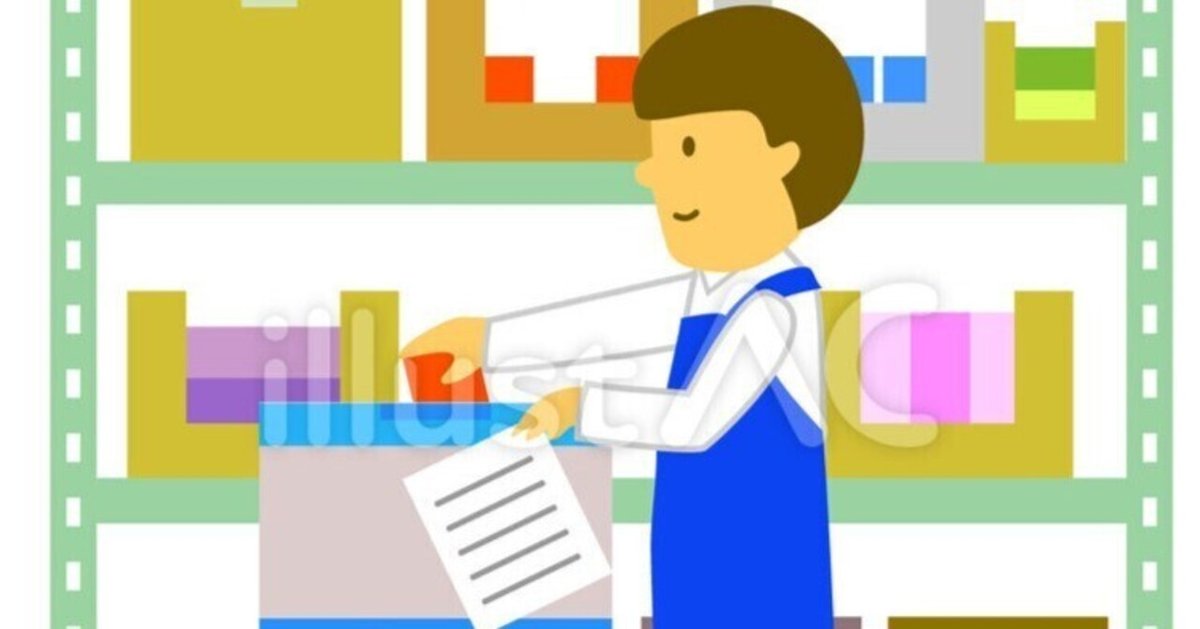
指示書に支配されるな!指示書を支配しろ!ということを学んだ件
現場リーダーたる者、その作業はどのような手順で行うべきかを考え、その手順で作業を行わせるために最適な指示書を出せ!
倉庫内の作業は当然、作業指示書の通りに正確に行わなければなりません。指示書と違った作業を行うと、誤出荷や在庫差異を引き起こす原因となります。
誤出荷や在庫差異は物流倉庫においてはあってはならない事故です。特に誤出荷の頻発は荷主の信用を失い、時には取引問題にまで発展します。
なので、倉庫業者においては誤出荷事故が発生した時は、即座に原因究明と再発防止策を徹底しなければなりません。それでも誤出荷、作業ミスは繰り返し発生します。何故か?それは、ミスの原因の95%以上がヒューマンエラーによるものだからです。ヒューマンエラーをなくすには人間工学の世界に踏み込まなけばなりません。これには大変な努力と投資が必要ですが、この領域にまで踏み込まないと作業ミスは減らせないでしょう。
昨今は、このヒューマンエラーをなくすため、又、人員不足に対応するために各倉庫において機械化が進められています。
古くからのバーコード検品機をはじめ、自動配分機、ピッキングロボット、ICチップの活用、etcさまざまは組み合わせで作業ミスの撲滅が図られています。
人間工学的アプローチも結構、自動化・機械化も大いに結構、どんどん進めるべきだと思います。
ただ、機械化のような大きな投資がなくできることで、見逃しがちなのが作業工程の見直しに伴う指示書の変更だと思います。例えば入荷商品の「棚入れ指図書」ですが、〇〇の商品を~~の棚に△△ケ格納しなさいという指図が出たとして、作業員はその商品を棚に格納しようとして指示された棚の前まで行きますが、その棚にはすでに満杯でもう格納しようにも格納できません。(新人作業員なんかは、そこで立ち往生します)
あるいはピッキングリスト、ある商品を50店舗に出荷する場合に、その商品を50店舗分まとめて棚からピッキングしたいところですが、ピッキングリストが店舗別に50枚出ているとしたら、50回棚に行って50回同じ商品をピッキングすることになります。
そのことにリーダーが事前に気付き、それなりの対応ができればよいのですが、他の出荷指示と混ざって出るようなときには、リーダーといえどもなかなか気付くのは困難です。いわんや現場の作業員においてをや。
先の棚入れの場合では、出したい指図書は棚入れ数ゼロ、延長置き(又はパッキン在庫行)×何ケでしょう。又、上のようなピッキングのケースにおいて、出したいピッキングリストはグロスのピッキングリストとなるしょう。
倉庫の作業員は指図書に忠実に作業をします。又、指導者はそのように指導するでしょう。なるほど倉庫作業は指図書通りに行わなければ作業ミスにつながります。なのでどのような指示書を出すかが作業の精度や効率を左右します。リーダーはそのあたりをよく理解して、どのように作業をしたいか又、させたいかを考えてその作業に必要な指図書を出す工夫が必要ですね。
といううことを、前述の記事の京都のセンターにおいて学びました。
(乱文御免)