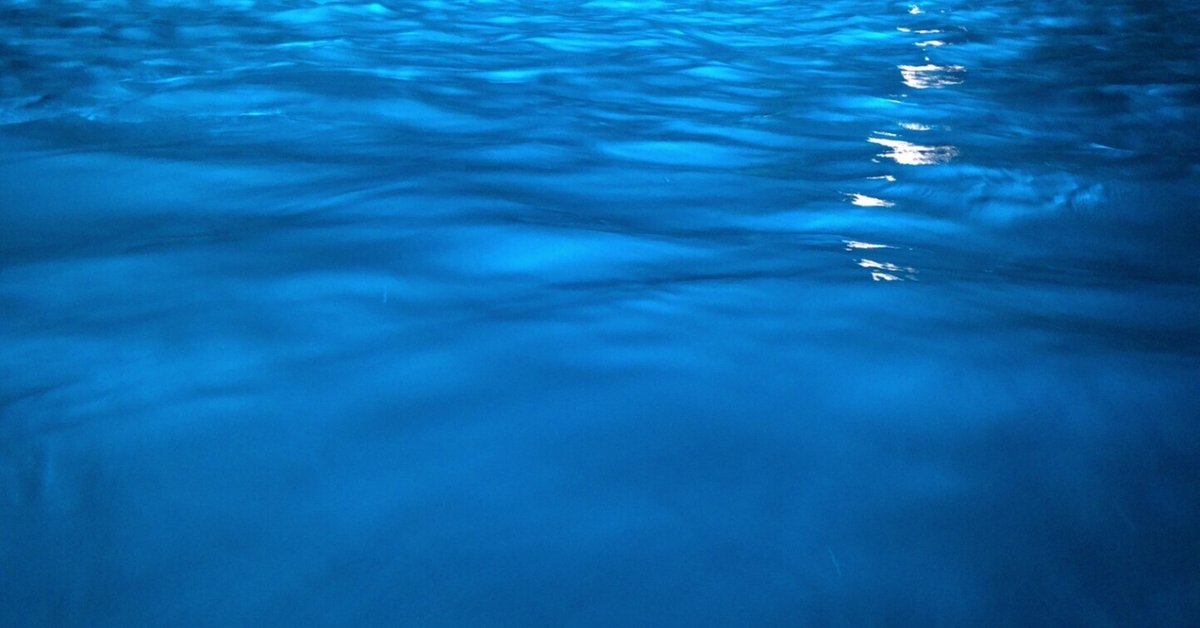
業務に落し込むとは?
これまで大企業から中小企業のいろいろな人達と仕事をしてきました。
製造業を中心に業務をしてきて気が付いたことを記します。
日々業務を行っていると何らかの問題が発生したり、新たな業務が発生したりします。これらに対応出来るように役職者が業務に落し込む、または、組込むことになります。しかし、この業務に組し込むのですがポイントがズレていると機能しないことや、改善が出来ないことが発生します。
役職者であってもこれが上手く出来ない者がいます。
特に製造工場で生産活動していると品質問題が発生することがある。
製造業として数十年も生産活動していれば同様な不具合が発生しており再発防止が出来ているはず?、ですが実際は再発することがあるのです。
これは本質的な対策が出来ていないことで再発してしまう。
製造プロセスの仕組みに落とし込まれていないと、人が変わったり製品が変わったことで結果的に再発が起こる。
事例
製造部門から出荷検査工程に送られてきたものを検査したところセメダイン塗布が全数されていない物が検出された。
この製造工場では、各工程完了ごとに製造経歴票(各工程の履歴)に担当者が日付と氏名を記載するので工程ジャンプ(工程飛び越す)は、起こらないはずでした。
ところが、実際はセメダイン塗布工程が行われず次の工程へ搬送された。
製造工程は、
①組付け工程 → ②セメダイン塗布 → ③最終目視 → ④出荷検査 → ⑤出荷
経緯を確認すると
・①組付け工程担当者(経験ある応援者)が次工程へ運搬時に③最終目視工程に運んだ
・③最終目視担当者は、製造経歴表にセメダイン塗布欄に記載が無かったため当該工程担当のリーダーに記載が無いことを伝えたところリーダーは現品を確認もせず、『記入漏れなので代理記入して』と依頼した。
・③最終目視担当者は、代理記入をして通常の作業を継続して出荷検査へ送付した。
・④出荷検査員はセメダインが塗布されていないことを検出した。
原因を確認してみると
・応援者が、間違った場所に運んだ
・作業エリア全体が次工程の置き場表示が、床のテープ表面に貼ってあるだけ(その場所に行かないと分からない)で、 そこに貼られていることを知っている者しか分からない状態
・リーダーは製品を確認もせず指示をした
最終目視工程に置いてあったので、そうした判斷をした
・最終目視担当者は指示にしたがって代理サインをした
作業漏れを確認しなかった
まとめると
間違わない作業環境の整備が出来ていない。
一人が間違うと歯止めが効かない作業となっていた。
注意深く作業をする習慣が職場に根付いていない。
ミスに気がつく仕組みが無い。
業務に落し込む方法として例えば
この担当係長に聞けば、『応援者に教育していなかったのが原因』
私『対策はどうする?』
係長『職場メンバー集めて伝えます』
私『いやいや、業務に落とし込みをしないと連絡しただけでは再発します』
これは職場運営している管理者のマネジメント不足である。
この事例から係長は、担当者に問題があると結論したが、そうではなく
職場の環境に問題があるので、そこを改善することが必要です。
製品をどこに運搬すれば良いのか分かるアドレスマップを掲示したり掲示板を設置し職場メンバーに伝えるなどして、応援者が来た時点でそれを確認させることで運搬間違いを無くすようにすること。
製造責任者としてヒューマンエラーが起きない環境を日々考え行動しているのであれば問題を防げたこと思われます。
まとめ
製造業における問題を業務に落し込むとは、真の原因を掴むことでありそれをヒューマンエラーが起らないようにすることになります。そもそも、ミスの起きにくい手順や、誰がどう見ても間違えない環境を整えることが管理監督者の業務と言うことです。
この記事が気に入ったらサポートをしてみませんか?