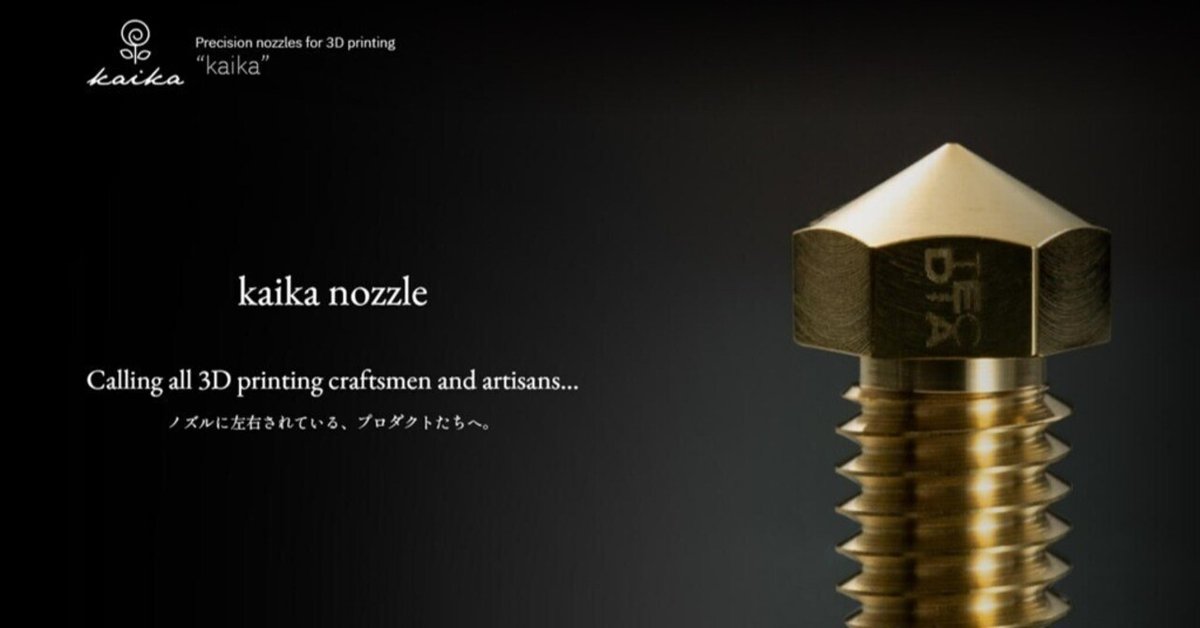
kaikaノズルは造形になぜ有利なのか考えてみる
kaikaノズルは最近とても人気がでてきています。造形外観がきれいになる、造形トラブルが減るなどメリットがたくさんあります。kaikaノズルは他のノズルと何が違うのでしょうか?どんな理屈があって、なぜkaikaが造形に有利なのかを思考実験的に考えてみたいと思います。あらかじめお断りしておきますが、ここで書いていることはあくまで私見で、裏付けがあるわけではありません。実際の造形で起きることを考える上での参考程度という形にてお願いします。
◆ ◆ ◆ ◆ ◆
今回はOsswaldのフィラメント溶融モデルで考えます。フィラメントはノズル内で十分に溶融せず、円錐部分に接触してはじめて溶融するというモデルです。Osswaldのモデルはフィラメント送り速度が比較的大きい時に実際の挙動と合致しやすいと考えられています。
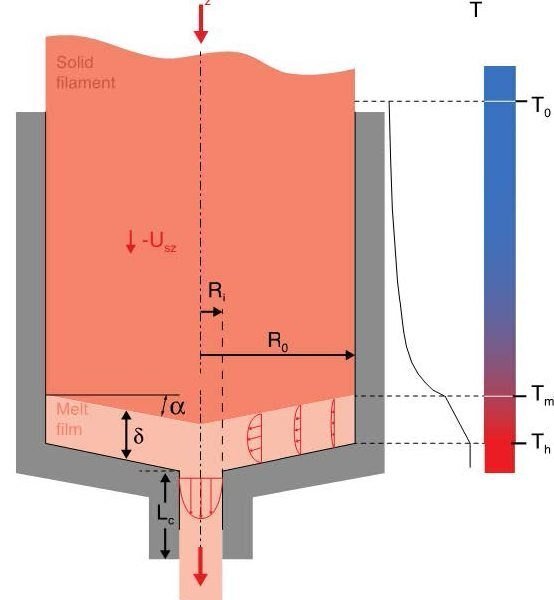
今回は扱いませんが、ノズルに到達すると樹脂が完全に溶融状態になるというBelliniのモデルもあります。興味があれば見てみてください。
3Dプリンタのフィラメント溶融モデル
一般的なノズルの場合
円錐部の角度は鈍角で加工仕上げが粗い状態です。ノズル壁面と溶融樹脂との摩擦が大きくなります。摩擦が大きいためフィラメント送りに大きい力が必要となり、エクストルーダーの負荷が大きくなります。力をかけてもノズル出口に向かって流れにくいため、一旦は円錐部分で樹脂は溶融するものの、一部は楽な方向に逃げてしまい、樹脂が逆流します。この逆流部分が渦を巻いて循環するため、どうしてもメルトプール部分が大きくなります。
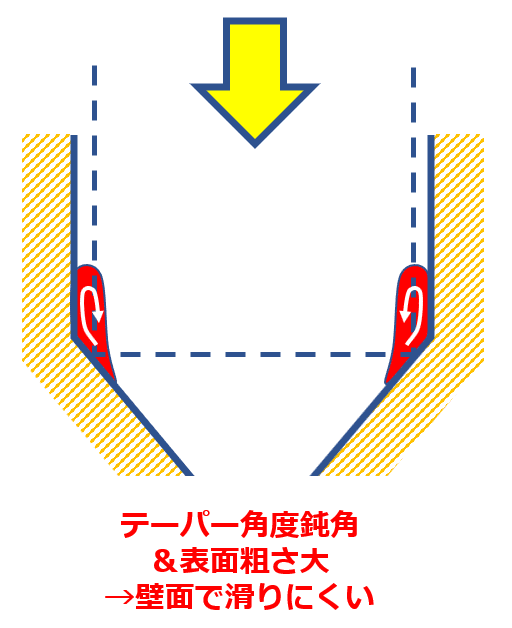
メルトプール部分が大きいということは、フィラメントを押し引きした際の応答の遅れにつながります。樹脂の滞留も大きいためノズル内の炭化が進みやすく、詰まりも起きやすくなります。
ノズルの中で樹脂が逆流するというのはちょっと意外な気がしますが、論文を見ていくといくつかでてきます。たとえばこんな感じの図で説明があります。
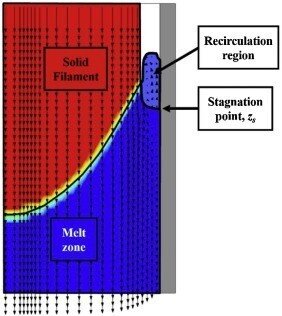
一般的なノズルでは壁面付近で滑りにくく、中心が優先的に流れるため、ノズル出口では中心付近と壁面付近との流速の差が大きくなり、流速分布は放物線状になります。各箇所での流速分布は下のようになると考えられます。
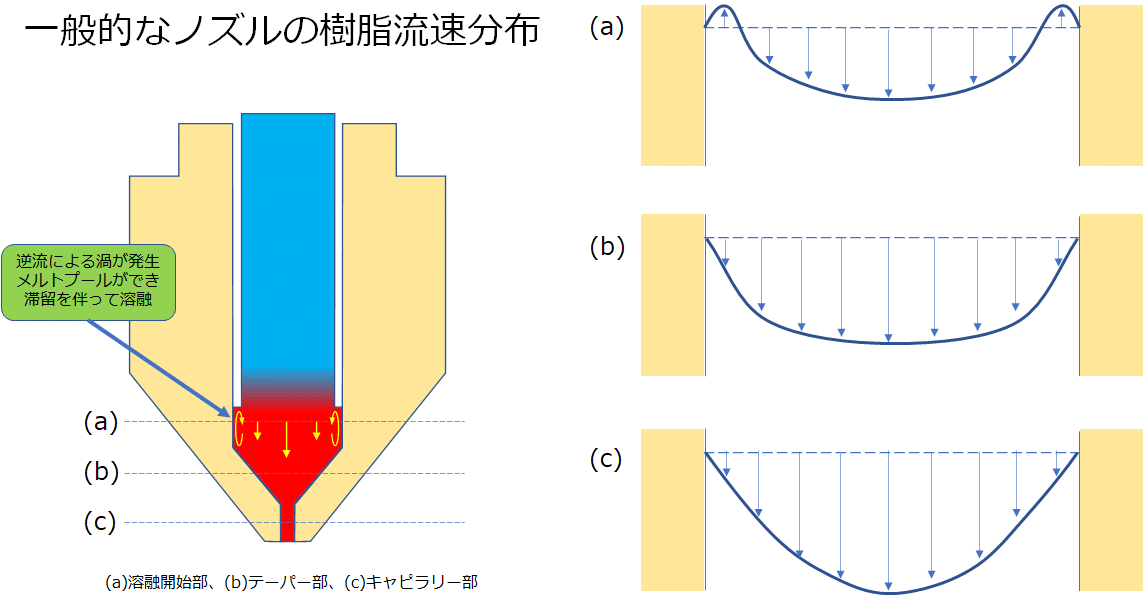
速度分布が放物線になるということは、ノズル壁面から流れの中心に向かってせん断が起きているということなので、せん断で変形した分の弾性回復がおきます。そのためダイスウェルが大きくなり、ノズル出口で樹脂が膨らみます。膨らんだ分側面が丸くなるので、最終的な造形品の側面も丸くなり、造形外観として積層痕が目立つということにつながります。
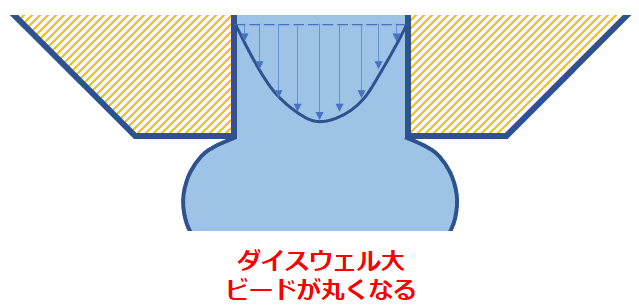
また、流速分布ができるということは、高分子の鎖が引き伸ばされやすいということでもあります。全体的に鎖が引き伸ばされるため、吐出ビード断面のほとんどが低粘度となり、引き伸ばされていない部分は中心に近い部分のみとなります。全体として粘度が低い状態で吐出されることになり、ダレが起きやすくなると考えられます。
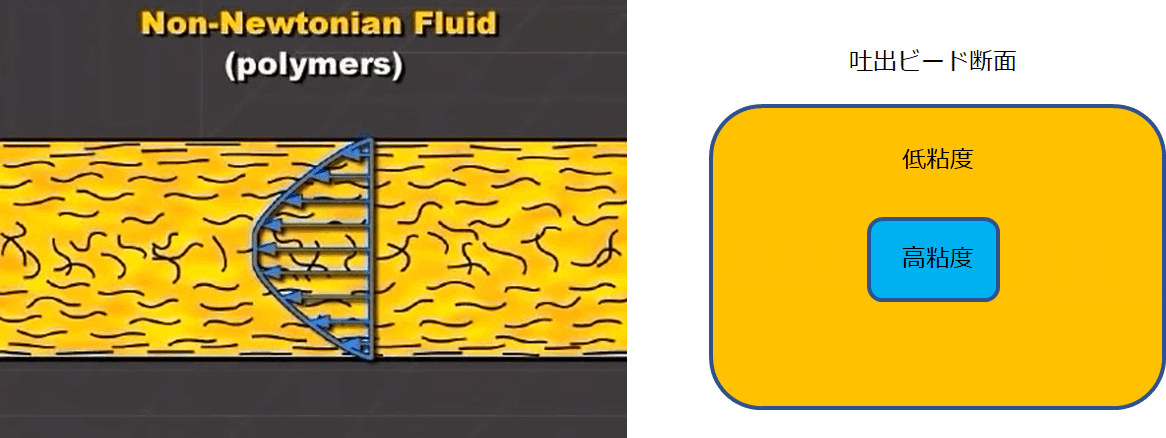
整理すると、一般的なノズルでは以下のことが起きやすいと考えられます。
一般的なノズルで起きやすいこと
・フィラメント送りに大きい力が必要(エクストルーダー負荷大)
・フィラメントを押し引きした際の応答が遅れやすい(造形外観悪化)
・樹脂の滞留が大きい(ノズル詰まりが起きやすい)
・ダイスウェルが大きい(積層痕が目立つ)
・ダレが起きやすい(造形外観悪化)
kaikaノズルの場合
円錐部分の角度は鋭角で、加工により内面がなめらかに仕上げられています(参考:テクダイヤ製3Dプリンターヘッドノズルが選ばれる2つの理由)。そのためノズル壁面と溶融樹脂の摩擦は小さくなります。より小さい力でフィラメントを送ることができ、エクストルーダーの負荷が小さくて済みます。ノズル出口に向かって樹脂が流れやすく、樹脂の逆流が小さくなるためメルトプールが小さくなります。
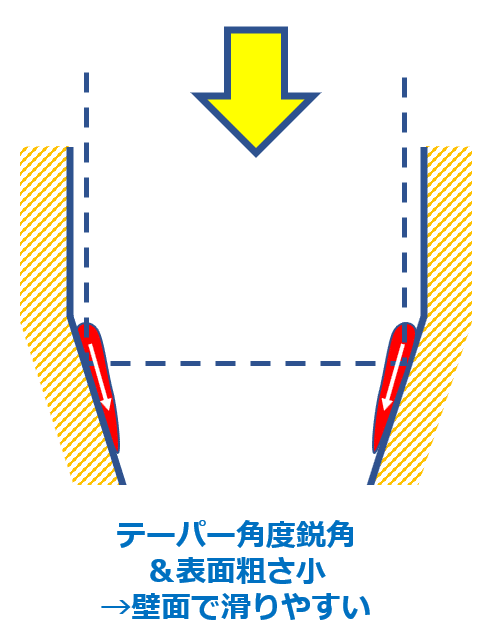
メルトプールが小さくなることで、フィラメント押し引きの際の応答が良好になるほか、樹脂の滞留も小さくなるためノズル内の炭化が起きにくくなり、ノズル詰まりは起きにくくなります。また、壁面付近が優先的に滑って流動するため、最終的なノズル出口付近で中心と壁面との流速の差が小さくなり、流速分布は均一に近くなると考えられます。
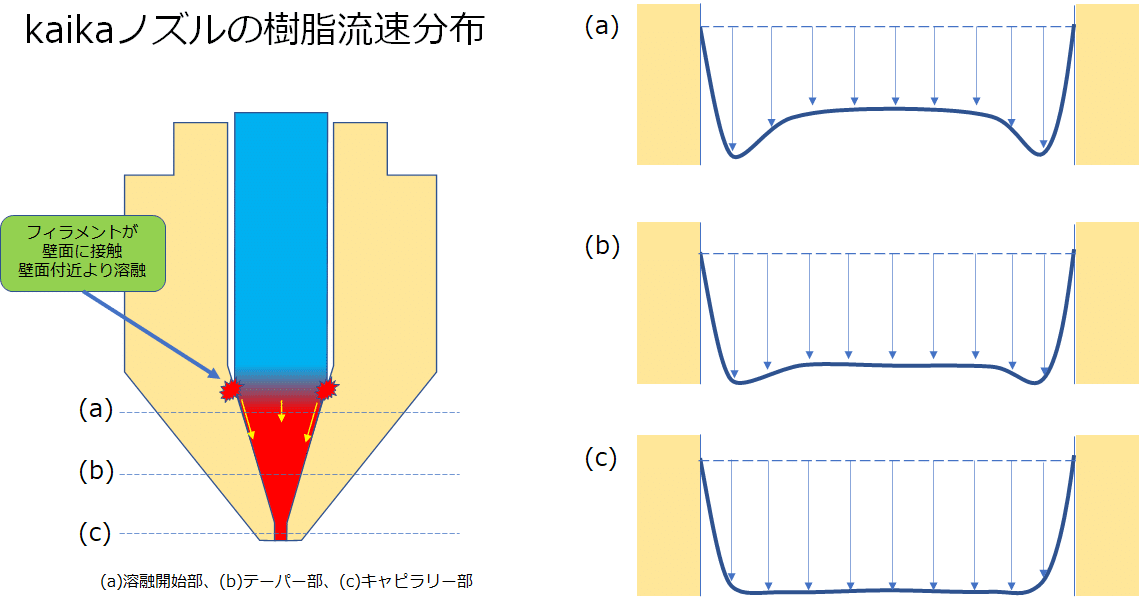
樹脂はハーゲンポアズイユ流れという放物線の速度分布で語られることが多く、実際にこんな流速分布になる可能性はあるのか?という疑問がでてきます。これもあくまで別の事例ですが、ノズル出口での流速分布をシミュレーションした結果があります。下図はフィラメント送り速度を変化させたときのノズル出口流速分布です。フィラメント送り速度をどんどん上げていくと、流速分布は均一に近づいていく結果となっています。これは送り速度が上がるとフィラメントがノズル内で十分溶融する時間がとれず、フィラメントが円錐部分に接触することで起こると書かれています。
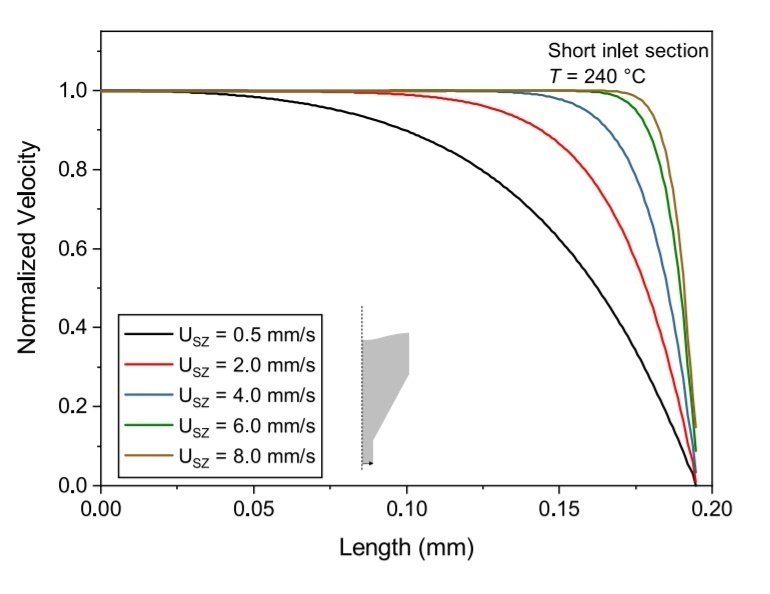
速度分布が均一に近づくということは、せん断はノズル壁面付近のみで起きているということになるので、ノズルを通過した後の弾性回復は起きにくいということになります。そのためダイスウェルは小さくなり、ノズル出口で樹脂はストレートに近い形状で吐出されることになります。ビード側面は切り立った形になるので、最終的な造形品の側面の丸みがなくなり、造形外観として積層痕が目立ちにくくなると考えられます。
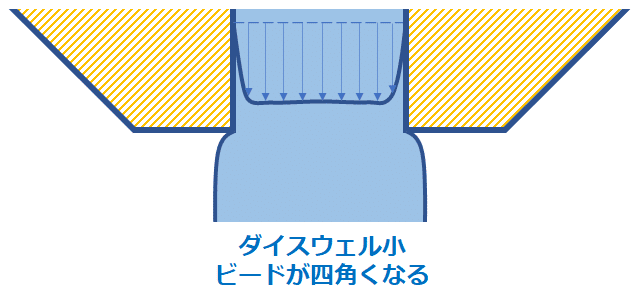
また、流速分布が均一に近づくことで、高分子の鎖が壁面付近でしか引き伸ばされなくなるということになります。壁面付近の滑りで流動していることになるため吐出ビード断面は外側のみが低粘度となり、引き伸ばされていない大部分は高粘度となります。全体として粘度が高い状態で吐出されることになり、ダレが起きにくくなると考えられます。
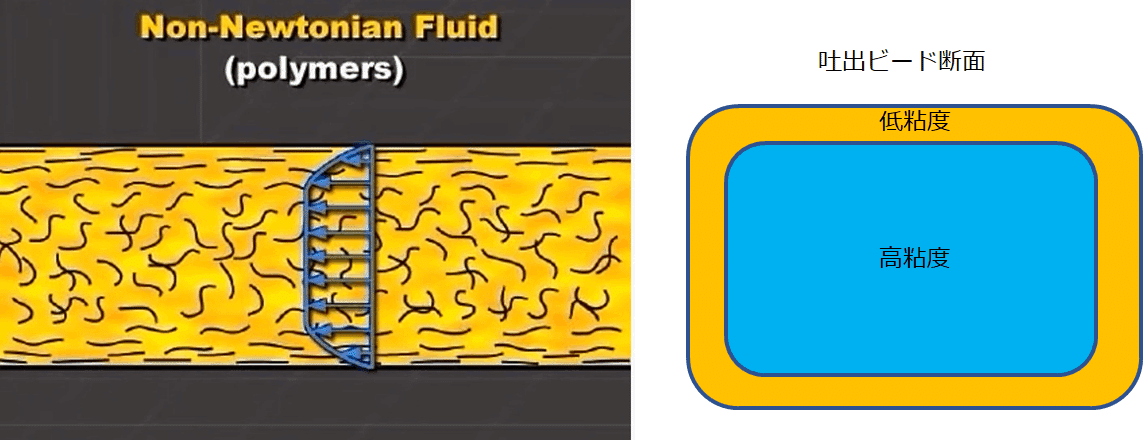
整理すると、kaikaノズルでは以下のことが起きやすいと考えられます。
kaikaノズルで起きやすいこと
・フィラメント送りが小さい力で済む(エクストルーダー負荷小)
・フィラメントを押し引きした際の応答が良好になる(造形外観向上)
・樹脂の滞留が小さい(ノズル詰まりが起きにくい)
・ダイスウェルが小さい(積層痕が目立ちにくい)
・ダレが起きにくい(造形外観向上)
3Dプリンタは細い穴から高い圧力をかけ、高い温度で吐出する加工法で、樹脂にとっては過酷な使われ方であるといわれます。その中でもkaikaノズルは樹脂にとって無理のない流れ方になるような設計や加工がなされており、この点が造形外観向上や造形安定化につながっているのだと考えられます。これらは理屈から考えても合致するように思います。
画像引用:
Single Screw Extrusion - Effects of Pressure, Temperature, and Flow
この記事が気に入ったらサポートをしてみませんか?