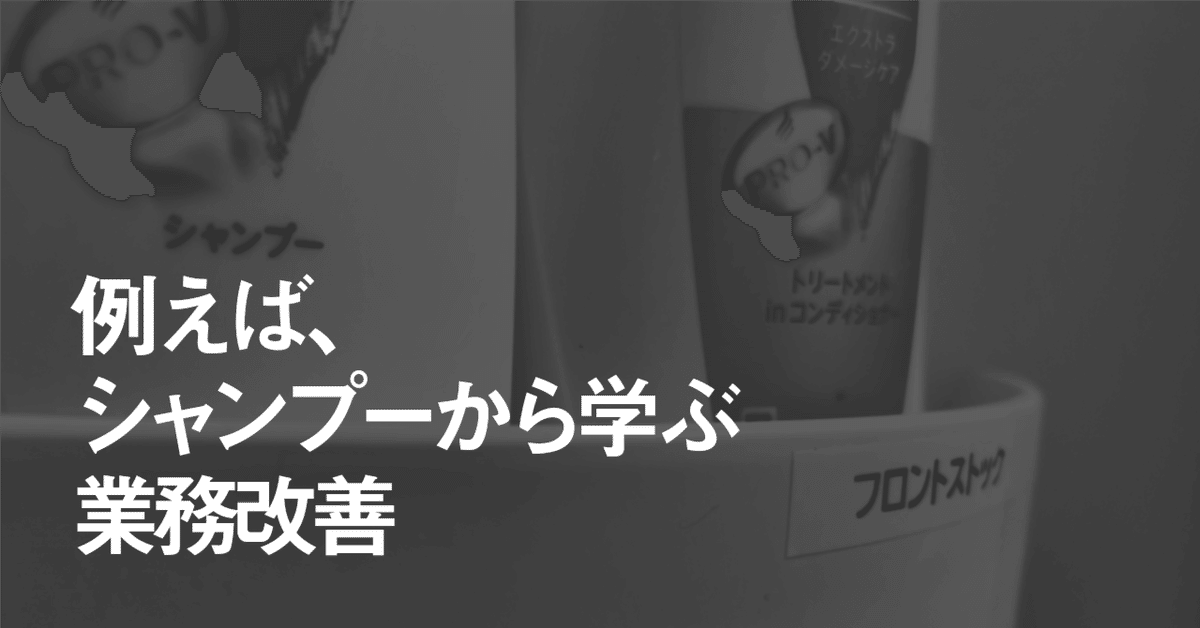
例えば、シャンプーから学ぶ業務改善
さて、人間は失敗する。
だが失敗は学習する機会である。
そして失敗から学習することは最も効率が良い。
なぜなら、不確かかつ複雑な世界において解決すべき問題を明らかにしてくれるからだ。
業務改善シリーズ、第1回目の今日は、失敗からの問題解決プロセスとその例を見る。
1. 原因を考える
当たり前だが、どのような失敗も原因が存在する。
身近な例では、「お風呂に入っているとき、シャンプーが切れており、髪を洗うことができない」ということも失敗に当てはまる。
シャンプーが切れていることを覚知するのは、大抵髪を濡らし終えたあとであり、すぐにシャンプーを詰め替えることはできない。すなわち、シャンプーが切れることで髪を洗うことができなくなり、「事故」が発生したこととなる。
体を清潔に保つという目的を達成するための手段として、「シャンプーを使って髪を洗う」が存在するが、このとき、シャンプーが切れていると目的は達成できない。
すなわち、この事故の発生原因は「シャンプーが切れていること」だと言える。そして、これが「直接原因」である。
2. 解決策は模倣から始めよう
シャンプーが切れたとき、「次こそは切れないようにしよう」とするのは精神論であり、次も失敗する確率が高まる。(=失敗の原因を、人の意識・理解に帰結する例)
そこで、先の直接原因が発生する原因、すなわち根本原因を明らかにしなければならない。
では、なぜシャンプーは切れるのだろうか。
シャンプーの入ったボトルには容量が存在し、シャンプー容量を使い切ることでシャンプーは使用不可な状態となる。つまり、使用可の状態を継続させるためにはシャンプーを補充し続ける必要がある。
すなわち、「シャンプーが切れていること」の根本原因は「シャンプーを補充していないから」である。
さて、失敗に対する再発防止策の立案である。
再発防止策には大きく2種類に分けられる。「不適合を取り除くこと」と、「不適合を再発させないため、その原因を取り除く処置・対策」(ISO 9000:2015)である。
「不適合を取り除くこと」は、例えばシャンプーが切れたとき、ボディーソープで髪を洗うことにより、髪を洗うことできないという失敗(=不適合)をなくすことである。
一方で「不適合を再発させないため、その原因を取り除く処置・対策」は、「シャンプーを補充していない」という原因(不適合の原因)をなくすことである。
「不適合を取り除くこと」は通常、そのときだけ(そのモノだけ)で終了するため、再発の可能性が高まると同時に二次被害が発生する可能性ある。(シャンプーの例ではボディーソープで洗うことにより、髪が痛むという二次被害が発生する。)
今回は、シャンプーが切れるという失敗は発生頻度が極めて高いため、「不適合を再発させないため、その原因を取り除く処置・対策」を行わなければならない。
ではどうやって「シャンプーを補充していない」という根本原因を解決するか。
まず簡単な解決手法としては、シャンプーの使用都度、シャンプーを補充する方法である。これは毎日お風呂に入った後、シャンプーボトルにシャンプーを補充することである。
しかし、この手法は合理的ではない。なぜならシャンプーの詰替はコストが高いからだ。
毎日、たかが3~6mlのために、「シャンプーボトルを開ける→シャンプーの詰替パックを開ける→注ぐ→詰替パックの封をする→シャンプーボトルを閉める→元の場所に戻す」という作業を行わなければならない。想定工数は1分だが、365日続けると、1年間に6時間はシャンプーの容量維持に時間を費やすことになる。極めてバカバカしい。
そこで、「シャンプーを補充していない」という根本原因の合理的な解決策の1つとして、トヨタの「カンバン方式」と「安全在庫」の考え方を応用させる。
カンバン方式と安全在庫について詳細に解説すると長くなってしまうので、各自検索してほしい。
カンバン方式をシャンプーに当てはめて説明するならば、
「シャンプーを詰め替える」必要があるときに、「シャンプーを詰め替える」というカンバンを表示し、詰め替えることである。
安全在庫の考え方をシャンプーに当てはめて説明するならば、
シャンプーの使用量に応じてシャンプーをストックしておくことである。
そして、かんばん方式×安全在庫による、解決策は以下の通りである。
1. シャンプーボトル1本が切れる期間を計測する(大体1ヶ月)
2. 1の期間シャンプーが切れても問題がない量のシャンプーボトルをもう一本用意する。(安全在庫を用意する)
3. シャンプーが切れたとき、すぐに手の届く場所にストックを置いておく
4. シャンプーを使用し、切れたとき、所定の位置に空になったシャンプーボトルを置く
5. 1の期間以下のスパンでシャンプーの詰め替えを行い、3を行う(発注を行う)
(3~5を繰り返す)
これを図解すると以下のようになる。
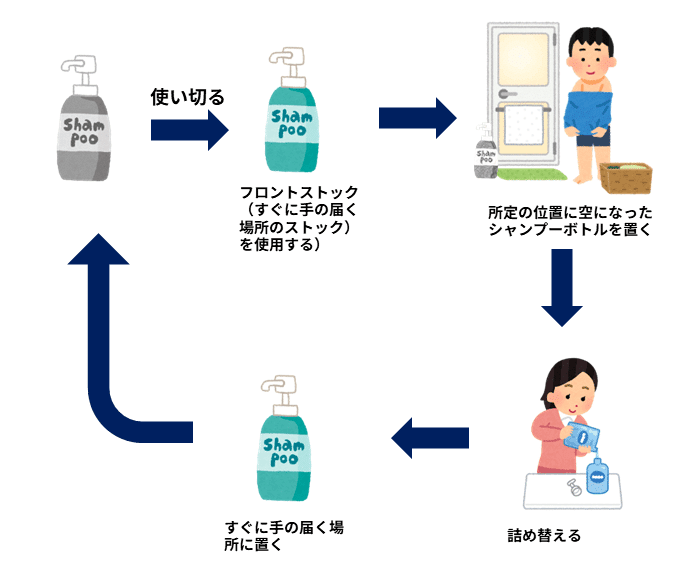
これにより、シャンプーの使用量が大幅に変動しない限り、シャンプーが切れることは無くなり、また無駄な時間を削減できる。
加えて、シャンプー以外の、例えばリンス、トイレットペーパー、中性洗剤などの日用品にも対応でき、5での発注タイミングを最小のものに合わせることで、一括して管理が可能となる。
まとめ
この一連の流れが、失敗から学ぶことであり、次に失敗しない方法であり、改善である。
そして、解決策を考えるとき、ヒントを探すことが重要である。
今回の場合、カンバン方式,安全在庫の考え方から解決策を導いた。人類は様々な失敗をしてきた。インターネット、本で、過去の失敗からヒントを収集しよう。
We cannot solve our problems with the same thinking we used when we created them.
いかなる問題も、それが発生したのと同じ次元で解決することはできない。
参考資料
情報処理システム高信頼化教訓活用ガイドブック(IT サービス編)
https://www.ipa.go.jp/files/000051042.pdf有効な是正処置のとり方 | ビューローベリタスジャパン株式会社
https://www.bureauveritas.jp/certification/standard/C002JISQ9000:2015 品質マネジメントシステム-基本及び用語
https://kikakurui.com/q/Q9000-2015-01.html
この記事が気に入ったらサポートをしてみませんか?