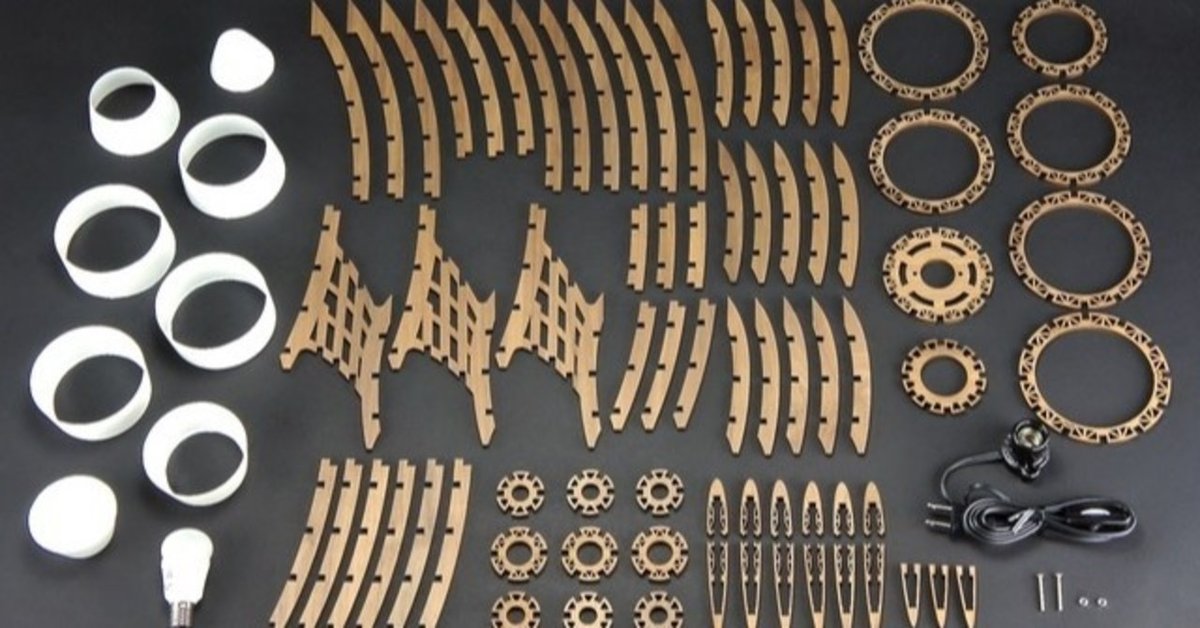
ロケット型ランプができるまで その4
みなさん、こんにちは。今日は2020年7月25日。
前回の記事で、外装パーツができるまで、をお話ししました。
今回は、外装パーツの中にはまるシェードパーツができるまで、をお話しします。
外装パーツの中にピッタリとはまるようなシェードパーツを作るには、高精度の型を作り、その型にプラスチックをはわすように形作る方法が一番良いと考えました。
TechShop TokyoにはCNCがあった、という話を『その2』で触れましたが、Gコードを自分で書く必要があるのでは、ということから敬遠していた、という話をしました。(CNCとは、回転する刃物が自分で作成した『刃物の動きデータ(Gコード)』のとおりに動いて削ってくれる機械)
高精度の型を作るには、そのCNCを使用する必要があります。
TechShop TokyoにあったCNCは『Roland MODERA PRO-Ⅱ MDX-540』という機械で、その機械は3D CADで作成したデータがあれば簡単にGコードを作成できるアプリケーションが使え、切削に使用する刃物のデータなどを選択すれば簡単にGコードが生成できてしまうという初心者の私でも簡単に扱える機械だったのです!(わからない人、すみません…)
3D CADならデータが作れるので、早速シェードのデータを作成。
シェードパーツはCNCの切削深さの限界やデザイン性、作りやすさを考えて8つのパーツに分けて作ることにしました。
この1つひとつのパーツデータから型のデータを作成し、CNCに送るデータの準備をします。
このデータを先ほどのアプリケーションに読み込ませ、セットした材料(薄い緑色)から削り出す形(濃い青い色)を生成するデータを作成します。
この形状の場合は刃物を途中で取り替える必要があるのですが、それ以外は自動で削り出してくれます。
加工にひとつの型あたり平均して6時間ほどかかり、このような型が出来上がります。
この型に熱したプラスチックをはわせるのですが、この型をそのままあてがってしまうと、角の部分からプラスチックが破れていってしまう可能性が高いです。ですので、この型を保護するような枠を作る必要があると考えました。
TechShop TokyoにはCNCがもうひと種類あり、主に木材切削専用であるShopbotという機械です。
このShopbotも取り扱いが容易で、加工物の上下方向から見た形状を読み込ませて刃物が動くデータを作成していきます。
中にある4つの四角と周りの枠を除くと、型を押さえるための枠が出来上がります。
そして型の高さをカバーできるように残りを同じように作製します。
凹凸があるところをヤスリで整えて綺麗にすると、このような綺麗になります。
そして型と合わせるとこのようになります。
この一体となった型に、熱したプラスチックをはわせます。
どのようにしてはわせるかというと、この真空成形器を使用します。
実は、この写真には、もう出来上がったシェードの部品が写っています。中央部分に白いデコボコした板が乗っているのですが、それがシェードのパーツです。
写真奥にFormechと書かれた横にハンドルが付いている装置があるのですが、それがプラスチックを温めるヒーター部分です。このヒーターを手前に引き、下に敷いておいたプラスチックの板を温め、あらかじめ機械の中にセットしておいた、先ほどの枠付きの型を押し当てて成形します。
こうして曲げることができたプラスチックの板を、今度はハサミで切り取っていきます。ここにきて急にアナログな作業ですが、こればかりは仕方ありません。1mm厚のプラスチックの板なので、普通のハサミではなく、金属も切れてしまうハサミを使うとカットできました。(簡単に、とは言わない。)
こうして切り出して形を整えると、下の写真のように切り出せます。
1番と8番のシェードパーツ以外は底もくり抜く必要があるので、この後に行います。
そうして切り抜いたシェードパーツと、前のnoteで書いた外装パーツ、ランプ用のコード付きソケット、締結用のネジ、電球を全て並べると、下の写真のようになります。
全てで88個のパーツ数となり、これを組み立てていくとロケット型ランプ『The GAZE』になります。
ようやくパーツが全て揃ったのですが、組み立てるのも一苦労なのです。。
今回はキリがいいのでこの辺で終わりにします。
次回の『その5』では、組み立ての様子と過去の展示会出展での様子をお話しします。
その4は終わり。
この記事が気に入ったらサポートをしてみませんか?