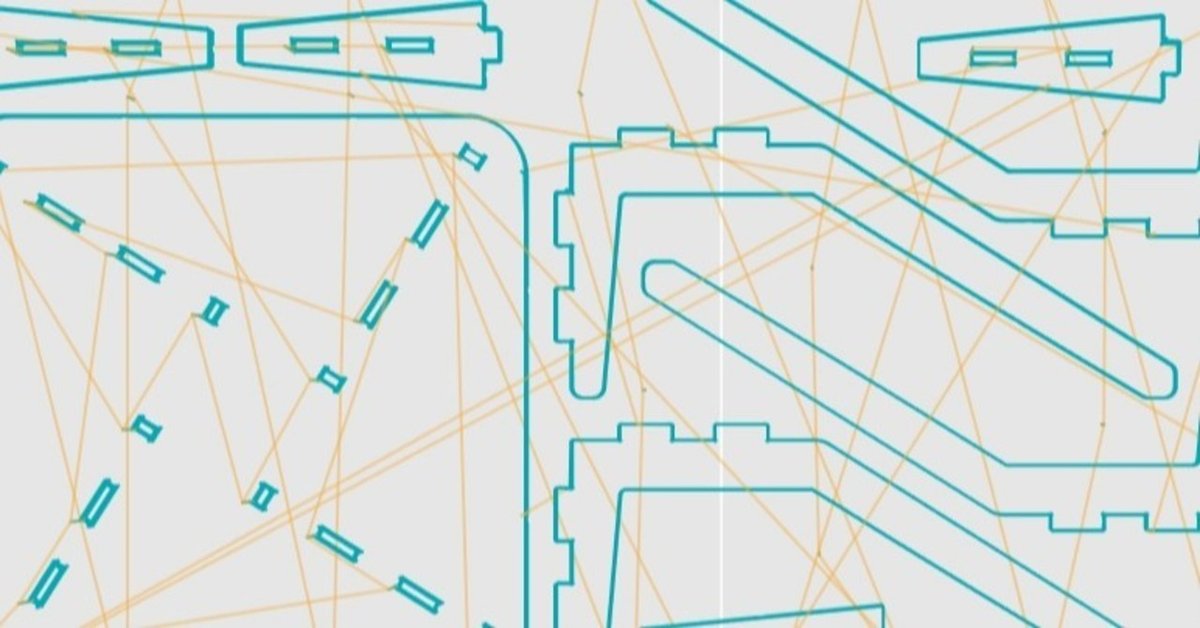
オンラインプレカットサービス『EMARF3.0』の手触りを試してみた
VUILD株式会社から5月27日にリリースされた、クラウドプレカットサービスの『EMARF3.0』をさっそく試してみました。
2019年にサービスが開始された『EMARF』は、予め用意されたデザインテンプレートを選び、自分の身体や部屋のサイズに合わせて寸法を調整するもので、同年11月にバージョンアップした『EMARF2.0』は、テンプレートの拡張機能を加えた、デザイナー向けのサービスでした。
どちらもテンプレートを調整するセミオーダーメイドの家具を頼めるサービスであったのに対して、今回の3.0ではユーザー自身がCADやillustratorを駆使することで、完全オリジナルの家具や建築までをもデザイン可能な、プラットフォームとして大きな転換を遂げています。
まさにVUILDが掲げる『すべての人を「設計者」にする』のミッション通り、ユーザーが直にコンテンツを設計するための「場」の提供に近づいています、クリス・アンダーソンの「MAKERS」を地で行くような展開で、国内のメイカームーブメントを盛り上げていくだろうと個人的にかなり期待しています。
たまたまテーブルを新調したいタイミングで、高さが可変なテーブルでなかなかいいものが売ってなかったため、無いなら作ろう!とさっそく試してみました。設計開始から10日ほどで完成したのがこちら。
思っていたよりもサクッと完成しましたが、いくつかEMARFに適応しなければいけないと思う点も見えてきたので、2020年6月の時点で、実際に利用してみた手触り感や気づいた点をまとめていこうと思います。
これから発展していく途上のプラットフォームなので、失敗も成功もオープンにユーザー全体で共有できる空気をつくって成長はどんどん加速させるため、また、興味があってまだ触れたことのない人にも手を出してみようと思える1サンプルになれば幸いです。
1.今回の設計条件について
・ベッド脇のサイドテーブルやサブの作業台(H=700㎜)として利用したい
・自室の広さから椅子を増やしたくないため複数人集まった際のローテーブル(H=300㎜)として利用したい
・コストと重量を抑える
の3点を目的に、部品を転用して数を抑える・軽量化を念頭に置いてます。
以下が設計時の仕様と条件。
①OS:win10 Home 1909
②CAD:Rhinoceros6 SR26
③材厚:18㎜
④材種:ラーチ合板
⑤ほぞ部分のオフセット:0.2㎜(要改善点1)
⑥ジョイント部分は脱着前提とする(要改善点2)
⑦角は曲線にして傷つきにくい形にすること
その他、細かな設計条件やEMARFのプラグインで出来ることは、ガイドに書かれている通りです。(https://docs.emarf.co/emarf3-guide/)
2.設計段階
プラグインのインストールは、Rhinocerosの場合、ツールバーレイアウトからEmarfCAMの読み込みを忘れなければ、すぐに使えるようになると思います。
操作も至って簡単で、オブジェクトをぴったりくっ付けた状態でデータを作っていれば、あとは自動で接合部を生成してくれます。
ホゾを生成する場合は、オス側の接触面の幅に最低寸法が設定されているようで、あまり細すぎるとプラグインがエラーを起こします。いくら以上の値が必要なのかは今後アップデートでガイドに表示されるとありがたいかも。
接合部の寸法と数は接触部分の長さを等分して作成されるので、端数込みの微妙な寸法になります。今回はオス・メスで不整合するのも嫌なので試してないですが、自動生成されたジョイントはマニュアルで数字を変更しても加工には影響しないとのことでした。
また、同じ寸法の振れ止め部材で、赤線部分の接触面に生成可能なホゾの最大本数が異なるケースが見られましたが、特に増やす必要もなかったので、原因はあまり考えず今回はホゾ穴を1か所に。
3.自動見積もりから出荷まで
emAlignで平面に起こしたパーツの配置が合板2枚にまたがった時、効率悪くないか?と少し不安になりましたが、emCAMでデータを送った際にまたshopbot用に配置し直されるので、そちらで確認できればOK。
一時見積もりの内訳はラーチ合板t18mmで1枚の場合がこちら。
(材料費+加工費)×1.2に送料がプラスされるので、今回は合計で15000円程度となった。
材料費に関しては大量発注の割安や材料納品によって割安にできるのかもしれませんが、EMARFで製作する家具は基本的にはどれだけ単純な形状でも、税込み10000円程度が製品価格のベースになりそう。
加工費に関しては2.2円/sec程度で、接合部を自動生成・CNC加工・秒速見積もりまでも出来てしまうので、既存のファブラボと比較しても破格。
部材が重すぎる懸念がある場合は、ついでに天板を肉抜きしたり、脚材をラチス化するような複雑で手間のかかる加工も頼んでしまった方が、自分で工具の準備や後片付けを考えると楽でしょう。今後、構造解析のような機能が追加されればこの辺りも調整できるかもしれないですね。
現在はコロナ禍のため出来ないようですが、将来的には加工場まで直に取りに行くこともできるかもしれない、とのことだったので、加工場のすぐ近くに住んでいる方や車を持っている方、公共交通機関でサブロク板を抱えて帰って平気な方は送料も調整可能になるかもしれない。
4.届いてから組み立てまで
最終的な見積もりを担当者とメールで確認し、入金後1週間で材が届いた。
非常に丁寧に梱包された状態。ガイドにはリブがついた状態で届く~とありましたが、部材以外の端材は含まれてませんでした。おそらく合板のJASマーク等をサンダーで削ったもらったからかもしれない。
パーツの状態はこんな感じ。同じくガイドに載っているような大きなバリもついていない。目立った割れや反りもなく、合板自体もホームセンターでよく見かけるものとは節も少なく綺麗な状態。
エッジの状態。
ほぞ穴。若干、秋材の部分が剥がれがち。
天板のアール部分もカクカクしておらず、非常に綺麗に加工されています。(今回はR=60で設計)
ホゾの寸法はノギスでそれぞれ図ったメモがこちら。
(赤字はRhinocerosのデータ上での寸法)
ガイドの記載にあったような±1mmもの誤差はなく、最大で-0.5mmから+0.4mm程度に収まった。shopbotの設定では、ホゾは大きめに・孔は小さめに、接合部はキツめに加工される傾向のようだ。
通常の無垢材であれば孔よりもホゾが+0.3㎜以下なら、7~8割程度を手ではめ込んだ後に叩き入れられそうですが、合板は表裏のベニヤが割れてしまう恐れがあるため、よりオフセットの調整はシビアになります。特にあられ組みの場合は出隅が目立つので、エッジが壊れないように、かつできれば接着剤も頼らないように調整したい。
一番想定外だったのは合板の厚みが厳密には18.0~18.3㎜あったため、ホゾの長手側がきつくなる点だった。始めにデータを厚み+0.2㎜程度に設定した上で接合部の詳細を作りこみ、EMARFに送信するタイミングで厚みを合板の規格に戻すのがよいかもしれない。18.3㎜のままでEMARFに送信しても支障なければ非常に楽だが、これはまた後日確かめてみよう。
今回はオフセットについて特に相談せずに進めてしまった上、ホゾ部分で脱着可能な設計にしたため、ちょうど良いハマり具合×抜きやすさになるまでヤスリで微調整を繰り返した。
最悪ゆるゆるなパターンは避けられたので、脚部の振れ止めパーツは使わないで済んだのはよかった。脚部の面外方向への倒れも問題なかった。
5.合板ー合板の接合部の考え方
ここまで実際に使ってみた中で分かった点・失敗した点・要望を時系列に沿ってつらつらと書いてきましたが、そもそもEMARFが抱えるデザインの特徴やフレームに適した考え方、工法のようなものを必要があると思います。
今回は天板と脚部をホゾだけでぴったりくっつけるように設計した点があまりEMARFに不向きだった。shopbotの加工精度や合板の厚みの誤差、クリアランスの設定など細かい調整が必要なポイントが増えすぎてしまい、設計がかなり煩わしくなってしまう。(改善点1・2)
脚部の倒れを抑えるなら、直交方向にゆるく組んで互いに支えあうようにすればよいし、天板はその脚に乗ってさえすれば成立するはずなので、
少なくとも家具の設計であれば、ちょうど現場で大工さんが使うような作業台から如何にデザインするか、という発想が出発点になるかもしれない。
(引用:https://marumohome.com/blog/blog_kenchiku/%EF%BD%8829-11-20.html)
これが天板勝ちの収まりなら机・テーブル・椅子、脚勝ちの収まりなら棚・梯子になるはず。
このように考えると、
・角度を絶対に固定したい場合 → ホゾ・相欠き・あられ組みでクリアを絶妙に調整
・乗ってさえいればOKな場合 → ホゾをゆるく設定 または 溝を掘って軽くはめ込む
・部材を倒れないようにする場合 → ゆるい相欠きで支えあう
などのように、接合部の種類は必要な強さに応じて分類できるでしょう。
すべてのジョイントを固める必要はあるのか、を頭の片隅に置いた方が発想の幅が広がる。
そのため、オンラインであることを生かし、接合部のパターンをユーザー間でシェアすることが出来れば、デザインの幅も広がり、誰でも設計者になれるまで敷居が下がるかと思います。
6.おわり
EMARFはとにかく設計から見積もり、加工までのプロセスが一気貫通しているため、その手軽さと素早さが最大の魅力なのは、実際その通りでした。
加えて木材の場合には、材の実際の硬さやめり込み、欠けや剥がれといった、模型だけでは掴み切れない部分も多く、複雑な形状でも比較的安価に試せる点も他にはない魅力です。
言われてみれば当たり前のようなことばかり書いた気もしますが、すべての人が設計者になるために、少しでもストレスを軽くできるヒントに繋がればうれしいです。
そういえばアレが欲しかったな、こんな製品って売ってないよな、と思いついた瞬間、さっそく試してみてはいかがでしょう。
この記事が気に入ったらサポートをしてみませんか?