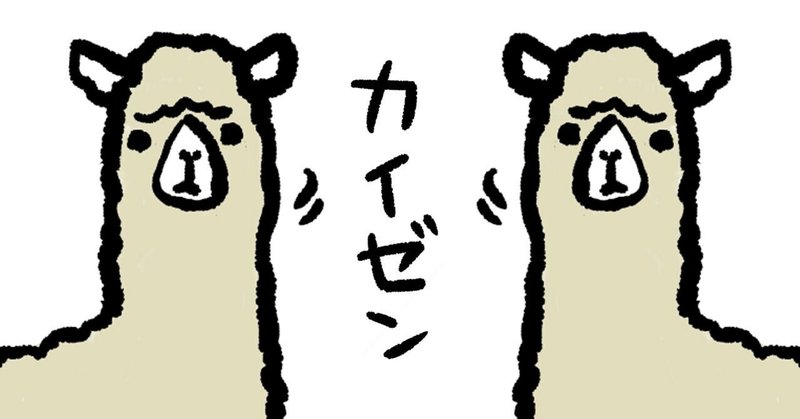
Photo by
soeji
業務改善に大事なことは『トヨタイムズ トヨタ生産方式取材(生産量を「100倍」にしたトヨタ生産方式の秘密)』が教えてくれる
動画のサマリ
100年近く雨がっぱを製造してきた船橋株式会社が、需要過多により不足している医療用防護ガウンの製造を開始する。500着/日しか生産能力を持たなかった企業が、トヨタのカイゼンの力を借りて、有志連合で50,000着/日まで生産能力を爆上げした話。
1. 現場に寄り添う。
外から観察するだけではなく、泥臭くても自らやってみることでしか分からないことがある。また、外から来た人間が偉そうに「こう変えるべき」と主張すると、たとえそれが正しくとも現場から反発を受けて不要な調整等が発生してしまう。入り込んで現場に寄り添って信頼を得ていくことは改善を推進していく上でとても重要。
・自分で1回やってみる。そこからしか我々の仕事はスタートしない。
・現場に来て、まずは寄り添えと。自分も体感してくれと。
・自分でやってみて、どうなの。
2. 流れをおさえる。
業務は一つ一つの作業のリレーによって成立しているので、バトンの受け渡しがスムーズにできている必要がある。作業の流れやそれに伴うヒトやモノの流れを阻害するようなものがあれば、取り除いてあげることで、生産性が向上する。
延反が要なので、すべての工程が手待ちになってしまうので、ここを最初にあげないことには全体の生産性が上がらない。
3. 基準を決める。
みんなが従うべき基準を設定することで、バラツキをなくし余計な手戻りを減らすことに繋がる。うまくできている・できていないの判断基準をつくることで、誰もが同じ認識にたってコミュニケーションをすることができる。
・例えば、目で見て分かること。Aさん、Bさん、バラついてちゃダメ。
・標準をしっかりしましょう。
・誰が引いても、この線上にいく。ズレがない。
・前工程でしっかり基準を決めてしっかりモノを作れと。
4. 数字で話す。
現状がどうで、結果どうなったのか。数字で語らなければ、効果も見えない。数字を語ることで、超えるべきハードルや現在地がクリアになる。
・一枚一分改善している。
・人が一人抜けます。なおかつ9秒でできます。
・2分3分かかった。今だと21秒くらいですね。
5. 改善を止めない。
改善は終わらない。今日のベストは、いずれ陳腐化するし、将来のベストではない。
・異常をちゃんと出そう。止まったことを顕在化させて、改善に導く。
・最初500枚、それが1,000枚になり2,000枚になりました。
以前の我々でしたら2,000枚になった時点で多分満足してた。
その時に、高橋さんが船橋だったら5,000枚いける!って言った時に、
何言ってんだこの人って。って正直思ったんですけど、今もう6,000枚
できるんですよ。
・昨日の記録を超えよう。
この記事が気に入ったらサポートをしてみませんか?