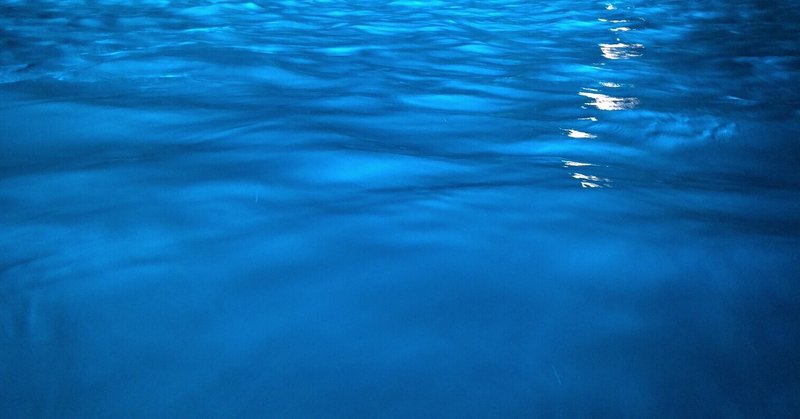
不良対策 作業漏れ
これまで大企業から中小企業のいろいろな人達と仕事してきました。
主に製造業を経験してきた中で、特に品質問題は必ず付いて回ります。
不良が発生すると、製造部門と品質部門が連携して原因と対策が行われることになります。
品質問題
製造業では日々の生産活動の中で様々な問題が発生します。
欠員、部品納入遅れ、特急増産要望、新製品生産、設計変更、、、
こういった日々の生産活動している中で不良が発生するが今回は作業が漏れてしまった事例。(作業漏れとは本来行うべき作業がされていないこと)
とある不良事例
作業手順は、
①ボディ部シャーシ組込
②レンズ組込
③光軸組立
④基板組込 ※コネクタ挿入
⑤内部確認 ※目視確認
⑥カバー取付
このような工程となっているが、不具合は④基板組込工程のコネクタ挿入がされていない不良が発生した。
原因調査
作業状況確認の為、録画ビデオで確認すると、
・この作業を行っていたAさんと、後工程担当Bさんの2名で作業をしていた
・Bさんは電気ドライバーを使ってネジ締め作業を行っていた
・Bさんがネジ締めを失敗し電気ドライバーをネジ頭のところで空転させた
・それを見たAさんは、作業途中であった④基板組込のコネクタ挿入しないまま、Bさんの所へ見に行った
・BさんのところでAさんは失敗した製品を確認した
・Aさんは自分の所に戻り、⑤内部確認から作業を開始した
その結果④のコネクタが挿入されない製品が組立てられた。
再発防止の取組
工程責任者と品質保証担当が再発防止をまとめた結果が、
原因
・作業を中断した際、手順の最初から確認して再開する手順が徹底されず不具合発生した。(元々社内ルールとなっている)
対策
・作業者全員に対して作業中断に関する手順を再指導し、作業途中の識別不備による作業漏れを防止するよう改善致しました。
これで再発しないのか?
この問題は、作業者だけが問題なのか?
作業指導すれば再発しないのか?
なぜ、作業者AさんはBさんの所に見に行ったのか?
このAさんは、トラブル対応をする役割があったのか?
と疑問が湧いてきます。
作業していると、突発的に今回のような様々なトラブルが発生します。
トラブルが発生した時に、作業者同士が相談して対応しようとすることが問題であり、組織的に対応することが出来ないのが最大の問題です。
作業手順は教育するが、トラブル発生の対応が曖昧になっている。
ここは厳密に、トラブル発生時は誰が対応するのか役割を徹底しておく必要がある。
問題発生時、『誰が』『何を』『対応する』など役割が明確になっていないと今回のように作業者同士が相談することになる。
ここでなら、作業だけ行う作業者、工程全体の問題を対応するリーダー、役割分担と、どこまで対応するのかを事前に決めておく。
まとめ
作業ミスが起きると、とかく作業者の問題として『教育しました』とか『再教育した』とかの対策をしてくるが実は、仕事の仕組みが曖昧のままになっていることが問題があることが原因となっている。
そもそも、作業ミスが発生するのは作業環境が出来ていないことがある。
簡単に作業者の問題として片付けてしまう。
これが分かっていない役職者がいるのです。
作業担当者に作業手順は教育するが、トラブル発生時の対応の仕方を明確に教育していないことが問題であり、手順通りにできなかった場合、誰に確認してもらうか決めておくこと。
作業範囲と役割を明確にしておくことが重要である。
この記事が気に入ったらサポートをしてみませんか?