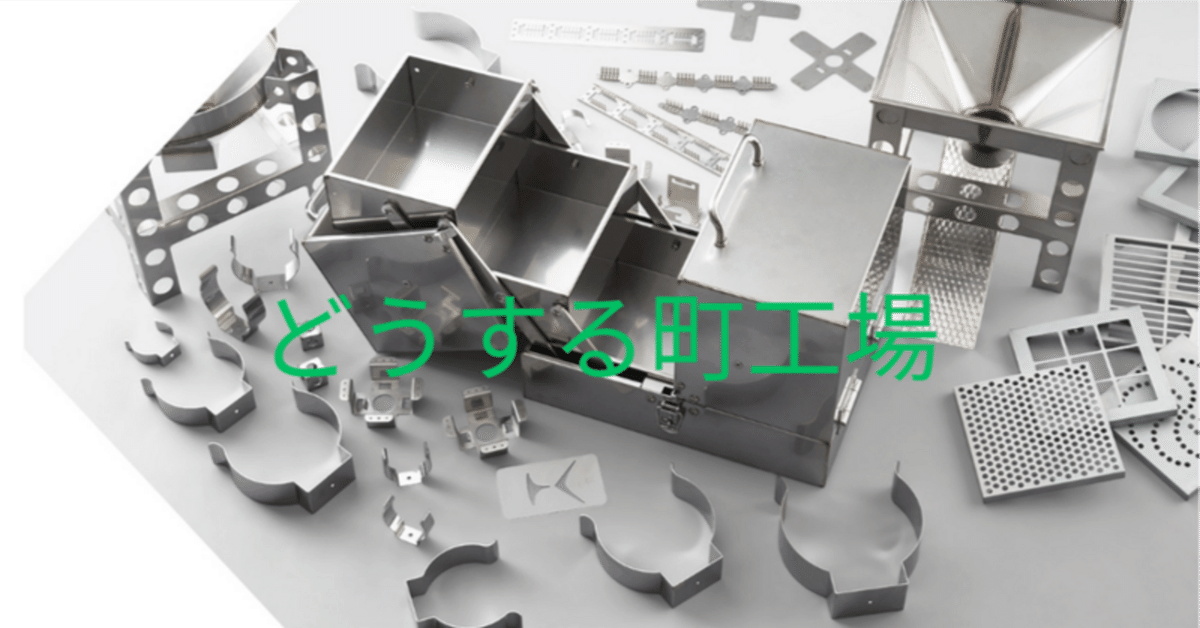
作業の習熟度を定点観測する:燕三条の町工場の一例
同じ作業を繰り返すことで習熟度は上がっていきます。
ものづくりの現場では同じような作業の繰り返しが多くなりますが、その習熟度によって品質・生産高が変わってきます。
一週間・一か月・一年などと期間をおいて、その習熟度合いを測ってみるとその違いは顕著に表れる事でしょう。個人差はありますが。
習熟度アップの要素
・慣れて手が早くなる
・要領を得て段取りが良くなる
慣れて手が早くなる
同じ作業を繰り返し行うと手が早くなり、時間当たりの生産高が上がってきます。学生時代の部活動や社会人になってからはゴルフの練習のようなものでしょうか。他の分野でも共通する事なのでしょうが、一定程度回数を重ねないと上達しないものです。
製造業は加工した一つ一つの製品単価に加工費が含まれています。そのため加工しなければ加工費を生むことが出来ず、売上を立てることが出来ません。対して、時間当たりの生産量によって売上高は変動しますので、手が早く生産量をアップすることで、売上高を増やし利益を増やすことが出来ます。
但し、あくまでも安全性を確保した上での作業であり、効率を上げるために事故や怪我に繋がりうる危険な行為は避けなければなりません。
要領を得て段取りが良くなる
トクニ工業では金属の板を曲げるベンダー加工の工程があります。初めて取り扱う製品は、加工条件を調整したり、曲げた製品を効率よく重ねたりするための調整が必要になります。2度目3度目と回数を重ねていくと、前回の経験を活かして作業できるため効率的に行う事が出来ます。
ベンダーの加工データはLANでサーバーと繋がっているため、過去の条件を呼び出すことが出来ます。同じ機械を使って同じ作業を行う場合、ほぼ同じ条件で加工することが出来ます。
また別の機械を使う場合でも、同じ機械メーカーの為、曲げデータを流用することが出来、段取り時間の短縮につながります。
機械のメリットはもちろんありますが、作業者が工程全体を見通して作業することで、迷いのないスムーズな動きが出来るようになります。余裕ができると次工程の作業内容を想定することが出来、どのような受け渡しをすると次の工程の人が作業しやすいか、どのような重ね方が効率的なのかなどの工夫をすることが出来ます。実際の作業時間は変わりませんが、次工程の作業効率化を促すことで全体の作業効率を上げることが出来ます。
作業に慣れてくると不良の発見にも寄与することが出来ます。
同じものを継続的に扱っていると、同じものと異なるものの違いを見出す感覚が研ぎ澄まされます。不良が混入した際には違和感を覚え、不良の早期発見に繋げることが出来ます。
不良は発生しないことに越したことはありませんが、ものづくりの現場ではどうしても発生してしまいます。いかに早期に発見し、対策を講じるか、再発防止策の策定を進めるかが重要になります。
別のスタッフに作業内容を伝授する
何度も繰り返し行われる作業は、一人だけで行うより複数で取り組んだ方が生産量が増し、完成速度を速めることが出来ます。また他の作業と重なった時などは、別のスタッフと作業を分担して行う必要があります。
別のスタッフに作業内容を伝える時は、作業の内容や品質、ポイントとなるところなどを共有する必要があります。特に自分が苦労したところや失敗履歴などを伝えることで、同じ過ちを繰り返さないよう努めなければなりません。
一日くらいでは代わり映えしませんが、五年・十年と長期のスパンで振り返ると習熟度は明らかに上がっています。特に手を使ってものづくりに携わっているからでしょうか、手が記憶していく要領が増えていくような気がします。
この記事が気に入ったらサポートをしてみませんか?