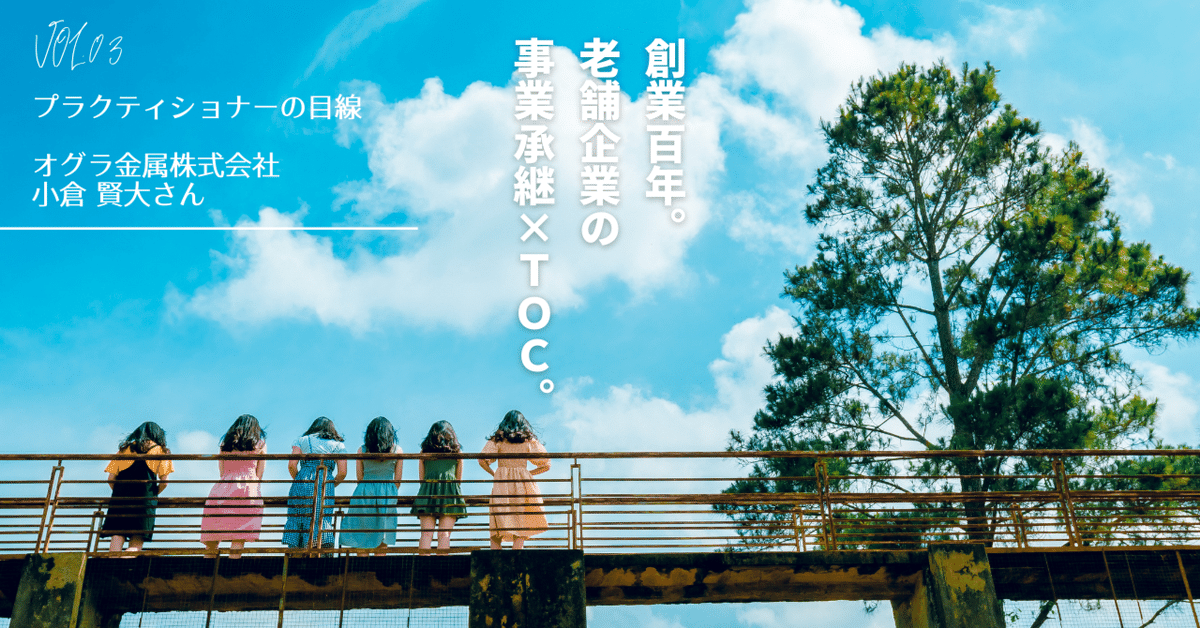
創業100年。老舗企業の事業承継×TOC。
今回は、2019年の第44回TOCPA国際カンファレンス、および2020年のTOCインダストリーフォーラムでご発表いただいたことのあるオグラ金属株式会社(以下、オグラ金属)の小倉賢大さん(同社常務取締役)にお話を伺います。オグラ金属は、1922年(大正11年)の創業から今年で100年を迎える老舗企業で、現社長の小倉勝興さん(賢大さんのお父様)が5代目になります。今、日本のモノづくりを支える多くの企業が事業承継の問題に頭を抱え、優れた技術や地域雇用が失われる危機に直面しています。そこで小倉さんには、次世代経営者への「事業承継を支えるTOC」といった観点も踏まえながらお話を伺っていきたいと思います。
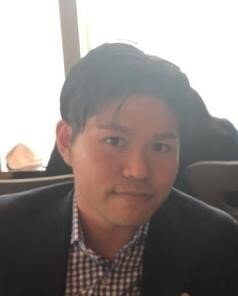
常務取締役 小倉賢大さん
1)いつごろからオグラ金属へ入社を考えたのですか。
-慶應義塾大学からウェディングプランナーへ。
小倉:大学時代、実はオグラ金属への入社は考えていませんでした。むしろ、製造業とは別の世界で挑戦してみたいという思いの方が強く、ウェディングプランナーという世界に飛び込みました。「実家を継ぐ」ということは、心の奥底には常にあったのですが、就職活動中は、家業を継がずに違う世界でやってみたいという反発心の方が強かったように思います。
-関東職業能力開発大学校での2年間
小倉:ウェディングプランナーとして約2年間働き、「このまま会社員として進むのか、それとも経営に携わっていくのか」ということを考える岐路に立った時、オグラ金属で経営に関わっていきたいと思い、入社を決断したんです。ただ、ずっと文系でやってきた私が、いきなりオグラ金属に入ってもやれることがありませんし、また両親からのアドバイスもあって、関東職業能力開発大学校(以下、能開大)に進学して「モノづくりの基礎」を学ぶことになりました。そこでは、プレス、溶接、設計、保全など、モノづくりに関する一通りの基礎を一から勉強し、資格取得にも取り組みました。
慶應を出て、一旦はウェディングプランナーという華やかな世界に飛び込んだ私でしたが、その後の環境は一変しましたね。髪の毛もぼさぼさのまま、毎日作業着を着てモノづくりの基礎を学ぶ、そんな楽しい日々を2年間過ごしましたが、今思えば、自分より何歳も年下の人たちと一緒に学べた時間が私の財産となっています。
-オグラ金属入社後
小倉:能開大を出てオグラ金属に入社した後は、4カ月ほどの現場研修を経て外部に出向し、品質保証や営業の経験を積みました。最初に出向した製造関係の商社では、全く新しい自動車部品の品質立上げ業務に携わったのですが、能開大でモノづくりの基礎を学んだといっても、品質保証については全くの素人でしたから相当揉まれましたね。毎日遅くまで仕事一色の日々でしたが、「大手カーメーカーが考える品質保証の仕組みや流れ」というものについて、座学では得難いものを学んだ貴重な機会でした。
2)TOC(制約理論)のことはもともとご存じだったのですか。
-お寺の住職との出会い
小倉:実は、オグラ金属入社前からTOCのことは知っていました。社会人になってすぐ、ウェディングプランナーをしていた頃に、「借景」で有名な京都の圓通寺を訪れる機会があったんです。自動車関係など、製造業の設計者達が訪れることでも知られるこのお寺の住職から、書籍「ザ・ゴール」を紹介されたのが最初のきっかけです。でも、あの本は分厚いですからね。当時は、全部読んでなかったと思います(笑)。
3)オグラ金属復帰後、すぐにTOC導入を決断されたのでしょうか。
-オグラ金属への復帰
小倉:出向先から戻り、2018年にオグラ金属に復帰してからは、経営会議などに参加し、社内の問題や混乱状況を目の当たりにするようになりました。それまで好調だった自動車関係の仕事が落ち込む一方で、新しい顧客の獲得が進んでいましたが、新しい仕事のみならず既存の仕事でも品質不具合や納期遅延の問題が頻発しており、当初目論んだ利益が確保できておりませんでした。製造現場は度重なる問題への対応で生産キャパシティが逼迫していましたから、営業部が新しい仕事を取ってきても協力工場に出すようになり、生産対応可能な社外の工場を探すことが常態化していました。そのような状況を「オグラ金属は商社か?」などと揶揄する声も社内に上がっていました。やがて遂には、「取引顧客数を減らそうか」といった議論まで出てきた時、「TOCなるものがあるのですが、これをやってみてからにしませんか」と提案したんです。
-TOCは良く分からん。
小倉:TOCを提案した後、 主要メンバーに「ザ・ゴール」のコミック版を読んでもらったんですが、「よく分からん。」という反応でした。そこで、TOCのエキスパートに来社してもらい、TOCの講義をしてもらったんです。それでも「やっぱり良く分からん。」という反応が大半だったのですが、CRS(Current Reality Study:現状調査)を通じて当社の問題点をずばり指摘された時、大きく潮目が変わったのを記憶しています。社内の主要メンバーは、「ソリューションのことはまだよく分らんが、なんで自分たちの問題が分かったんだ。」と驚き、その結果TOCエキスパートへの信頼感、期待感が一気に膨らみ、「もしかしたら(今の状況を打開できる可能性があるかもしれない)」という方向へ傾きました。当時の私は、オグラ金属へ復帰して間もなかったため、まだ内部の問題構造を理解しきれていませんでしたし、TOCの知見もありませんでしたから、エキスパートによる現状調査と問題分析は大変有難いものでした。
4)TOC試行時は、どなたかが手を挙げられたのですか。
-半信半疑からのスタート。
小倉:誰かが手を挙げて、さあやってみようとなったわけではないんです。正直なところ、この段階では私も含めて他のメンバーたちも、まだ半信半疑でした。「投資もしないのに考え方だけで何とかなるなんて、そんな魔法の杖があるのか。」という反応が大半だったと思います。そこで、本格的なCRSをやってみようということになり、ジュントスコンサルティングの白土さんに関わっていただくことになりました。
2か月という時間をかけて入念な現状調査をやっていただいて、いざ社内プレゼンという段取りになったのですが、私自身はこの段階でもまだ半信半疑でしたので、白土さんに社内プレゼンをやってもらったというのが実情です。白土さんのプレゼンを伺っても、やはり「まだ良く分からない」という反応が大半だったのですが、最終的には「失敗してもよいから、駄目元でやってみようじゃないか。」ということになりました。
-手溶接チームでの2 Tier CCPM試行
小倉:最初に試行したのは、生産キャパ不足や納期遅延など最も大きな問題を抱えていた「手溶接チーム」でした。おそらく製造業で2 Tier CCPMを適用した事例は、当時国内にまだ例がなかったのではないでしょうか。現場から反対されたり、怒られたり、色んなハードルがありましたが、駄目元でチャレンジしてみたら、結果的に効果があったんですよね。最も大きな問題を抱えていた手溶接チームで結果が出たんだから、他でもやってみようじゃないかという機運が生まれていきました。
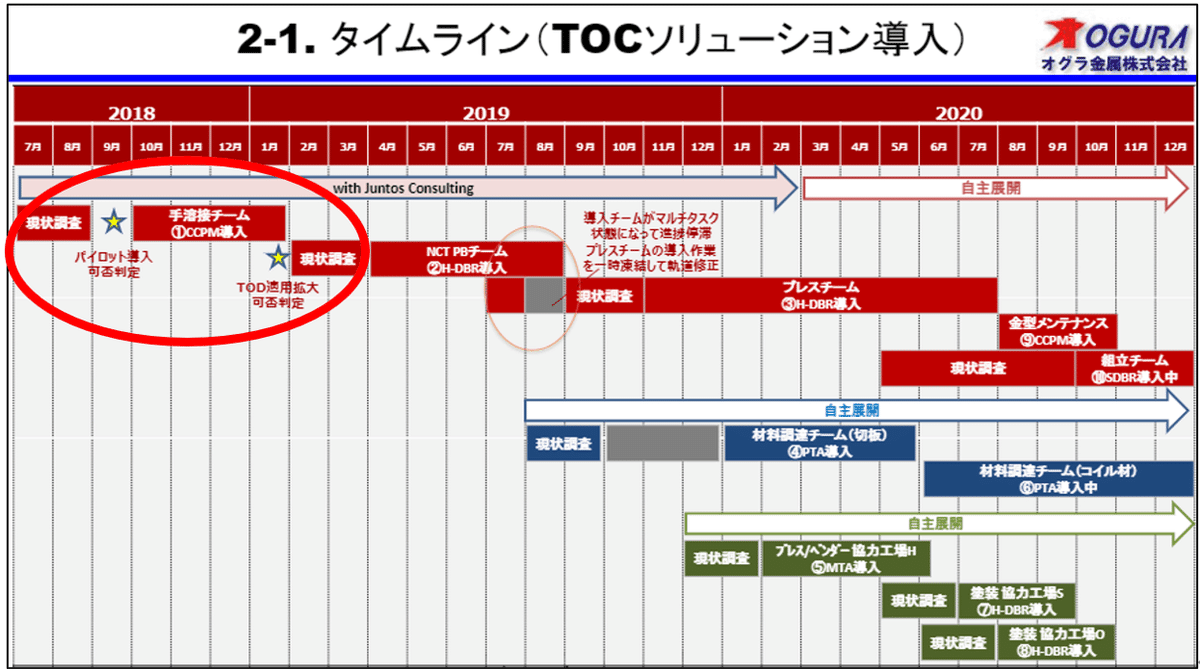
-エキスパートの「姿勢」から学んだ大事なもの
小倉:TOCソリューションの試行から本格導入まで、TOCの根幹をなす「3つの基本仮定*」を実直に実践される白土さんの姿勢には、私も製造部長も感銘を受けましたし、大きな影響を受けました。ただ単に「やりなさい。」というスタイルではなく、ソリューション導入に伴う懸念点があれば、それが障害なのか、あるいは副作用なのかを注意深く聞きとって分析し、一つ一つ丁寧に対策を講じる。そして、全ての準備が整って初めて導入するというステップを、根気強く実践していかれる姿に感動し、「自分達もそうありたい」と強く思ったんです。これは今現在も、私と製造部長が最も大きな影響を受けている点であり、TOCの理論やソリューションももちろん大事なんですが、それ以上に大切にしていかなければならないことだと思っています。
*3つの基本仮定:TOCの根幹をなす基本仮定として、①「Convergence(収束)」、②「No Conflict Between Local and Global(部分と全体の間に対立はない)」、③「Respect(尊重)」の3つが定義されています。TOCPA School Japanのモジュール1「制約を軸にしたマネジメント(2日間)」の冒頭で解説されます。
5)独自のマネジメントシステム「QCD+DM」を掲げておられますが。
-Dは「開発力」、Mは「マネジメント」
小倉:「QCDDM」とはオグラ金属の現会長が謳ったものなのですが、QCD(品質・コスト・納期)は当然のこととして、DはDevelopment(開発力・技術力)のD、そして経営品質を上げていこうということでManagement(マネジメント)のMをとって、QCD+DMとしました。今になって、経営品質とTOCは非常に親和性が高いことに気付きました。ただTOCの知識体系で用意されている各アプリケーションは、「具体的にどうするのか」というところまで、しっかりと補完してくれていると感じています。
-継続的な社内教育
小倉:2019年に取締役となり、TOCの全社導入プロジェクトを推進する立場になってからは、私自身がTOCPA School Japanで「TOCコア、サプライチェーン、思考プロセス、現状調査、プロジェクト・マネジメント」といったモジュールプログラムを受講して学びながら、自社の経営陣や部長メンバー、グループリーダーに至るまで、特にTOCの基本仮定を大切にしつつ、自分の言葉にして伝えていくよう努めました。2020年からは、TOC開発センターを設置し、少数精鋭の集中的な勉強会を継続的に実施しています。
さらには、営業部や品質保証部からのニーズを受けて、「TOCの基礎とスループット会計」の勉強会を実施しました。製造の状況をみながら「何を、どう受注すべきか」といった受注管理の考え方を学ぶことで、営業部門には『製造との関係性を慎重に考えて、きちんと話し合いながら受注活動を行う意識』が芽生えました。また品質保証部においては、なかなか品質活動をお金に紐づけて考えることがなかったのですが、「品質を良くすることでどれだけ利益貢献するのか」という視点を持つのに、スループット会計の考え方が有効だったと感じています。
2021年からも、引き続きTOCソリューション(MTO、MTA、CCPM)の勉強会を継続していますが、参加メンバーについては、既にソリューション導入済み部署の責任者なども、改めて『考え方を学びなおす』という意味で参加してもらっています。ソリューションを導入したといっても、例えば2 Tier CCPMの導入部署では「リソース集中がうまくいかない」など、根底にある考え方の理解が不十分なためにうまく運用できないケースも見受けられましたので、学びなおす機会を意識的に用意し、メンバーが自主的に継続的改善をできるよう心がけています。

6)TOCの知識体系をフル活用されていますね。
-TOCを経営戦略に活かす。
小倉:まだありますよ。TOCフローアプリケーションの導入と並行して、2019年の後半からはMT(Management Tool:TOC思考プロセス)を活用した会社全体の変革にも取り組み始めました。部長とグループリーダーを対象にしたMT研修も白土さんにやってもらいましたが、2020年には戦略合宿を張って、マインドセットからオペレーショナルエクセレンス、そしてバリューオファーの設計まで行いました。戦略立案から戦術を導入、実行するまでは、マインドセットや全社指標の変更だけでも丸1年はかかりましたね。
-自分達で考え、インジェクションを出す。
小倉:「継続的改善」ということで、昨年2021年後半からは、UDE(Un-Desirable Effect:好ましくない結果)の洗い出しを再度実施ました。前回UDEを抽出したのが2019年でしたから、当然ながら前提も変わっているだろうということで再度全部署の管理者へヒアリングを行ったんです。2019年当初にあった納期遅延や品質不具合などの問題は大きく軽減されていた一方、新たな別の問題が目立つようになりました。そこで、ここからは白土さんに頼らず、自分たちで考えていくことを選択したんです。いつまでも頼り続けてしまうと、本来自分達で考えるべきことまでお願いしてしまうことになりますよね。ですから、自分達で問題を分析し、自力でインジェクションを捻りだしていくことにしました。私の他、取締役と部長の7名で毎週セッションをやっておりますが、自分達で考えることで、徐々に思考を深めていく力が付いてきて、TOC思考プロセスを実戦に活かせるようになってきたのを実感しています。
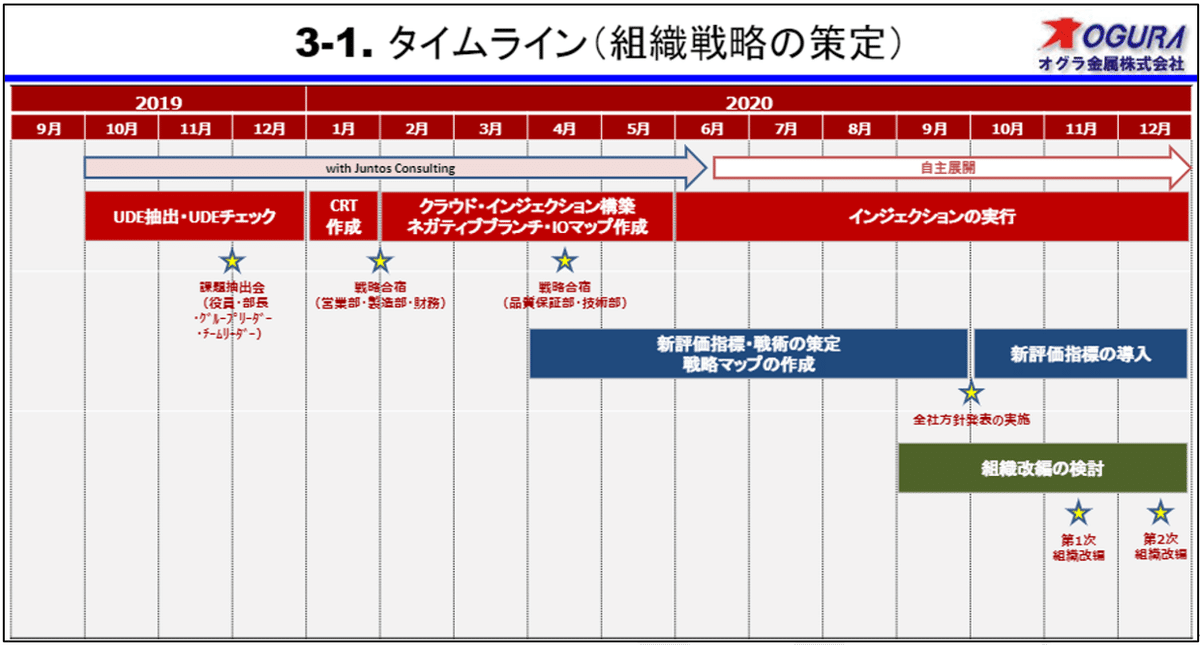
-最後に、「事業承継とTOC」について。
小倉:現社長は、現在、TOCに全幅の信頼を寄せています。全社員の前で話をする時も、「TOCをベースに会社を成長させていく」ということを公言しているほどです。しかしながら、これは決して私がお願いしている訳ではないんです。
「事業承継」において、世間でよく耳にするのは、後継ぎが総務部に配属されたり、営業で実績を残してから役員に就任したりといったイメージがありますが、私の場合は、製造部で関係メンバーと共に改善していくというスタイルから入って現在に至っています。ここまでを振り返って良かったと思えるのは、私自身がTOCを勉強し、本業である製造現場のメンバーや管理者にそれを伝え、一緒に課題解決に当たってきたことが何より嬉しく、また安心できることだと、社長である父が受け止めてくれていることです。最初の頃は、「TOCで会社を変えるぞ!」と、独りよがりのまま突っ走ってしまったこともありましたが、やはり自分独りではできないことですから、皆の協力を得て進めていくことの大切さを認識し、今に至る次第です。
あとがき
小倉さん、今回はインタビューにご協力いただき有難うございました。今年で創業100周年を迎えられるオグラ金属様ですが、小倉さんご自身が精力的に学ばれ、それを伝えていかれる姿には頭が下がります。大事にされている『Respect(尊重)』の精神が受け継がれていく限り、更に素晴らしい企業へと発展していかれることを確信します。また、TOCの知識体系を習得し、実践してこられた今、同社事業の一つとして研修や改善支援サービスを展開し、日本の中小企業に貢献していかれることも視野に入れておられるとのことですので、今後益々、ご活躍の場を広げていかれることを祈念しております。
会社概要
会社名:オグラ金属株式会社
所在地:栃木県足利市
創業:1922年(大正11年)
資本金:9,900万円
従業員数:350名
事業内容:鉄、アルミニウム、ステンレスの金属加工
小倉 賢大氏の略歴
2011年 慶應義塾大学 卒業
(株)Plan.Do.See. 入社
2013年 関東職業能力開発大学校 入学
2015年 関東職業能力開発大学校 卒業
オグラ金属(株) 入社
現場研修後、(株)NCネットワークに出向
加工事業部にて新規立上げ自動車部品の品質保証業務に従事
2016年 (株)メタルワンに出向
薄板事業部 東京薄板第一課にて、国内営業業務に従事
2018年 オグラ金属(株) 復帰
現場研修後、製造部 生産管理グループに配属
2018年秋よりTOCの試験導入を開始
2019年 取締役として、TOC全社導入プロジェクトを推進
2021年 常務取締役就任(現在に至る)
事例発表
第44回TOCPA国際カンファレンス -2019年11月18日
「TOCを活用した金属部品加工業の製造革新」~手溶接工程へのCCPM適用と、板金・プレス工程へのMTO/MTAハイブリッド生産方式の適用
TOCインダストリーフォーラム -2020年11月27日
「TOCソリューションの社内展開と、TOC思考プロセスを活用した組織戦略の策定」
本記事に関するご質問、その他TOCPA Japanへのお問合せはこちらから。