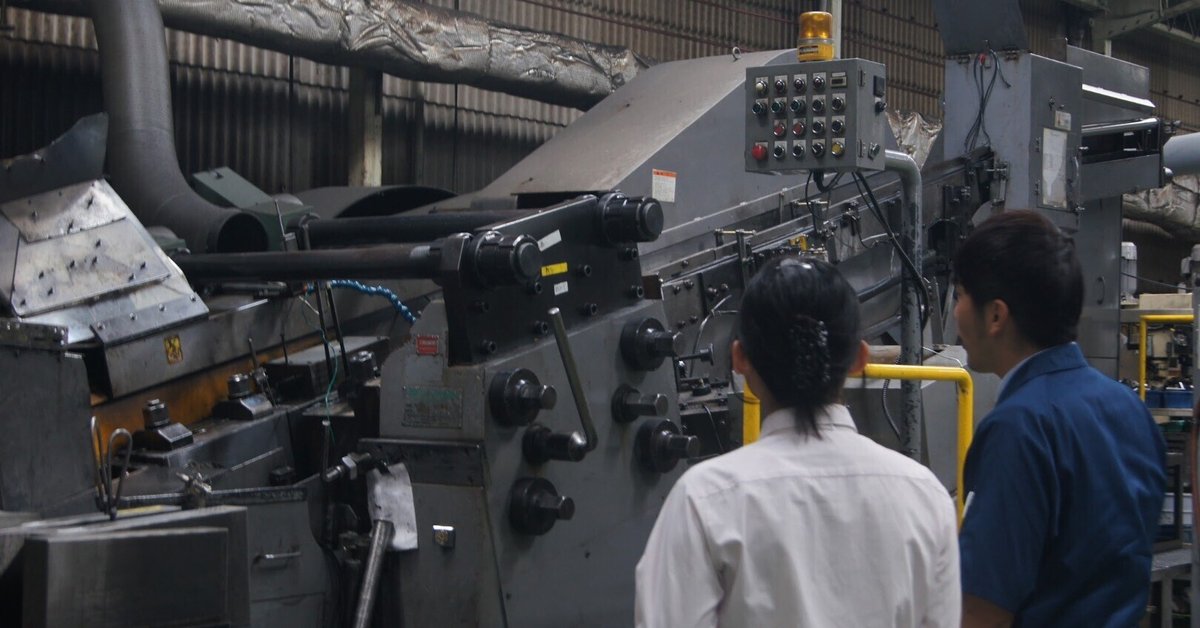
現役高校生・大学生が「ねじ」製作の"ウラガワ"を徹底調査!Part.03 「ねじ」ってどうやってできてるの?
こんにちは!Potential の取材担当のまりこです!
先週に引き続き「ねじ」製作の"ウラガワ"を徹底調査するべくPotential の代表のるなと共に「金剛鋲螺株式会社」様の本社に直接訪問してきました!
今回は「ねじ」について調査します!✨
(Part.02の記事を貼る)
⬆️
Part02のNoteです。ぜひ読んでください!
企業情報
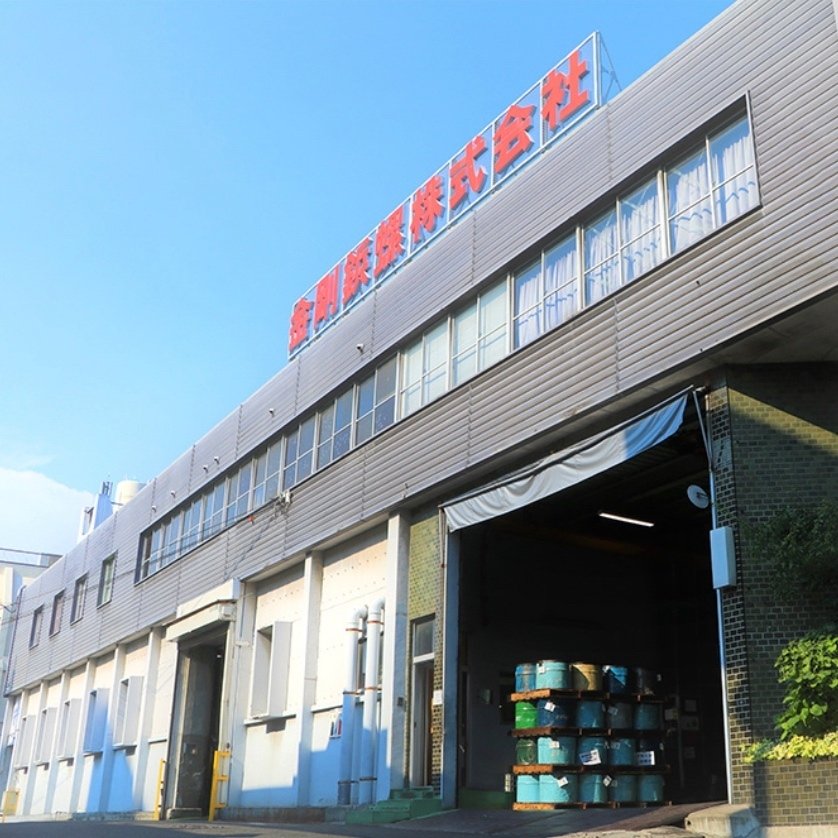
金剛鋲螺(こんごうびょうら)株式会社様は高い品質と豊富な品揃えを誇り、数多くのねじ製品を作っている会社です。
六角ボルトを中心に、座金組み込み六角ボルトや特殊冷間圧迫部品、切削加工部品も取り扱っています。「以和為貴」(和を以って貴しとなす)を社是に置き、Instagramやnoteなどのツールを使った発信にも力を入れています。
創業 1946年5月1日
創立 1956年10月29日
本社
〒577-0016
大阪府東大阪市長田西3丁目5番1号
営業部 TEL (06)6744-3255
総務部 TEL (06)6744-3257
FAX (06)6744-2188
詳しくはこちら
金剛鋲螺株式会社様HP⏬
http://www.kongobyora.co.jp
「ねじ」製造の工程
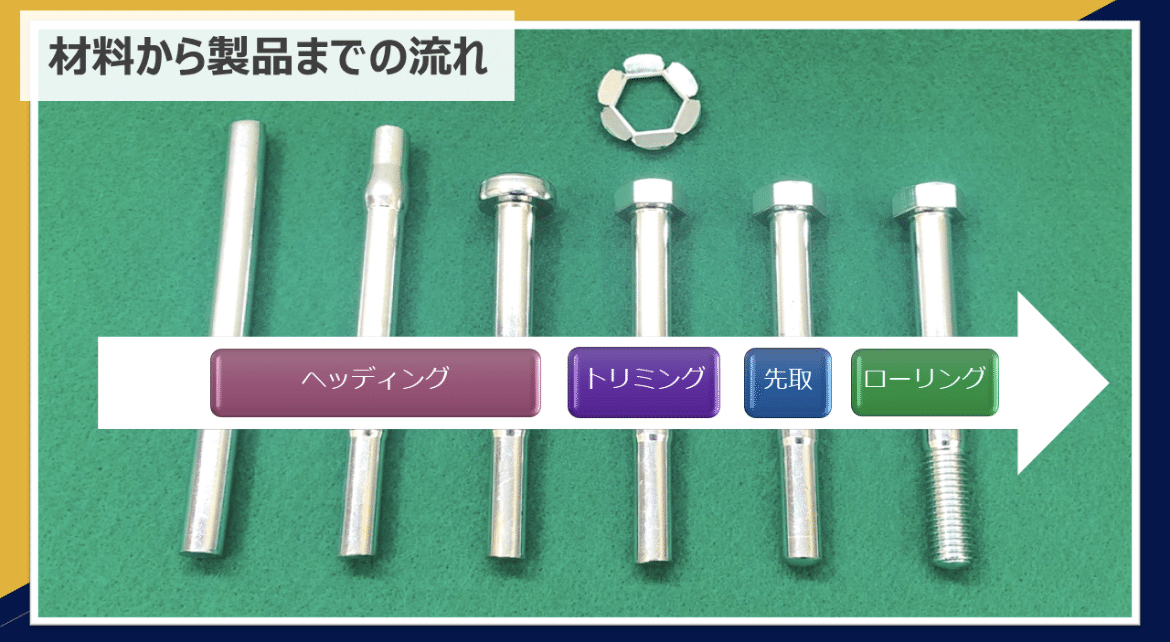
ねじの製造工程は、①ヘッディング工程、②トリミング工程、③先取工程、④ローリング工程、の大きく4つに分かれます。
最初のヘッディング工程は、切断した材料を専用の金型で叩き、頭部を成形する工程です。締結機能の重要な役割を担う頭部が破断しないよう、1回目の予備成形で軽く膨らましてから、2回目の仕上成形で丸くします。
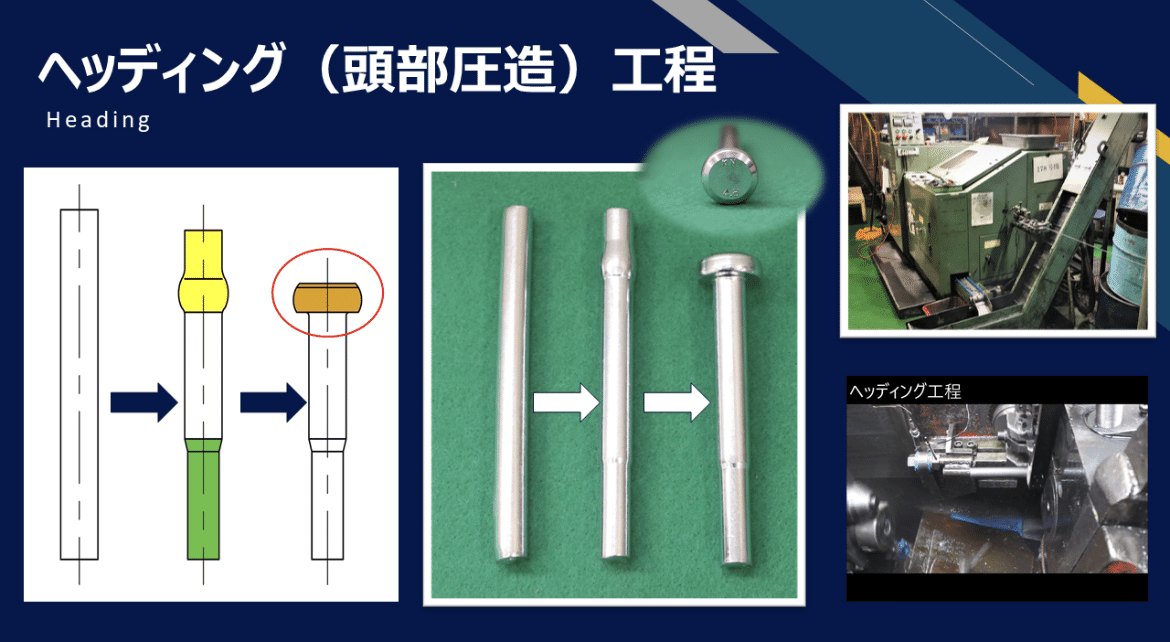
2つ目のトリミング工程は、丸い頭部を六角形に抜く工程です。スクラップ(抜きカス)も大量に発生します。
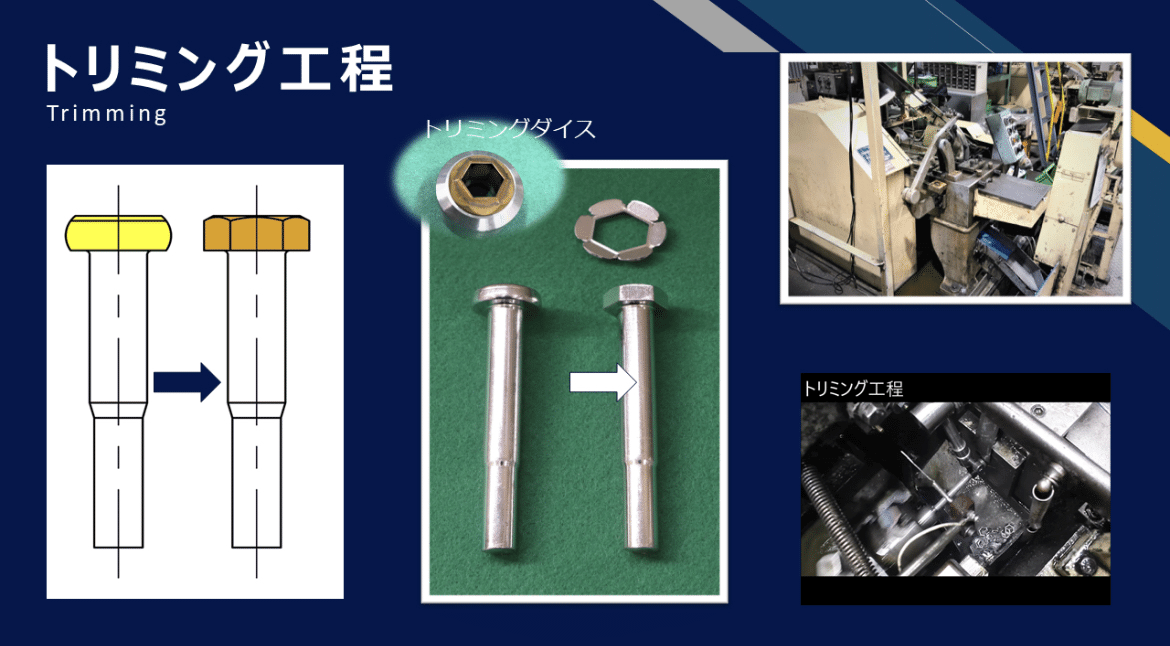
ちなみに、ヘッディング工程とトリミング工程はそれぞれ専用の機械もありますが、ヘッディング工程とトリミング工程を一気に行えるボルトフォーマーという機械が最近の主流です。サイズにもよりますが、1分間におよそ200~250本のねじが製造されます。
まりこの視点👀
取材当日にねじの頭が作られる動画を見させてもらえました。次々とねじの頭ができていき、面白さを感じましたが、普段のスピードで再生されると、目にも止まらぬ速さで機械が動き、圧巻の光景でした!
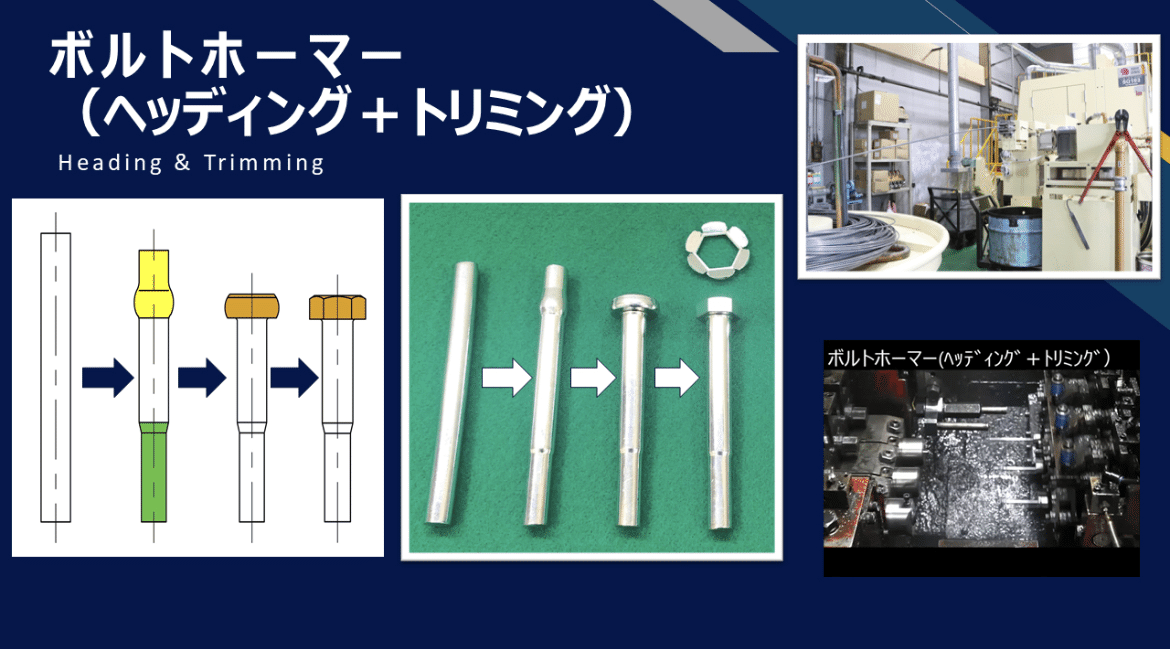
3つ目の先取工程は、ねじ先を削る工程です。先取りバイトという細長い刃物を当てて、丸先形状への加工や、面取り加工を行っています。
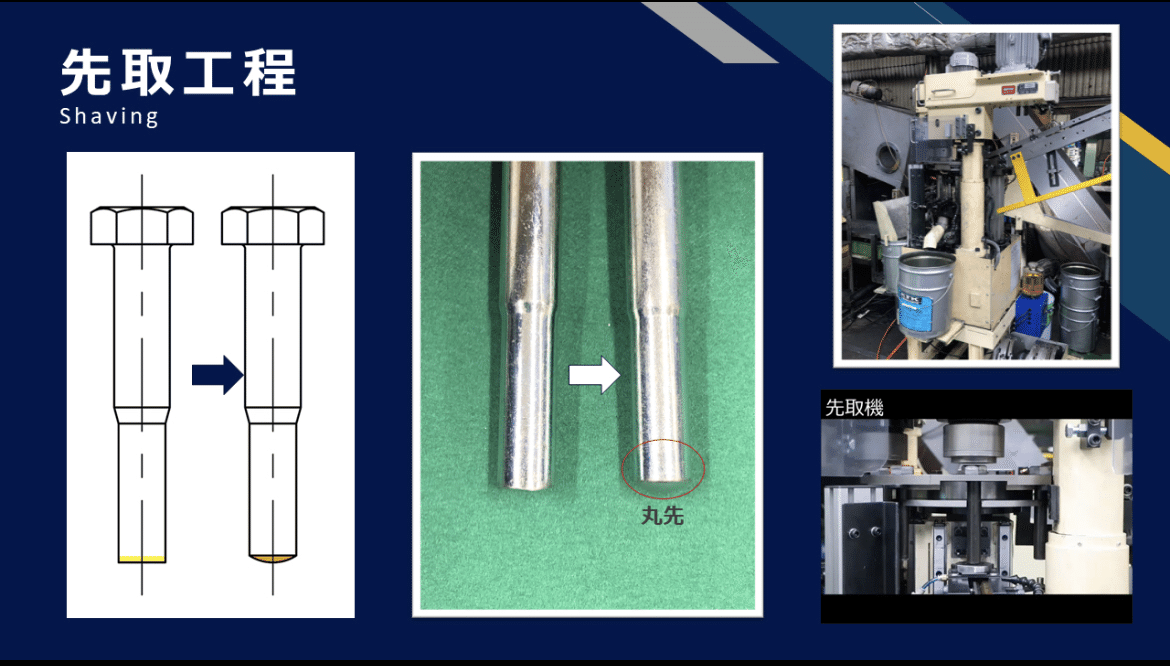
最後のローリング工程は、製品を金型に押し当てながら転がし、ねじ山を成形する工程です。ローリング工程には、ロータリー式と平ダイス式の2種類の工法があります。
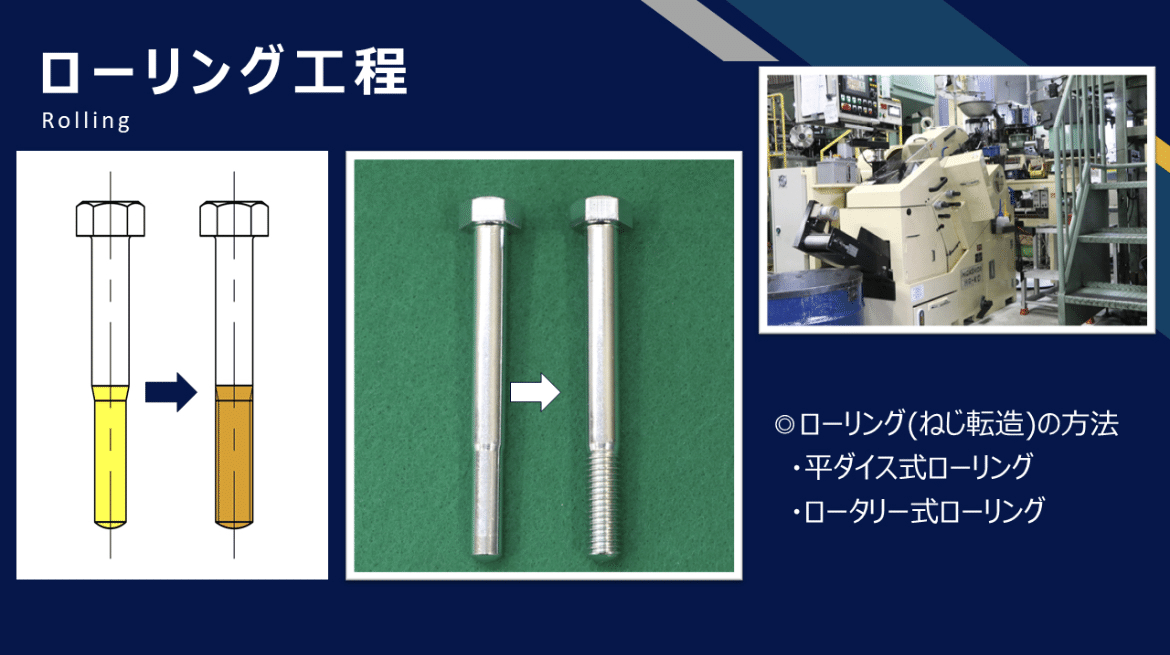
ロータリー式は、丸い金型が回転することによりねじ山を成形する工法です。1回転する間に4~5本のねじが切れるため、大量生産に向いています。
一方で平ダイス式は、直方体の金型が前後にスライドすることでねじ山を成形する工法です。前後1往復で1本の生産となるため、ロータリー式と比べて生産速度は落ちますが、加工性はよく複雑な形状の成形ができます。
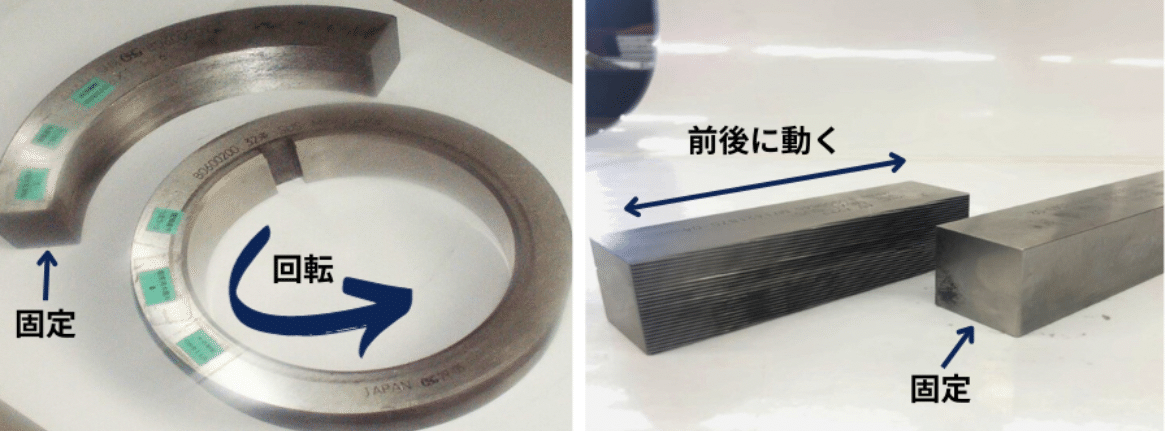
ローリング工程を終えた製品は、加工に使用する油が大量に付着しているため、専用の機械を使い洗浄します。一般的に油の洗浄は水で流すイメージがあるかもしれません。しかし、弊社製品の多くは鉄素材で水だと錆びてしまうため、付着した油を専用の油で洗浄してから、遠心分離機で飛ばします。
まりこの視点👀
油を水で落とす物と思っていた固定概念が壊れるような話でした。油を落とす油が存在していることも驚きです!!
所要時間は製品によって異なりますが、主力製品の六角ボルトは、スムーズに進めば1週間程度で完成します。
「ねじ」製造の現場に潜入!!
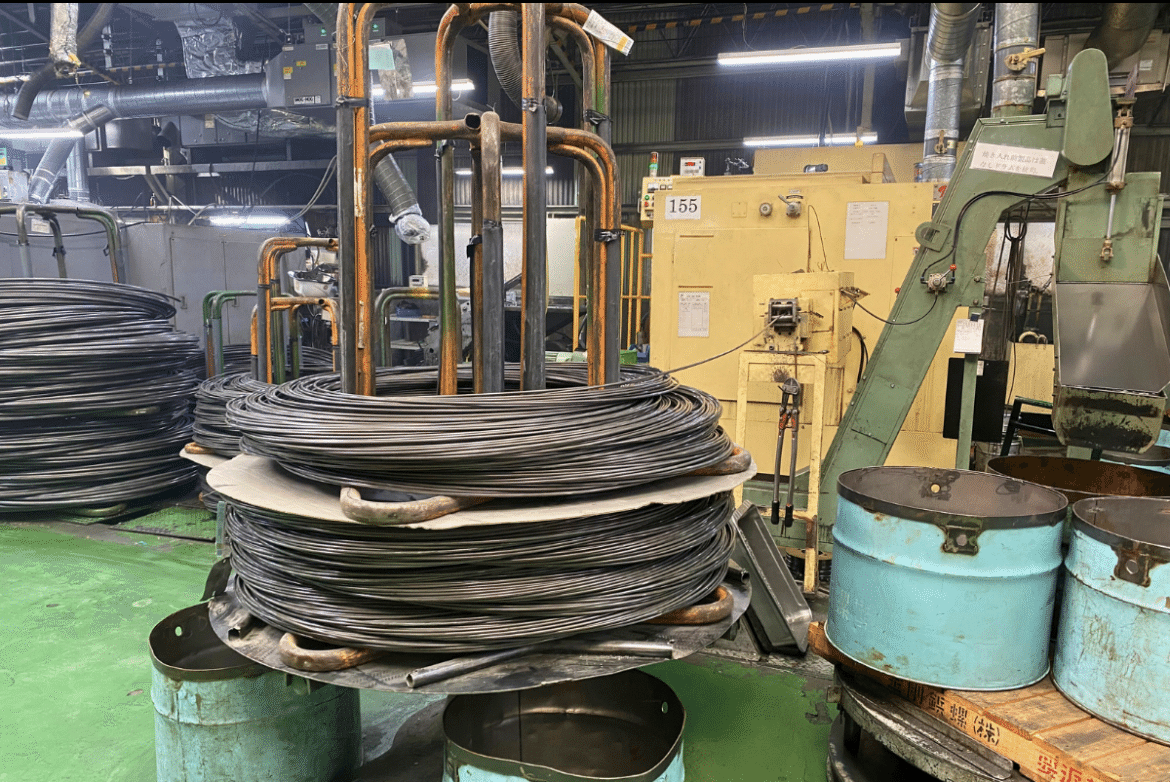
ーーこの巻き付けてある太い針金のようなものはなんですか?
これは、ねじの材料です。さまざまな太さがあり、製品に合わせて使い分けます。材料~製品になる過程で、1割程度はスクラップになります。
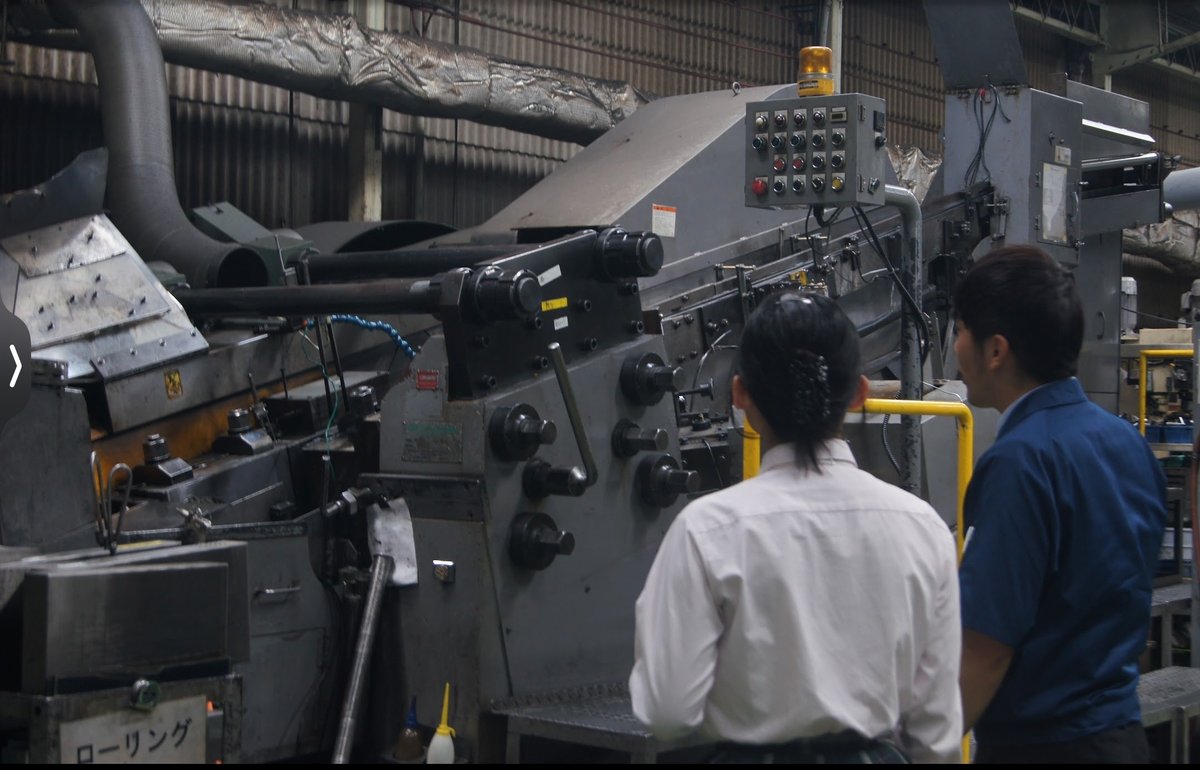
ーーなるほど!この大きな機械は何ですか?
こちらの機械は、ローリング工程で使う機械です。弊社で一番太いサイズのねじを転造しています。真ん中に見える細長い青い管は加工油の噴射口です。加工油をかけることで、金型の摩耗や焼き付きを防止する効果があります。
また、製造工程で油を使用するため、作業中は換気が必要です。夏場は機械付近にスポットクーラーを設置し、できる限り暑さを凌いでいます。
転造・・・素材に強い力を加えて盛り上げて成形する金属加工方法です。
株式会社ニッセーHPより参照
まりこの視点👀
取材日当日の工場内は、機械や従業員の方はいらっしゃらない状態でもサウナのような暑苦しさ。この中で毎日作業するのは本当に大変な仕事であることがよく分かりました!
ーー大変な仕事ですね。沢山あるドラム缶には何が入っているんですか?
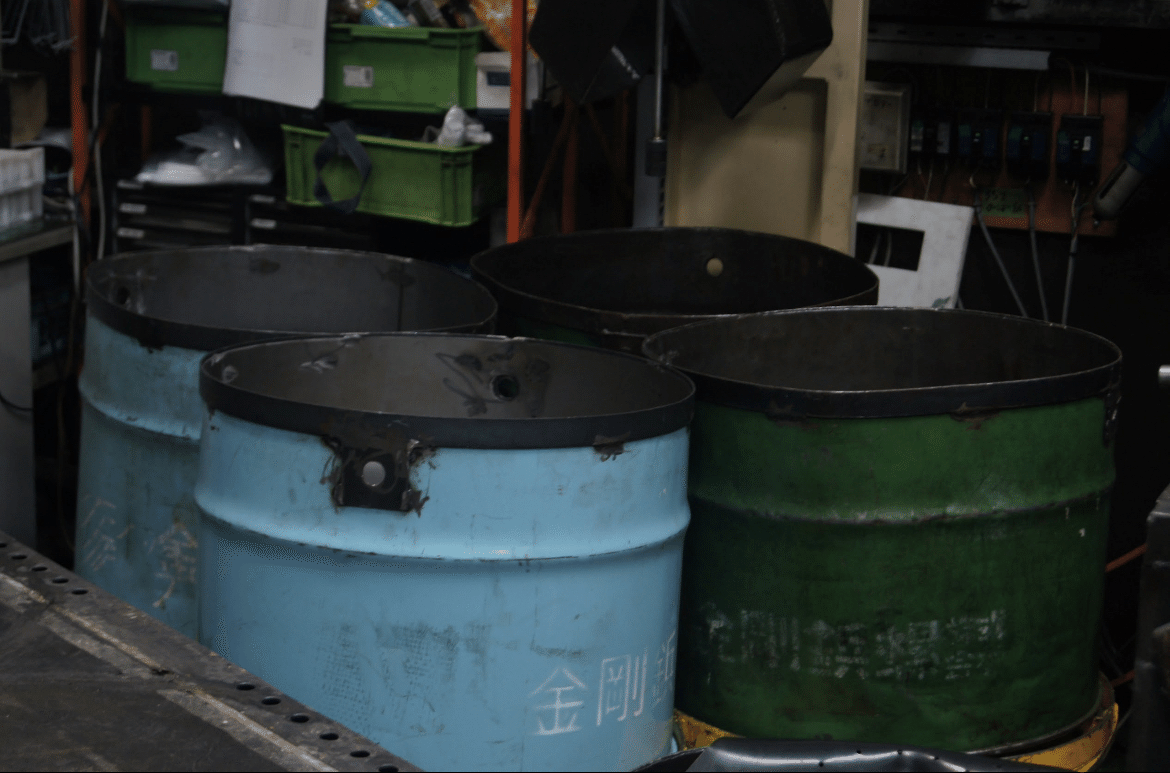
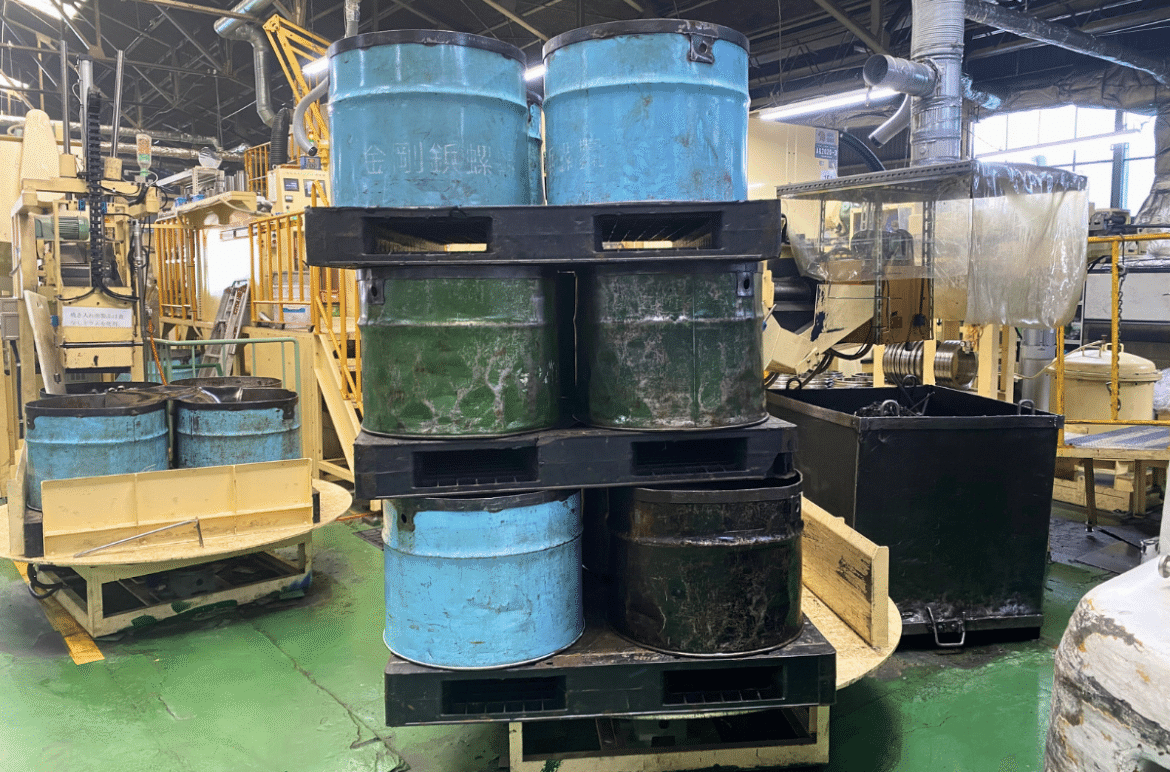
ドラム缶には製造中のねじが入っています。ドラム缶は1缶あたり250~300キロとなるため、ホイストクレーンやリフトを使い、次の工程に移動します。
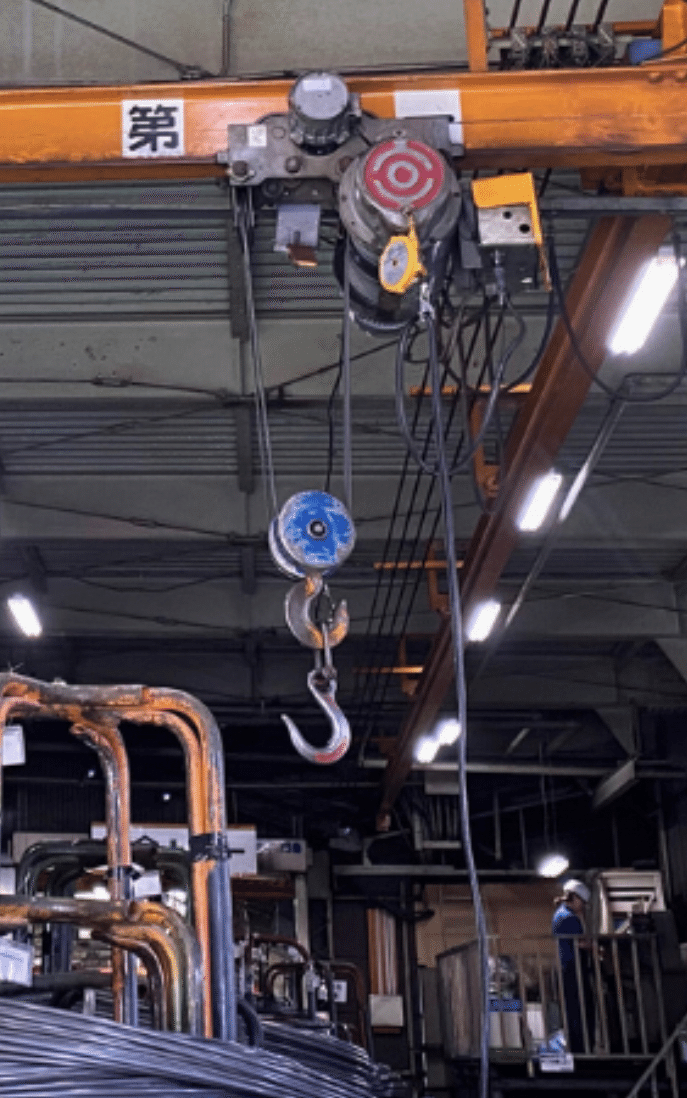
カラフルな「ねじ」の秘密・・・
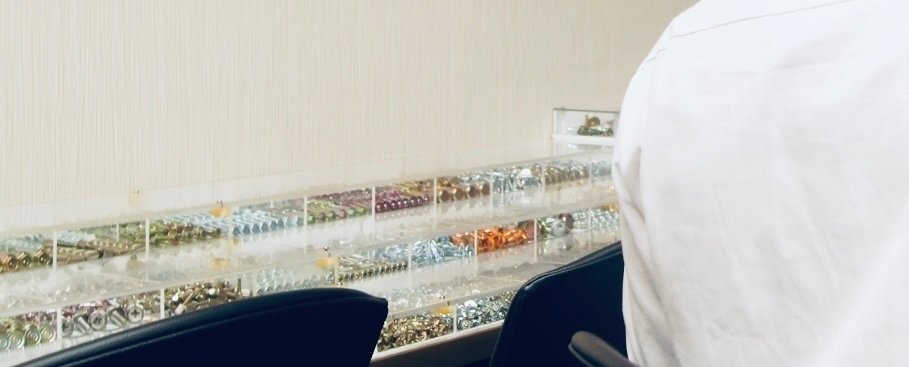
ーーずっと気になってたのですが、すごくカラフルな「ねじ」ですね。
それは装飾めっきの製品です。基本的には防錆(耐食性)を目的としためっき加工が多いですが、お客様のご要望に合わせて対応しています。
ホームセンターで売られているねじも、めっき加工されたものが多いです。ちなみに、弊社はめっき加工の設備がないため、めっき加工専門の協力会社さんに依頼しています。
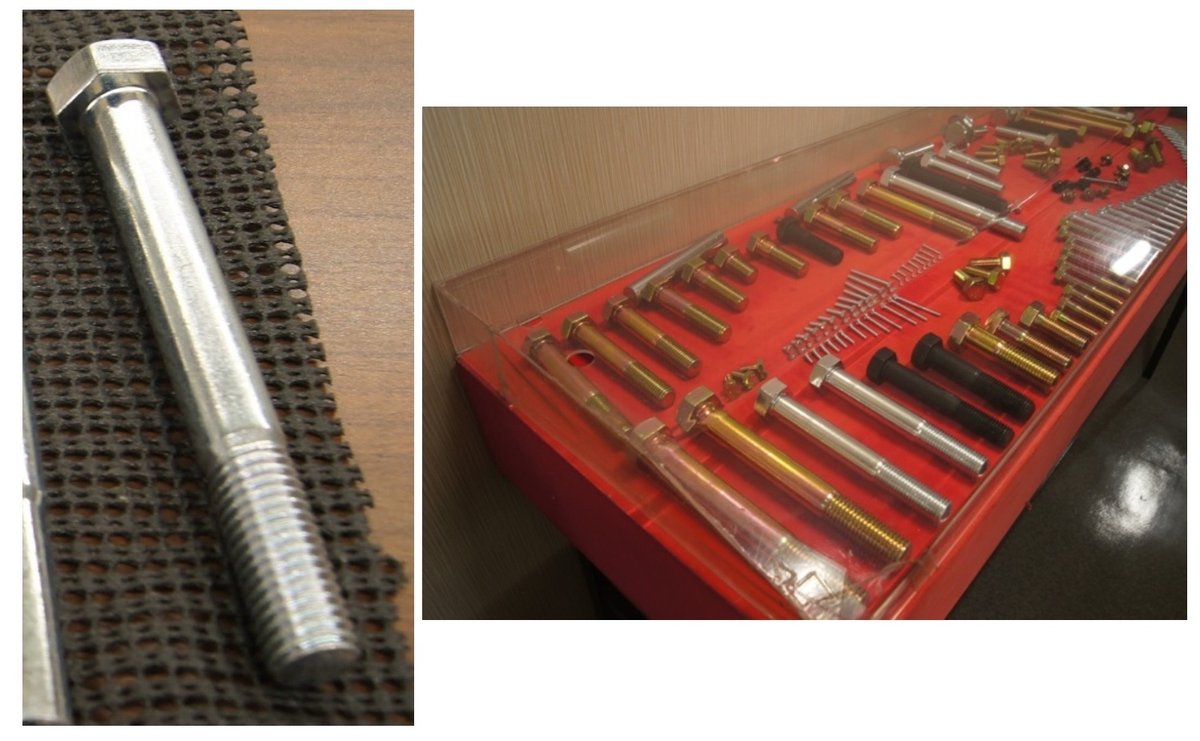
こちらは六角ボルトの製品サンプルです。ねじ山の太さ(呼び径)がそれぞれ異なり、弊社では最小3ミリから最大24ミリまで製造できます。太いサイズの製品は、土木建築で使われることが多いです。
また色味の違いは、めっき種類の違いです。めっきの種類によって錆びにくさも変わるため、用途に応じて使い分けされています。
まりこの視点👀
オレンジや紫色などの今まで見たことのないカラフルなネジの数々。私の知らないねじの世界が広がってことを感じました!
今後の課題
2022年3月に奈良工場が完成し、生産体制は整ってきました。今後は生産能力に応じた売上確保や人材の採用・定着が課題と言えます。
私たちの仕事は機械だけでどうにかなるものではありません。現場でねじを製造する社員の中には、60~70歳の方も多くいらっしゃいます。先輩方が引退される前に技能を継承できるよう、新卒採用には力を注いでいます。
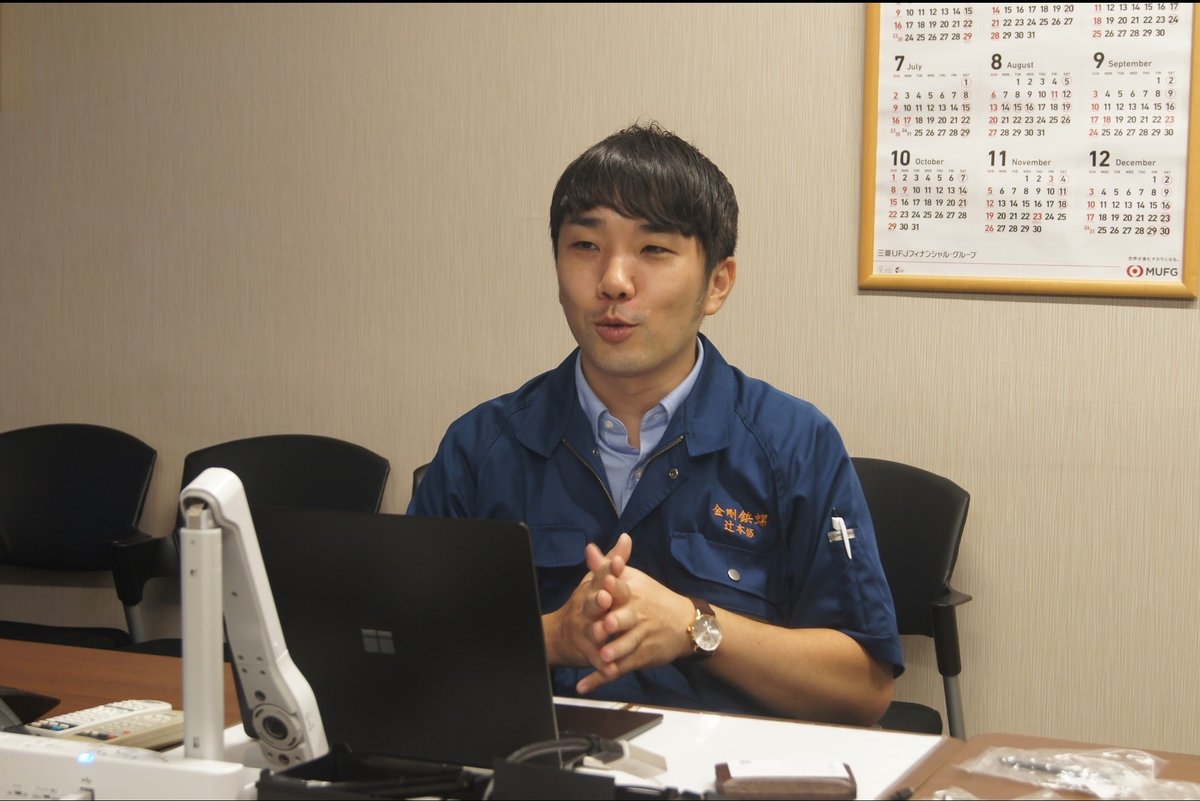
人材求人サイトを使い、新しい人材を集めたり、専門学生や大学生に声をかけたりしています。また、奈良の工場の人材に関しては大学が近くになかった場合は高校生にも声をかけるときもあります。
作る側にとっての「ねじ」とは
ーー辻本さんたちは作る側であり、私たちは使う側にいます。そんな作る側として"ねじ"とはどんな存在であると思いますか
ねじは機能部品なので、ボルトとナットを組み合わせ、締結できることが大前提です。そのため、ねじ単体が目立つ必要はなく、日常を裏側から支える存在になれればと思っています。
ちなみに、ねじは1ロット当たり数千~数万本の単位で製造しますが、1本でも不良品があると、すべてのねじを目視で選別することもあります。もちろん起こってはならないことですが、それぐらい使用場所によっては重要な部品なのです。
まりこの視点👀
ねじ製作の仕事は地味と思われがちですが、大きな責任が伴う仕事。少しのミスで多くの損害が出るという話を聞き、学生では感じづらい社会の厳しさを知りました。
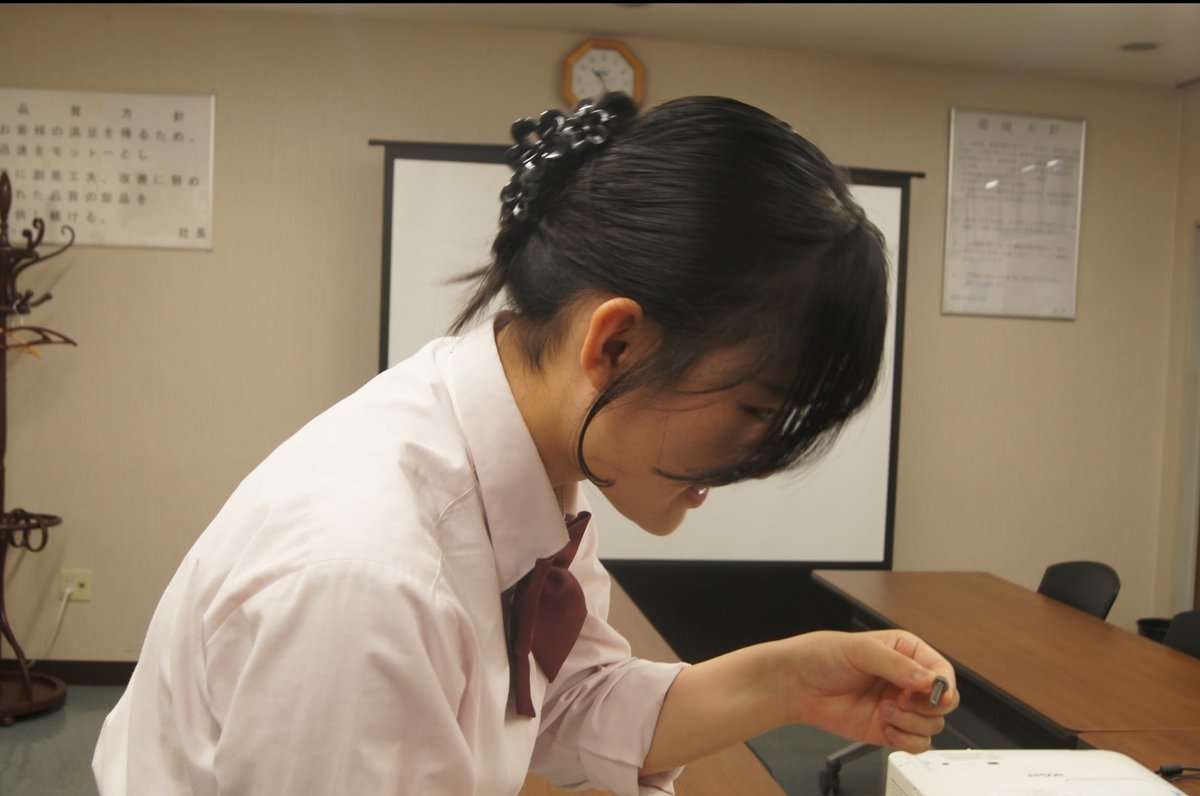
私たちはエンドユーザーさん(消費者)に製品を直接販売していないため、その方々からの声を聞くことは難しいのですが、販売先のねじ商社様から「金剛鋲螺の製品は信頼できる」と思っていただけるよう、製販一体となり期待に応えていきたいです。
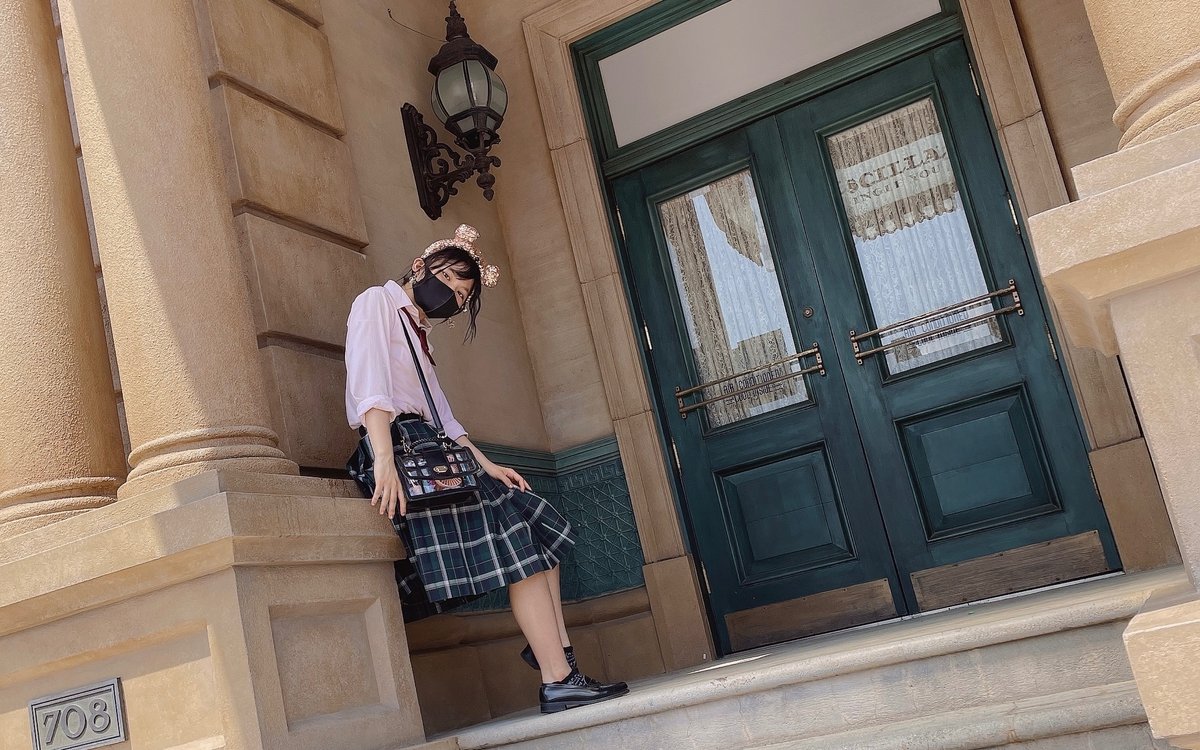
執筆者:丸山璃子
立命館守山高等学校3年生。
滋賀県甲賀市出身。
音楽やアニメが好きで、新しいことにチャレンジすることも好き!
現在はPotentialで取材担当。学校でラジオのMCの一人として活動をしている。学外では、地元の忍者を使ったZ世代向けの商品を開発中!
編集後記
今回のインタビューはpotentialの取材担当として初めてのお仕事!
不安と緊張でいっぱいでした。そんな中、取材日は日光がサンサンと照りつけ、気温も高かったため、肉体的にも精神的にも大変なスタートでした。取材した部屋は涼しい風で冷やされていたので、辻本さんの配慮に感動し、それと同時に普段はこの暑さの中社員さんは工場内で働いていると思うと、頭が下がる思いでした。インタビューに答えてくださった際は、私たちの質問に親身になって答えてくださったおかげで取材は円滑に進み、素晴らしいインタビューが出来たと思います!この記事を少しでも多くの人に読んでくださることを心から願います。協力してくださった金剛鋲螺株式会社様、ありがとうございました!!
ではまたの記事をお楽しみに!!!!!!
是非、potentialのnoteをフォロー、いいねしてくださいね!
PotentialのHPにて電子廃材を使ったアクセサリーを販売しています。
また、Instagramも行っております。是非ご覧ください!
Potential HP⏬
https://www.potential0.me/
Instagram ⏬
https://instagram.com/potential.official0?igshid=MWZjMTM2ODFkZg==
この記事が気に入ったらサポートをしてみませんか?